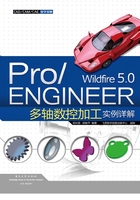
1.2 数控铣削加工基本知识
数控铣削是机械加工中最常用和最主要的数控加工方法之一,它除了能铣削普通铣床所能铣削的各种零件表面外,还能铣削普通铣床不能铣削的需要2~5轴坐标联动的各种平面轮廓和立体轮廓。
1.2.1 三轴数控加工原理
数控铣床的基本组成如图1-2所示。它由床身、立柱、主轴箱、工作台、滑鞍、滚珠丝杠、伺服电机、伺服装置、数控系统等组成。
床身用于支撑和连接机床各部件。主轴箱用于安装主轴。主轴下端的锥孔用于安装铣刀。当主轴箱内的主轴电机驱动主轴旋转时,铣刀能够切削工件。主轴箱还可沿立柱上的导轨在Z向移动,使刀具上升或下降。工作台用于安装工件或夹具。工作台可沿滑鞍上的导轨在X向移动,滑鞍可沿床身上的导轨在Y向移动,从而实现工件在X和Y向的移动。无论是X向、Y向,还是Z向的移动,都靠伺服电机驱动滚珠丝杠来实现。伺服装置用于驱动伺服电机。控制器用于输入零件加工程序和控制机床工作状态。控制电源用于向伺服装置和控制器供电。

图1-2 数控铣床结构
1.数控铣床的工作原理
根据零件形状、尺寸、精度和表面粗糙度等技术要求制定加工工艺,选择加工参数。通过手工编程或利用CAM软件自动编程,将编好的加工程序输入到控制器。控制器对加工程序处理后,向伺服装置传送指令。伺服装置向伺服电机发出控制信号。主轴电机使刀具旋转,X、Y和Z向的伺服电机控制刀具和工件按一定的轨迹相对运动,从而实现工件的切削。
2.数控铣床加工的特点
(1)用数控铣床加工零件,精度很稳定。如果忽略刀具的磨损,用同一程序加工出的零件具有相同的精度。
(2)数控铣床尤其适合加工形状比较复杂的零件,如各种模具等。
(3)数控铣床自动化程度很高,生产率高,适合加工批量较大的零件。
1.2.2 五轴数控加工原理
要学习五轴数控加工技术,首先需要了解数控加工的原理和特点,所以,本节介绍五轴数控加工的原理和应用范围、特点等。
五轴数控加工就是指在一台机床上至少有5个坐标轴(3个直线坐标和2个旋转坐标),而且可在计算机数控系统控制下同时协调运动进行加工。图1-3为典型的五轴联动数控机床。

图1-3 五轴联动数控机床
1.五轴数控加工特点
五轴数控加工中一台机床至少有5个坐标轴,可在计算机控制下联合工作,具有以下特点。
(1)可以加工一般三轴数控机床不能加工或很难在一次装夹完成加工的连续、平滑的自由曲面,如航空发动机和汽轮机的叶片、螺旋推进器等,如图1-4所示。如采用三轴数控机床加工,由于其刀具相对于工件的姿态在加工过程中不能改变,加工某些复杂曲面时,就可能产生干涉和欠加工。而用五轴加工由于刀具的轴线可随时调整,避免刀具与工件的干涉,并能一次装夹完成全部加工。

