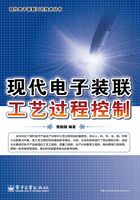
1.3.3 控制项目和方法
1.控制项目
实施正确的过程控制方法和选择正确的工艺装备,将有助于过程能力的稳定性和可重复性。过程控制是一系列仔细计划和周密设定的事件,当按照要求完成时,将突出地体现在以下事项中。
① 定义组装要求、组装过程、过程参数和过程品质计划;
② 存档组装程序;
③ 培训和签发上岗证;
④ 小批试生产;
⑤ 收集变量数据;
⑥ 计算过程能力;
⑦ 收集特性数据;
⑧ 开始批量生产;
⑨ 继续数据收集。
所有过程都有变量,统计过程控制可提供基本的工具,用于测量和监测过程变异(波动)。这种变异(波动)可分为两种类型:正常变异(波动)和异常变异(波动)。
正常变异(波动):亦称普通原因造成的波动,它是上述六大因素同时作用的随机波动(如设备的正常振动、刀具的正常磨损,测量的允许误差等)。普通原因变量是那些自然存在于一个稳定的和可重复的过程中,但这些波动综合起来对产品制造质量的影响并不太大,属于不可避免的波动,或称受控制的波动。
异常变异(波动):亦称特殊原因引发的波动,它是由系统原因作用引发的波动。这种变异是那些出现在由于特殊的原因(如没有符合已建立的过程参数)而缺乏控制能力的过程中的变异。异常波动对产品制造质量影响大,属于可以避免的波动,或称非控制的波动。
对于工艺过程控制中所出现的上述两种波动,要加以区别,分别进行控制。从掌握产品制造质量波动规律的角度来看,工艺过程控制的目的就是要做到维持正常的波动,消除异常的波动。
2.控制方法
数理统计方法是揭示波动规律和区别正常波动与异常波动的有力工具。工艺过程控制运用这种科学方法,从产品生产过程中无数变化的现象里,客观地抽取有用的数据,加以整理分析,找出其规律性,作为决定行动、采取措施的基础。
掌握发生波动规律的目的,就是要及时发现异常,找出影响系统的因素,发现潜在的隐患,防止问题再次发生。在产品制造中,质量的明显不良,犹如漂浮在海洋中冰山的尖顶,而潜在的不良则更大,往往占10倍以上,如图1.1所示。所以,工艺过程控制不仅要消除明显不良(如废品),更重要的是预测和探索发生不良的各种可能形式,找出潜在不良的发生原因,制定预防措施,消除质量隐患。

图1.1 明显不良与潜在不良