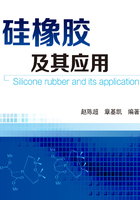
2.4 硅橡胶生胶的种类及制备方法
2.4.1 二甲基硅橡胶
二甲基硅橡胶是分子以Si—O键为主链,侧基全部由甲基组成的聚硅氧烷,其结构式如下:
与二甲基硅油一样,惟聚合度高得多。它是最早合成和使用的通用硅橡胶生胶,其外观为无色透明弹性体,呈半固态状,相对密度约为0.98,折射率为1.4035,具有耐水、耐臭氧、耐电弧、耐电晕和耐气候老化等优点。在-60~250℃温度范围内使用,能保持良好的弹性,具有一般硅橡胶的特性。因此,广泛用作电子电气元件的灌注和密封材料,仪器仪表的防潮、防震、耐高低温灌注和密封材料。也可用于制造模具,用于浇铸聚酯树脂、环氧树脂和低熔点合金零部件,也可用作齿科的印模材料。
由于硅原子上连接的全为惰性的甲基,故硫化活性低,通常用活性较高的有机过氧化物进行硫化。硫化胶力学性能较差,高温永久压缩变形大,不宜于制厚制品,厚制品硫化比较困难,内层亦易起泡,耐热性也差等缺点,目前已很少使用,基本上已被甲基乙烯基硅橡胶所取代,只少量用于某些膏状物载体或织物涂覆,涂布在棉布、纸袋上,可做成用于输送黏性物品的输送带和包装袋。
2.4.2 甲基乙烯基硅橡胶
乙烯基生胶是在甲基硅橡胶的基础上,分子侧链或端基引进少量[0.05%~2%(摩尔分数)]乙烯基而形成的,是目前较常用的一种硅橡胶。其结构式如下:
①甲基封端型
②乙烯基封端型
其中,m=6000~11000n=3~150
由于硅橡胶大分子结构中引入少量乙烯基,极大地提高了硅橡胶硫化活性,故比甲基硅橡胶容易硫化,使得有更多种类的过氧化物可供硫化使用,并可大大减少过氧化物的用量,可大大改善硅橡胶的硫化加工性能和物理机械性能。它除具有二甲基硅橡胶一般特性外,还具有较宽的使用温度范围,可在-60~260℃范围内保持良好弹性,可使抗压缩永久变形性能获得显著的改进,较好的耐溶剂的膨胀性和耐高压蒸汽的稳定性以及优良的耐寒性等,而且又因为采用活性较低的过氧化物进行硫化,从而克服了硫化时产生气泡及橡胶稳定性差的弱点。故一般用甲基乙烯基硅橡胶可制作厚度较大的制品,因此极大地拓展了应用领域;其乙烯基的含量对硫化作用和硫化胶的耐热性有很大影响,含量少则不显著,含量过大(0.5%,摩尔分数)会降低硫化胶的耐热性;端乙烯基生胶的合成,使硫化胶微观分子中端基产生交联,减少了不稳定的“悬挂链”,因而不但性能更好,而且更适于人体材料的制造。
甲基乙烯基硅橡胶性能优异,合成工艺成熟,成本增加不多,因而成为目前用量最大、应用最广、最具有代表性的产品,除大量应用的通用型胶料外,各种专用性硅橡胶和具有加工特性的橡胶也都以它为基础进行加工配合,如高强度硅橡胶、低压缩永久变形硅橡胶、耐热导电硅橡胶、导热硅橡胶及简便操作不需后硫化的硅橡胶、颗粒硅橡胶和医用硅橡胶等。
甲基乙烯基硅橡胶在航空工业上,广泛用作垫圈、密封材料及易碎、防震部件的保护层;在电气工业中可作电子元件等高级绝缘材料、耐高温电位器的动态密封圈、地下长途通信装备的密封圈;在医学上,由于甲基乙烯基硅橡胶对人体的生理反应小、无毒,故用作外科整形、人造心脏瓣膜、血管等。
我国甲基乙烯基硅橡胶于1965年由上海树脂厂和四科院化学研究所共同研究成功并投入生产,产品牌号110-1、110-2、110-3。国内外生产甲基乙烯基硅橡胶的厂商和产品型号见表2-3。
表2-3 国内外生产甲基乙烯基硅橡胶的厂商和产品型号

(1)产品技术指标 国家化工行业标准HG/T 3312~3313—2000规定:110甲基乙烯基硅橡胶产品按其乙烯基含量不同分为110-1、110-2和110-3三种型号。每种型号按分子量大小又分为A和B两种牌号。产品外观为无色透明,无机械杂质。理化性能符合表2-4要求。
表2-4 生胶成品质量指标(化工部标准HG2-1493)

