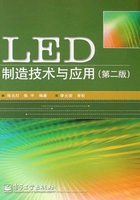
1.2 LED芯片制作的工艺流程
LED的制作工艺与半导体器件的制作工艺有很多相同之处。因此,除了个别设备之外,多数半导体设备经过适当的改造后,均可用于LED产品的制作。图1.5给出了制作LED芯片的工艺流程及相应工艺所需的设备。
LED制作工艺流程分为两大部分。首先在衬底上制作氮化镓(GaN)基的外延片,这个过程主要是在金属有机物化学气相沉积(Metalorganic Chemical Vapor Deposition,MOCVD)外延炉中完成的。准备好制作GaN基外延片所需的材料源和各种高纯的气体之后,按照工艺的要求就可以逐步把外延片做好(具体的工艺做法,这里不详细说明)。接下来是对LED pn结的两个电极进行加工(电极加工也是制作LED芯片的关键工序),并对LED毛片进行减薄、划片;然后对毛片进行测试和分选,就可以得到所需的LED芯片。
补充资料
MOCVD外延炉是最重要的LED制造设备,一台MOCVD外延炉的造价就要100多万美元。MOCVD是制作LED芯片最重要的一种技术,也是投资最大的一个环节。此外,制作电极需要用到光刻机、刻蚀机、离子注入机,这也是一个投资较大的环节。再则是减薄、划片和测试过程。由于生产中使用的蓝宝石衬底的硬度很高,要将其从400 nm减到100 nm左右,并要求厚度均匀、避免碎片,因此减薄也是一项工艺要求很高的过程。划片机要求使用十分坚硬的刀片,否则不能划断蓝宝石(也可用激光技术)。总的来说,这几台制作LED的设备造价都比较昂贵,是生产环节的一个投资重点。

图1.5 LED制作工艺的流程图
下面从LED的衬底、外延片、pn结电极三部分来具体讲解LED的制作工艺。
1.2.1 LED衬底材料的选用
对于制作LED芯片来说,衬底材料的选用是首要考虑的问题。应该采用哪种合适的衬底,需要根据设备和LED器件的要求进行选择。目前市面上一般有三种材料可作为衬底:
● 蓝宝石(Al2O3);
● 硅(Si);
● 碳化硅(SiC)。
蓝宝石衬底
通常,GaN基材料和器件的外延层主要生长在蓝宝石衬底上。蓝宝石衬底有许多的优点:首先,蓝宝石衬底的生产技术成熟、器件质量较好;其次,蓝宝石的稳定性很好,能够运用在高温生长过程中;最后,蓝宝石的机械强度高,易于处理和清洗。因此,大多数工艺一般都以蓝宝石作为衬底。图1.6所示为使用蓝宝石衬底做成的LED芯片。

图1.6 蓝宝石作为衬底的LED芯片
使用蓝宝石作为衬底也存在一些问题,例如,晶格失配和热应力失配,这会在外延层中产生大量缺陷,同时给后续的器件加工工艺造成困难。蓝宝石是一种绝缘体,常温下的电阻率大于1011 Ω·cm,在这种情况下无法制作垂直结构的器件;通常只在外延层上表面制作n型和p型电极(如图1.6所示)。在上表面制作两个电极,造成有效发光面积减少,同时增加了器件制造中的光刻和刻蚀工艺过程,结果使材料利用率降低、成本增加。由于p型GaN掺杂困难,当前普遍采用在p型GaN上制备金属透明电极的方法,使电流扩散,以达到均匀发光的目的,但是金属透明电极一般要吸收30%~40%的光,同时GaN基材料的化学性能稳定、机械强度较高,不容易对其进行刻蚀,因此在刻蚀过程中需要较好的设备,这会增加生产成本。
蓝宝石的硬度非常高,在自然材料中其硬度仅次于金刚石,但是在LED器件的制作过程中却需要对它进行减薄和切割(从400 nm减到100 nm左右)。添置完成减薄和切割工艺的设备又要增加一笔较大的投资。
蓝宝石的导热性能不是很好(在100℃约为25 W/(m•K))。因此在使用LED器件时,会传导出大量的热量;特别是对面积较大的大功率器件,导热性能是一个非常重要的考虑因素。为了克服以上困难,很多人试图将GaN光电器件直接生长在硅衬底上,从而改善导热和导电性能。
硅衬底
目前有一部分LED芯片采用硅衬底。硅衬底的芯片电极可采用两种接触方式,分别是L接触(Level-contact,水平接触)和V接触(Vertical-contact,垂直接触),以下简称为L型电极和V型电极。通过这两种接触方式,LED芯片内部的电流可以是横向流动的,也可以是纵向流动的。由于电流可以纵向流动,因此增大了LED的发光面积,从而提高了LED的出光效率。因为硅是热的良导体,所以器件的导热性能可以明显改善,从而延长了器件的寿命。
碳化硅衬底
碳化硅衬底(美国的CREE公司专门采用SiC材料作为衬底)的LED芯片电极是V型电极,电流是纵向流动的。采用这种衬底制作的器件导电和导热性能都非常好,有利于做成面积较大的大功率器件。采用蓝宝石衬底和碳化硅衬底的LED芯片如图1.7所示。

