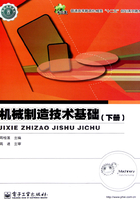
1.2 刀具材料
对金属的切削加工,除了要求刀具有合理的几何角度外,尚需刀具材料具有良好的切削性能。刀具材料的切削性能直接影响着生产率、工件的加工质量及刀具的制造成本等。正确选择刀具材料是设计和选用刀具的重要内容之一,特别是对某些难加工材料的切削,刀具材料的选用显得尤为重要。
1.2.1 刀具材料应具备的性能
刀具材料是指刀具切削部分的材料。由于刀具切削部分是在高温、高压及强烈挤压与摩擦的恶劣条件下工作的,对刀具材料的性能有较高的要求。
1)足够的强度和韧性
刀具的切削部分在切削时要承受很大的切削力、冲击力和切削振动,为防止刀具脆性断裂和崩刃现象的发生,刀具材料的抗弯强度和冲击韧性必须足够。
2)较高的硬度和耐磨性
硬度是指刀具材料抵抗其他物体压入其表面的能力。刀具材料的硬度必须更高于被加工材料的硬度,一般要求刀具材料的常温硬度在HRC 62以上。
耐磨性指刀具材料抵抗摩擦磨损的能力。通常,刀具材料硬度越高,耐磨性也越好。
3)较好的耐热性
耐热性是指刀具在高温环境下仍能保持足够的强度、韧性、硬度和耐磨性的能力。通常用高温硬度来衡量刀具材料耐热性的好坏。
4)良好的热物理性能和耐热冲击性
刀具材料的导热系数越大,导热性越好,切削热容易向外传散,有利于降低切削温度;线膨胀系数越小,可减小刀具的热变形,耐热冲击性越好,不会因较大的热冲击而使刀具产生微裂纹,甚至刀具断裂。
5)良好的工艺性
为便于刀具本身的制造和刃磨,要求刀具材料有良好的工艺性。工艺性包括冷加工工艺性(切削性能和磨削性能)和热加工工艺性(焊接性能、热塑性能和热处理性能等)。
另外,在满足以上性能要求的前提下,尽量采用资源丰富、价格低廉等比较经济的材料。
但是,上述对刀具材料的各项要求,往往是相互矛盾的。如强度高、韧性好的材料,其硬度和耐磨性较差;耐热性较好的材料,其韧性又不足够。所以应根据具体的切削条件,综合考虑上述各项要求,合理选择刀具材料。
1.2.2 常用刀具材料
刀具材料主要可分为工具钢(碳素工具钢、合金工具钢和高速钢)、硬质合金和超硬刀具材料(陶瓷、金刚石及立方氮化硼)等三大类。其中,碳素工具钢(如T10A)、合金工具钢(如9SiCr),因热处理工艺性和耐热性较差,一般常用于制造手工工具或一些形状比较简单的低速刀具,如锯条、锉刀、手用铰刀等。而超硬刀具材料,强度低、脆性大,且成本较高,仅适用于某些有限的场合。在实际生产中,应用最为广泛的刀具材料还是高速钢和硬质合金。
1.高速钢
高速钢是加入了较多的W、Cr、Mo、V等合金元素的高合金工具钢。和其他工具钢相比,其综合力学性能有所提高,特别是耐热性显著提高,当切削温度达到600℃时,仍能正常切削,切削速度可提高2~4倍。高速钢的抗弯强度甚至可达到4GPa,是硬质合金的2~3倍,是陶瓷的5~6倍。由于高速钢刀具材料综合力学性能较好,故广泛应用于形状复杂、尺寸较大的刀具制造中,如麻花钻、铰刀、铣刀、拉刀、各种齿轮加工刀具及其他各种成形刀具。表1-1所示为几种常用高速钢的牌号、性能及主要用途。
表1-1 几种常用高速钢的牌号、性能及主要用途

2.硬质合金
硬质合金由高硬度、难熔金属碳化物(WC、TiC、TaC和NbC等)和金属黏结剂(Co、Ni)通过粉末冶金的方法制成。这些金属碳化物的种类和含量决定了刀具材料的硬度,称为硬质相。而金属黏结剂的含量决定刀具材料的强度和韧性,称为黏结相。硬质合金刀具材料的硬度、耐磨性和耐热性均优于高速钢,常温硬度可达HRA 89~94,在800~1000℃仍能进行切削,切削速度是高速钢的2~5倍,加工效率很高,应用非常广泛。但是硬质合金的强度和韧性较低,制造工艺性较差。表1-2所示为几种金属碳化物的性能。
表1-2 几种金属碳化物的性能

1)硬质合金的分类
硬质合金刀具材料以碳化钨基(WC)应用较为广泛,国际上将碳化钨基硬质合金分为三类:K类、P类和M类。其常用牌号、成分及性能如表1-3所示。
表1-3 常用WC基硬质合金的牌号、化学成分及物理性能

