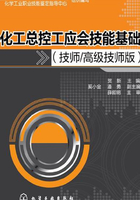
结晶操作技术与运行管理
一、晶体基本理论
固体从形态上分为有晶形和无定形两种。例如,食盐、蔗糖等都是晶体,而木炭、橡胶都为无定形物质。其区别主要在于内部结构中的质点元素(原子、分子)的排列方式互不相同。
(一)溶解度和溶解度曲线
任何固体物质与其溶液相接触时,如溶液尚未饱和,则固体溶解,如溶液恰好达到饱和,则固体溶解与析出的速度相等,结果是既无溶解也无析出,此时固体与其溶液已达到相平衡。固液相平衡时,单位质量的溶剂所能溶解的固体的质量,称为固体在该溶剂中的溶解度。工业上通常采用1(或100)份质量的溶剂中溶解多少份质量的无水溶质来表示溶解度的大小。
溶解度的大小与溶质及溶剂的性质、温度及压强等因素有关。一般情况下,溶质在特定溶剂中的溶解度主要随温度而变化。因此,溶解度数据通常用溶解度对温度所标绘的曲线来表示,该曲线称为溶解度曲线。图2-79中示出了几种常见的无机物在水中的溶解度曲线。

图2-79 几种无机物在水中的溶解度曲线
由图2-79可知,有些物质的溶解度随温度的升高而迅速增大,如NaNO3、KNO3等;有些物质的溶解度随温度升高以中等速度增加,如KCl、(NH4)2SO4等;还有一类物质,如NaCl等,随温度的升高溶解度变化不明显;此外,一些化合物的溶解度曲线上有折点,物质在折点两侧含有的水分子数不等,故转折点又称为变态点。例如,低于32.4℃时,从硫酸钠水溶液中结晶出来的固体是Na2SO4·10H2O,而在这个温度以上结晶出来的固体是Na2SO4。
溶解度特征对于结晶方法的选择起决定性的作用。对于溶解度随温度变化敏感的物质,适合用变温结晶方法分离;对于溶解度随温度变化缓慢的物质,适合用蒸发结晶法分离等。
(二)饱和溶液与过饱和溶液
1.饱和溶液与溶解度曲线
达到固、液相平衡时的溶液称为饱和溶液。溶液含有超过饱和量的溶质,则称为过饱和溶液。同一温度下,过饱和溶液与饱和溶液的浓度差称为过饱和度。
溶液的过饱和度与结晶的关系可用图2-80表示。图中AB线为具有正溶解度特性的溶解度曲线,CD线表示溶液过饱和且能自发产生晶核的浓度曲线,称为超溶解度曲线。这两条曲线将浓度-温度图分为三个区域:AB线以下的区域称为稳定区,稳定区中溶液尚未达到饱和,因此没有结晶的可能;CD线以上的区域称为不稳区,在此区域中,溶液能自发地产生晶核;AB线和CD线之间的区域称为介稳区,在这个区域内,不会自发地产生晶核,但如果在溶液中加入晶种(在过饱和溶液中人为地加入的小颗粒溶质晶体),这些晶种就会长大。此外,大量的研究工作证实,一个特定物系只有一条确定的溶解度曲线,但超溶解度曲线的位置却要受很多因素的影响,如有无搅拌、搅拌强度大小、有无晶种、晶种大小与多寡、冷却速率快慢等,因此应将超溶解度曲线视为一簇曲线。

