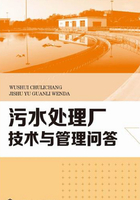
第二节 污水处理厂的生产操作管理
67.初次沉淀池运行管理中的关注重点有哪些方面?
初次沉淀池的工艺控制节点可概括为:一进一出二截留。一进是指进水;一出是指出水;二截留是指水面的浮渣和池底的污泥。在运行管理中,抓住这四个节点就抓住了工艺控制的主动权。
68.初次沉淀池的进水如何控制管理?
初次沉淀池的运行管理从进水管理开始。进水管理关注以下几方面。
(1)进水管理从配水管理开始。一般来讲,污水处理厂规模越大,初沉池的数量越多。各个初沉池的进水量通常由配水井调节。各个初沉池的进水量分配,不但要考虑沉淀效果,还需要兼顾考虑各池的排泥情况,不可片面追求配水平均。这是因为各池的排泥管线路径不同、水力损失不同,所以各池的排泥能力也随之不尽相同,如果各池的配水量片面追求相同,可能会造成个别池每次排泥都不能排净,积累而造成排泥管频繁堵塞或出水SS恶化。
(2)进水管理应该对水质进行监测,常规项目和频次见表2-5。
表2-5 初沉池水质监测频次

SS的进出水监测是最重要的性能分析指标,初沉池的各项去除率(如COD、BOD5)大部分都是以去除SS的方式来实现的。
由于进水水质不同以及污水处理工艺的不同,进水中可能有因管线过长而腐败的污泥或回流的生化污泥,腐败污泥因细碎而不易沉淀,回流污泥因气泡而上浮。通过长期分析统计初沉池的SS去除率可以掌握正常运行时的波动范围,一旦数据明显偏低,能够立即提示管理人员查找原因。
(3)进水量的监测。对于一个运行中的初沉池,进水量决定了表面负荷和水力停留时间,也决定了流速。过大的流速,不但不利于悬浮物的沉降,还可能冲起已经沉淀的污泥,引起出水SS恶化。
(4)投加絮凝剂是提高SS去除率的有效手段。
69.初次沉淀池的出水SS升高的因素有哪些?
易引起出水SS升高的原因见表2-6。
表2-6 初次沉淀池的出水SS升高的原因

70.初次沉淀池的排泥如何管理?
排泥首先要保证池内泥层高度在合理范围内、已经沉淀的污泥不会被水流再次冲起。其次要保证污泥排出的通畅。然后要统筹考虑这些因素。
(1)各池的进水量。进水量大,污泥多,排泥时间要长或频次要快。
(2)各池的排泥管线的水力损失。管线长度、管径、转弯数量、液位差等都会对排泥通畅度产生影响,要根据不同情况对排泥时间和频次进行不同安排,或对配水比例进行调整。
(3)污泥去向不同,排泥方式也不尽相同。如污泥送往浓缩池,初沉池排泥要尽量排净;如送往消化池,则要根据消化池的投配率、池内污泥浓度等因素统筹考虑。如消化池内污泥浓度高,可以延长初沉池排泥时间,多向消化池排入低浓度的污泥混合液;如消化池污泥浓度低,可以缩短排泥时间,以提高污泥浓度。
排泥时间的确定可在确保排泥管线不堵塞的前提下,根据需要灵活安排。
(4)排泥时要查看排出的污泥浓度,应与池底污泥有大致的对应关系。发现排泥浓度明显低于池底污泥时,要考虑池底排泥管口被砂石等杂质淤塞的可能。
(5)排泥口、排泥管及阀门长期运行会沉积砂石、生长结晶或挂着纤维而影响过流甚至堵塞,应定期用逆向水流或气流进行冲洗。
71.初次沉淀池刮泥机运行时需要注意哪些方面?
(1)根据初次沉淀池的形式及刮泥机的形式,确定刮泥方式、刮泥周期的长短。避免沉积污泥停留时间过长造成浮泥,或刮泥过于频繁或刮泥太快扰动已下沉的污泥。
(2)如果水面上有上浮污泥,可注意观察污泥上浮点是否有规律可循,以判断是否有刮板损坏。
(3)平流池刮泥机要检查刮板、导轨和链条的磨损情况,及时修理和更换损坏部位。辐流池刮泥机巡检时要重点检查动力装置和传动机构;中心驱动型的更要经常检查减速机,泥量多时易对其造成损伤。
(4)每年要停水放空检修沉淀池和刮泥机。出水堰、导流筒、池底及壁、刮板、桁架、水下行走轮、动力及传动机构、中心轴承、除渣装置等都要仔细检查和修理。
(5)轨道和走轮是每日巡检的必查项目。特别是北方冬季,轨道易有冰霜雪,要安装清除装置。北方地区不宜选用胶轮式刮泥机,由于四季温差太大,胶轮和轨道经常损坏,更换和修复需要一笔不小的费用;而且轨道宽,冬季清除冰雪特别困难,耗费人力物力。
72.除渣装置应注意哪些问题?