图1.7 采用蓝宝石衬底与碳化硅衬底的LED芯片
碳化硅衬底的导热性能(碳化硅的导热系数为490 W/(m·K))要比蓝宝石衬底高10倍以上。蓝宝石本身是热的不良导体,并且在制作器件时底部需要使用银胶固晶,这种银胶的传热性能也很差。使用碳化硅衬底的芯片电极为V型,两个电极分布在器件的表面和底部,所产生的热量可以通过电极直接导出;同时这种衬底不需要电流扩散层,因此光不会被电流扩散层的材料吸收,这样又提高了出光效率。但是相对于蓝宝石衬底而言,碳化硅制造成本较高,实现其商业化还需要降低相应的成本。
三种衬底的性能比较
前面的内容介绍的就是制作LED芯片常用的三种衬底材料,这三种衬底材料的综合性能比较可参见表1.1。
表1.1 三种衬底材料的性能比较

注 1:ESD——抗静电能力。
除了以上三种常用的衬底材料之外,还有GaAS、AlN、ZnO等材料也可作为衬底,通常根据设计的需要选择使用。
1.2.2 制作LED外延片
Ⅲ族氮化物半导体材料广泛用于紫色、蓝色、绿色和白色LED,以及高密度光学存储所采用的紫色激光器,紫外光探测器和大功率高频电子器件。目前市场上的红色和绿色LED大多采用的是以液相外延成长法为主的外延技术,而黄色、橙色LED的外延层仍以磷砷化镓(GaAsP)材料为主,这是用气相外延成长法生成的。MOCVD外延炉(也称MOCVD机台)是制作LED外延片最常用的设备。
补充资料
LED芯片的亮度及产品特性主要取决于发光层品质及相应材料的优劣。发光层主要是由单层的InGaN量子阱或多层量子阱(Multiple Quantum Well,MQW)组成的。尽管制造LED的技术一直在进步,但其多层量子阱的品质并没有成比例增长。其中主要原因是,MOCVD外延炉很难克服发光层中铟(Indium)的高挥发性和氨气(NH3)的热裂解效率低等问题(氨气与铟的裂解需要很高的温度和极佳的方向性才能顺利地沉积在InGaN的表面)。
金属有机物化学气相沉积法
金属有机物化学气相沉积(MOCVD)是一种制程过程,该方法利用气相反应物(或是前驱物)及Ⅲ族的有机金属和V族的NH3在衬底表面进行反应,从而在其上生成固态沉积物。MOCVD利用气相反应物的化学反应,将所需的产物沉积在衬底表面。其中蒸镀层的成长速率和性质(成分、晶相)会受到温度、压力、反应物种类、反应物浓度、反应时间、衬底种类、衬底表面性质等因素的影响。温度、压力、反应物浓度、反应物种类等重要的制程参数首先由热力学分析计算得出,再经修正后即可实现可行的程序工艺流程。
反应物扩散至衬底表面、衬底表面的化学反应、固态生长物沉积与气态产物的扩散脱离等微观的动力学过程对制程也有不可忽视的影响。MOCVD的化学反应过程有:反应气体在衬底的吸附、表面扩散、化学反应、固态生成物的成核与成长、气态生成物的脱附过程等,其中反应速率最慢的过程既是应该控制反应速率的步骤,也是决定沉积膜组织形态与各种性质的关键所在。
MOCVD反应系统的结构
MOCVD很容易控制镀膜成分、晶相等品质,可在形状复杂的衬底上实现镀膜均匀、结构密致、附着力良好等特点,因此MOCVD已经成为工业界主要使用的镀膜技术。MOCVD的制程因不同用途而有所差异,制程设备也有不同的构造和形态,整套系统大致可分为以下三部分:
● 进料区;
● 反应室;
● 废气处理系统。
进料区可控制反应物的浓度。气体反应物可用高压气体钢瓶质量流量控制器(Mass Flow Controller,MFC)来精确控制流量。而固态或液态原料则需采用蒸发器来使进料蒸发或升华,再以氢气(H2)或氩气(Ar)等惰性气体作为载体而将原反应物吸入反应室中。
反应室控制化学反应的温度与压力。在反应室里,反应物吸收系统供给的能量,突破反应活化能的障碍而开始进行反应。根据操作压力的不同,化学反应可分为:常压化学气相沉积(APCVD),低压化学气相沉积(LPCVD),超低压化学气相沉积(SLPCVD)。根据加热方式不同,化学反应可分为热墙式和冷墙式。热墙式是由反应室外围直接加热,并以高温作为能量来源。冷墙式的操作方式包括等离子辅助MOCVD、电子回旋共振式电浆辅助、高频MOCVD及Photo-MOCVD。
废气处理系统通常由多种装置组成,包括淋洗塔,酸性、碱性、毒性气体收集装置,集尘装置,以及排气淡化装置。废气处理系统用来吸收制程中的废气,使其符合排放标准的要求,不会对人体产生伤害。
外延技术与设备是外延片制造技术的关键所在。气相外延(VPE)、液相外延(LPE)、分子束外延(MBE)和金属有机化合物气相外延(MOCVD)都是常用的外延技术。大量实践证明,MOCVD是一种工业化的实用技术。当前,MOCVD工艺已成为制造绝大多数光电子材料的基本技术。
MOVCD反应系统的技术要求
先进的MOCVD装置首先应具有一个能同时生长多片均匀材料并能长时间保持稳定的生长系统,该系统不但有很高的产出量,而且能在短时间内生长出具有预定器件结构的单片材料。
精确的过程控制是保证重复和灵活地调整并生产先进LED器件复杂结构的必备技术。先进的MOCVD设备具有精确的对于载气和反应剂的压力与流量控制系统,配备有快速的气体转换开关和压力平衡装置,并且应选用合适的结构,用于减少反应剂的记忆效应,优化反应剂的浓度,以及改善生长区温度场的均匀分布状况。