蓝星公司江西星火化工厂的甲基乙烯基硅橡胶企业标准的技术指标如表2-5所示。
表2-5 110甲基乙烯基硅橡胶企业标准的技术指标

它在国家行业标准的基础上增加了低乙烯基和高乙烯基的型号,因而具有更大的适应性。国内各公司产品的技术指标基本相近。
(2)甲基乙烯基硅橡胶生胶的合成方法 热硫化硅橡胶生胶聚合过程包括原料计量、脱水、配料、聚合、催化剂分解、脱低分子、冷却、出料等操作。聚合工艺路线可分为间歇法、半连续法和连续法流程。
无论采用哪种聚合工艺路线,在聚合前要求物料绝对干燥,其方法都是采用在干燥氮气鼓泡下共沸蒸馏出一部分环体混合物(5%~10%)或用分子筛干燥处理。以国内工业生产中连续化工艺为例,流程示意如图2-3所示。

图2-3 甲基乙烯基硅橡胶生胶的合成工艺流程
合格的D4经计量过滤后放入脱水釜中,进行第一次脱水(为保证连续聚合,脱水釜两台交替使用)。脱水釜夹套通入经水预热器预热的水,加热到48~50℃,减压下(真空度-1.3kPa),通入经干燥器干燥的氮气鼓泡搅拌脱水3h,然后再在脱水釜中加入共聚的甲基乙烯基环硅氧烷或甲基苯基环硅氧烷及占环体总量0.01%~0.02%的催化剂——碱胶和适量的止链剂——低黏度硅油,再在同样条件下进行第二次脱水1h。脱水完毕后釜内通干燥氮气解除真空,夹套通水冷却至室温。两次共沸蒸馏出的水及质量为总量5%~10%的D4冷凝后收集,分出水分后返回脱水釜作为原料重复使用。
将聚合釜、物料管、熟化器先抽真空,并加热干燥,然后用干燥氮气将脱水釜压力维护在50~100kPa(表压)下启动计量泵,将脱水后物料以一定速度连续加到温度为(95±20)℃带有搅拌的聚合釜中,在聚合釜中停留1h后打开阀门,边加料边出料进入温度为(115±2)℃的熟化器中,停留2~2.5h,使在熟化器中反应物分子量接近控制值,然后进入脱低分子器。聚合釜、熟化器夹套都用蒸汽加热。
脱低分子器上部列管加热器用导热油作载体加热,其温度保持在100~200℃,下部夹套用蒸汽加热,控制真空度≤-1.3kPa。物料在这里分解催化剂并闪蒸出低沸物,由螺杆出料器连续冷却出料,流入包装桶。
低沸物量为反应物的12.5%~14%,其组成大致是:D451.5%,D531%,D68.5%,D7~D99%。经冷凝器冷凝收集,经处理后可以掺混到原料D4中再用于生胶制造,也可用于生产硅油。
①间歇法。使用间歇法时,选用一台大体积(8~12m3)的带搅拌器的反应釜,将脱水、聚合、中和催化剂及脱除低分子等操作,在一台设备中进行,制备完成后,将产物压入贮存器冷却,准备送往混炼胶装置进一步加工或包装出厂。间歇法工艺流程短,设备台数少,但存在搅拌功率大、能耗高、生产效率低等缺点,GE、信越等公司采用的是间歇法。
②静态混合连续法。使用静态混合连续法生产热硫化硅橡胶的新技术。该技术将静态混合器组成反应器,闪蒸脱分子器和逆向螺杆挤出机结合起来。该工艺具有设备简单、投资少、功力消耗少、产品质量高等优点,在国内得到广泛应用。
该工艺先使物料在低温下(40~45℃)抽真空脱水,然后加入催化剂及其他配合剂,搅拌均匀,用柱塞泵连续送入静态混合器进行预热和聚合反应,通过控制反应条件完成调聚过程,再经加热破坏催化剂和脱除低分子,用逆向旋转螺杆挤出机出料。静态混合器由多节预热筒和反应筒组成,筒内装有静态混合单元(片状波纹填料)。该单元的选择和组装必须合理,使物料轴向和径向助力平衡,达到静态混合的目的。
③釜式反应半连续法。近年来,国内一些公司通过吸收先进技术,自主开发了双釜式反应半连续法合成热硫化硅橡胶新工艺。该技术采用2台反应釜分别进行聚合反应,反应完成后,物料通过双釜轮流切换连续进入闪蒸脱低分子器和螺杆出料机,形成连续法生产。生产设备中原料贮槽、计量槽、过滤器、反应釜、脱低分子器、出料机等全部用不锈钢材料制作,以保证产品质量;聚合反应釜用热油或蒸汽加热,装备有特殊形式的搅拌器。该工艺具有操作稳定,容易掌握,能耗低,产品质量高,装置能力便于放大等优点。目前釜式反应半连法单套生产线能力已达5000t/a。将我国高温胶生产技术提高到一个新水平。
工艺流程方框图如下:
(3)釜式反应 聚合工艺条件和过程。