(1)排渣斗(堰)的安装高度及坡度要适宜。太高太陡,则刮渣板不易把浮渣刮送进排渣口,且水难以流进排渣斗,不能推动浮渣的移动;太低,则排渣斗进水量过大。
(2)平流池的浮渣去除相对于辐流池较为容易,可将去除槽改为螺旋输送机,定时启动即可把浮渣排到车内。辐流池受高程控制,排渣斗经过管道连接的排渣井多在地下,清理不易。目前多数设计是把排渣井下水又输送到总进水端,而未对井中的浮渣设置机械去除。可用筛网制作一个滤筐放置在井中,井上安吊架用电动葫芦起降,定期吊起清除。
73.带式污泥脱水机管理的重点有哪些?
带式机运行管理的重点有如下几点:污泥浓度、絮凝剂浓度及质量、污泥和絮凝剂的比例和混合、重力脱水段的分离效果、压榨段的压榨效果、污泥的剥离、滤带张紧和调偏、滤带冲洗效果等。
74.进入带式污泥脱水机的污泥浓度有何要求?
一般来讲,设有浓缩池的,污泥浓度应在30~50g/L之间。浓度太低,絮凝效果差,浪费絮凝剂;浓度太高,一是泥药混合不易,二是可能造成浓缩池排泥不畅。二级消化池排出的污泥,因其不搅拌,浓度基本也在30~50g/L之间。近年来,针对小型污水处理装置没有浓缩池的情况,设计推出了一些带有浓缩机构的一体机,独特之处是在污泥进入重力脱水区前段,采用转鼓离心浓缩机,先将絮凝后的污泥进行泥水分离,以减轻脱水区后段的工作负荷。
75.污泥脱水处理的常用药剂有哪些?
污泥处理目前常用的絮凝剂主要是无机高分子絮凝剂和有机高分子絮凝剂。无机高分子絮凝剂有聚合氯化铝(PAC)、聚硫氯化铝(PACS)、聚合硫酸铝(PAS)、聚合氯化铁(PFC)、聚合硫酸铁(PFS)等。使用无机高分子絮凝剂,需认真对待其对设备的腐蚀问题。
有机高分子絮凝剂分为天然和人工合成两大类。天然高分子絮凝剂有淀粉类、多聚糖类、蛋白质类、壳聚糖类;人工合成高分子絮凝剂应用较多的是聚丙烯酰胺(PAM)及其衍生物,分为阳离子型、阴离子型、非离子型和两性离子型。
阳离子型和两性离子型的技术指标有含固量、分子量、离子度。阴离子型、非离子型的技术指标有含固量、分子量、水解度。
此外,还有以铝盐和铁盐为代表的无机低分子药剂,多作为助凝剂或混凝剂,在污水处理的预处理阶段投加,以提高悬浮物的沉淀效果。
76.污泥脱水处理污泥和药剂的混合絮凝的方式有哪些?
常用的方式有管道混合、管道混合器混合、折板式混合器混合、机械搅拌式混合。单独使用管道混合一般不能达到较好效果,需与其他方式组合使用。使用管道混合器混合,要求污泥中不能含有纤维状物质,否则极易堵塞。一般来讲,只要带式机的重力脱水段足够长,管道混合结合折板式混合器混合足以满足带式机的要求,除非黏度较大等特殊泥质。机械搅拌式混合,非特殊泥质和特殊机型尽量不要采用,原因一是维护修理比较麻烦;二是由于搅拌强度难以控制调节,随着污泥浓度的变化,搅拌效果时好时坏,有时是混合不足,有时是把已形成的絮凝体破坏。
77.对于带式污泥脱水机如何根据重力脱水段的现象判断运行效果?
