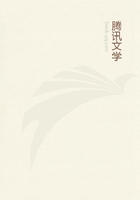
第28章
A 66-inch diameter vertical boring-mill was the first machine used in making these experiments, and large locomotive tires, made out of hard steel of uniform quality, were day after day cut up into chips in gradually learning how to make, shape, and use the cutting tools so that they would do faster work.At the end of six months sufficient practical information had been obtained to far more than repay the cost of materials and wages which had been expended in experimenting.And yet the comparatively small number of experiments which had been made served principally to make it clear that the actual knowledge attained was but a small fraction of that which still remained to be developed, and which was badly needed by us, in our daily attempt to direct and help the machinists in their tasks.
Experiments in this field were carried on, with occasional interruption, through a period of about 26 years, in the course of which ten different experimental machines were especially fitted up to do this work.Between 30,000 and 50,000 experiments were carefully recorded, and many other experiments were made, of which no record was kept.In studying these laws more than 800,000 pounds of steel and iron was cut up into chips with the experimental tools, and it is estimated that from $150,000 to $200,000 was spent in the investigation.
Work of this character is intensely interesting to any one who has any love for scientific research.For the purpose of this paper, however, it should be fully appreciated that the motive power which kept these experiments going through many years, and which supplied the money and the opportunity for their accomplishment, was not an abstract search after scientific knowledge, but was the very practical fact that we lacked the exact information which was needed every day, in order to help our machinists to do their work in the best way and in the quickest time.
All of these experiments were made to enable us to answer correctly the two questions which face every machinist each time that he does a piece of work in a metal-cutting machine, such as a lathe, planer, drill press, or milling machine.These two questions are: In order to do the work in the quickest time, At what cutting speed shall I run my machine? And What feed shall I use?
They sound so simple that they would appear to call for merely the trained judgment of any good mechanic.In fact, however, after working 26 years, it has been found that the answer in every case involves the solution of an intricate mathematical problem, in which the effect of twelve independent variables must be determined.
Each of the twelve following variables has an important effect upon the answer.The figures which are given with each of the variables represent the effect of this element upon the cutting speed.For example, after the first variable (A) we quote, "The proportion is as 1 in the case of semi-hardened steel or chilled iron to 100 in the case of a very soft, low-carbon steel." The meaning of this quotation is that soft steel can be cut 100 times as fast as the hard steel or chilled iron.The ratios which are given, then, after each of these elements, indicate the wide range of judgment which practically every machinist has been called upon to exercise in the past in determining the best speed at which to run the machine and the best feed to use.
(A) The quality of the metal which is to be cut; i.e., its hardness or other qualities which affect the cutting speed.The proportion is as 1 in the case of semi-hardened steel or chilled iron to 100 in the case of very soft, low-carbon steel.
(B) The chemical composition of the steel from which the tool is made, and the heat treatment of the tool.The proportion is as 1 in tools made from tempered carbon steel to 7 in the best high-speed tools.
(C) The thickness of the shaving, or, the thickness of the spiral strip or band of metal which is to be removed by the tool.The proportion is as 1 with thickness of shaving 3/16 of an inch to 3 1/2 with thickness of shaving 1/64 of an inch.
(D) The shape or contour of the cutting edge of the tool.The proportion is as 1 in a thread tool to 6 in a broad-nosed cutting tool.
(E) Whether a copious stream of water or other cooling medium is used on the tool.The proportion is as 1 for tool running dry to 1.41 for tool cooled by a copious stream of water.
(F) The depth of the cut.The proportion is as 1 with 1/2-inch depth of cut to 1.36 with 1/8-inch depth of cut.
(G) The duration of the cut, i.e., the time which a tool must last under pressure of the shaving without being reground.The proportion is as 1 when tool is to be ground every 1 1/2 hours to 1.20 when tool is to be ground every 20 minutes.
(H) The lip and clearance angles of the tool.The proportion is as 1 with lip angle of 68 degrees to 1.023 with lip angle of 61 degrees.
(J) The elasticity of the work and of the tool on account of producing chatter.The proportion is as 1 with tool chattering to 1.15 with tool running smoothly.
(K) The diameter of the casting or forging which is being cut.
(L) The pressure of the chip or shaving upon the cutting surface of the tool.
(M) The pulling power and the speed and feed changes of the machine.
It may seem preposterous to many people that it should have required a period of 26 years to investigate the effect of these twelve variables upon the cutting speed of metals.To those, however, who have had personal experience as experimenters, it will be appreciated that the great difficulty of the problem lies in the fact that it contains so many variable elements.And in fact the great length of time consumed in making each single experiment was caused by the difficulty of holding eleven variables constant and uniform throughout the experiment, while the effect of the twelfth variable was being investigated.Holding the eleven variables constant was far more difficult than the investigation of the twelfth element.