①脱水。热硫化硅橡胶制备过程中,原料DMC经打入计量槽计量后,首先经过滤以除去部分水分和杂质。然后进入脱水釜进行脱水。原料中存在的水分会破坏催化剂,使聚合反应受到影响,同时,水分也是封端剂,产生羟基封端的硅橡胶分子,影响产品质量。实践表明,原料经脱水后的含水量应控制在50×10-6以内,才能顺利进行高分子聚合反应,因此,脱水工艺是必须严格掌握的。目前,采纳的脱水工艺有三种:a.低温、高真空(40~45℃);b.中温、高真空(80~90℃);c.高温、低真空(105~110℃)。要根据具体情况选择。脱水时间一般为2~3h。为了加强脱水效果,一般都要用干燥氮气鼓泡搅拌。
②聚合和熟化。脱水后的物料用真空抽入聚合反应釜,加热并开动搅拌,先加入封端剂和乙烯基环体后,将物料搅匀并到达一定温度后才加入催化剂开始聚合反应。环硅氧烷在碱性催化下,温度>95℃即可开始开环聚合,105~110℃为较佳聚合温度条件。硅橡胶在聚合过程中只放出少量热,因此聚合温度主要靠外部供热获得。环硅氧烷在引发以后,反应速度非常快,物料的黏度在几分钟迅速达到上百万厘泊(P,1P=0.1Pa·s),形成黏度高峰。由于高聚物的传热性很差,因此,传质和传热都十分困难,要做好匀质和匀热,必须靠加强搅拌。在反应过程中,采用点段式搅拌或连续搅拌是不可少的。这样,平衡反应才能达到最佳效果,产物分子量分布更加均匀。为了减少产物中的低分子,要适当调整反应温度,静态混合器“反应2”的温度要升至大于120℃,釜式反应后期也应有一个提高体系温度(>120℃)的过程。聚合反应过程,一般维持2~3h,物料即可达到平衡,在氮气压力作用下送往下工序。
③催化剂分解。反应完成后,物料经熟化器进入脱低分子器加热升温,以便分解催化剂。暂时性催化剂四甲基氢氧化铵留在物料中将十分有害,必须通过加热使其分解。物料进入脱低器的油加热器后,裂管中胶料的温度可达到160~180℃,经停留足够的时间而达到完全分解。四甲基氢氧化铵的半衰期如下表:
④脱低分子。硅橡胶在调聚反应中达到平衡后,其原料环硅氧烷转化率仅为85%左右,另有15%左右的环体存在胶中成为低分子,必须脱除。目前采用最普遍的方法是将加热分解催化剂后的物料,经过有众多小孔的花板被拉成细丝,进入闪蒸室,在加热和抽真空下,低分子物被抽出经冷凝收集。通过调整体系真空度和温度,可以控制胶料的低分子含量(挥发分值),以满足后期加工的需要。
脱除低分子的胶料进入螺旋出料机出料,经冷却后用塑料袋和纸箱包装。
配方实例:投料进口D4550kg,国产DMC750kg,低分子200kg,乙烯基四环体2.2kg,低黏度乙烯基硅油(20CS)5.5kg,碱胶(3%浓度)2.5kg。按规定的工艺条件进行操作。制得的产品测试结果:外观无色透明胶状液体,分子量60万,乙烯基含量0.17%,挥发分1.8%。
(4)影响产品质量的因素分析
①产品外观。甲基乙烯基硅橡胶的外观是无色透明、无机械杂质。经常易出现的问题是外观变黄。产生的原因一是原料的影响,DMC中如含铁质或呈酸性,极易腐蚀设备而影响产品。另一原因是低分子的反复使用,其中的三甲胺(CH3)3N会累积而浓度增加,经加热氧化而产生黄色物质。
②分子量大小及分布。分子量的大小对硅橡胶的物理机械性能和加工性有较明显的影响,一般可以通过调节配方达到目标值。而分子量的分布,一般要求要适中,尽量减少低聚物的含量,聚合度小于400的分子很少含乙烯基,不易产生交联点,残存于胶料中易使胶料发黏,使硫化胶强度降低。分子量分布的状况受反应温度(平衡温度),搅拌程度和催化剂加入量的影响。要合理选择工艺条件。
③挥发分。生胶若在120℃达到聚合平衡,其可挥发成分可达13%~14%。生胶中挥发分的高低取决于以下因素:脱低分子器的结构(包括花板孔径的大小),脱低分子器的真空度,花板上生胶的温度,生胶的摩尔质量等。一般采用真空度来调节生胶的挥发分。挥发分太大,硅橡胶制品收缩率大,逸出的气体还可能会损害周围的电子元件。挥发分太小,混炼胶加工时,不易吃粉,生产效率低,胶料流动性差。
④三官能链节的含量。生胶中的三官能链节会使线型分子形成支链。在生产过程中,如生胶中存在较多的三官能链节,花板会出现部分堵塞,胶料呈片状而不是呈细丝下落,花板压力升高,出胶速度变慢,从出胶机出口流出的胶料不光滑,有亮点。在相同配方下,生产的胶料分子量偏低。这种生胶在加工混炼胶时,吃白炭黑更困难,白炭黑分散均匀性较差,胶料强度偏低。