图1-4 典型复杂型面零件
(2)可以提高空间自由曲面的加工精度、质量和效率。例如三轴加工复杂曲面时,多采用球头铣刀,球头铣刀是以点接触,切削效率低,刀具/工件姿态在加工过程中不能调整,一般很难保证用球头上的最佳切削点(即球头上线速度最高点)进行切削。如果采用五轴机床加工,由于刀具/工件姿态在加工过程随时调整,可获得更高的切削速度、切削效率和切削质量。
(3)符合于工件一次装夹便可完成全部或大部分加工的机床特点。当前,为了进一步提高产品性能和质量,不仅像航空、航天产品和运载工具的现代产品,而且包括精密仪器、仪表、运动器械等产品的零件,都越来越多地采用整体材料铣成,而且其上面还有许多各式各样的复杂曲面和斜孔,如果采用三轴加工,必须经过多次定位安装才能完成,而采用五轴数控加工可一次装夹完成大部分的工作。
2.五轴数控加工机床
和三轴联动数控机床相比,五轴联动数控机床多了两个转动轴。但是在结构布置方面,往往不仅仅是在三轴联动数控机床上添加两个转动轴就可以的。按照主轴的位置关系可分为以下两大类。
1)立式五轴加工中心
如图1-5所示是工作台回转轴式,设置在床身上的工作台可以环绕X轴回转,定义为A轴,A轴一般工作范围为+30度至-120度。工作台的中间还设有一个回转台,在图示的位置上环绕Z轴回转,定义为C轴,C轴都是360度回转。这样通过A轴与C轴的组合,固定在工作台上的工件除了底面之外,其余的5个面都可以由立式主轴进行加工。A轴和C轴最小分度值一般为0.001度,这样又可以把工件细分成任意角度,加工出倾斜面、倾斜孔等。A轴和C轴如与X、Y、Z三直线轴实现联动,就可加工出复杂的空间曲面,当然这需要高档的数控系统、伺服系统及软件的支持。这种设置方式的优点是主轴的结构比较简单,主轴刚性非常好,制造成本比较低。但一般工作台不能设计太大,承重也较小,特别是当A轴回转大于等于90度时,工件切削时会对工作台带来很大的承载力矩。

图1-5 工作台回转的立式五轴加工中心
另一种是依靠立式主轴头的回转,如图1-6所示。主轴前端是一个回转头,能自行环绕Z轴360度,成为C轴,回转头上还带可环绕X轴旋转的A轴,一般可达±90度以上,实现上述同样的功能。这种设置方式的优点是主轴加工非常灵活,工作台也可以设计得非常大,客机庞大的机身、巨大的发动机壳都可以在这类加工中心上加工。

图1-6 主轴回转的立式五轴加工中心
2)卧式五轴加工中心
图1-7为传统的工作台回转轴式五轴加工中心,设置在床身上的工作台A轴一般工作范围为+20度至-100度。工作台的中间也设有一个回转台B轴,B轴可双向360度回转。这种卧式五轴加工中心的联动特性比较好,常用于加工大型叶轮的复杂曲面。回转轴也可配置圆光栅尺反馈,分度精度达到几秒,当然这种回转轴结构比较复杂,价格也昂贵。

图1-7 工作台回转的卧式五轴加工中心叶轮
从旋转轴和直线运动轴之间的关系来看,五轴联动数控机床的结构形式主要有:双旋转主轴头机床、双摆头轴头机床和一个旋转工作台一个旋转主轴头机床这样三大类,如图1-8至图1-10所示。

图1-8 双旋转主轴头机床

图1-9 双摆头主轴头机床

图1-10 一个旋转工作台一个旋转主轴头机床
1.2.3 控制轴和加工坐标系
进行数控加工首先要了解控制轴和加工坐标系的相关知识,下面加以简单介绍。
由数控系统控制的机床运动轴称为控制轴,如图1-11所示。数控机床通过各个移动件的运动产生刀具与工件之间的相对运动来实现切削加工。为了表示各移动件的移动方位和方向(机床坐标轴),在ISO标准中统一规定采用右手直角笛卡儿坐标系对机床的坐标系进行命名,直线轴用X、Y、Z表示,旋转轴用A、B、C分别表示绕X、Y、Z的旋转轴。