图2-80 溶液的过饱和与超溶解度曲线
图2-80中初始状态为E的洁净溶液,分别通过冷却法(EFH)、蒸发法(EF′G′)或真空绝热蒸发法(EF″G″)结晶。
2.溶液的过饱和度
溶质浓度超过该条件下的溶解度时,该溶液称为过饱和溶液,过饱和溶液达到一定过饱和度时会有溶质析出。
一般过饱和度可用两种方式来表示。第一种,以浓度差来表示过饱和度:
Δc=c-c*
(2-40)
式中 Δc——溶度差过饱和度,kg溶质/100kg溶剂;
c——操作温度下的过饱和浓度,kg溶质/100kg溶剂;
c*——操作温度下的溶解度,kg溶质/100kg溶剂。
第二种,以温度差来表示过饱和度:
Δt=t*-t
(2-41)
式中 Δt——温度差过饱和度,K;
t*——该溶液在饱和状态时所对应的温度,K;
t——该溶液经冷却达到过饱和状态时的温度,K。
(三)结晶过程的两个阶段
晶体的生成包括晶核的形成和晶体的生长两个阶段。
1.晶核的形成
晶核是过饱和溶液中初始生成的微小晶粒,是晶体成长过程中必不可少的核心。结晶过程是一个相变过程。在开始由气相或液相形成晶相时,一般说是很困难的,原子或分子在气相或液相的吉布斯函数很高,必须在很大程度上降低其分子熵才能形成晶核。晶核可以由均相成核或非均相成核两种过程及三种成核形式:初级均相成核、初级非均相成核及二次成核。在高过饱和度下,溶液自发地生成晶核的过程,称为初级均相成核;溶液在外来物(如大气中的微尘)的诱导下生成晶核的过程,称为初级非均相成核;而在含有溶质晶体的溶液中的成核过程,称为二次成核。二次成核也属于非均相成核过程,它是在晶体之间或晶体与其他固体(器壁、搅拌器等)碰撞时所产生的微小晶粒的诱导下发生的。均相成核是指在大体积过饱和体系中自然形成晶核,体系各部分成核的概率相同。
晶核形成的过程:在溶液中,质点元素不断地作不规则的运动,随着温度的降低或溶剂量的减少,不同质点元素间的引力相对地越来越大,以致达到不能再分离的程度,结合成线晶,线晶结合成面晶,面晶结核成按一定规律排列的细小晶体,形成所谓的“晶胚”。晶胚不稳定,进一步长大则成为稳定的晶核。
结晶是以过饱和度为推动力的,如果溶液没有过饱和度产生,晶核就不能形成。在介稳区内,晶体就可以增长,但晶核的形成速率却很慢,尤其在温度较低,溶液的黏度很高,溶液的密度较大时,阻力也比较大,晶核的形成也比较困难。
在大部分的结晶操作中,晶核的产生并不困难,而晶体的粒度增长到要求的大小则需要精细的控制。往往有相当一部分多余出来的晶核远远超过取出的晶体粒数,必须把多余的晶核从细晶捕集装置中不断取出,加以溶解,再回到结晶器内,重新生成较大粒的晶体。
2.晶体的生长
晶体的生长过程是指在过饱和溶液中已有晶核形成或加晶种后,以过饱和度为推动力,溶液中的溶质向晶核或加入的晶体运动并在其表面上进行有序排列,使晶体格子扩大的过程。
影响结晶成长速率的因素很多:过饱和度、粒度、物质移动的扩散过程等。
解释结晶成长的机理有:层生长理论、布拉维法则、扩散理论、吸附层理论。下面介绍关于晶体生长的三种主要的理论。
(1)层生长理论 科塞尔(Kossel,1927)首先提出,后经斯特兰斯基(Stranski)加以发展的晶体的层生长理论亦称为科塞尔-斯特兰斯基理论。
它的主要观点是在晶核的光滑表面上生长一层原子面时,质点在界面上进入晶格“座位”的最佳位置是具有三面凹入角的位置。质点在此位置上与晶核结合成键放出的能量最大。因为每一个来自环境相的新质点在环境相与新相界面的晶格上就位时,最可能结合的位置是能量上最有利的位置,即结合成键时应该是成键数目最多,释放出能量最大的位置。
(2)布拉维法则 1855年,法国结晶学家布拉维(A.Bravis)从晶体具有空间格子构造的几何概念出发,论述了实际晶面与空间格子构造中面网之间的关系,即实际晶体的晶面常常平行于网面结点密度最大的面网,这就是布拉维法则。
(3)扩散理论 按照扩散理论,晶体的生长过程由三个步骤组成:①溶质由溶液扩散到晶体表面附近的静止液层;②溶质穿过静止液层后达到晶体表面,生长在晶体表面上,晶体增大,放出结晶热;③释放出的结晶热再靠扩散传递到溶液的主体去。
二、结晶设备
(一)常见的冷却结晶设备
冷却结晶法是指基本上不除去溶剂,而是使溶液冷却而成为过饱和溶液而结晶。适用于溶解度随温度下降而显著减小的物系。例如,硝酸钾、硝酸钠等溶液。
1.空气冷却式结晶器
空气冷却式结晶器是一种最简单的敞开型结晶器,靠顶部较大的开敞液面以及器壁与空气间的换热而达到冷却析出结晶的目的。由于操作是间歇的,冷却又很缓慢,对于含有多结晶水的盐类往往可以得到高质量、较大的结晶。但必须指出,这种结晶器的能力是较低的,占用地面积大。它适用于生产硼砂、铁矾、铁铵矾等。
2.釜式结晶器
冷却结晶过程所需的冷量由夹套或外部换热器供给,如图2-81及图2-82所示,采用搅拌是为了提高传热和传质速率并使釜内溶液温度和浓度均匀,同时可使晶体悬浮,有利于晶体各晶面成长。图2-82所示的结晶器为外循环式冷却结晶器,既可间歇操作,也可连续操作。若制作大颗粒结晶,宜采用间歇操作,而制备小颗粒结晶时,采用连续操作为好。