生胶中三官能链节的来源:一是原料甲基环硅氧烷(DMC)或甲基乙烯基环硅氧烷(VMC)带来的;二是封端剂带来的。用于制造低黏度硅油的六甲基二硅氧烷,由于其原料成分比较复杂,又不注意精制,因此,经常容易带进杂质。为避免生成更多的三官能链节,必须严格控制所有原料的质量。
⑤分子端羟基。理想的生胶分子是以二甲基乙烯基甲硅氧基封端的。但原料中的水分和SiOH基、碱胶、封端剂中的端羟基链节却会使生胶分子带上端羟基。带有较多端羟基的生胶在制造混炼胶时,会与白炭黑上的羟基发生反应,而使胶料加重结构化。带有大量端羟基的生胶加工性会变差,胶料表面发黏,在开炼机上黏辊,同时,还会使硫化胶黏模,降低生产效率和成品完好率。另外,大量羟基存在还会降低硫化胶的耐热性,其分解温度比完全甲基封端的胶要降低30~40℃。因此,必须尽量减少胶料中羟基封端的存在。国产生胶端羟基的来源之一是原料中的水分。采用合理的脱水条件可以达到降低端羟基的要求;另一方面,采用压缩冷冻法制成的氮气,含水量很低,不会给系统带进水分。但钢瓶氮气往往含有水分,要注意进行干燥。如何减少DMC中微量—OH封端的线型物以减少生胶中的羟基含量,这是提高热硫化硅橡胶质量的关键措施之一。为了判断生胶中羟基含量的多少,可以用下列方法进行测定:将生胶配成甲苯溶液,在此溶液中加入(MeO)4Si和缩合催化剂,生胶的端羟基将发生如下的缩合反应。
上述缩合反应使生胶的分子量增大,并形成支化或交联的分子,从而使溶液的黏度增加。测定溶液黏度的变化,以此来相对判断生胶的端羟基含量。
2.4.3 二甲基双苯基室温硫化硅橡胶
甲基双苯基室温硫化硅橡胶是一种由羟基封端的二甲基硅氧烷链节和二苯基硅氧烷链节组成的聚硅氧烷。其分子结构可表示如下:
用环硅氧烷阴离子开环聚合的方法合成:链段中二甲基链段可由D4开环而来,双苯基链段可由八苯基环硅氧烷开环而来。先由二甲基环四硅氧烷和八苯基环硅氧烷在四甲基氢氧化铵碱胶的催化下,进行碱催化重排化反应。然后,进行KOH裂解分馏得到液态二甲基二苯基环硅氧烷混合环体。再将此混合环体与D4进行碱催化重排成带有活性基聚合物体,然后加水降解成羟基封端的聚二甲基硅氧烷和二苯基硅氧烷。其反应如下:
第一步:
二甲基二苯基环四硅氧烷混合环体(混合四环体),它对应下列各组分:
第二步:
二甲基双苯基室温硫化硅橡胶除具有甲基室温硫化硅橡胶的优良性能外,比甲基室温硫化硅橡胶具有更宽的使用温度范围(-100~250℃),无色、无味、无毒流动液体,呈中性。使用时只要加入交联剂(正硅酸乙酯)和催化剂(二丁基二月桂酸锡)在室温就能硫化成橡胶。苯基含量在2.5%~5%的低苯基室温硫化硅橡胶(108-1)可在-90℃低温条件下保持弹性,是目前硅橡胶中低温性能最好的一个品种;苯基含量在10%~20%的室温胶具有很好的耐辐照、耐烧蚀和自熄性,若在其中加入一定量的耐热添加剂如Fe2O3,等可提高热老化性能,适用于250℃以上高温下使用或作耐烧蚀腻子涂层和包封材料等。因此是国防军工、电子行业不可缺少的。
2.4.4 甲基乙烯基苯基硅橡胶生胶(PVMQ)
甲基苯基乙烯基硅橡胶是在甲基乙烯基硅橡胶的分子链中引入甲基苯基硅氧链节或二苯基硅氧链节而得的产品。其分子结构可表示如下:
或者是
苯基硅橡胶20世纪50年代初由美国研制成功,前苏联也在1970年生产出苯基硅橡胶CKT B-803、CKT B-2-803、CKT B-210和CKB B-2103。我国上海树脂厂则在20世纪60年代中期研制出并中试成功PVMQ120-1和PVMQ120-2。
甲基苯基乙烯基硅橡胶可采用酸催化聚合法或碱催化聚合法制取,前者是二甲基二氯硅烷与甲基苯基二氯硅烷,在硫酸浓度为30%时进行共水解和聚合反应制得;后者是采用八甲基环四硅氧烷与八苯基环四硅氧烷的混合环体在碱性催化剂作用下聚合制得。若要制备二甲基二苯基乙烯基硅橡胶,可采用二甲基二苯基混合环体以及甲基乙烯基环四硅氧烷的混合物,在110℃下用(CH3)4NOH碱胶催化剂开环聚合而制得。
