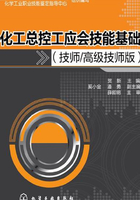
第二节 间歇釜式反应器的操作与控制
一、间歇釜式反应器的工艺原理
间歇釜式反应器又称槽型反应器或锅式反应器,它是各类反应器中结构较为简单且又应用较广的一种。主要应用于液-液均相反应过程,在气-液、液-液非均相反应过程也有应用。间歇釜式反应器具有温度和压力范围宽、适应性强,操作弹性大,连续操作时温度、浓度容易控制,产品质量均一等特点。
一般在较缓和的操作条件(如常压、温度较低且低于物料沸点)下应用间歇釜式反应器操作。
现以橡胶制品硫化促进剂DM(2,2-二硫代苯并噻唑)的中间产品(2-巯基苯并噻唑)为例,介绍间歇式反应釜的操作与控制。
2-巯基苯并噻唑的缩合反应包括备料工序和缩合工序,此处就与间歇釜式反应器有关的缩合工序作介绍。则以多硫化钠(Na2Sn)、邻硝基氯苯(C6H4ClNO2)及二硫化碳(CS2)为原料的缩合工序的反应如下。
主反应:
(3-4)
(3-5)
副反应:
(3-6)
二、间歇釜式反应器的工艺流程
(一)工艺流程及说明
1.工艺流程图
间歇釜式反应器单元带控制点的工艺流程图如图3-2所示。

图3-2 间歇釜式反应器单元带控制点的工艺流程图
2.工艺流程说明
来自备料工序的CS2、C6H4ClNO2、Na2Sn分别注入计量罐及沉淀罐中,经计量沉淀后利用位差及离心泵压入反应釜中,釜温由夹套中的蒸汽、冷却水及蛇管中的冷却水控制,设有分程控制TIC101(只控制冷却水),通过控制反应釜温来控制反应速率及副反应速率,来获得较高的收率及确保反应过程安全。
本工艺流程中,主反应的活化能要比副反应的活化能要高,因此升温后更利于反应收率。在90℃的时候,主反应和副反应的速率比较接近,因此,要尽量延长反应温度在90℃以上时的时间,以获得更多的主反应产物。
(二)主要设备及作用
1.间歇反应釜单元主要设备
间歇反应釜单元主要设备及作用见表3-1。
表3-1 间歇反应釜单元主要设备及作用

