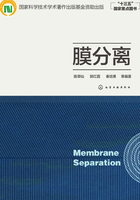
第2章 微滤
2.1 微滤技术简介
2.1.1 微滤分离原理及特点
(1)分离原理
微滤(microfiltration,简称MF)是利用微滤膜的“筛分”作用进行分离的膜过程,其分离的基本原理与普通过滤类似。如图2-1所示,在微滤膜两侧压力差作用下,原料液体(气体)中的尺寸小于膜孔的物质透过膜的微孔流到膜的下游侧,液体(气体)中大于膜孔的微粒被截留在膜的上游侧,从而实现溶液(气体)中悬浮粒子与溶剂(气体)的分离。膜的孔径大小与被截留物质的相对尺寸决定分离效果。由于被分离粒子的直径一般大于0.1μm,因此,又被称为精密过滤。与常规过滤相似,微滤过程滤液中微粒的浓度可以是10-6级的稀溶液,也可以是浓度达20%的浓浆液。由于微滤所分离的粒子通常远大于反渗透和超滤分离溶液中的溶质及大分子,基本属于固液分离,且微孔滤膜孔径相对较大,空隙率高,因而阻力小,可在0.01~0.2MPa的跨膜压力差下进行,其渗透通量远大于反渗透和超滤。

图2-1 微滤原理示意图
代表悬浮粒子及胶体;
代表水及小分子物质;
代表微生物、细胞
(2)微滤膜的截留作用机理
微滤分离机制复杂,影响因素较多,现有研究认为,微滤膜的分离机理多为筛孔分离过程,膜的结构对分离起决定性作用。此外,吸附、膜表面的化学性质和电性能等因素对分离也有影响,这些也是微滤膜及其分离技术研究的主要方向之一。如图2-2所示,对于固液分离的微滤过程,其截留作用主要有几种。

图2-2 微滤过程的截留作用
①机械截留作用 微滤膜将尺寸大于其孔径的固体颗粒或颗粒聚集体截留,而液体和尺寸小于膜孔径的组分可以透过膜,即筛分作用。
②吸附截留作用 Pusch等认为,除了要考虑孔径因素外,还要考虑微滤膜表面通过物理或化学吸附作用,将尺寸小于其孔径的固体颗粒截留。
③架桥作用 固体颗粒在膜的微孔入口处因架桥作用而被截留。
④孔内部截留作用 孔内部截留作用主要是由于膜孔的弯曲而将微粒截留在膜的内部而不是在膜的表面。Davis等研究表明,弯曲孔膜能够截留比其标称孔径小得多的胶体,而柱状孔膜对小于其孔径的胶体粒子截留要少得多。所以,需要尽可能除去悬浮液中的所有颗粒时,弯曲孔膜相对柱状孔膜更有效。但是,柱状膜用于悬浮液中颗粒的分级较弯曲孔膜更有效。
⑤静电截留 为了分离悬浮液中的带电颗粒,可采用带相反电荷的微滤膜,这样就可以用孔径比被分离尺寸大许多的微滤膜进行,既可达到预期分离效果,又可增加通量。通常情况下,很多颗粒带有负电荷,则宜采用带正电荷的微滤膜。例如,孔径为0.2μm带正电荷的尼龙微滤膜对水中的热原的去除率大于95%,而孔径0.22μm的不带电荷的醋酸纤维微孔膜对热原的去除效果则不理想。
(3)微滤的特点
与机械过滤相比,微滤过程有以下几个特点:
①过滤精度高,微滤膜的孔径比较均匀,呈正态分布,尺寸大的孔的孔径与平均孔径之比一般为3~4,截留精度高。
②通量大,由于微滤膜的孔隙率高,在同等过滤精度下,流体的过滤速率可比常规过滤介质快几十倍。
③膜厚度小,吸附少,微滤膜的厚度只有10~100μm,对过滤对象的吸附量远远小于传统的机械过滤介质,可以大大减少物料(尤其是贵重物料)的吸附损失,但膜表面吸附的积累形成的膜污染是通量降低的主要因素。
④无介质脱落,不产生二次污染,微滤膜为连续的整体结构,可避免一般机械过滤介质容易产生卸载和滤材脱落的问题,该特点使微滤膜的应用领域更加广泛。
⑤颗粒容纳量小,易堵塞,微滤膜内部的比表面积小,颗粒容纳量小,易被物料中与膜孔大小相近的微粒堵塞,这是微滤膜和含有微孔结构的分离膜存在的共性问题。
上述特点表明,微滤膜具有在气相、液相流体中截留细菌、固体微粒、有机胶体等杂质的作用,反映出微滤膜技术在净化、分离和浓缩等众多领域中的应用前景。
2.1.2 微滤膜结构及其表征、测定方法
(1)微滤膜孔结构、形貌及其表征
微滤膜按结构分有对称膜和非对称膜。
对称膜的孔结构有毛细管状的通孔型孔、曲孔状的网络型孔和狭缝型孔。通孔型孔如核孔膜,见图2-3,其膜孔呈圆柱状垂直通于膜面,孔长度均匀,对大于其孔径的微粒具有绝对过滤作用;网络型孔微观结构与开孔型的泡沫海绵类似,见图2-4,分布有孔径大于其名义过滤精度的孔,孔道呈不规则交错,这种膜不具有绝对过滤的作用;狭缝型孔,如2-5所示,是硬弹性高分子材料形成的垂直于应力方向平行排列的层状片晶,在拉伸过程中,片晶被拉开,片晶之间的无定形区产生相互贯通的裂纹状微孔结构。