重力脱水段是带式机最基本的工作阶段,污泥脱水的最终效果基本决定于此。此段效果好,则最终效果也好;反之亦然。观察此段的现象,就可基本判断和解决带式机运行的绝大多数问题。从泥药混合器中流出的污泥接触到上滤带后,经布料器大致分配,应在滤带行走0.3~0.5m的距离即基本失去流动性,絮凝体形状非常明显,泥水分离界限分明,大量滤液透过上滤带滴落到接水盘内,在上滤带转向时,污泥从上滤带跌落到下滤带时,较少有溅起,这种情况表明前部各项指标(污泥浓度、絮凝剂浓度及质量、污泥和絮凝剂的比例和混合)合格,滤带冲洗干净,承托性和透过性好。相关现象分析见表2-7。
表2-7 重力脱水段现象分析

另外,根据实践运行对比,重力脱水段以滤带水平行走样式为宜,不宜选用有坡度的设备。
78.带式污泥脱水机楔形段的作用是什么?
一般来讲,带式机或长或短都有楔形段,楔形段是两条滤带逐渐靠近,完成对污泥的包夹,在此段污泥受力不大,脱水量极小。主要任务是使污泥进一步失去流动性,并且不被挤出滤带边缘。
79.带式污泥脱水机张紧压和张紧气缸对脱水效果有何影响?
滤带能够正常发挥作用的前提是,有足够的拉力使其保持一定的绷紧度,必须能够承托住全部的泥水载荷而不产生明显凹陷或打滑。拉力的来源,就是由张紧压和气缸联合提供的张紧力。张紧力计算公式如下:
F=PA
式中,F为张紧力;P为张紧压;A为气缸的截面面积。
拉力由双侧气缸提供,为了减小对气源的要求,气缸的内径要尽量大,一般缸径为160mm的气缸,气压在0.3~0.4MPa就可满足需要。
足够的拉力,还要能保持滤带的孔隙度,有利于滤液的透过。
在挤压段,挤压力完全来源于滤带的拉力。托辊两侧滤带的拉力产生的合力与托辊的反作用力形成了对污泥的挤压。托辊及两侧滤带如图2-17所示。

图2-17 托辊及两侧滤带
在图2-17中,托辊A处污泥受力要小于托辊B处,因为托辊A两侧滤带夹角大,托辊B两侧滤带夹角小,托辊A处两侧滤带形成的合力要小于托辊B。
滤带张力太大,会导致在楔形区或挤压区污泥从滤带两侧被挤出。滤带张力太小,不能产生足够的压榨力和剪切力,使带式污泥脱水机脱水泥饼的含固率下降,还可能导致滤带打滑或褶皱。
80.如何选择带式污泥脱水机滤带?
目前滤带的材质、编织方式和接头的方法很多。不同的泥质对滤带样式的要求不同,要选择适宜的滤带。
首先,要能使泥水分离迅速,透水性强,滤带不是编织得越密越好,更不是价格越高越好。选择滤带要经过试验,泥水分离迅速,滤液较清澈的即可。如果污泥中含有颗粒物,滤带的网眼孔径要小于颗粒物,否则滤带网眼会很快堵塞,而且极难冲洗。
其次,要韧性好,耐酸碱,强度高,使用寿命长,特别是要容易冲洗。
再次,滤带的接缝方式以插接式为宜,插接式接缝浑然一体,滤带整体运转性能一致,不会产生卡勾式连接在卡勾处污泥截断的情况。另外,插接式接缝对滤带、剥泥板、辊的磨损较小,卡勾对剥泥板的磨损要多加注意。
81.带式污泥脱水机对调偏有何要求?
调偏良好的带式机,在剥泥板处观察,滤带距托辊边沿的距离应大致相等,且两条滤带没有较大错位,滤带调偏气缸能动作,灵活,能起到调偏作用。上下滤带不能错位过大,应控制在2cm以内。这是滤带的较理想状态。在调试阶段,就要观察滤带的行走情况,是否经常向某一侧跑偏,甚至无法纠正而被迫停机;或者自动调偏机构做出调偏动作后,长时间保持不变。如果有此现象,就要对转向辊进行调整。一般来讲,不论上带还是下带,一定都有一个滤带在该辊进行大角度转折的转向辊,该辊的两侧基座螺栓孔是条形的,可以沿着滤带行走方向前后移动调整螺栓。可根据滤带的张紧情况和跑偏情况,调整单侧或双侧基座,一般调整位移以mm计。调整好的滤带,基本不出现偏移,自动调偏机构很长时间才需要做出调整动作,理想状态,可以超过半小时不需要调偏。新带式机和滤带长时间使用出现变形时,需要进行上述调整。
另外,根据运行经验,调偏气缸的气压一般应稍高于张紧压。
82.如何确定带式污泥脱水机的带速、张紧压?
