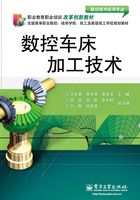
任务四 数控机床上的有关点
任务描述
机床原点与机床参考点之间有什么关系,它的重要性在哪里?工件坐标系原点是怎么样确定的,它的选择原则有哪些?
学习目标
了解数控机床上的相关点,掌握数控机床参考点的应用,理解数控机床参考点和机床原点之间的关系。理解工件坐标系原点确定的实质。
任务分析
数控机床上有关点的学习是编程应用中的关键,只有搞清楚相关点的联系才能更好地理解数控机床的应用。
任务完成
在数控机床中,刀具的运动是在坐标系中进行的,在一台机床上,有各种坐标系与零点。理解它们对使用、操作机床及编程都是很重要的。
一、机床原点
机床原点是指在机床上设置的一个固定的点,即机床坐标系的原点。它在机床装配、调试时就已确定下来了,是数控机床进行加工运动的基准参考点。在数控车床上,原点一般取在卡盘端面与主轴中线的交点处,如图1-2-10所示。图中O1即为机床原点。在数控铣床上,机床原点一般取在X、Y、Z三个直线坐标轴正方向的极限位置上,如图1-2-11所示。图中O1即为立式数控铣床的机床原点。

图1-2-10 数控车床机床原点

图1-2-11 数控铣床机床原点
二、机床参考点
许多数控机床(全功能型及高档型)都设有机床参考点,该点至机床原点在其进给坐标轴方向上的距离在机床出厂时已准确确定,使用时可通过“返回参考点操作”方式进行确认。它与机床原点相对应,有的机床参考点与原点重合。它是机床制造商在机床上借助行程开关设置的一个物理位置,与机床原点的相对位置是固定的,机床出厂之前由机床制造商精密测量确定。一般来说,加工中心的参考点为机床的自动换刀位置。有的数控机床可以设置多个参考点,其中第一参考点与机床参考点一致,第二、第三和第四参考点与第一参考点的距离利用参数事先设置。接通电源后,必须先进行第一参考点返回,否则不能进行其他操作。
机床原点实际上是通过返回(或称寻找)机床参考点来完成确定的。机床参考点的位置在每个轴上都是通过减速行程开关粗定位,然后由编码器零位脉冲(或称栅格零点)精定位的。数控机床通电后,必须首先使各轴均返回各自参考点,从而确定了机床坐标系后,才能进行其他操作。机床参考点相对机床原点的值是一个可设定的参数值。它由机床厂家测量并输入至数控系统中,用户不得改变。当返回参考点的工作完成后,显示器即显示出机床参考点在机床坐标系中的坐标值,表明机床坐标系已经建立。数控车床、铣工机床参考点如图1-2-12和图1-2-13所示。

图1-2-12 数控车床机床参考点

图1-2-13 数控铣床机床参考点
三、刀架相关点
从机械上说,所谓寻找机床参考点,就是使刀架相关点与机床参考点重合,从而使数控系统得知刀架相关点在机床坐标系中的坐标位置。所有刀具的长度补偿量均是刀尖相对该点(刀架相关点)长度尺寸,即为刀长。例如,对于车床有X刀长、Z刀长,对于铣床有Z刀长。可采用机上或机外刀具测量的方法测得每把刀具的补偿量。
有些数控机床使用某把刀具作为基准刀具,其他刀具的长度补偿均以该刀具作为基准,对刀则直接用基准刀具完成。这样编程人员在编程中不管刀具多少,只要考虑一把刀的运行轨迹就可以了。但采用这种方式,当基准刀具出现误差或损坏时,整个刀库的刀补要重新设置。
四、装夹原点
装夹原点(Fixture Origin),用C表示。装夹原点常见于带回转(或摆动)工作台的数控机床或加工中心,一般是机床工作台上的一个固定点,如回转中心,与机床参考点的偏移量可通过测量,存入CNC系统的原点偏置寄存器(Origin Offset Register)中,供CNC系统原点偏移计算用。
五、工件坐标系原点
在工件坐标系上,确定工件轮廓的编程和计算原点,称为工件坐标系原点,简称工件原点,也称为编程零点。
在加工时,工件随夹具安装在机床上,这时测量工件原点与机床原点间的距离,称为工件原点偏置。这个偏置一般用对刀或者测量得到。该偏置值预存入数控系统中(G50、G92、G54~G59),加工时工件原点偏置便能自动加到工件坐标系上,使数控系统可按机床坐标系确定加工时的绝对坐标值。因此,编程人员可以不考虑工件在机床上的实际安装位置和安装精度,而利用原点偏置功能,补偿工件在工作台上的位置偏差。
编程原点也称工件原点,由编程人员在工件上根据编程方便,自行设定的编制加工程序用的原点。工件原点只与工件有关,而与机床坐标系无关。但考虑到编程的方便性,工件坐标系中各轴的方向应该与所使用的数控机床的坐标轴方向一致。工件原点的设置一般遵循以下原则。
(1)工件原点与设计基准或装配基准重合,以利于编程。
(2)工件原点尽量选在尺寸精度高、表面粗糙度值小的工件表面上。
(3)工件原点最好选在工件的对称中心上,如图1-2-14所示。
(4)要便于测量和检验,如图1-2-15所示。