优异的控制技术与生产高质量的外延材料密切相关。在实际生产中,必须保持影响外延层性能的参数尽可能恒定,特别要捕捉那些敏感参数并加以特殊关注。严密监控外延过程中如生长速率、组分、掺杂、表面形貌与结晶质量等重要参数。
为确保合理的成品率,材料的均匀性、重复性必须控制在某一统计容许范围内,外延片单片的均匀性生产工艺的选择与定位十分重要。同一炉内片与片之间的性能是否一致,以及不同生产批号之间的参数重复性,都具有重要的意义。
一般情况下,一组理想的MOCVD反应系统必须符合下列要求:
● 提供清净的环境。
● 反应物在抵达衬底之前应充分混合,从而确保外延层的成分均匀。
● 反应物气流需在衬底上方保持稳定流动,从而确保外延层的厚度均匀。
● 反应物提供系统应切换迅速,从而长出上下层接口分明的多层结构。
补充资料
外延片在光电产业中扮演了一个十分重要的角色,而MOCVD外延炉是制作外延片的不可缺少的设备。有些专家经常用一个国家或地区有多少台MOCVD外延炉来衡量这个国家或地区光电行业的发展规模,这已充分说明了MOCVD外延炉的重要性。根据生长的需要,MOCVD外延炉一次可以制出11片或15片外延片,有时也可以制出24片外延片。用户可以根据产量来选择MOCVD外延炉的规模大小。
1.2.3 LED对外延片的技术要求
LED对外延片的技术要求主要有以下四点:
● 禁带宽度适合。
LED的波长取决于外延材料的禁带宽度 Eg。pn结注入的少数载流子与多数载流子复合发光时,释放的光子峰值波长λ与禁带宽度的关系通常可表示为
λ=1240/Eg
式中,Eg的单位为电子伏特(eV),波长的单位为纳米(nm)。当选定了发光波长后,通常可通过多元半导体化合物材料的组分来调整Eg的值。例如,对应于InGaAlp材料,可选取合适的Al-Ga组分配比,以便在黄绿色到深红色的光谱范围内调整LED的波长。
● 制得电导率高的p型和n型材料。
为了制备优良的pn结,要有p型和n型两种外延材料。为获得较大的结电场,p区和n区的载流子浓度应足够高,通常掺杂的浓度不应小于1×1017/cm3。另外,为了减小正向串联电阻,应尽量选取高迁移率材料,以便获得较高的体电阻率。工艺上,这两种导电类型的材料是通过外延掺杂工艺来得到的。因此,选择适当的外延工艺和掺杂材料,确定适当的掺杂温度和浓度,是能否获得高电阻率材料的重要因素。同时掺杂的均匀性也将直接影响LED外延材料的质量。
● 获得完整性好的优质晶体。
晶体的错位、空位等缺陷及氧气等外来杂质,导致了复合中的质量问题,从而对发光效率产生很大的影响。因此,获得完整性好的优质晶体是制造高效率LED的必要条件。晶体的完整性与晶体的生长方法密切相关,选择合适的外延技术、精密控制外延层内在质量及各层界面的缺陷,对于制造超高亮度LED外延片来讲是至关重要的。
● 要求发光复合概率大。
发光复合概率大对于提高发光效率是必要的,一般采用直接跃迁型半导体材料。四元半导体化合物材料的禁带宽度能随组分变化而变化。晶体结构也会随组分而从直接跃迁型变化到间接跃迁型。在外延材料的结构设计中,如何适当地选择组分对于提高发光效率也是很重要的。
检验外延片
制作好外延片后要对其进行检验,主要从以下几方面来检查外延片:
● 表面平整度;
● 厚度的均匀性;
● 径向电阻分布。
通过光强测试仪的两根探针直接接触外延片进行测试,如果外延片表面有非常多的小突起、针孔和六角晶体,那么就会发现有上述现象的外延片发出的光很不稳定、漏电流很大且光强低。如果外延片表面非常细腻,并且光泽度和平整度都很好,那么使用上述方法测量的正向电压会较低,一般在3~3.3 V之间,同时发光稳定、光强较高、反向漏电小。
出现表面质量差、漏电大等情况,其原因很可能是在生长GaN外延层时,镓流量与NH3流量没有达到良好的化学计量比及氮化的时间不同。外延片的质量决定了LED芯片的质量,如果要得到理想的LED,首先要制作出高质量的外延片。
1.2.4 制作LED的pn结电极
任何半导体器件最终都要通过电极引线和外部电路相连,金属-半导体界面的性质对整个器件的性能有很大影响,对于GaN基发光二极管也不例外。金属-半导体界面接触部分的电流-电压降呈线性关系,相当于一个阻值很小的电阻(也称为欧姆接触电阻)。
由于界面没有势垒,接触部分的电压降与器件内部的电压降相比可以忽略。如果欧姆接触电阻太大,那么将使LED器件的正向工作电压Vf增大、注入效率降低,并且器件发热、亮度下降、寿命缩短,所以LED芯片的pn结电极的质量直接影响LED器件的质量。
pn结电极的制作工艺一般采用光刻、真空电子束蒸发、湿法腐蚀和剥离等方法。当前普遍采用的p型接触电极是镍/铜(Ni/Au),可以使电极具有良好的透光性和电学性能。在LED芯片的制作工艺中,为了尽量减少电极之间的相互影响,需要对n型电极进行合金。然而在n型电极的合金过程中也会对p型接触电极产生影响,所以电极管芯在氮气中进行合金时使p型接触电极的性能维持不变是很重要的。
LED的I-V特性与I-P特性
电极位置的不同对LED的I-V(电流-电压)特性也会产生影响。图1.8和图1.9中的四种芯片都是V型接触电极,其n型接触电极采用Ti/Ai/Ti/Au结构,p型接触电极用氧化Ni/Au透明电极,焊线电极为Ti/Au,并采用一致性很好的外延片。