带式机的带速、张紧压一般应根据需要处理的污泥量和泥饼含水率来调节。带速慢、张紧压高,出泥的含水率低,处理的污泥量少。带速快、张紧压低,处理的污泥量大,泥饼含水率高。可根据每小时需处理的污泥量,选择能使泥饼含水率达到要求的带速和张紧压。带速和张紧压可以只调整一项,也可两项都调整。基本要求是带速要满足污泥不被从滤带两端挤出,带速越快,泥幅越窄;张紧压要满足滤带不出现明显凹陷、不打滑、能调偏。对于某一种特定的污泥来说,存在最佳带速和张紧压控制范围,在该范围内,脱水机既能保证一定的处理能力,又能得到高质量的泥饼,固体回收率也较高。高质量的泥饼,从实践经验看,具有以下特点:泥幅较宽,距滤带两侧边缘10~15cm;泥饼有一定厚度,在5~20mm之间,某些特殊污泥可能更厚;泥饼含水率通常在80%左右;泥饼易于从滤带剥离。
83.带式污泥脱水机脱水效果的评价指标有哪些?
评价带式机脱水效果,有两个主要指标:一个是泥饼含固量Cu;另一个是固体回收率η。
泥饼含固量的高低是评价脱水效果好坏的最重要指标,含固量越高,污泥体积越小,运输和处置越方便。
固体回收率是泥饼中的固体量占脱水污泥中总干固体量的百分比,用η表示。η越高,说明污泥脱水后转移到泥饼中的干固体越多,随滤液流失的干固体越少,脱水率越高。η可用下式计算:
式中,Cu为泥饼的含固量, %;Ce为滤液中的含固量, %;Co为脱水机进泥的含固量, %。
【例】 某浓缩污泥的含固量为3%,经脱水之后,实测泥饼的含固量为20%,脱水滤液的含固量为0.5%。试计算该脱水系统的固体回收率。
【解】 已有数据为Co=3%、Cu=20%、Ce=0.5%。
将Co、Cu、Ce代入上式,得:
η=20%(3%-0.5%)/[3%(20%-0.5%)]=85.47%
即该脱水系统的固体回收率为85.47%。
需用泥饼含固量和固体回收率两个指标同时评价脱水效果的好坏。只获得较高的泥饼含固量,而固体回收率很低,或者固体回收率很高,但泥饼含固量很低,都说明脱水效果不佳,应分析其原因。
根据运行实践,固体回收率的测定计算比较麻烦,通常用滤液含固量替代。滤液含固量低于0.5%即可认为脱水效果较好,因为浓缩池出水的含固量也不过如此,完全不必对脱水设备的滤液浓度太过苛求。
84.带式污泥脱水机有哪些原因会造成滤带堵塞?
滤带堵塞,水分无法滤出,使泥饼含水率上升或者污泥从滤带两端流出(挤出),使带式机不能正常运行。滤带堵塞的原因有滤带冲洗水压力低、滤带走速过快冲洗时间不足、滤带张力太小、进泥中细沙含量太多、絮凝剂投加过多使污泥黏度过大等。
85.如何选购带式污泥脱水机?
选购带式机,除基本的结构强度要求外,应从以下这些方面进行考查。
(1)主体结构防腐蚀性要好,带式机工况环境多数为高湿度,有酸碱性,腐蚀性强。
(2)主体框架梁柱间要有足够的距离,便于检修时拆卸和抽出托辊。
(3)张紧气缸缸径要足够大,气缸活塞要能双向运动,在停机后能将活塞收回气缸避免腐蚀。
(4)重力脱水段不能太短。
(5)挤压段的布局要合理,污泥受力要由小变大,即托辊两侧滤带的夹角要由大变小,辊径由大变小。
(6)接水盘的材质要耐腐蚀。
(7)轴承要防水,轴承最好不在托辊内,而在框架上,便于检查和维修。
(8)调偏气缸的设置位置,应在气缸动作时,能有效引起滤带的变形。
(9)托辊的中心轴,最好是通轴,即一根轴贯穿托辊,而不是只在辊两侧焊接轴头。重、长、粗的托辊更要注意,因易发生托辊单侧断裂故障。
(10)要有配套的泥药混合器。
(11)气路进口要安有气源处理三联件(必须包含油雾器),起调压、除湿、加油润滑作用,保证活塞伸缩灵活,延长气缸寿命。
86.在用离心污泥脱水机脱水时哪些参数会影响离心机的运行?