图2-81 内循环式冷却结晶器

图2-82 外循环式冷却结晶器
外循环式冷却结晶器的优点是:冷却换热器面积大,传热速率大,有利于溶液过饱和度的控制。缺点是循环泵易破碎晶体。
3.Krystal-Oslo分级结晶器
Krystal-Oslo结晶器是1919年由挪威Issachen及Jeremiassen等人开发的一种制造大粒结晶、连续操作的结晶器,又称为Oslo(奥斯陆)式结晶器、Jeremiassen式结晶器或Krystal式结晶器。如图2-83所示,这种结晶器至今还广泛使用着。这类结晶器根据用途分为蒸发式与冷析式以及真空蒸发式三种类型。不论过饱和度产生的方法如何,过饱和溶液都是通过晶床的底部,然后上升,从而消失过饱和度。接近饱和的溶液由结晶段的上部溢流而出,再经过循环泵进行下一次强制循环,送入过饱和发生器再返回晶床的底部。设计与操作控制在过饱和发生器中不超过介稳定区的限度;在溢流口上面的一段,通过的流量在不取出成品晶浆时等于在溢流管处注入的加料流率,因此上升速度很低,细小结晶就在这一段积累,由一个外设的细晶捕集器间歇式连续取出,经过沉降后,或者过滤,或者用新鲜加料液溶解,也可以辅之以加热助溶的办法,消除过剩的细小结晶,溶化后的溶液供给结晶器作为原料液。这样可以保证结晶颗粒稳步长大。

图2-83 Krystal式冷却结晶器
A—结晶器进料管;B—循环管入口;C—主循环泵;D—冷却器;E—过饱和吸入管;F—放空管;G—晶浆取出管;H—细晶捕集器
冷却式Krystal分级结晶器(图2-84)的过饱和产生设备是一个冷却换热器,一般是溶液通过换热器的管程,且管程是以单程式的最普遍,冷却介质通过壳程。

图2-84 冷却式连续分级结晶器
A—细晶器捕集器;B—中心降液管;C—分级段;D—主循环泵;E—冷却器;F—溢流口;G—辅助循环泵;H—取出口;I—加液口;J—冷剂出口;K—排放出口
须指出的是壳程冷却介质的循环方式。在管程通过的溶液的过饱和度设计限是靠主循环泵的流量所控制,但是冷却介质的状况也同样会使溶液发生过饱和度超过设计限的问题,因为新鲜的冷却介质冲入换热器壳程时,与溶液温度差很大,而过饱和度的介稳区是很狭窄的一个区域。为了防止这一现象发生,不致使溶液在冷却介质入口处迅速结垢,必须再加上一套辅助循环泵以消除这一现象。这说明换热器中产生的过饱和度超限不仅可能发生在管程的进出口两端;而且也受到管壁内外两侧流体状况的影响。为此就不得不使冷剂间接地通过辅助循环系统加以缓冲,见图2-85。

图2-85 Krystal-Oslo结晶器冷却换热器的辅助冷剂循环系统
(二)常见的蒸发结晶设备
蒸发结晶与冷却结晶不同之处在于,前者需将溶液加热到沸点,并浓缩达过饱和而产生结晶。
现代的蒸发结晶器(包括以蒸发为主,又有盐类析出的装置,如隔膜电解液的蒸发装置),都是指严格控制过饱和度与成品结晶粒度的各种装置。它是在蒸发装置的基础上发展起来,又在结晶原理上前进了一大步。
1.Krystal-Oslo蒸发式生长型结晶器
图2-86是典型蒸发式Krystal-Oslo生长型结晶器。加料溶液由G进入,经循环泵进入加热器,产生蒸汽(或者前级的二次蒸汽)在管间通入,溶液达到过饱和,结晶操作控制在介稳区以内。溶液在蒸发室内排出的蒸气(A点)由顶部导出。如果是单级生产,分离的蒸气直接去大气冷凝器,然后有必要时通过真空发生装置(如真空泵或者蒸汽喷射器及冷凝器组);如果是多效的蒸发流程,排出蒸气则通入下一级加热器或者末效的排气、冷凝装置。

