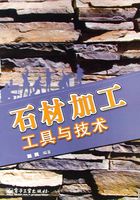
第二节 金刚石切割石材的研究
第一个用于锯割石材的金刚石圆锯片是法国人Felix Fromholt在1885年研制的。14年后金刚石锯片在Euville采石场得到应用。最早的金刚石锯片是在锯片的圆周上使用黑金刚石,并在巴黎的建筑过程中利用这种锯片锯割石灰岩和大理石。在1940年,由于粉末冶金技术的发展和应用,产生了金刚石烧结结块锯片。金刚石锯片技术的发展归结于合成金刚石的发明。天然金刚石的使用已经有几百年历史了,在这几百年中人们一直在努力寻找一种合成晶体的方法。一直到1953年瑞典的ASEA公司一个研究小组发明生产人造金刚石方法。美国DE公司在1955年开始在工业上大规模地生产人造金刚石。在过去40年间基于现代金刚石工具制造技术发展,金刚石工具已经广泛地应用到石材加工领域。目前金刚石工具市场连续地增长,用于切割石材的金刚石工具占整个欧洲金刚石工具的 50%。目前的发展趋势是大范围地采用金刚石线锯加工花岗岩和石材表面磨削和抛光。
金刚石磨料通常通过烧结或电镀的方式制成切割工具。金刚石工具的切割过程类似于磨削加工,但由于受材质的影响,石材的加工机理与金属加工机理不同,且加工过程更为复杂。由于金刚石切割工具最早应用于石材切割,因此对金刚石切割石材的机理研究较多。国内外学者对金刚石工具锯切花岗岩的加工机理进行了长期研究:从早期应用岩石在压头侵入下的断裂理论、单颗粒金刚石划伤表面形貌观察法逐渐发展到综合应用偏光显微镜和扫描电镜观察岩石加工表面形貌以及裂纹的产生和扩展规律、用声发射信号评价岩石的切削状态等。但由于岩石等硬脆材料的切割状态及切割过程非常复杂,因此对其切割机理的研究至今尚未形成统一的认识。与磨削加工的研究类似,人们首先研究了金刚石工具切割石材时单颗金刚石与石材之间的作用机理。早期的试验研究表明:单颗粒金刚石在不同条件下切削花岗岩时,岩石的破坏方式主要以脆性崩碎为主;同时,根据不同的矿物成分,岩石中仍有塑性变形产生。
石材切削力的研究对石材设备设计、石材工具使用和制造具有重要意义。石材切削力主要来源于金刚石颗粒受到石材断裂应力、刀头与石材的摩擦力。石材切削影响石材加工设备的主轴刚度、结构机构的强度和刚度、主电机功率等,同时还影响工具寿命、工具基体的强度和刚度等力学性能。影响石材切削力的因素主要有三方面构成:第一是石材性能,包括石材强度、硬度、化学成分、石材结构和构造等;第二是石材加工工艺参数,包括切削深度、进给速度、切割线速度、冷却水流量等;第三是工具参数,包括金刚石粒度、金刚石强度、金刚石浓度、结合剂类型等。加工石材方式不同,所产生的切削力也不同。切削力采用各种传感器进行测量。
切削热主要是金刚石刀头与石材摩擦产生。由于石材导热性差,大部分热量传到工具中,使工具表面温度升高,造成金刚石工具金刚石石墨化,金刚石切削能力降低,同时导致工具基体产生热疲劳,强度和刚度降低,加工石材时噪声增加,振动加剧,金刚石刀头早期破损,工具寿命降低。测量切削温度主要采用热电偶和红外线测温仪。
金刚石工具的磨损对其工具切削能力和加工过程的稳定性有着重要的影响。同时对切削力、切削温度和加工表面质量有很大影响。石材锯切过程是磨粒切削加工过程,因此,在锯切过程中应不断有金刚石磨粒的机械微破碎及相应的胎体磨损。金刚石磨损过程可以分成正常磨损和非正常磨损。金刚石正常磨损指金刚石颗粒在加工石材过程中受到石材摩擦力和断裂应力作用,金刚石体积不断减少,最终导致金刚石磨粒从胎体中出刃高度降低或脱落而完全丧失切削能力。非正常磨损是金刚石没有达到使用寿命而产生破损或脱落。金刚石磨损整个过程可以分为初期磨损(出刃)、正常磨损、急剧磨损三个阶段。金刚石磨损形式主要有表面磨平、表面破碎、整体脱落等。其中金刚石表面磨平和脱落使金刚石失去切削能力,而金刚石表面破碎降低金刚石切削能力。金刚石工具的磨损可以通过切削力和切削温度反映出来。影响金刚石工具磨损因素主要包括石材因素、工具因素和加工因素等。