影响离心机运行效果的因素很多,并且各个因素又互相影响,因此处理效果是各个因素综合作用的结果,各项参数的调整应从脱水后泥饼最终处置方法所要求最佳泥饼含水率、固体回收率和经济性等因素综合考虑。
综合影响离心机的运行的各项因素,大致归纳为三方面的参数:一是污泥的性质、流量和浓度;二是絮凝剂的种类、质量和配制;三是离心机的运行参数调节。
87.离心污泥脱水机运行需要如何关注污泥的性质?
由于污水水质、水量和污水处理的工艺参数在不断变化,必然引起泥质的不断变化,如污泥浓度、污泥有机质含量、污泥密度、污泥颗粒规格、pH值等。这些变化都要影响到絮凝剂的使用和离心机的运行控制。要经常对污泥进行检测分析,特别是要重点关注污水的变化情况和污水处理工艺的调整,因为从前述变化传递到污泥的变化要有一定的时间差,这样会有更强的预见性,可以提前做出相应的准备。例如,污水中的SS减少,十几个小时后传递到浓缩池的变化是进泥SS降低、可沉降压缩的SS减少,如果离心机的进泥量不减少,那么浓缩池的泥层就在不断降低,污泥压缩时间不断减少,污泥浓度不断降低,最终会使离心机不出泥而出水;反映到离心机的运行,会发现差转速越来越小,如果搞不清原因,就会不断提高絮凝剂的投加量,造成浪费。
污泥浓度过低或过高均会消耗更多的絮凝剂,污泥浓度必须控制在一定的波动区间。
进泥中不能有大量的纤维状物质,否则容易导致设备堵塞、振动加大,影响稳定运行。这种污泥要先进行破碎切割处理。
88.离心污泥脱水机的进泥量如何控制?
在污泥浓度处于合理波动区间内,进泥量要考虑以下因素:一是对出泥含水率的要求;二是对絮凝剂单耗的要求。当絮凝剂投加比例一定的情况下,处理的泥量越大,固体回收率和泥饼含固量越低;反之,进泥量降低,则固体回收率和泥饼含固量将提高。当处理的泥量大时,如果对出泥含水率要求较严格,就要提高絮凝剂的投加比例。但泥量越大,对絮凝体的扰动越大,絮凝效果变差,即使加大投加比例,也可能达不到含水率的要求。进泥量过低,意味着电能的浪费。每台离心机都有其最佳进泥量的范围,对应着最佳的投药比例和最佳的技术经济效益。这必须通过实践来摸索、验证。
89.离心污泥脱水机对絮凝剂有何特殊要求?
离心机的泥药混合一般只有管道混合方式,且混合管道不长,泥药的混合多在离心机内高速旋转的状态下完成,所以,很多情况下,在絮凝剂选型烧杯试验中效果表现较好的药剂,在实际应用中效果并不一定好。絮凝剂的选型、质量要求、配制要求基本要在实践中确定。絮凝剂不但要能满足污泥的特性,还要满足离心机的工作特性,这是离心机和压力分离机型的很大不同。
絮凝剂的投加比例,要兼顾出泥的含水率和分离液的含固率。一味提高投加比例,对含水率的影响效果越来越小,远不及对分离液的含固率影响。从经济上考虑,得不偿失。
总结实践经验,在絮凝剂方面影响出泥含水率的最重要指标不是投加比例,而是絮凝剂的质量和配制浓度、配制质量。某一特定的泥质,会有特定的絮凝剂质量指标和浓度与其相对应,有最佳的处理效果。当然,由于污泥浓度不断变化,必须随之不断调节加药量,这时投加比例(从表面上看)可能是最大影响因素。
90.离心污泥脱水机有哪些参数可以进行调节?
离心机可以调节的参数有转鼓转速、差转速、液环层厚度。
91.离心污泥脱水机转鼓转速如何控制调节?
转速越大,离心力越大,有助于提高泥饼含固率。但转速过大会使污泥絮凝体被破坏,反而降低脱水效果。同时较高转速对材料的要求高,对机器的磨损增大,动力消耗、振动及噪声水平也会相应增加。离心机运行中,可以通过调节转速,以适应不同的泥质。一般来说,颗粒大、密度大,需要的转速低;颗粒小、密度小,需要的转速高,初沉池污泥需要的转速比活性污泥低。泥质稳定的情况下,提高转速,可提高脱水的固体回收率,提高分离液的清澈度。高转速会带来一系列的负面影响,除非必要,尽量不要采取高转速的运行方式,而应采取调节其他参数的方式。
92.离心污泥脱水机差转速如何控制调节?