图2-86 Krystal-Oslo型蒸发结晶器
溶液在蒸发室分离蒸汽之后,由中央下行管送到结晶生长段的底部(E点),然后再向上方流经晶体流化床层,过饱和得以消失,晶床中的晶粒得以生长。当粒子生长到要求的大小后,从产品取出口排出,排出晶浆经稠厚器离心分离,母液送回结晶器。固体直接作为商品,或者干燥后出售。
Krystal蒸发结晶器大多数是采用分级的流化床,粒子长大后沉降速度超过悬浮速度而下沉,因此底部聚积着大粒的结晶,晶浆的浓度也比上面的高,空隙率减小,实际悬浮速度也必然增加,因此正适合分级粒度的需要。这也正好是新鲜的过饱和溶液先接触的所在,在密集的晶群中迅速消失过饱和度,流经上部由O点排出,作为母液排出系统;或者在多效蒸发系统中进入下一级蒸发。
生长型蒸发结晶器的结构比一般蒸发器复杂得多,投资也必然高。因此,原则上在前级没有达到析出结晶的浓度时,就无必要按照这种结晶器设计。只有肯定有结晶析出时才采用Krystal型生长结晶器,这一点要给予注意。
Krystal蒸发结晶器除以分级式操作外,也可以采用晶浆循环(magmarecycling)式操作。为了达到晶浆循环的目的,一种办法是保持较高的晶浆积累浓度,最后循环泵进口处吸入的也是较浓的晶浆,经循环泵送入蒸发器再进入蒸发室循环;另一种办法是加大循环速度,同时保持较高的晶浆浓度。晶浆循环操作法的生产能力要高于分级结晶操作法,只是循环泵的转动部件及加热管有晶浆的磨损。同时要注意选择泵型,防止晶粒破碎,产生大量的细晶,以及长大的晶粒又被破碎。
2.DTB型蒸发式结晶器
DTB是drafttubebafflecrystallizer的缩写,即遮挡板与导流管的意思,简称“遮导式”结晶器,如图2-87所示。

图2-87 DTB蒸发结晶装置简图
DTB型蒸发式结晶器可以与蒸发加热器联用,也可以把加热器分开,结晶器作为真空闪蒸制冷型结晶器使用。这种结晶器是目前采用最多的类型。它的特点是结晶循环泵设在内部,阻力小,驱动功率省。为了提高循环螺旋桨的效率,需要有一个导热液管。遮挡板的钟罩形构造是为了把强烈循环的结晶生长区与溢流液穿过的细晶沉淀区隔开,互不干扰。
过饱和产生在蒸汽蒸发室。液体循环方向是经过导流管快速上升至蒸发液面,然后使过饱和液沿环形面积流向下部,属于快升慢降型循环,在强烈循环区内晶浆的浓度是一致的,所以过饱和度的消失比较容易,而且过饱和溶液始终与加料溶液并流。由于搅拌桨的水力阻力小,循环量较大,所以这是一种过饱和度最低的结晶器。器底设有一个分级腿(elutriationleg),取出的产品晶浆要先穿过它,在此腿内用另外一股加料溶液进入,作为分级液流,把细微晶体重新漂浮进入结晶生长区,合格的大颗粒冲不下来,落在分级腿的底部,同时对产品也进行一次洗涤,最后由晶浆泵排出器外分离,这样可以保证产品结晶的质量和粒径均匀,不夹杂细晶。一部分细晶随着溢流溶液排出器外,用新鲜加料液或者用蒸汽溶解后返回。
3.喷雾式结晶器
当溶液与冷剂不互溶时,就可以利用溶液直接接触,这样,就省去了与溶液接触的换热器,防止了过饱和度超过时造成结垢。如喷雾式结晶器。
喷雾式结晶器也称湿壁蒸发结晶器,结构简图如图2-88所示。这种结晶器在操作时将浓缩的热溶液与大量的冷空气相混合,产生冷却及蒸发的效应,从而使溶液达到过饱和,结晶得以析出。有很多工厂用浓缩热溶液进行真空闪蒸直接得到绝热蒸发的效果使结晶析出的例子。操作时以25~40m/s高速度由一台鼓风机直接送入冷空气,溶液由中心部分吸入并被雾化,这时雾滴高度浓缩直接变为干燥结晶,附着在前方的硬质玻璃管上;或者变成两相混合的晶浆由末端排出,稠厚,离心过滤。此类结晶器设备紧凑简单,缺点是结晶粒度往往比较细小。