图1-2-14 铣削编程原点

图1-2-15 车削编程原点
六、程序起点
程序起点指刀具(或工作台)按加工程序执行时的起点,数控车床常用这一点作为换刀点。
七、刀位点
刀位点是刀具上的一个基准点,刀位点相对运动的轨迹即为加工路线,也称为编程轨迹。
八、换刀点
换刀点是为了加工中心、数控车床等采用多刀加工的机床而设置的,因为这些机床在加工过程中要自动换刀,在编程时应考虑选择合适的换刀位置,对于手动换刀的数控铣床,也应确定相应的换刀位置,为防止换刀时碰伤零件、刀具或夹具,换刀点常常设置在被加工零件的轮廓之外,并留有一定的安全量。
知识链接
在加工程序执行前,调整每把刀的位点,使其尽量与某一理想基准点重合,这一过程称为对刀。理想基准点可以设定在刀具上,如基准刀的刀尖上;也可以设定在刀具外,如光学对刀镜内的十字刻线交点。
对刀是指操作员在启动数控程序之前,通过一定的测量手段,使刀位点与对刀点重合。可以用对刀仪对刀,其操作比较简单,测量数据也比较准确。还可以在数控机床上定位好夹具和安装好零件后,使用量块、塞尺、千分表等,利用数控机床上的坐标对刀。在大批量生产过程中,更要考虑到对刀点的重复精度,该精度可用对刀点相对机床原点的坐标值来进行校核,操作者有必要加深对数控设备的了解,掌握更多对刀技巧。
1.对刀点的选择原则
(1)在机床上容易找正,在加工中便于检查,编程时便于计算,而且对刀误差小。
(2)对刀点可以选择零件上的某个点(如零件的定位孔中心),也可以选择零件外的某一点(如夹具或机床上的某一点),但必须与零件的定位基准有一定的坐标关系。提高对刀的准确性和精度,即便零件精度要求不高或者程序要求不严格,所选对刀部位的加工精度也应高于其他位置的加工精度。
(3)选择接触面大、容易监测、加工过程未定的部位作为对刀点。
(4)对刀点尽可能与设计基准或工艺基准统一,避免由于尺寸换算导致对刀精度甚至加工精度降低,增加数控程序编写的难度或零件数控加工的难度。对刀点的精度既取决于数控设备的精度,也取决于零件加工的要求,人工检查对刀精度以提高零件数控加工的质量。
2.对刀点的选择方法
对于数控车床或车铣加工中心类数控设备,由于中心位置(X0,Y0,Z0)已由数控设备确定,确定轴向位置即可确定整个加工坐标系,因此,只需要确定轴向的某个端面作为对刀点即可。
对于三坐标数控铣床或三坐标加工中心,相对数控车床或车铣加工中心复杂很多,根据数控程序的要求,不仅需要确定坐标系的原点位置(X0,Y0,Z0),而且要同加工坐标系G54、G55、G56、G57等的确定有关,有时也取决于操作者的习惯,对刀点可以设置在被加工零件上,也可以设在夹具上,但是必须与零件的定位基准有一定的坐标关系,Z方向可以简单的通过确定一个容易检测的平面去定,而X、Y方向需要根据具体零件选择与定位基准有关的平面或圆来定。对于四轴或五轴数控设备,增加了第四、第五个旋转轴,同三坐标数控设备选择对刀点类似,由于设备更加复杂,同时数控系统更加智能化,提供了更多的对刀方法,需要根据具体数控设备和具体加工零件确定。
3.对刀的基本方法
1)定位对刀法
定位对刀法的实质是按接触式设定基准重合原理而进行的一种粗定位对刀方法,其定位基准预设的对刀基准点来体现。对刀时,只要将各号刀的刀位点调整至与对刀基准点重合即可。该方法简便易行,因而得到较广泛的应用,但其对刀精度受到操作者技术熟练程度的影响,一般情况下其精度都不高,还须在加工或试切中修正。
2)光学对刀法
这是一种按非接触式设定基准重合原理而进行的对刀方法,其定位基准通常由光学显微镜(或投影放大镜)上的十字基准刻线交点来体现。这种对刀方法比定位对刀法的对刀精度高,并且不会损坏刀尖,是一种推广采用的方法。
3)试切对刀法
在以上各种手动对刀方法中,均因可能受到手动和目测等多种误差的影响,导致其对刀精度十分有限,往往需要通过试切对刀,以得到更加准确和可靠的结果。不同的系统操作方法不一样,请参考说明书。
思考与练习
1.简述数控机床上各种点的含义。
2.数控车削类机床上工件坐标系的原点是怎样确定的?
3.数控镗铣类机床上工件零点是怎么样确定的?