图1-11 数控系统的控制轴
确定机床坐标轴,一般是先确定Z轴,再确定X轴和Y轴。
1)确定Z轴
对于有主轴的机床,如车床、铣床等,则以机床主轴,其轴线方向作为Z轴方向。对于没有主轴的机床,如刨床,则以与装卡工件的工作台相垂直的直线作为Z轴方向。如果机床有几个主轴,则选择其中一个与机床工作台面相垂直的主轴作为主要主轴,并以它来确定Z轴方向。
2)确定X轴
X轴一般位于与工件安装面相平行的水平面内。对于机床主轴带动工件旋转的机床,如车床、磨床等,则在水平面内选定垂直于工件旋转轴线的方向为X轴,且刀具远离主轴轴线方向为X轴的正方向。对于机床主轴带动刀具旋转的机床,当主轴是水平的,如卧式铣床、卧式镗床等,则规定人面对主轴,选定主轴左侧方向为X轴正方向;当主轴是竖直时,如立式铣床、立式钻床等,则规定人面对主轴,选定主轴右侧方向为X轴正方向。对于无主轴的机床,如刨床,则选定切削方向为X轴正方向。
3)确定Y轴
Y轴方向可以根据已选定的Z、X轴方向,按右手直角坐标系来确定。
1.2.4 数控铣削加工工艺制定
1.零件数控加工工艺分析
加工工艺分析就是指对零件的加工顺序进行规划,其具体安排应该根据零件的结构、材料特性、夹紧定位、机床功能、加工部位的数量及安装次数等进行灵活划分,一般可根据“粗精加工”进行划分。
粗加工阶段:粗加工阶段是为了去除毛坯上大部分的余量,使毛坯在形状和尺寸上基本接近零件的成品状态,这个阶段最主要的问题是如何获得较高的生产率。
半精加工阶段:半精加工阶段是使零件的主要表面达到工艺规定的加工精度,并保留一定的精加工余量,为精加工做好准备。半精加工阶段一般安排在热处理之前进行,在这个阶段,可以将不影响零件使用性能和设计精度的零件次要表面加工完毕。
精加工阶段:精加工阶段的目的是保证加工零件达到设计图纸所规定的尺寸精度、技术要求和表面质量要求。零件精加工的余量都很小,主要考虑的问题是如何达到最高的加工精度和表面质量。
2.设置加工工艺参数
加工工艺参数的选择是数控加工关键因素之一,它直接影响到加工效率、刀具寿命或零件精度等问题。合理的选择切削用量要有丰富的实践经验才行,在数控编程时,只能凭借编程者的经验和刀具切削用量的推荐值初步确定,而最终的切削用量将根据重件数控程序的调试结果和实际加工情况来确定。
合理确定加工工艺参数的原则是:粗加工时,为了提高效率,在保证刀具、夹具和机床刚性足够的条件下,切削用量选择的顺序是:首先把切削深度选大一些,其次选择较大的进给量,然后选择适当的切削速度。精加工时,加工余量小,为了保证工件的表面粗糙度,尽可能增加切削速度,这时可适当减少进给量。
粗加工:粗加工是大体积切除工件材料,表面质量要求很低。工件表面粗糙度Ra要达到12.5~25um,可以取轴向切削深度为3~6mm,径向切深为2.5~5mm,为后续半精加工留1~2mm的加工余量。如果粗加工后直接精加工,则留0.5~1mm的加工余量。
半精加工:半精加工是把粗加工后的表面加工得光滑一点,同时切除凹角的残余材料,给精加工留厚度均匀的加工余量。半精加工后工件表面的粗糙度Ra要达到3.2~12.5um,轴向切削深度和径向切削深度可取1.5~2mm,给后续精加工留0.3~0.5mm的加工余量。
精加工:精加工是最后达到尺寸精度和表面粗糙度要求的加工。工件的表面粗糙度Ra要达0.8~3.2um,轴向切削深度可取0.5~1mm,径向切削深度可取0.3~0.5mm。
1.2.5 铣削加工刀具与材料
1.刀具材料
刀具材料对刀具使用寿命、加工效率、加工质量和加工成本都有很大影响,因此必须合理选择。常用的刀具材料包括以下几种。
1)高速钢