图2-88 喷雾式结晶器
三、结晶器操作
(一)间歇式冷却结晶器的操作
在中小规模的结晶过程中广泛采用间歇操作,它与连续结晶相比,操作较为简单。
(1)控制降温速度结晶 在间歇操作的结晶过程中,为了控制晶体的大小和晶形,获得粒度较均匀的晶体产品,必须尽一切可能防止多余的晶核生成,一种较好的控制手段是缓缓降温,将溶液的过饱和度控制在介稳区中,以使晶体能更好地生长。
(2)搅拌结晶 间歇式结晶釜一般都配有搅拌装置,搅拌能促进传热,使结晶温度均匀,不致颗粒大小不一,但应注意搅拌的形式和搅拌的速度。
锚式搅拌径向流动较好,而桨式搅拌则有利于轴向流动,框式搅拌则既有径向流动又有轴向流动,在间歇式结晶釜中是一个很好的选择。
搅拌转速过慢,影响结晶釜内的传热过程,不利于结晶产能的提高;搅拌转速太快,会导致对晶体的机械破损加剧,影响产品的质量,转速太慢,则可能起不到搅拌的作用,适当的搅拌速度对间歇结晶是很重要的操作参数。
(3)加晶种的控制结晶 在间歇操作的结晶过程中,为了控制晶体的晶型,往往通过向溶液中加入适当数量及适当粒度的晶种,让被结晶的溶质只在晶种表面上生长。在整个结晶过程中,加入晶种并小心地控制溶液的温度或浓度,这种操作方式称为“加晶种的控制结晶”。晶种的加入量取决于整个结晶过程中可被结晶出来的溶质量、晶种的粒度和所希望得到的产品粒度。
(4)间歇冷却结晶的最佳操作程序 采用自然冷却操作,则在结晶过程的初始阶段溶液的过饱和度急升或急降,有发生初级成核的危险,又有生产能力低下的问题;采用按恒速降温操作,比自然冷却稍好,但类似于上述自然冷却操作的缺点依然存在;按适宜冷却程序操作,使过饱和度自始至终维持在某一预期的恒定值,能使操作得到实质性的改善。
(二)连续式冷却结晶器的操作
连续结晶器的操作有以下几项要求:①结晶器控制产品粒度分布合理;②结晶器具有尽可能高的生产强度;③降低结晶垢的速率,延长结晶器正常运行的周期;④维持结晶器的稳定操作。
为了使连续结晶器具有良好的操作性能,往往采用“细晶消除”、“粒度分级排料”、“清母液溢流”等技术,使结晶器成为所谓“复杂构型结晶器”。
1.细晶消除
在连续操作的结晶器中,由于成核过程很不容易控制,较普遍的情况是晶核的生成速率过高。如何尽早地把过量的晶核除掉,而不应让它们生长到大一些的粒度后再消除之是很重要的。
通常采用的去除细晶的办法是根据淘析原理,在结晶器内部或外部建立一个澄清区,在此区域内,晶浆以很低的速度向上流动,使大于某一“细晶切割粒度”的晶体能从溶液中沉降出来,回到结晶器的主体部分,重新参与器内晶浆循环,并继续生长。所谓细晶切割粒度是指操作者或设计者要求去除的细晶的最大粒度,小于此粒度的细晶将从澄清区溢流而出,进入细晶消除循环系统,以加热或稀释的方法使之溶解,然后经循环泵重新回到结晶器中去。
2.清母液溢流
清母液溢流是调节结晶器内晶浆密度的主要手段,增加清母液溢流量无疑可有效地提高器内的晶浆密度。
从澄清区溢流而出的母液分为两部分,一部分排出结晶系统,另一部分则进入细晶消除系统,经溶解消晶后重又回到结晶器中去。当澄清区的细晶切割粒度较大时,为了避免流失过多的固相产品,可使溢流而出的含有细晶的母液先经过旋液分离器或湿筛,而后分为两股,使含有细晶较多的流股进入细晶消除循环,而含有少量细晶的流股则排出结晶系统。
四、结晶操作的故障判断及处理
在结晶操作中,由于控制不当,会出现一些不正常工作现象,主要有以下方面:①晶体颗粒太细;②产生晶垢;③堵塞;④蒸发结晶器的压力波动;⑤晶浆泵不上量;⑥稠厚器下料管堵。具体产生原因及处理方法见表2-10。
表2-10 结晶操作的不正常现象、产生原因及处理方法