图2-3 核孔膜表面电镜照片

图2-4 网络型孔膜电镜照片

图2-5 狭缝型孔膜电镜照片
非对称型膜是由细孔表皮层与大孔支撑层组成的复合结构形态,可以区分为整体不对称结构和组合不对称结构两大类。整体不对称膜可通过相转化法来制备,见图2-6,而组合不对称结构,是将一层均质的尽可能薄的聚合物涂到微孔结构上。

图2-6 具有整体型非对称微滤膜的电镜照片
微滤膜的微孔结构是膜分离效果或截留性能的决定因素,直接影响膜的分离效率和分离水平。一般地,微孔结构及形貌表征是通过扫描电子显微镜、透射电子显微镜等直接观察,以获得膜的表面、底面和断面的形态特征。其中,扫描电镜(SEM)法是表征微滤膜孔径结构最简捷的方法。由于扫描电镜的分辨率可达到10nm范围,微滤膜的孔径一般在0.1~10μm之间,因而,通过SEM观察膜表面和断面的形貌,可直接得到膜的表面与断面孔结构,可观测其表面、内部的孔径大小及分布的均匀性等。此外,原子力显微镜是一种新型膜孔表征方法,微孔滤膜不需要特殊处理,可直接观察,特别适合于聚合物材料微孔滤膜的孔结构测量。
(2)微滤膜的孔结构参数
微滤膜的孔结构参数包括膜的孔径、孔径分布、孔隙率及膜厚度。膜孔径又分为最大孔径及平均孔径。其中最大孔径定义为与微滤膜最大孔径等效的圆形毛细管直径。
①膜孔径及其孔径分布的测定 膜的孔径是微滤膜的重要孔结构参数之一,它直接影响微滤膜的分离效率的高低及透过通量大小,在实际应用中,需要根据所要求达到的分离、浓缩效果来选择适当孔径的膜。膜孔径包括最大孔径和平均孔径。
微滤膜的孔径测试方法很多,归纳起来大体可分为直接法和间接法两种。直接法就是采用电子显微扫描法直接观测到膜的几何结构,采用图像分析法来确定膜孔径的大小。间接测量法是根据多孔膜呈现的各种物理特性,利用实验测出各有关物理参数,并按照有关公式换算出孔径的。应该指出,即使对同一种微滤膜进行测定,不同方法测得的孔径也不完全相同,但它们之间存在一定的关系。因此,采用间接法测量时一般要告知孔径测试的方法。
直接法大多用来测量膜表面孔的大小,对于具有一定厚度或孔隙深度的多孔膜则采用间接测试方法。鉴于膜在使用时,总是依据膜的某些物理性质,因此间接法测定的膜孔数据与实际应用更为密切。
间接测试法有泡点法、压汞法、气相吸附法(BET法)、滤速法、气体渗透法等,其中,被广泛采用的方法为泡点法,本章重点介绍泡点法,其他方法可查阅相关文献、书籍。
泡点法(也称泡压法)是利用毛细管现象测量微滤膜最大孔径的一种方法。
当微滤膜的膜孔被某种已知表面张力的液体所润湿时,由于毛细吸附及表面张力的作用,液体被固定于膜孔内部,驱动这些液体透过膜孔的最小N2压力是表征膜孔尺寸的功能参数。利用这一原理来测定微滤膜孔径的方法即为泡点法。其测试装置如图2-7所示。