差转速是指转鼓与螺旋的转速之差,即两者之间的相对转速。被分离出的污泥就是利用这个速度差被输送出脱水机的。一方面,当进泥量一定时,差转速越大,污泥在脱水机中停留的时间越短,固环层就越薄;另一方面,差转速越大,由于转鼓与螺旋之间的相对运动增大,必然使对液环层的扰动程度增大,固环层内部被分离出来的污泥会被重新泛至液环层,并有可能随分离液流失。
综上所述,差转速增大时,脱水的固体回收率和泥饼的含固量都将降低,但增大差转速可提高离心机的处理能力。反之,减小差转速时,污泥在转鼓内接受离心分离的时间将延长,同时由于转鼓和螺旋之间的相对运动减小,对液环层的扰动也减轻,因此固体回收率和泥饼含固量均将提高,但减小差转速,需降低处理能力。差转速不能太小,否则将由于污泥在机内积累,使固环层厚度大于液环层,导致污泥随分离液大量流失,固体回收率急剧下降,严重时还会由于阻力过大,扭矩超负荷损坏离心机。
目前的多数离心机,已实现离心机、泥泵、药泵的自动控制。其主要工作方式是自动调节差转速。以扭矩为控制因数,当扭矩大时,自动加大差转速,来降低扭矩;当扭矩小时,自动降低差转速。当扭矩过大且持续无法调节下降时,会实现离心机、泥泵、药泵的自动停机,保护设备不受损伤。
93.离心污泥脱水机液环层厚度如何控制调节?
液环层厚度是设备优化的一个重要参数,直接影响离心机的有效沉降容积和干燥区(岸区)长度,进而影响污泥脱水的处理效果。一般在停机状态下通过手动调节液位挡板的高低来实现,调整时必须确保各个液位挡板的高低一致,否则会导致离心机运行时剧烈振动。当进泥量一定时,液环层加厚,一般会提高脱水的固体回收率和分离液质量,但泥饼含水率会提高。调低液环层厚度可获得较低的泥饼含水率,但分离液质量会下降。在控制液环层厚度时,应在高固体回收率与泥饼含水率之间权衡。如果无需追求过低的泥饼含水率,应选择适当调大液环层厚度。
94.离心污泥脱水机运行中如何综合调节各项参数?
离心机的各项参数相互影响,调节一个参数可能会引起多个参数的调节,由于污泥泥质和浓度时常变化,各项参数也要经常进行调节。
下面是一些实践经验,供大家参考。
(1)首先确定最大处理泥量。一般不宜超过设备铭牌所标示最大泥量的85%,不处理最大的泥量,亦为降低转速创造条件。泥质不同,最大处理量也不同,颗粒大、密度高可取较大处理量。
(2)确定转鼓转速。一般不宜超过设备铭牌所标示最大转鼓转速的80%。一般设备选型时,都会进行试验,同样的分离因数,宁可选取较大的直径,也要降低转速。运行时,经实践验证的转速,除非泥质有重大变化,轻易不要调整。因为转速调整后,其他参数大多需要跟随调整。
(3)差转速一般根据扭矩来调节。调试阶段,转速、扭矩、差转速要联合调试。先大致稳定转速,根据扭矩,调节差转速,查看泥饼含水率和分离液质量。如果泥饼含水率和分离液质量不达标,再调整至其他转速,重复进行。自动控制的离心机,也应先设定转速,然后设定扭矩及相关参数,进行验证。无自动控制的离心机,操作人员工作量要远远高于自控型,且稳定性和质量差距甚大。
(4)絮凝剂投加量,是最常用的调节参数,一般来讲,污泥的浓度变化是最常见的,浓度变化会引起扭矩的变化。运行中,常根据扭矩的变化来调节投药量。根据经验,在进泥浓度适宜的情况下,扭矩与泥饼含水率有相关性,污泥扭矩大致稳定在一个区间,泥饼含水率也大致稳定在一定范围。污泥浓度偏高或偏低,前述相关性不强。
(5)保持进泥性质和浓度的稳定,是保证离心机正常运行的最重要条件。
95.生化反应系统A/O工艺的日常操作主要控制内容有哪些?
A/O工艺的反应中,进入生化反应系统的废水所含碱度及生化反应时间是保证氨氮成功去除的关键。同时,装置的运行参数及相关条件的优化,也是保证运行效果、降低能耗的有效途径。一般运行中要做好进水量、供氧、碱度保障、污泥回流量保障等控制。
96.生化反应系统A/O工艺反应需氧量如何计算?
