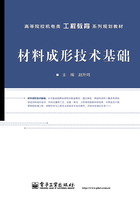
1.2铸件的凝固与收缩
浇入铸型中的合金液在冷却凝固过程中要发生结晶,同时伴随着收缩。凝固和收缩对铸件的质量影响很大,为了保证铸件质量,必须合理地控制铸件的凝固和收缩过程。
1.铸造合金的结晶
铸造合金的结晶也是通过晶核的形成和晶体的长大这两个过程来实现的。实际生产过程中,铸造合金的结晶大多以非均质方式形核。由于实际铸造合金中往往存在杂质,这样在液态铸造合金结晶时就会由一些外来的微小固态质点形成外来晶核,即非均质形核,也称为孕育(变质)处理。非均质形核所需能量较小,因而可以在较小的过冷度下获得较多的晶核数目,从而获得晶粒细小的铸件。
铸造合金的结晶与凝固条件有关,凝固条件不同,晶体形态会发生变化。铸型型壁处传热快,型壁表面又有促进形核的作用,这样达到结晶条件的那部分液体在型壁上就会产生大量晶核,在型壁“激冷”及液体合金热对流的综合作用下,形成一层很薄的等轴细晶区。与此同时,铸型温度升高,液体合金的冷却速度降低,过冷度减小,形核率降低,使那些与传热最快方向相反、与型壁垂直的晶核优先长大并进入液体合金,而其他方向上的晶核由于受相邻晶体的阻碍而生长较慢。此过程持续进行,就形成了向液体合金内部平行长大的柱状晶区。铸型心部,由于过冷度减小较大,温度梯度小,传热逐渐无方向性,晶体向各个方向均匀长大,即形成粗大的等轴晶区。
铸件的质量和力学性能主要取决于柱状晶和等轴晶所占比例的大小。铸件结晶后是以等轴晶为主还是以柱状晶为主,除了与铸造合金的成分有关,还与铸件的凝固方式有关。
2.铸件的凝固方式
铸件的成形过程是液态金属在铸型中的凝固过程。合金的凝固方式对铸件的质量、性能及铸造工艺等都有极大的影响。
铸件在凝固过程中,其断面一般存在3 个区域,即固相区、凝固区和液相区,其中液相和固相并存的凝固区对铸件质量影响最大。通常,根据凝固区的宽窄将铸件的凝固方式分为逐层凝固、中间凝固和糊状凝固三种方式,如图1-3所示。

图1-3 铸件的凝固方式
1)逐层凝固
纯金属或共晶成分的合金在凝固过程中因不存在液、固相并存的凝固区,故断面上外层的固体和内层的液体由一条界线(凝固前沿)清楚地分开,如图1-3(a)所示。随着温度的下降,固体层不断加厚,液体层不断减小,直到中心层全部凝固。这种凝固方式称为逐层凝固。逐层凝固得到的晶体主要是柱状晶。灰铸铁、铝硅合金、硅黄铜及低碳钢等倾向于这种凝固方式。
2)糊状凝固
当合金的结晶温度范围很宽且铸件断面温度分布较为平坦时,在凝固的某段时间内,铸件表面并不存在固体层,而液、固相并存的凝固区贯穿整个断面,如图1-3(c)所示。由于这种凝固方式与水泥凝固方式很相似,先成糊状而后固化,故称为糊状凝固。糊状凝固得到的晶体主要是等轴晶,由于在凝固过程中固态枝晶的析出会阻碍液态合金的流动,故充型能力较差,且难以补缩,往往会产生多种铸造缺陷。铝铜合金、锡青铜、球墨铸铁及高碳钢等,倾向于这种凝固方式。
3)中间凝固
介于逐层凝固和糊状凝固之间的凝固方式称为中间凝固,如图1-3(b)所示。中间凝固得到的晶体既有等轴晶,又有柱状晶,大多数合金都属于这种凝固方式。
铸件质量与其凝固方式密切相关。一般来说,逐层凝固时,液态合金的充型能力强,便于防止缩孔和缩松。糊状凝固时,充型能力较差,且难以补缩,难以获得致密的铸件。尽管大多数的合金都属于中间凝固,在铸造选材时,仍倾向于选择逐层凝固的合金,如灰铸铁。同时采用适当的工艺措施,减少铸造缺陷的形成,保证铸件质量。
3.铸造合金的收缩性
1)合金收缩的概念
合金在浇注、凝固直至冷却到室温的过程中体积或尺寸缩减的现象,称为收缩。收缩是合金固有的物理特性,但如果在铸造过程中不能对收缩进行控制,常常会导致铸件产生缩孔、缩松、变形和裂纹等缺陷。因此,必须研究合金的收缩规律及对铸件质量的影响。
合金的收缩量是用体积收缩率和线收缩率来表示的。当合金的温度自T0下降到T1时,体收缩率是以单位体积的相对变化量来表示的;线收缩率是以单位长度的相对变化量来表示的,即
体收缩率:

线收缩率:

式中,V0、V1为合金在T0、T1时的体积;L0、L1为合金在T0、T1时的长度(cm);aV、aL为合金在T0至T1温度范围内的体收缩系数和线收缩系数(1/℃)。
金属从液态冷却到室温要经历三个相互联系的收缩阶段,如图1-4所示。

图1-4 合金收缩三阶段
(1)液态收缩 指合金从浇注温度(T浇)冷却到液相线温度(T液)过程中的收缩。从式(1-1)可看出,浇注温度高,过热度(T浇-T液)大和收缩系数较大,都会使液态收缩率增加。
(2)凝固收缩 指合金从液相线(T液)到固相线(T固)之间凝固过程中的收缩。对于纯金属和共晶成分的合金,凝固期间的体收缩是由于状态的改变,与温度无关;具有结晶温度范围的合金,凝固收缩由状态改变和温度下降两部分产生,结晶温度范围(T液-T固)越大,则凝固收缩越大。
液态收缩和凝固收缩使金属液体积缩小,一般表现为型内液面降低,是铸件产生缩孔和缩松的基本原因。
(3)固态收缩 指合金从固相线温度冷却到室温时的收缩。固态收缩通常直接表现为铸件外形尺寸的减小,故一般用线收缩率来表示。线收缩对铸件形状和尺寸精度影响很大,是铸造应力、变形和裂纹等缺陷产生的基本原因。
合金总的收缩率为上述三种收缩的和。对于不同的合金,有不同的收缩率。在常用铸造合金中,铸钢收缩率较大,而灰铸铁较小。这是由于灰铸铁中的碳在凝固过程中以石墨态析出的缘故。石墨的比容大,产生体积膨胀,部分抵消了合金的收缩。
2)影响合金收缩的因素
影响收缩的因素主要有化学成分、浇注温度、铸件结构和铸型条件等。
(1)化学成分 碳素钢的碳含量增加,其ε凝增加而ε固略减。灰铸铁中的碳、硅含量越高,其石墨化能力越强,故灰铸铁的收缩率越小;硫可阻碍石墨析出,使灰铸铁收缩率增大。表1-2所示的是几种铁碳合金的体积收缩率。
表1-2 几种铁碳合金的体积收缩率

(2)浇注温度 浇注温度越高,过热度越大,合金的ε液和总收缩率就越大。为减小合金液态收缩及氧化、吸气,并兼顾流动性,浇注温度一般控制在合金液相线温度以上50~150℃。
(3)铸件结构和铸型条件 铸件结构和铸型条件对收缩的影响主要表现在使铸件收缩受阻。由于铸件壁厚不均匀,各部分冷却速度不同,收缩不一致,从而相互制约产生阻力;而铸型和型芯则直接阻碍收缩,从而产生机械阻力。铸件结构越复杂,铸型硬度越高,芯骨越粗大,铸件收缩时受阻越大,实际收缩率越小。因此,在设计和制造模样时,应根据合金的种类和铸件的受阻情况,综合考虑收缩率的影响。