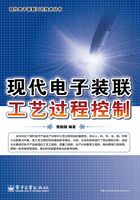
1.5.3 正确地分离变异原因
1.变异产生的原因
所有组装过程都有某些变异。统计过程控制(SPC)提供工具来检测过程和监测变异的产生原因:
① 普通原因:变异是在一个稳定的过程中固有的,即过程虽然不完美,但能满足可重复性和可检测性的关键要求。因此,一个过程是可重复的,其结果(如在X和R图表上所显示的)将反映的是操作员的变异而不是过程变异。
② 特殊原因:变异是特殊行动的结果,如执行错误(制定的文件过程没有遵循)而导致的变异。
统计过程控制应该用来稳定新的过程和改进现有的过程。基本过程控制必须基于从精确测量与观察所获得的事实。通常,收集与分析特性数据是被动反应的行动,而收集与分析变异数据则是更加积极的步骤。
2.描述变异的工具
过程控制依靠统计工具来测量、反馈和分析。众所周知的7个品质控制工具,是过程控制中的必要部分,因为它们可用来收集、显示和分析数据。
① 检查表:用于收集数据,也可显示数据。它简单、容易应用,并能有效地显示各种结果发生的频率。
② Pareto图:在柱状图上以下降的顺序显示缺陷种类,它对于把影响最大的缺陷从众多影响小的缺陷中分离出来是非常有用的。
③ 因果关系图:它将注意力集中在一个缺陷的最可能的原因和其潜在的相互关联性上面。注意力通常集中于人、机、法、料四个方面。
④ 流程图:使用标准化的标识来说明过程中的各种步骤。一个流程图清晰地说明从开始到结束的整个组装过程。
⑤ 柱状图:显示统计分布的条形/柱形图,它们在显示数据的分散性中有帮助,使得容易比较和分析。
⑥ 散布图:绘出无数的数据点来显示一个过程或产品的两个不同但又相关的特征之间的因果关系。
⑦ 控制图:在时间上和在上/下极限之间,显示特性(计数的)或变量(测量的)数据。可清楚地揭示可能影响过程能力的异常特性曲线、趋势和周期。有6种基本图形,即X图、R图、C图、U图、P图和Np图。
3.检查
某个级别的产品检查是必要的和所希望的。可是,大批量的检查不会改进产品质量。检查是一个筛选过程,尽力找出需要修理的不可接受的产品。应该避免大量检查,除非发生有必要100%筛选产品的事件。对于日常检查,应该基于一个合理的抽样计划。
定义检查方法与工具是重要的。检查应该当做一个过程来定义,像任何其他过程一样要制作出文件。事实上,检查可分成三个基本模式:
① 对每个PCBA板上的每个元件都检查(大批量检查);
② 对确认某个PCBA板上的特殊元件进行检查(减少的批量检查);
③ 检查特殊板上的特殊元件(抽样检查)。
PCBA的复杂性影响检查,因为每个PCBA板的元器件数量不断增加,对检查每个PCBA板上的每个元器件造成了更多困难。事实上,复杂性是批量检查不能改善产品质量的主要原因。
基于历史数据(Pareto图),要使显示更高缺陷率的元器件接受更频繁的检查。这个方法保证缺陷率高的元器件得到更多的关注。更少检查或完全不检查缺陷率低的元器件,以改善整个检查过程。
4.监测
检查是集中在产品上的,监测则是集中在过程上的。一个良好的过程品质计划应该包括上述两者。可是,长期目标应该是少检查和多监测,因为产品检查是被动性的(缺陷已经发生)而过程监测是积极性的(预防缺陷的产生),这是一个价值增值概念。
5.缺陷原因
有四种缺陷原因。
① 过程能力不良:意味着过程不能达到所希望的结果。例如,一台不能持续产生所希望的胶点尺寸的滴胶机。
② 过程执行不完善:在这里过程是可行的,但整体执行差。例如,机器操作员没有熟练地掌握操作规程。
③ 材料缺陷:如密间距元器件的引脚不能持续地满足共面性规格要求。
④ 可制造性设计存在问题:如PCB设计的组装工艺不良,造成组装困难。例如,基准点目标设计不正确。
6.过程控制误区
误区1:过程控制与统计过程控制(SPC)是相同的。过程控制是一个概念,SPC是一套支持该概念的工具。在SPC可以成为一个有效的工具之前,过程必须是稳定的和可重复的(但可能不是完美的)。
误区2:产生和显示的图形图表是过程控制。使用图表是用来分析和防止缺陷,而解决问题才是过程控制的部分。
误区3:大批量检查是一个有效的过程控制工具。批量检查不是过程控制,它只是将产品分类为可接受/不可接受的一种企图。过程品质计划应该是消除批量检查的需要。
7.FPY与DPMO
(1)FPY
一个经常使用的检测是第一次通过合格率(FPY)。通常SMT生产线的成功是以这个测量来评定的。工序顺序通常是从焊膏印刷到在线测试(ICT),包括焊膏印刷、滴胶、元器件贴装、再流焊接、通孔装配、波峰焊接、清洗和二次装配(压接连接器、模压、增加其他元件、导线等)。FPY的定义可描述为
FPY=(合格PCB数÷组装PCB的总数)×100%
(2)DPMO
FPY测量的一个问题是它只处理好PCB与坏PCB的数量,忽视了与坏PCB有联系的缺陷数量。当要调配资源来修理各种产品的现场问题时,由于每块PCB的缺陷数的差异,将带来返工与人力成本失去比例。例如,如果贴装机器的送料器转换不正确,或者焊膏印刷量不足,虽然只是影响部分PCB,但在短期内产生的缺陷可能比每小时平均PCB数高得多。因此,近来的发展趋势是:用一个更现实的度量标准来替代FPY。釆用的这种度量标准叫做百万机会的缺陷数(DPMO)。
DPMO提供一个将缺陷按照PCBA的复杂程度进行规范化的方法,即对于相同的DPMO,机会较少的PCB将会有较少的缺陷,而具有多机会的高复杂性组装,对于相同的DPMO将会有更多的缺陷。DPMO的定义为
DPMO=(缺陷数÷机会数)×106
式中的机会数等于元器件和零件数加上焊接点数(只对元器件而言,通路孔与测试点除外)。
DPMO与FPY的关系是反比例的,对一个固定的过程能力,随着机会数的增加,FPY将成比例地减少。
8.长期趋势-条形图
在一个度量上反映总趋势的一个方法是在时间上使用条形图,其理念是要通过简单的条形图来总结每年或每季度的数据,并在每月或每周的基础上显示不断更新的信息,该图表可以一目了然地提供一个长期的数据和所发生的历史事件。