2.现场手动阀
手动阀见表3-2。
表3-2 手动阀

(三)主要控制点及正常工况工艺指标
1.本单元的调节阀及控制点(控制阀)
调节阀及控制点见表3-3。
表3-3 调节阀及控制点

2.正常工况工艺指标
正常工况工艺指标见表3-4。
表3-4 正常工况工艺指标

(四)仿真操作界面图
1.间歇反应釜系统DCS图
仿真系统中间歇反应釜DCS图如图3-3所示。

图3-3 间歇反应釜系统DCS图
2.间歇反应釜系统现场图
间歇反应釜系统现场图如图3-4所示。

图3-4 间歇反应釜系统现场图
三、间歇釜式反应器的操作与运行
(一)开车前准备
一般间歇釜式反应器开车前准备按如下步骤进行:
(1)通入惰气对系统进行试漏,惰气置换;
(2)投运冷却水、蒸汽、热水、惰气、工厂风、仪表风、润滑油、密封油等系统;
(3)检查转动设备的润滑情况;
(4)投运仪表、电气、安全联锁系统往反应釜中加入原料;
(5)当釜内液体淹没最低一层搅拌叶后,启动反应釜搅拌器;
(6)继续往釜内加入原料,到达正常料位时停止;
(7)升温使釜温达到正常值;
(8)当温度达到某一规定值时,向釜内加入催化剂等辅料;
(9)控制反应温度、压力、反应釜料位等工艺指示,使之达正常值。
(二)冷态开车操作
装置开工状态为各计量罐、反应釜、沉淀罐处于常温、常压状态,各种物料均已备好,大部分阀门、机泵处于关停状态(除蒸汽联锁阀外)。
1.备料过程
(1)向沉淀罐VX03进料(Na2Sn)
①开阀门V9,向罐VX03充液。
②VX03液位接近3.60m时,关小V9,至3.60m时关闭V9。
③静置4min(实际4h)备用。
(2)向计量罐VX01进料(CS2)
①开放空阀门V2。
②开溢流阀门V3。
③开进料阀V1,开度约为50%,向罐VX01充液。液位接近1.4m时,可关小V1。
④溢流标志变绿后,迅速关闭V1。
⑤待溢流标志再度变红后,可关闭溢流阀V3。
(3)向计量罐VX02进料(邻硝基氯苯)
①开放空阀门V6。
②开溢流阀门V7。
③开进料阀V5,开度约为50%,向罐VX01充液。液位接近1.2m时,可关小V5。
④溢流标志变绿后,迅速关闭V5。
⑤待溢流标志再度变红后,可关闭溢流阀V7。
2.进料
(1)微开放空阀V12,准备进料。
(2)从VX03中向反应器RX01中进料(Na2Sn)
①打开泵前阀V10,向进料泵PUM1中充液。
②打开进料泵PUM1。
③打开泵后阀V11,向RX01中进料。
④至液位小于0.1m时停止进料。关泵后阀V11。
⑤关泵PUM1。
⑥关泵前阀V10。
(3)从VX01中向反应器RX01中进料(CS2)
①检查放空阀V2开放。
②打开进料阀V4向RX01中进料。
③待进料完毕后关闭V4。
(4)从VX02中向反应器RX01中进料(邻硝基氯苯)
①检查放空阀V6开放。
②打开进料阀V8向RX01中进料。
③待进料完毕后关闭V8。
(5)进料完毕后关闭放空阀V12。
3.开车
(1)检查放空阀V12、进料阀V4、V8、V11是否关闭。打开联锁控制。
(2)开启反应釜搅拌电机M1。
(3)适当打开夹套蒸汽加热阀V19,观察反应釜内温度和压力上升情况,保持适当的升温速度。
(4)控制反应温度直至反应结束。
4.反应过程控制
(1)当温度升至55~65℃左右关闭V19,停止通蒸汽加热。
(2)当温度升至70~80℃左右时微开TIC101(冷却水阀V22、V23),控制升温速度。
(3)当温度升至110℃以上时,是反应剧烈的阶段。应小心加以控制,防止超温。当温度难以控制时,打开高压水阀V20。并可关闭搅拌器M1以使反应降速。当压力过高时,可微开放空阀V12以降低气压,但放空会使CS2损失,污染大气。
(4)反应温度大于128℃时,相当于压力超过8atm(1atm=101325Pa),已处于事故状态,如联锁开关处于“on”的状态,联锁启动(开高压冷却水阀,关搅拌器,关加热蒸汽阀)。
(5)压力超过15atm(相当于温度大于160℃),反应釜安全阀作用。
(三)热态开车操作
1.反应中要求的工艺参数
(1)反应釜中压力不大于8atm。
(2)冷却水出口温度不小于60℃,如小于60℃易使硫在反应釜壁和蛇管表面结晶,使传热不畅。
2.主要工艺生产指标的调整方法
(1)温度调节 操作过程中以温度为主要调节对象,以压力为辅助调节对象。升温慢会引起副反应速率大于主反应速率的时间段过长,因而引起反应的产率低。升温快则容易反应失控。
(2)压力调节 压力调节主要是通过调节温度实现的,但在超温的时候可以微开放空阀,使压力降低,以达到安全生产的目的。
(3)收率 由于在90℃以下时,副反应速率大于正反应速率,因此在安全的前提下快速升温是收率高的保证。
(四)停车操作
间歇釜式反应器的停车应首先停进催化剂、原料等;再继续加入溶剂,维持反应系统继续运行;待化学反应停止后,停进所有物料,停搅拌器和其他传动设备,卸料;最后用惰气置换,置换合格后交检修。
在冷却水量很小的情况下,反应釜的温度下降仍较快,则说明反应接近尾声,可以进行停车出料操作了。
(1)打开放空阀V12约5~10s,放掉釜内残存的可燃气体。关闭V12。
(2)向釜内通增压蒸汽。
①打开蒸汽总阀V15。
②打开蒸汽加压阀V13给釜内升压,使釜内气压高于4atm。
(3)打开蒸汽预热阀V14片刻。
(4)打开出料阀门V16出料。
(5)出料完毕后保持开V16约10s进行吹扫。
(6)关闭出料阀V16(尽快关闭,超过1min不关闭将不能得分)。
(7)关闭蒸汽阀V15。
四、间歇釜式反应器典型事故及处理
间歇反应釜单元操作的典型事故及处理方法见表3-5。
表3-5 间歇反应釜单元操作的典型事故及处理方法

五、间歇釜式反应器的运行控制
1.反应温度控制
对于反应系统操作是最关键的。反应温度的控制一般有如下三种方法:
(1)通过夹套冷却水换热;
(2)通过反应釜组成气相外循环系统,调节循环气体的温度,并使其中的易冷凝气相冷凝,冷凝液流回反应釜,从而达到控制反应温度的目的;
(3)料液循环泵,料液换热器和反应釜组成料液外循环系统控制反应温度,通过料液换热器能够调节循环料液的温度,从而达到控制反应温度的目的。
2.压力控制
反应温度恒定时,在反应物料为气相时主要通过催化剂的加料量和反应物料的加料量来控制反应压力。如反应物料为液相时,反应釜压力主要决定物料的蒸气分压,也就是反应温度。反应釜气相中,不凝性惰性气体的含量过高是造成反应釜压力超高的原因之一。此时需放火炬,以降低反应釜的压力。
3.液位控制
反应釜液位应该严格控制。一般反应釜液位控制在70%左右,通过料液的出料速率来控制。连续反应时反应釜必须有液位自动控制系统,以确保液位准确控制。液位控制过低反应产率低;液位控制过高,甚至满釜,就会造成物料浆液进入换热器、风机等设备中造成事故。
4.原料浓度控制
料液浓度过高,造成搅拌器电机电流过高,引起超负载跳闸,停转,就会造成釜内物料结块,甚至引发飞温,出现事故。停止搅拌是造成事故的主要原因之一。控制料液浓度主要通过控制溶剂的加入量和反应物产率来实现。
有些反应过程还要考虑对加料速度和催化剂用量的控制。