用环硅氧烷阴离子开环聚合的方法合成PVMQ:PVMQ链段中二甲基链段可由D4开环而来,甲基乙烯基硅氧链段可由开环而来,苯基链段可由甲基苯基环硅氧烷开环而来。环硅氧烷的制备通常采用氯硅烷的水解而获取,但由于苯基的空间位阻较大,甲基苯基二氯硅烷单独水解后的水解产物已经固态,无法使其参加后续的反应,因而需要使甲基苯基二氯硅烷和二甲基二氯硅烷按一定的比例先共水解,然后再裂解制得含二甲基硅氧链段的环状甲基苯基硅氧烷。其反应如下:
在装有搅拌装置、加料漏斗及温度计的反应釜中,加入100kg水,在加料漏斗中装入摩尔比为1:1(体积比约为33:50)的二甲基二氯硅烷和甲基苯基二氯硅烷配成的混合液体。开动搅拌,缓慢地把加料漏斗中的液体加入到三口瓶内进行水解缩合,温度控制在30℃左右。加完料后继续搅拌30min,然后静置至分层,分出有机层。有机层用KOH水溶液洗一次,再用温水洗至中性或微碱性,得到含线型和环状硅氧烷的混合物。
将得到的含线型和环状硅氧烷的水解混合物置入有分馏塔的反应釜中,再加入水解物质量0.5%的粉末状KOH。先在减压及60℃左右脱水,待水解物透明后,升温至90~100℃,继续聚合,反应物成胶状,得到含Me2SiO链节的甲基苯基环状硅氧烷。
按配比量加入含Me2SiO链节的环状聚甲基苯基硅氧烷、D4、,催化剂四甲基氢氧化铵0.03%和封端剂低黏度(MDnM)甲基硅油用量0.1%。在减压、通N2条件下,升温保持50℃脱水30min,再升温至100℃聚合2h。结束反应后升温至170~180℃减压条件下破坏催化剂及除低沸物,即得到甲基苯基乙烯基硅橡胶生胶。通过调节环状的聚甲基苯基硅氧烷与D4的配比,可以制出不同苯基含量的PVMQ。
这些性能随分子链中苯基含量的不同而有所变化,一般来说,根据硅橡胶中苯基含量(苯基与硅原子之比)的不同,可将其分为低苯基硅橡胶、中苯基硅橡胶、高苯基硅橡胶。
①低苯基硅橡胶。苯基含量[C6H5/Si]5%~15%(摩尔分数,下同),橡胶的硬化温度降到最低值(-115℃),使它具有最佳的耐低温性能,在-100℃下仍具有柔曲弹力,且与所用苯基单体类型无关,是所有橡胶中低温性能最好的一种。
②中苯基硅橡胶。苯基含量[C6H5/Si]15%~25%,随着苯基含量的增加,分子链的刚性增大,其结晶温度反而上升。它具有卓越的耐烧蚀特性,一旦着火可以自熄。
③高苯基硅橡胶。苯基含量[C6H5/Si]30%~50%,它具有优异的耐辐射性能,耐γ射线为1×108R。一般说来,随着苯基含量的增加,硅橡胶分子链的刚性逐渐增大,硅橡胶的混炼工艺性能变差,耐低温性能逐渐下降,但随着苯基含量的增加,提高了硫化胶的耐燃性和耐辐照性。
其原因是,当橡胶发生结晶或接近于玻璃化转变点或者这两种情况重叠,均会导致橡胶呈现僵硬状态。在聚硅氧烷的侧基上引入适量的大体积的苯基团,使二甲基硅氧烷聚合物链结构的规整性受到破坏,则可降低聚合物的结晶温度,同时由于大体积基团的引入改变了聚合物分子间的作用力,故也可以改变玻璃化温度,扩大了该聚合物材料的低温应用范围。使其具有良好的耐低温性能。因此,甲基苯基乙烯基硅橡胶除了具有甲基乙烯基硅橡胶所有的压缩永久变形小、使用温度范围宽、抗氧化、耐候、防震、防潮和良好的电气绝缘性能外,还具有卓越的耐低温、耐烧蚀和耐辐照等性能。低苯基硅橡胶兼有乙烯基硅橡胶的优点,而且成本也不很高,因此大有取代乙烯基硅橡胶的趋势。
苯基硅橡胶应用在要求耐低温、耐烧蚀、耐高能辐射、隔热等场合。中苯基和高苯基硅橡胶由于加工困难、物理机械性能较差,生产和应用受到一定限制。甲基苯基乙烯基硅橡胶是宇航工业、尖端技术和国民经济其他部门的重要材料之一,可供制作各种模压和挤出制品如用作航空工业的耐寒橡胶和用于耐烧蚀、耐热老化或耐辐射部位的密封圈、垫、管材和棒材等。
硅橡胶暴露于超低温度下不会发生永久性变化。当回到室温放置后,橡胶可重新获得其原有力学性能。然而,最重要的结论是,硅橡胶即使在大多数弹性体脆化并且易于弯曲断裂的温度下仍然保持柔韧,性能良好。
北京航空材料研究院、西北橡胶制品研究院对国产甲基乙烯基硅橡胶和苯基硅橡胶的耐寒性进行的对比试验表明:苯基硅橡胶具有良好的低温弹性,见表2-6。
表2-6 几种硅橡胶性能比较