高速钢全称高速合金工具钢,也称为白钢,19世纪研制而成。高速钢是含有较多钨、钼、铬、钒等元素的高合金工具钢。具有较高的硬度(热处理硬度达HRC62~67)和耐热性(切削温度可达550℃~600℃),切削速度比碳素工具钢和合金工具钢高1~3倍(因此而得名),此刀具耐用度高10~40倍,甚至更多,可以加工从有色金属到高温合金的范围广泛的材料。
2)硬质合金
硬质合金是用高耐热性和高耐磨性的金属碳化物(碳化钨、碳化铁、碳化钽、碳化铌等)与金属粘结剂(钻、镍、铬等)在高温下烧结而成的粉末冶金制品。常用的硬质合金有钨钻类(YG类)、钨钛钴类(YT类)和通用型硬质合金(YW类)3类。
● 钨钻类硬质合金(YG类):主要由碳化钨和钻组成,抗弯强度和冲击韧性较好,不易崩刃,很适宜切削切屑呈崩碎状的铸铁等脆性材料;YG类硬质合金的刃磨性较好,刃口可以磨得较锋利,故切削有色金属及合金的效果也较好。
● 钨钛钴类硬质合金(YT类):主要由碳化钨、碳化钛和钴组成。由于YT类硬质合金的抗弯强度和冲击韧性较差,故主要用于切削切屑一般呈带状的普通碳钢及合金钢等塑性材料。
● 钨钛钽(铌)钴类硬质合金(YW类):在普通硬质合金中加入了碳化钽或碳化铌,从而提高了硬质合金的韧性和耐热性,使其具有较好的综合切削性能,主要用于不锈钢、耐热钢、高锰钢的加工,也适用于普通碳钢和铸铁的加工,因此被称为通用型硬质合金。
3)涂层刀具
涂层刀具是在韧性较好的硬质合金或高速钢刀具基体上,涂覆一薄层耐磨性高的难熔金属化合物而获得的。常用的涂层材料有碳化钛、氮化钛、氧化铝等。碳化钛的硬度比氮化钛高,抗磨损性能好,对于会产生剧烈磨损的刀具,碳化钛涂层较好。氮化钛与金属的亲和力小,润湿性能好,在容易产生粘结的条件下,氮化钛涂层较好。在高速切削产生大量热量的场合,以采用氧化铝涂层为好,因为氧化铝在高温下有良好的热稳定性能。
涂层硬质合金刀片的耐用度至少可提高1~3倍,涂层高速钢刀具的耐用度则可提高2~10倍。加工材料的硬度愈高,则涂层刀具的效果愈好。
4)陶瓷材料
陶瓷材料是以氧化铝为主要成分,经压制成形后烧结而成的一种刀具材料。它的硬度可达到HRA91~95,在1200℃的切削温度下仍可保持HRA80的硬度。另外,它的化学惰性大,摩擦系数小,耐磨性好,加工钢件时的寿命为硬质合金的10~12倍。其最大缺点是脆性大,抗弯强度和冲击韧性低。因此,它主要用于半精加工和精加工高硬度、高强度钢和冷硬铸铁等材料。常用的陶瓷刀具材料有氧化铝陶瓷、复合氧化铝陶瓷及复合氧化硅陶瓷等。
5)人造金刚石
人造金刚石是通过合金触媒的作用,在高温高压下由石墨转化而成的。人造金刚石具有极高的硬度(显微硬度可达HV10000)和耐磨性,其摩擦系数小,切削刃可以做得非常锋利。因此,用人造金刚石做刀具可以获得很高的加工表面质量,多用于在高速下精细车削或镗削有色金属及非金属材料。尤其是用它切削加工硬质合金、陶瓷、高硅铝合金及耐磨塑料等高硬度、高耐磨性的材料时,具有很大的优越性。
6)立方氮化硼(CBN)
立方氮化硼是由氮化硼在高温高压下加入催化剂转变而成的超硬刀具材料。它是20世纪70年代才发展起来的一种新型刀具材料,立方氮化硼的硬度很高(可达到HV8000~9000),并具有很高的热稳定性(在1370℃以上时才由立方晶体转变为六面晶体而开始软化),它最大的优点是在高温(1200℃~1300℃)时也不易与钛族金属起反应。因此,它能胜任淬火钢、冷硬铸铁的粗车和精车,同时还能高速切削高温合金、热喷涂材料、硬质合金及其他难加工材料。
2.铣刀种类
数控加工中要选择合适的铣刀类型,刀具类型的选择直接影响到加工范围和加工质量,如图1-12所示。