(1)K类硬质合金(WC—Co)。K类硬质合金相当于旧牌号YG类硬质合金。和其他硬质合金相比,强度高,韧性好,可制出比较锋利的切削刃且抗冲击性好,适用于加工短切屑的黑色金属(脆性材料,如铸铁)、有色金属和非金属材料,但硬度和耐磨性较差。常用牌号有K01、K10、K20、K30、K40(旧牌号有YG3、YG6X、YG6、YG8等),牌号中的数字越大,则含Co量越多,刀具材料的强度和韧性就越好,硬度和耐磨性越差。因此,K01适合于精加工,K10、K20适合于半精加工,K30、K40适合于粗加工。
(2)P类硬质合金(WC—TiC—Co)。P类硬质合金相当于旧牌号YT类硬质合金。与含钴量相同的K类硬质合金相比,P类硬质合金的硬度和耐磨性较好,强度和韧性较差,特别是具有较高的耐热性、较好的抗黏结和抗氧化能力,适合于加工长切屑的黑色金属,如钢料等塑性材料。常用牌号有P01、P10、P20、P30、P40等,牌号中的数字越大,则Co的含量越多,TiC的含量越少,刀具材料的硬度和耐磨性越差,强度和韧性越好。因此,P01适合于精加工,P10、P20适合于半精加工,P30、P40适合于粗加工。旧牌号有YT5、YT14、YT15和YT30等。
(3)M类硬质合金(WC—TiC—TaC(NbC)—Co)。M类硬质合金相当于旧牌号YW类硬质合金。在P类硬质合金中加入TaC(NbC),可提高其抗弯强度和冲击韧性,并提高硬质合金的高温强度和高温硬度,提高抗氧化能力。这类合金既可加工短切屑的黑色金属、有色金属,也可加工长切屑的黑色金属,因此又称做通用硬质合金。常用的有M10、M20、M30等牌号。牌号中的数字越大,则Co的含量越多,韧性越高而耐磨性越低,适合于粗加工;反之,适合于精加工。旧牌号有YW1、YW2等。
2)硬质合金的选用
正确选用硬质合金的牌号对刀具的切削性能有重要的影响。如上所述,K类硬质合金适于加工铸铁、有色金属和非金属材料;P类硬质合金适于加工钢料等塑性材料;M类硬质合金既可加工铸铁、有色金属,也可加工钢料。
硬质合金刀具材料选用时还应考虑以下几点:
① 粗加工时,切削力较大并伴随着切削振动,刀具易崩刃,应选用强度高、韧性好的刀具材料。
② 精加工时,切削速度往往较高,工件与刀具摩擦严重,应选用硬度高、耐磨性好的刀具材料。
③ 断续切削时,对刀具的冲击大,应选用强度高、韧性好的刀具材料。
④ 在切削淬硬钢、高强度钢、奥氏体钢和高温合金时,切削力集中在切削刃附近,易造成崩刃,不宜选用P类硬质合金,而用强度高、韧性好的K类硬质合金。
⑤ 在切削钛合金(如1Cr18Ni9Ti)时,若采用P类硬质合金,则由于硬质合金中的钛元素与工件中的钛元素之间的亲和力会使刀具产生冷焊现象,会使切削温度升高,加剧刀具磨损,这时应选用不含钛且导热性好的K类硬质合金刀具加工。
⑥ 由于硬质合金制造工艺性较差且强度和韧性较低(与合金工具钢相比),不适于制造形状复杂、尺寸大的刀具。
不同硬质合金的牌号及应用范围见表1-4。
表1-4 常用硬质合金的牌号及用途

3.其他刀具材料
1)陶瓷
常用的陶瓷材料有Al2O3基陶瓷和Si3N4基陶瓷两类。
(1)Al2O3基陶瓷。Al2O3基陶瓷又可分为纯氧化铝基陶瓷和复合氧化铝基陶瓷,其中复合氧化铝基陶瓷较为常用。
复合氧化铝基陶瓷是在Al2O3中加入高硬度、难熔碳化物(如WC、TiC)及金属添加剂(如Ni、Mo)经热压而成,其抗弯强度可达0.80GPa,硬度达到HRA 93~94。和硬质合金刀具材料相比,有以下特点:切削速度是硬质合金的2~5倍;耐热性很好,在1200℃时,硬质合金已丧失切削能力,而陶瓷此时的硬度可达HRA 80,仍能进行切削;有很高的化学稳定性,抗冷焊、扩散磨损的能力强;与金属材料的摩擦系数小,加工表面粗糙度较小;但强度和韧性相对较弱,抗冲击能力差。主要用于淬硬钢、冷硬铸铁等材料的半精加工和精加工。
(2)Si3N4基陶瓷。Si3N4基陶瓷是在Si3N4中加入TiC及Co等进行热压而成,其强度和韧性可达到1GPa以上,抗冲击性较好。同时,导热系数、线膨胀系数及耐热冲击性均优于Al2O3基陶瓷。
2)人造金刚石
人造金刚石是在高温高压条件下,借助催化剂由石墨转化而成的。它是目前已知最硬的刀具材料,其硬度可达HV 10000,是硬质合金硬度的6~8倍,可制成非常锋利的切削刃,且切削时不易产生积屑瘤,已加工表面粗糙度小。它既可以加工硬质合金、陶瓷、玻璃等高硬耐磨材料,也可加工有色金属及其合金。但也存在一些缺点:
(1)耐热性较差。当切削温度超过700~800℃时,碳原子即转化为石墨结构而丧失原有的硬度。
(2)不适于加工铁族材料。由于金刚石刀具材料中的碳元素与工件材料总的铁元素有很强的化学亲和性,在高温下碳元素极易产生扩散现象,使金刚石刀具表面石墨化,因此不适于加工铁族材料。
3)立方氮化硼
立方氮化硼是由较软的六方氮化硼在高温高压下加入催化剂转化而成的,其硬度仅次于金刚石,但热稳定性和化学稳定性均优于金刚石,可耐1500℃高温,可以用较高的切削速度实现对淬硬钢、冷硬铸铁、高温合金等材料的半精加工和精加工。