从上表可见,苯基硅橡胶在-70℃下压缩耐寒系数在0.65以上,具有良好的低温弹性,而乙烯基硅橡胶在-70℃时压缩耐寒系数为0,低温性能较差。
苯基硅橡胶的制备对单体纯度要求较高,工艺技术条件比较严格,因而产品成本高,价格贵,限制了它的应用和发展。
国内外甲基乙烯基苯基硅橡胶生胶主要生产厂家及型号见表2-7。
表2-7 国内外甲基乙烯基苯基硅橡胶生胶主要生产厂家及型号

国产甲基乙烯基苯基硅橡胶的技术指标如表2-8所示。
表2-8 国产甲基乙烯基苯基硅橡胶的技术指标

2.4.5 甲基乙烯基三氟丙基硅橡胶(氟硅橡胶FVMQ)
氟硅橡胶最早于1956年由美国Dow Corning公司和空军部门研制开发,并应用于航空领域,随后前苏联、德国、日本等国先后开发出一系列产品,使得氟硅橡胶性能和质量得到了逐步的改进。我国最早于1966年由中科院、上海有机氟研究所和上海树脂厂共同协作制得相当于美国LS-420的氟硅橡胶生胶,并成功开发出性能优良的SF系列氟硅胶料。
氟硅橡胶是侧链引入氟代烷基的一类硅橡胶,其种类繁多,现已大规模生产的氟硅橡胶主要是以γ-三氟丙基甲基硅氧烷为结构单体的聚合物。常用的氟硅橡胶为含有甲基、三氟丙基和乙烯基的氟硅橡胶,在乙烯基硅橡胶(乙烯基含量一般为0.3%)的分子链中引入氟带烷基(一般为三氟丙基),称甲基乙烯基三氟丙基硅橡胶。其结构式可表示如下:
氟硅橡胶的合成是由三氟丙烯与甲基氢二氯硅烷在氯铂酸催化下加成制得甲基三氟丙基二氯硅烷,甲基三氟丙基二氯硅烷经水解裂解得到1,3,5-甲基三氟丙基环三硅氧烷;然后,1,3,5-甲基三氟丙基环三硅氧烷加入封端剂在热碱催化下开环缩合成硅氟橡胶。反应式如下:
将三氟丙基引入到硅氧烷侧链上,大大克服了硅橡胶的某些缺陷,从而具有一系列优良的性能。国产氟硅橡胶的技术要求(沪Q/HG6-010-83)如表2-9所示。
表2-9 国产氟硅橡胶的技术要求

国产氟硅橡胶性能见表2-10。
表2-10 国产氟硅混炼胶的性能

DC公司的氟硅橡胶的物理机械性能如表2-11所示。
表2-11 DC公司的氟硅橡胶的物理机械性能

2.4.5.1 氟硅橡胶的性能
(1)耐化学药品、耐溶剂和耐油性能 氟硅橡胶与甲基乙烯基硅橡胶相比,其耐溶剂、耐燃料油、耐润滑油、耐化学药品和耐油性极其优良。在相同介质、温度和时间下浸渍后,均显示优良的耐久性,它是目前唯一种在-68~232℃的燃油介质下耐非极性的弹性体。氟硅橡胶耐甲醇汽油性也比较好,在甲醇/汽油混合体系中,经500h长时间浸渍后各项物性几乎没有变化。例如它对脂肪族、芳香族和氯化烃类溶剂、石油基的各种燃料油(1#油、3#油等)、润滑油、液压油以及某些合成油(二脂类润滑油、硅酸脂类液压油)在常温和高温下稳定性良好,这些是单纯的硅橡胶所不及的,此种硅橡胶在非极性溶剂中的膨胀率小。DC公司氟硅橡胶耐药品、耐溶剂和耐油性能见表2-12。
表2-12 DC公司氟硅橡胶耐燃料、耐油、耐溶剂性

注:1psi=6894.76Pa。
(2)耐热性能 氟硅橡胶兼有硅橡胶的耐高低温性能,其高温分解与硅橡胶一样,即有侧链氧化、主链断裂而引起各种复合反应。它的耐热性比一般硅橡胶稍差,分解温度约300℃,工作温度范围:-50~250℃,并放出有毒气体。但通过加入铁、钛、稀土氧化物等少量的热稳定剂可以得到改善。氟硅橡胶与甲基乙烯基硅橡胶的耐热性比较如表2-13所示。
表2-13 氟硅橡胶与甲基乙烯基硅橡胶的耐热性比较