图2-7 泡点法测试装置
测试方法:将所测膜样品用预先选择的液体完全润湿后安装于膜样品检测器中,向被液体润湿的微滤膜样品一侧缓慢施加N2压力,当出现第一个气泡时即为通过膜上最大孔径的气泡。第一个气泡出现并引导连续出泡时的临界压力为“泡点”压力,利用泡点压力可计算出膜的最大孔径。
利用N2通过膜孔所需的压力与膜孔表面张力相平衡的原理,可以推导出膜孔径的计算公式。
式中,p为泡点压力,Pa;d为最大孔径,m;σ为润湿液体的表面张力,N/m;θ为润湿液体与孔壁之间的接触角。
由式(2-1),只需测定出气泡发生时对应的压力p,即可计算出微滤膜的最大孔径。
实验还可以测定气泡最多时对应的压力,计算出最小孔径。由最大孔径和最小孔径即可算出平均孔径,但这种计算值是粗略的。另外最大孔径和最小孔径还可以反映膜孔径的均匀性,二者之间相差越小,说明膜孔径越均匀,反之,膜孔径均匀性差。
泡点法测孔径实验简单易行,因此广泛用于产品质量控制和使用时的检验,但由于该法测出的孔径是假设膜孔具有圆形毛细孔的截面,因此有些大公司的产品样本中,在泡点计算公式中加上孔形修正系数κ,即
研究表明,κ值并不是一个常数,主要与膜材料及制膜方法有关。
当膜润湿液体与膜孔接触角为0°时,cosθ=1,此时
泡点法还可以用来测定孔径分布。
微滤膜具有孔径大小不同的孔,在泡点法测试中,气体通过膜上不同孔径时所需的压力也不同,膜孔径越小,所需压力越大。同时不同压力下,气体通过膜孔的流速也不同。根据描述流体通过毛细管作滞流流动的柏谡叶方程,可以得出气体流量与通过膜孔的N2压力之间的关系式:
式中,Q为透过膜的N2的体积流量,m3/s;p为透气压力,Pa;r为膜孔半径,m;μ为N2黏度,Pa·s;L为膜的厚度,m。
当压力为p1时,半径为r1的微孔有n1个可以透过气体,相应的N2流量为Q1,若压力由p1增至p2,此时又有孔径r1-r2范围内的n个微孔被打开,从而使气体流量有相应的增加,其增加值为ΔQ,
式中,为p1和p2的平均值;
为r1和r2的平均值;n为压力从p1增到p2时被打开的微孔数。
孔径介于r1至r2的孔体积ΔV为
代入式整理得到
实验选择一系列被测膜孔径尺寸的区间,并逐个将区间端点值代入到式(2-4)中求出压力-流量(p-Q)曲线,如图2-8。表2-1为泡点法测孔径分布实验数据记录表。

图2-8 p-Q实验曲线
表2-1 泡点法测孔径分布实验数据记录表

由曲线求出ΔQ,按公式求出ΔV、、
、Δr,将
对
作图,就可以作出孔径分布曲线,如图2-9。

图2-9 孔径分布曲线
②膜孔隙率的测定 微滤膜的孔隙率是指膜内孔体积占膜总体积的比例。由于膜内的孔由开孔和闭孔两部分组成(如图2-10所示),因而,微滤膜的孔隙率有总孔隙率和有效孔隙率两种,其中,有效孔隙率也称开孔孔隙率。由于膜中的闭孔不能透过流体,只有开放孔的孔隙率才能透过流体,对膜速率(膜通量)有贡献,因此提高开放孔孔隙率是提高微滤膜通量的有效手段。

图2-10 具有开孔、闭孔的示意图
微滤膜的孔隙率大小还与微孔结构有关。网络孔膜的孔隙率较高,一般为35%~90%;柱状孔膜的孔隙率较低,一般小于10%。网络结构容易降低膜的强度,为保证膜的强度其厚度需要控制在40μm以上;柱状孔膜通常具有良好的强度,其膜厚可控制在15μm以下。一般地,微滤过程中膜通量与膜厚呈反比,这样,虽然柱状孔膜孔隙率较低,但仍可具有较高的通量。
常用的孔隙率测定方法有体积重量法、干湿膜重量法和压汞法。本书介绍前两种方法,压汞法要采用压汞仪进行测量,请参考相关文献。
a.体积重量法。根据膜的表观密度(ρ0)和膜材料的密度(ρ1),可由式(2-8)求得孔隙率ε。计算公式如下:
式中 ——微孔滤膜的表观密度,g/cm3;
——制膜材料的真密度,g/cm3;
——孔隙率,即滤膜中的微孔总体积与微孔滤膜体积的百分比,
为总孔隙率。
b.干湿膜重量法。先测定干膜的质量W1,然后将干膜浸入能润湿膜材料的液体()中,取出后擦干称重W2,按下式计算开孔孔隙率。
式中,V为膜的表观体积。
操作时,对湿膜的处理,既不能让湿膜表面有水,也不能将膜孔内的水析出。
③膜厚度测定 微孔滤膜的厚度测定通常是采用0.01mm的螺旋千分尺进行,以稍有接触为限。比较严格的方法是用薄膜测厚仪测定,这种测厚仪的优点是可使样品统一承受某一固定压强(如0.098MPa),由此得到比较精确的结果。
2.1.3 膜性能评价指标
(1)过滤速率
过滤速率主要采用恒压连续过滤装置测定液体在一定温度和压力下的透过速率,为单位时间单位膜面积上透过的液体体积。
式中 ——过滤速率,L/(m2·h);
V——透过液的体积,L;
A——膜的有效面积,m2;
t——过滤时间,h。
(2)过滤效率
过滤效率为料液中杂质被去除的百分比。理论上标定过滤效率最简单的办法就是通过计数原料液及透过液的颗粒数。在实际中有几种表示效率的方法:
式中,为料液中颗粒质量;
为透过液中颗粒质量。
式中,为料液的浊度;
为透过液的浊度。
这两种方法只能宏观地给出检测范围内所有颗粒的过滤效率,无法标定某个特定尺寸颗粒的效率。
近年来所出现的高精度激光颗粒计数仪有可能测得一个很窄分布的颗粒数,计算过滤效率,并有可能制定比较科学的测试标准。例如,采用贝克曼库尔特LS 13 320系列激光粒度分析仪可测量从0.4~2000μm范围的粒度。