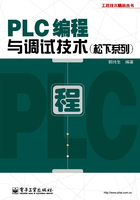
1.1 PLC的历史和特点
1.1.1 PLC的历史和定义
1.PLC的历史
世界上第一台PLC是1969年由美国数字设备公司(DEC)生产的。当时工厂中生产线的控制系统都是继电器控制系统,虽然具有简单易懂,操作方便,价格较低的优点,但硬件设备多,接线复杂。在市场经济的环境下,产品的品种和型号经常不断地更新换代,导致产品的生产线及其控制系统需要不断地修改或再设计,采用继电器控制系统既浪费了许多硬件设备,又延长了施工周期,大大增加了产品的成本、企业的负担。于是人们迫切需要研制一种新型的通用控制系统,以取代原来的继电器控制系统,使其既保留继电器控制系统的优点,又能吸收当时的计算机技术,功能丰富,控制灵活,通用性强,少换设备,简化接线,缩短施工周期,降低生产成本,可在恶劣的工业环境下运行。根据上述要求,1968年,美国通用汽车公司(GM)采用招标的形式向世界各国发包,在标书中明确提出了如下10项指标(又称GM10条):
(1)编程简单,可在现场修改和调试程序。
(2)维护方便,各部件最好采用插件方式。
(3)可靠性高于继电器控制系统。
(4)设备体积要小于继电器控制柜。
(5)数据可以直接送入管理计算机。
(6)成本可与继电器控制系统相竞争。
(7)输入量是115V交流电压。
(8)输出量为115V交流电压,输出电流2A以上,能直接驱动电磁阀。
(9)系统扩展时,原系统只需进行很小的改动。
(10)用户程序存储器容量能扩展到4KB。
结果美国数字设备公司(DEC)中标,并于1969年研制出世界上第一台PLC,在GM公司首先成功使用。初期的可编程序控制器主要用于顺序控制,只能进行逻辑运算,所以称之为可编程序逻辑控制器(Programmable Logic Controller),简称PLC。后来随着电子技术和计算机技术的迅速发展,可编程序控制器不仅能实现继电器控制所具有的逻辑判断、计时、计数等顺序功能,同时还增加了数据传送、算术运算、对模拟量进行控制等功能,真正成为一种电子计算机工业控制装置,而且做到了体积超小型化。这种采用微电脑技术的工业控制装置的功能远远超出了逻辑控制、顺序控制的范围,故称为可编程序控制器,简称PC(Programmable Controller)。但由于广为人用的个人电脑(Personal Computer)也简称PC,为免混淆,所以世界各国都习惯将可编程序控制器统称为PLC。
2.PLC的定义
可编程序控制器的出现,立即引起了各国的注意。日本于1971年引进了可编程序控制器技术,德国于1973年引进了可编程序控制器技术,我国于1973年开始研制可编程序控制器,1977年应用到工业生产线上。
随着生产PLC的国家越来越多,国际上需要对PLC这种装置下一个统一的定义。1985年1月国际电工委员会给PLC下的定义是:可编程序控制器是一种数字运算操作的电子系统,专为在工业环境下应用而设计的。它采用可编程的存储器,在其内部存储执行逻辑运算、顺序控制、定时、计数和算术运算等操作指令,并通过数字式和模拟式的输入和输出,控制各种类型的机械或生产过程。可编程序控制器及其有关设备,都应按易于与工业控制系统形成一个整体,易于扩展其功能的原则设计。
1.1.2 PLC的特点
和传统的继电器控制系统相比较,可编程序控制器主要具有如下优点:
■ 编程简单,维护方便。国际电工委员会(IEC)在规定PLC的编程语言时认为,主要的程序组织语言是顺序执行功能表,功能表的每个动作和转换条件可以运用梯形图编程。PLC采用面向用户的梯形图编程语言,这是一种以继电器梯形图为基础的形象编程语言,其中的梯形图符号与定义和常见的继电器控制系统中的继电器图符号完全相类似,电气工程技术人员很容易掌握,用起来得心应手,这种轻而易举的编程风格是PLC能迅速推广应用的一个重要因素。由于PLC采用软件编程来完成控制任务,所以随着要求的变化对程序的维护也显得十分方便。
■ 接线简单,成本降低。PLC实现了硬件软件化,在需要大量中间继电器、时间继电器和计数器的场合,PLC无需增加硬件设备,利用微处理器及存储器的功能,就可以很容易地完成,并大大减少了复杂的接线,从而降低了控制成本,使产品具有很强的竞争力。
■ 可靠性高,抗干扰能力强。由于采用了大规模集成电路和计算机技术,因此可靠性高,抗干扰能力强,坚固耐用和密封性好,MBTF(平均无故障时间)约为5万小时,可经受1 000V/1µs矩形脉冲的干扰,所以PLC特别适合在恶劣的工业环境下运行。
■ 模块化组合,灵活方便。现在的PLC多采用模块化组合,而且多种多样,这使得用户可以针对不同的控制对象灵活组合和扩展,以满足不同的工业控制需要。
■ 维修便利,施工周期缩短。PLC具有完善的监控诊断功能,内部工作状态、通信状态、I/O点的状态及异常状态均有醒目的显示,维修人员可以及时准确地发现和排除故障,大大缩短了维修时间。
■ 通信功能强,高度网络化。采用适配器、RS-232/RS-422/RS-485/USB等多种通信接口、C-NET网络,并采用多种功能的编程语言和先进指令系统,如Basic等高级语言,能轻松实现PLC之间以及PLC与管理计算机之间的通信,形成多层分布控制系统或整个工厂的自动化网络,使通信更方便快捷。