图1.8 L型接触电极Ⅰ

图1.9 L型接触电极Ⅱ
通过考察图1.10的I-V特性曲线和图1.11的I-P特性曲线,可以看出LED芯片在20 mA电流以下的I-V特性和I-P特性与芯片尺寸的关系不大,但与电极位置有一定关系。p型焊线电极远离n型电极的芯片在20 mA电流下的光输出功率高,其正向压降较大。在大电流下,p型焊线电极远离n型电极的芯片很容易饱和,这时若芯片尺寸较大,则其大电流性能要好一些。因此在选择芯片将其封装成LED时,要注意芯片两极的位置,尽量做到在同一批芯片中,避免有不同的电极结构,继而防止在不同的电流下工作时出现不同的I-P特性,结果造成LED的性能不一致。
相对于L型接触电极在大电流情况下的工作效果,V型接触电极的芯片的I-P特性较好,而且导热也非常好。这种芯片在封装时只需要焊接一根线,因此其抗静电能力好、光输出效率高。

图1.10 图1.8和图1.9中芯片的I-V特性曲线

图1.11 图1.8和图1.9中芯片的I-P特性曲线
pn型电极对LED器件而言是十分重要的,应重点关注这一部分的制作。对于不同功率的LED器件,其电极的结构也不一样,将在“根据LED芯片的功率进行分类”一节(1.3.2节)说明。