五、连续式蒸发结晶操作的参数控制
1.投入量的控制
在投入量的恒稳控制系统中,流量的测量仪表应选用电磁流量计或堰式流量计等。投入量的变化直接影响结晶器内溶液过饱和度的大小。此外,投入量还与产量成正比。
2.取出量的控制
取出量的控制是个重要但未能妥善解决的问题。许多连续结晶器在晶浆取出管路上安装调节阀来调节取出量,但这样做并不可靠,因为这种阀常有堵塞的可能。可加装定时器,使阀每隔1~2min全开一次以清除堆积在阀门处的晶体,从而避免堵塞现象。调节阀堵塞的发生与产品的粒度关系很大,一般情况下只有产品粒度很细时才能使用节流方法来调节取出量。目前,也有用考克或改用胶管阀的,便于晶疤堵塞时清理。在冬季,取出管最容易结疤堵塞。在取出时还可采用变速泵,根据结晶器内的液位高低来控制变速泵的转速。这个方法的缺点在于泵的转速与取出量的关系是非线性的,因而调节特性不良,且可调范围亦较窄。现在更常采用的方法是在结晶器的排料口处,将一股母液引回到取出管中去,以降低管中的晶浆密度,低密度晶浆的流量可以在很宽的范围内调节。这个方法的缺点是所取出的晶浆必须先经过一个沉降槽或增稠器,使晶浆密度增至适合于过滤或离心分离的程度。
3.液位控制
绝大多数的真空冷却结晶器需在恒定的液位高度下操作,所以液位控制系统须能保证液位与预期高度相差在150mm之内。对于DTB结晶器,液位高度是指结晶器的进料口与器内沸腾表面之间的高度差。过高的液位使循环晶浆中的晶粒不能被充分地送入产生过饱和度的液体表面层。液位过低时,液位的微小变化可能切断导流筒上缘的循环通道,破坏结晶器的运行。真空冷却结晶器的液位控制系统中,变送器可采用压差变送器,其低压测压口与结晶器的气液分离室相连。压差变送器可以是法兰插入式,也可以用测压连接管与结晶器相连,而连接管内可被清洗,但清洗溶液的温度应较低,以防止它在连接管中沸腾而干扰液面控制。一般情况下,液位控制系统以进料量作为调节参数,但在有些情况下则以母液的再循环量或取出量为调节参数。
4.绝对压力的控制
真空冷却结晶器的操作压力(绝压)必须仔细控制,因为它的变化可直接影响结晶温度。结晶器内的绝压由真空系统的排气速率控制。绝压控制系统应能使器内温度保持在预置点0.5K之间。通常在结晶器顶部安装压力变送器。
5.加热蒸汽量的控制
对于蒸发结晶器,溶液的过饱和度主要取决于输入的热流强度。控制加热蒸汽压力或流量皆可达到控制热流强度的目的,经验证明最好是控制蒸汽流量。对于大多数的蒸发结晶设备,加热蒸汽流量直接正比于结晶器的生产速率、循环晶浆的单程温升及热交换温差。控制系统不但应能监测此温差值,据以重新设置加热蒸汽流量的给定值,还须具有内部自锁功能,当驱动循环泵或螺旋桨的电机因过载或断电而停止转动时,应能自动切断蒸汽的输入。
6.晶浆密度的控制
结晶器内的晶浆密度是一个重要的操作参数,可用悬浮液中两点间的压差来表征晶浆密度,此两点在垂直方向上必须有足够大的距离,使测量仪表有较大的读数,如晶浆有较大的密度,则两测压点间的垂直距离可为150~250mm。一般情况下,此两测压点可设置在结晶器主体的液面下方。对于强制外循环结晶器,两测压点安装在晶浆循环管路上也能成功地测量晶浆密度。液体的湍流运动使输出信号存在相当强的噪声,故须在测压连接管上加装阻尼阀或采用适当的电子阻尼器。在晶浆控制系统中,按压差变送器输出的信号,调节清母液溢流速率,保持结晶器内晶浆密度恒定。
7.其他需要监测的参数
结晶系统需要测量温度的点包括进料、出料、液氨、冷却水或其他载冷体等,还需要监测加热器的温差以及各种母液成分的变化。循环泵或循环螺旋桨的电机的电流波动,也需监测。还需经常监测晶浆泵的电机的电流大小。