供氧是A/O工艺的运行条件的关键因素之一,A/O工艺的需氧量由四部分组成,以吉化污水处理厂正常运行负荷为例,分别计算如下。
(1)降解BOD5耗氧(kg/h):
5000×(0.24-0.01)×0.75=862.5(忽略反硝化段去除的BOD5)
式中,5000为平均水量,m3/h;0.75为系数,表示去除的BOD5中有75%被氧化,其余用于合成细胞,这是参照石油化工废水的经验值选取的;0.24和0.01为生化进出水BOD5。
(2)微生物内源呼吸耗氧(kg/h):
126490×0.008=1012
式中,126490为好氧段有效容积,m3;0.008为内源呼吸系数,经实测得出。
(3)氨氮去除耗氧(kg/h):
5000×0.053×4.57=1211.05
式中,氨氮绝对去除量取0.053g/L;4.57是每1g氨氮被硝化为-N的理论需氧量。但氨氮并非全部被硝化作用转化,按80%转化估算,耗氧量应为968.84kg/h。
(4)出水携带氧(kg/h):
5000×(1+0.8)×6.0/1000=54
式中,0.8为回流比;出水溶解氧为6.0mg/L。
总需氧量(kg/h):
862.5+1012+968.84+54=2897.3
每1m3空气含O2 0.29232kg;曝气系统传氧效率为0.20。则A/O工艺在当前水质、水量条件下需供空气量(m3/h):
2897.34÷0.29232÷0.20=49557.7
97.生化反应系统A/O工艺运行中如何控制供氧?
以上面计算结果可知,降解BOD5耗氧29.8%;微生物内源呼吸耗氧34.9%;氨氮去除耗氧33.4%;出水携带氧1.9%。A/O工艺在运行中,必须依靠水质、水量情况科学计算出空气需求量,按要求组织供气,保证系统运行效果达到最佳。而A/O工艺的实际生产控制过程中,直观所能测得的是出水端的剩余溶解氧(DO),剩余溶解氧在本装置供氧中所占比例很小,仅为1.9%,却能反映出系统的供氧情况。一般情况下,只要不是长期缺氧,生化反应池内溶解氧对运行结果的影响并不十分明显。不同溶解氧条件下与氨氮去除率的关系如图2-18所示。由图2-18可见,生化池内出水DO与NH3-N去除率关系趋势线,显示当出水DO大于1.5mg/L时,随着出水DO的增加,NH3-N去除率变化不大。一般情况下,生化反应池内氧平均分布符合设计的2~4mg/L,出水溶解氧可达6mg/L左右,如再增加,则浪费能耗,增加了不必要的消耗。因此,A/O工艺供氧,要在考虑进水污染物浓度的前提下,通过监测出水溶解氧并及时调整供氧量,来实现运行消耗最低的条件下完成污染物去除的任务。

图2-18 生化池内DO与NH3-N去除率的关系
98.生化反应系统回流比在A/O工艺运行中应如何控制?
回流比是生化处理中最实际的操作指标,A/O工艺设计回流比为100%,比原传统活性污泥法的回流比50%高出一倍。在实际生产中已经证实,传统活性污泥法的50%回流比,即使再增加一倍,也不会带来COD去除效率的提高。在A/O工艺系统运行中,分阶段改变回流比以考核其对氨氮去除的影响,考核结果如图2-19所示。

图2-19 生化池回流比与NH3-N去除率的关系
由图2-19可见,回流比在50%~230%之间的不同数值,出水氨氮差异较小。在A/O工艺理论中,除正常回流比要比传统活性污泥法大以外,还应增加出水回流或混合液回流,这样可以使硝化过程中产生的硝态氮大量在A段分解成氮气释放到空气中,从而有效地降低出水的硝态氮和总氮。反硝化还可以产生部分碱度,为氨氮的硝化去除创造有利的条件。从本装置优化运行结果看,回流比增加后氨氮去除效率并未有明显提高;同时,反硝化所产碱度与所需碱度相比,所占比例较小;其所产碱度对氨氮去除也不会有太大的影响。由此可以分析,大量回流对出水氨氮并无太大益处。更重要的是,在污泥回流比为50%时,回流用电占污水处理厂电耗的3%左右,如果大量回流,将会加大能耗和设备维护费用,提高污水处理成本。因此,A/O工艺运行要在水质条件允许的情况下适当降低回流比,以降低污水处理运行能耗。
99.生化反应系统A/O工艺中污泥浓度如何优化控制?