含三氟丙基的氟硅橡胶保持弹性的温度范围一般为-50~200℃,耐寒性及热稳定性好,抗着火性也好,耐高低温性能较乙烯基硅橡胶差,且在加热到300℃以上时将会产生有毒气体。
(3)耐寒性、电性能和耐辐射性能 氟硅橡胶与普通硅橡胶一样,耐低温性能良好。由于氟硅橡胶是以柔软的Si—O键为主链构成的线型聚合物,所以它的低温特性优于比以C—C键为主链的氟橡胶,它的脆性温度可达-85℃,而一般氟橡胶为-30℃。
氟硅橡胶的电性能和普通硅橡胶相近,但其特点是在高温、低温、潮湿、油、溶剂化学、药品、臭氧等苛刻条件下变化很小。
氟硅橡胶的耐辐射性能并不突出,但耐辐老化性能优于甲基乙烯基硅橡胶。
(4)物理机械性能 氟硅橡胶与普通硅橡胶一样,它的硫化胶物理机械性能不高,因此改善和提高氟硅橡胶的物理机械性能是一个重要的课题。
(5)其他性能 氟硅橡胶的耐气候性能非常优良,即使暴露5年后,仍保存有良好的性能。此外,氟硅橡胶的耐臭氧性、防霉性、生理惰性、抗凝血性也十分良好。
2.4.5.2 氟硅橡胶的加工
氟硅橡胶属固态物质,可塑度高,可直接用开炼机或密炼机进行混炼。其开炼加料和工艺过程如下:
生胶(氟硅橡胶+少量硅橡胶)白炭黑+结构控制剂+加工助剂→切割,薄通多次→热处理→返炼,加硫化制→薄通,出片→停放待用。
采用密炼机密炼,可以提高生产效率,降低劳动强度,减少白炭黑飞扬。密炼加料顺序与开炼相同,但热处理在密炼机中同时进行。密炼时加料完成以后,要升温至160~180℃,并抽真空至-0.07~-0.06MPa,热处理1~1.5h。出料后,胶料要冷却停放12h以上,然后再返炼,在滤胶机用150~200目金属网过滤,包装待用。
胶料经停放后,出现结构化现象,凝胶含量增加,所以使用时必须进行返炼,胶料返炼要适度,做到柔软、表面光滑即可。如返炼过度,可能使胶料分子量下降,胶料发黏,对加工和产品质量不利。
氟硅橡胶硫化是分一段、二段两次完成的。一段硫化时间短(3~15min),仅能使制品达到定型。经过二段硫化(3~6h)后才能达到完全硫化,硫化胶的各种性能才能达到稳定。模压制品和挤出制品的一段硫化和二段硫化条件如表2-14和表2-15。
表2-14 模压制品一段硫化条件

表2-15 挤出制品的一段硫化条件

2.4.5.3 硅氟橡胶的应用
硅氟橡胶是兼具有硅橡胶和氟橡胶两者特性的强性材料,与甲基乙烯基硅橡胶相比,最大的特点是耐油、耐溶剂,优良的电性能及回弹性能和氟橡胶的特性——耐饱和蒸汽和高温抗降解性能;与氟橡胶相比,它的耐热、耐寒和压缩永久变形更优,而且,物性对温度的依赖很小,从高温到低温都显示出了优良的性能。因此,硅氟橡胶作为一种新的高性能材料正在广泛地被应用。
但与硅橡胶相类似,氟硅橡胶强度较差,表面能低,属于较难粘接的材料,具有加工困难等缺陷,另外随着三氟丙基的引入,给硫化造成困难,所以研究出合适的配方和加工工艺,提高胶料的使用性能,对氟硅橡胶的应用有着至关重要的作用。
氟硅橡胶在电绝缘性能方面较乙烯基硅橡胶差得多。在氟硅橡胶的胶料中加入适量的低黏度羟基氟硅油,胶料热处理,再加入少量乙烯基硅橡胶,可使工艺性能显著改善,有利于解决胶料黏辊和存放结构化严重等问题,能延长胶料的有效使用期。在上述氟硅橡胶中引入甲基苯基硅氧链节时,会有助于耐低温性能的改善,且加工性能良好,具有良好的挤出性能。
氟硅橡胶的应用主要在航天航空、电子通信、车辆船舶、精密仪器、石油化工和医疗卫生等领域。例如航空设备中的航空薄膜,静、动态密封件;超音速飞机整体油箱的密封、火箭、导弹、宇宙飞行、石油化工中用作与燃料油和润滑油接触整体油箱的衬里、密封、胶管、垫片、嵌缝、汽车发动机曲轴后密封圈、汽缸垫、燃油泵密封件、油箱盖垫圈、滤油器密封件、燃油泵隔膜,氟硅橡胶垫圈,垫片的黏结固定;硅橡胶和氟硅橡胶的黏合,以及化学工程和一般工业上耐燃料油;耐溶剂部位的黏结,也可用于制造耐腐蚀的衣服、手套以及涂料、胶黏剂等。
2.4.6 甲基三氟丙基室温硫化硅橡胶
(1)技术路线 以氟硅单体(3,3,3-三氟丙基、三甲基环三硅氧烷)为原料,以氢氧化钠为引发剂,在羟基氟硅油的存在下实施调节聚合,得到所需分子量的氟硅聚合物。
(2)反应机理
①阴离子开环聚合(链的引发和链增长)
②羟基氟硅油使聚合链转移
③平衡化反应
④链终止反应
(3)工艺流程
(4)工艺过程
①聚合与中和。将和羟基氟硅油按比例加入带有机械搅拌装置的聚合釜中,在50~60℃及1.3~2.6kPa下抽空脱水1h,加入30~80×10-6的氢氧化钠胶浆,搅拌0.5h,使之混合均匀。升温至120℃,聚合开始,当达到或接近预定黏度值时,即停止反应,降温至70~80℃,加入与反应体系中的氢氧化钠等当量的乙酸水溶液,继续搅拌半小时。
②水洗。搅拌下,经乙酸中和过的聚合物用1.5倍(净重)的乙酸乙酯溶解成均相,加入2倍(质量)的去离子水,剧烈搅拌半小时,使其充分混合,然后倒入分液漏斗,静置分层。分出的下层液体,在室温下用真空泵抽出溶剂,待溶液变稠后,逐步提高真空度,同时慢慢升温,待胶液变至均匀透明后降温。
③脱低沸物。将所得聚合物放入足够大的搪瓷盘中,放进真空干燥箱,升温并开启真空泵,至180℃,0.1kPa下维持4~6h后降温,关闭真空泵,切断电源。取出胶样,测试性能,满足指标要求,包装入库。
(5)影响因素
①PTFPMS的制备技术主要有两种:一是在混合催化剂存在下,进行本体聚合然后出料(美国道康宁公司技术路线);二是在催化剂、分子量调节剂存在下,进行本体聚合,然后经后处理再出料(上海三爱富公司技术路线)。这两种路线对比见表2-16。
表2-16 道康宁公司与三爱富公司技术路线对比

