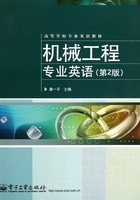
6.2 Electrical Discharge Machining (EDM)
Electrical discharge machining (EDM) sometimes is colloquially referred to as spark machining, spark eroding, burning, die sinking or wire erosion. It is one of the most widely used non-traditional machining processes. The main attraction of EDM over traditional machining processes such as metal cutting using different tools and grinding is that this technique utilizes thermoelectric process to erode undesired materials from the workpiece by a series of rapidly recurring discrete electrical sparks between workpiece and electrode. [2]
The traditional machining processes rely on harder tool or abrasive material to remove the softer material whereas nontraditional machining processes such as EDM uses electrical spark or thermal energy to erode unwanted material in order to create desired shapes. So, the hardness of the material is no longer a dominating factor for EDM process.
EDM removes material by discharging an electrical current, normally stored in a capacitor bank, across a small gap between the tool (cathode) and the workpiece (anode) typically in the order of 50 volts/10amps. As shown in Fig.6.1, at the beginning of EDM operation, a high voltage is applied across the narrow gap between the electrode and the workpiece. This high voltage induces an electric field in the insulating dielectric that is present in narrow gap between electrode and workpiece. This causes conducting particles suspended in the dielectric to concentrate at the points of strongest electrical field. When the potential difference between the electrode and the workpiece is sufficiently high, the dielectric breaks down and a transient spark discharges through the dielectric fluid, removing small amount of material from the workpiece surface. The volume of the material removed per spark discharge is typically in the range of 10-5 to 10-6 mm3. The gap is only a few thousandths of an inch, which is maintained at a constant value by the servomechanism that actuates and controls the tool feed.