在A/O工艺实践中,污泥浓度是对氨氮去除效果的关键参数之一,在硝化作用启动后,各种不同污泥浓度下氨氮的去除率如图2-20所示。由图2-20可见,污泥浓度为5g/L,氨氮的去除效果达到较高水平。因此,运行中要较稳定地控制好生化反应池内的污泥浓度。污泥浓度的稳定控制方式,主要是控制好剩余污泥的排放量,剩余污泥的排放量为当前条件下的污泥增长量,即正常运行过程中,新增污泥量要通过排放剩余污泥的方式来维持A/O工艺中污泥浓度的稳定,而新增污泥量的多少取决于当前水质条件下微生物的繁殖情况,要在运行中不断摸索。一般A/O工艺污泥龄为40d以上,操作中可按生化系统总污泥量的1/40以下进行剩余污泥排放,即每日排泥总量低于A/O工艺系统中的1/40,观察污泥浓度的变化,如污泥浓度有上升趋势则适当增加剩余污泥排放量,如降低则减少剩余污泥排放量。

图2-20 生化池MLSS与NH3-N的关系
100.污泥厌氧消化系统消化池的压力如何控制?
消化池运行的压力比较低,对于成熟的污泥消化系统,运行压力的监控是非常重要的,在实际运行操作中,消化池的压力是浮动的,消化池的进泥、排泥、搅拌都有可能影响消化系统的压力。其中最重要的是沼气管道内的冷凝水的影响。及时排放管道中析出的冷凝水,保持管路畅通,避免系统压力过高,是消化系统稳定运行的重要保证。在北方的冬季,出消化池沼气含有大量热水汽,易结成霜挂在阀门及管线内,形成管线冻塞现象,这种情况是非常危险的。因此,在日常运行中要严密关注消化池的运行压力,防止意外情况的发生。
101.污泥厌氧消化系统消化池的温度如何控制?
在已有的研究中,均有甲烷细菌对温度的敏感性的详细描述,工业化的厌氧消化系统,保持温度的恒定是非常困难的。在实际的运行中,是将操作温度控制在一定范围内,吉化污水处理厂采用中温消化(35±1)℃的操作温度。一般的控制方式为将每日投入消化池的新鲜污泥加热至38℃以上,即可保证日常运行的消化温度稳定在(35±1)℃范围内,实现消化系统的平稳运行。
102.污泥厌氧消化系统消化池的液位如何控制?
消化池液位的浮动,直接反馈到消化池的压力变化,消化池的液位作为一个重要的监控指标。保持消化池液位的相对稳定,对保持消化池压力系统的稳定是非常重要的。在实际中,主要是通过定期校核消化池进、排泥泵,定期校核消化池液位计来进行液位的控制的。常规固定盖式消化池在排泥和投泥时,若操作不当,有可能使池内造成负压或超压,导致严重后果。
103.污泥厌氧消化系统消化池的搅拌状态如何控制?
除了保证每天足够的进泥量外,污泥搅拌也是一项重要内容。连续而均匀地进泥与排泥可使消化池内有机物最大限度地维持在一定水平上,搅拌则能使池内的有机物浓度、微生物的分布、温度、pH值等都均匀一致地处在最有利的状态。
104.污泥厌氧消化系统消化池内污泥浓度如何控制?
污泥厌氧消化池内,运行中要控制污泥浓度处在一个较为稳定的范围,才能确保日常运行的稳定。一般污泥浓度应在50g/L左右。污泥浓度的稳定是通过排放上清液来实现的。在污泥厌氧消化反应过程中,污泥分解会产生一部分水,消化池内不搅拌使这部分水浮在消化池内部形成上清液,日常运行中要经常有规律地排放上清液,来保证消化池内污泥浓度的稳定。同时,上清液属于碱性消化液,在消化池投泥后的搅拌中可以起到较好的缓冲作用。因此,消化池内还要有一定的存量,根据池内平均污泥浓度情况,适量排放。
105.污泥厌氧消化系统消化池要有哪些安全注意事项?
消化池应密封,不得渗入空气,以保证甲烷细菌的正常发育,消化池中的浮渣与沉砂应定期清除,在运行中应十分注意安全问题。因沼气易燃易爆,沼气的主要成分甲烷在空气中含量达到5%~6%时,遇明火即爆炸,故消化池、贮气罐、污泥气管道等都必须绝对密封。周边严禁明火和电气火花。还必须注意控制室与消化池等设备的连接点,不能有空气进入消化池的可能。检修消化池时,必须完全排除池内的消化气。消化池的所有仪表(压力表、真空表、温度计、pH计等)应定期检查,保证随时完好。消化启动过程中会产生爆炸性气体,因此要加强气体监测,一旦发现爆炸性气体就要立即采取有效的安全措施。