图1-12 铣刀类型和加工范围
1)端铣刀
端铣刀是数控铣加工中最常用的一种铣刀,广泛用于加工平面类零件,图1-13是两种最常见的端铣刀。端铣刀除用其端刃铣削外,也常用其侧刃铣削,有时端刃、侧刃同时进行铣削,端铣刀也可称为圆柱铣刀。

图1-13 端铣刀
2)成型铣刀
成型铣刀一般都是为特定的工件或加工内容专门设计制造的,适用于加工平面类零件的特定形状(如角度面、凹槽面等),也适用于特形孔或台。图1-14是几种常用的成型铣刀。

图1-14 成型铣刀
3)球头铣刀
适用于加工空间曲面零件,有时也用于平面类零件较大的转接凹圆弧的补加工。图1-15是一种常见的球头铣刀。

图1-15 球头铣刀
1.2.6 切削用量的确定
数控切削用量主要包括“切削速度”、“进给速度”和“切削深度”等。合理选择切削用量的原则是:粗加工时,一般以提高生产率为主,但也应考虑经济性和加工成本;半精加工和精加工时,应在保证加工质量的前提下,兼顾切削效率、经济性和加工成本。具体数值应根据机床说明书切削用量手册,并结合经验而定。
1)进给速度
进给速度表示单位时间内刀具沿进给方向移动的距离,以vf表示。
vf应根据零件的加工精度和表面粗糙度要求及刀具和工件材料来选择。vf的增加也可以提高生产效率。加工表面粗糙度要求低时,vf可选择大些。在加工过程中,vf也可通过机床控制面板上的修调开关进行人工调整,但是最大进给速度要受到设备刚度和进给系统性能等的限制。
通常根据主轴转速、刀具材料、切削毛坯材料等因素,选择较大的进给率以提高加工效率,一般设定为300~600mm/min。
2)切削深度
切削时铣刀的端面和一个方向的侧面切入工件,端面切入工件的深度成为轴向切削深度,侧面切入工件的深度成为侧向切削深度。
在机床、工件和刀具刚度允许的情况下,背吃刀量就等于加工余量,这是提高生产率的一个有效措施。但是为了保证零件的加工精度和表面粗糙度,一般应留一定的余量进行精加工。在数控加工中,为保证零件必要的加工精度和表面粗糙度,建议留少量的余量(0.2~0.5mm),在最后的精加工中沿轮廓走一刀。粗加工时,除了留有必要的半精加工和精加工余量外,在工艺系统刚性允许的条件下,应以最少的次数完成粗加工。留给精加工的余量应大于零件的变形量和确保零件表面完整性。
3)切削速度
切削速度表示铣刀的圆周切线速度,也称为铣削速度,通常用主轴转速n表示。
提高切削速度也是提高生产率的一个措施,但切削速度与刀具耐用度的关系比较密切。随着切削速度的增大,刀具耐用度急剧下降,故切削速度的选择主要取决于刀具耐用度。
通常经验值高速钢Φ3~Φ16mm刀具,一般设置主轴转速为500~1800rpm,硬质合金刀具为1500~3000rpm(高速加工除外)。