在PTFPMS合成过程中,采用新的合成方法,加入分子量调节剂,使黏度控制较稳定,反应催化剂以钠胶代替锂胶,降低了聚合反应温度,增加了生胶后处理工艺,合成的PTF PMS生胶质量明显提高,硫化好,能稳定贮存。
②分子量封端剂对聚合产物的影响。目前是以釜式反应为主制备含氟硅聚合物,该聚合方法的主要问题是聚合反应速率太快,含氟硅聚合物在聚合反应过程中,在很短的时间内,随着聚合物分子链的快速增长,黏度快速增加,使传质、传热变得非常困难,造成聚合物分子量难以控制、分子量分布宽的问题,影响氟硅橡胶的性能。
另外,3,3,3-三氟丙基甲基环三硅氧烷单体的聚合反应对单体的纯度要求非常高。当单体的纯度不能达到一定值(例如99.0%)时,要么聚合反应不能进行,要么得到低分子量的聚合物。结果,不能采用甲基硅油、乙烯基硅油等分子量调节剂来控制聚合物的分子量和分子量分布。否则,这些分子量封端剂会起杂质的作用,影响聚合反应的进程和最终产品的性能。
经过大量实验研究发现,当在上述硅醇盐催化剂组分中加入选自甲基氟硅油、羟基氟硅油、乙烯基氟硅油的含氟有机硅低聚物时,形成的催化剂组合物可在含氟硅聚合物的合成过程中按需要控制该聚合物的分子量和分子量分布,同样重要的是,这些含氟有机硅低聚物不会影响共聚单体的聚合活性和最终产品的性能。
上述含氟有机硅低聚物在聚合反应中起分子量封端剂的作用,但是又不同于甲基硅油、乙烯基硅油等分子量封端剂,即它不会对聚合单体的聚合活性产生不利影响,也不会对最终产品的性能产生影响。
液体氟硅橡胶聚合反应过程及机理:在聚合反应开始时加入作为分子量封端剂的含氟有机硅低聚物,用以控制聚合物的分子量分布,使之不至于过宽,并向反应体系中加入碱金属硅醇盐催化剂组分,在一定温度、真空度下引发聚合反应。聚合反应的初期阶段,以的开环聚合为主要反应。由于开环反应是放热反应,因此整个聚合体系的温度上升,聚合物分子量逐步增长。加入分子量调节剂的目的是控制
开环速度,以及适当控制聚合反应后期的缩聚反应速率,提高聚合物的搅拌混合质量,延长聚合反应时间,最终控制生成聚合物的分子量分布。
没有加入分子量封端剂,氟硅聚合反应速率太快,真正聚合时间一般为10min左右,分子量呈几何级数增长,一旦到达所需分子量,分子量难以控制,另外,聚合产物分子量分布宽,聚合产物的挥发分较高,不利于聚合产物的硫化加工。
加入作为分子量封端剂的含氟有机硅低聚物,聚合反应速率明显降低,分子量不是呈几何级数增长,也就是说用分子量调节剂能够控制聚合反应速率,从而可以延长聚合反应时间,能够间接调节氟硅聚合物的分子量。另外,加入分子量封端剂后,分子量分布较均匀。但是,分子量封端剂毕竟是小分子,过多使用虽然会使氟硅聚合物的分子量分布更加均匀,可是却会使聚合物硫化加工后的力学性能有所降低。
总之,在釜式反应过程中,加入分子量封端剂的氟硅聚合物分布的均匀性明显好于未加分子量调节剂的氟硅聚合物,并且更利于聚合物的硫化加工。为防止聚合物链中引入其他杂质,同时又保证聚合物为端羟基,加工时又采用脱小分子的缩合型硫化方法,因此采用羟基氟硅油作为黏度封端剂,得到效果如表2-17所示。
表2-17 聚合物黏度、得率与分子量封端剂用量的关系

从表2-17看出:分子量封端剂用量与聚合物的得率基本无关,而聚合物的黏度虽然差别很大,但无规律变化,说明聚合单体基本上都参加了聚合反应,进入了聚合物链。但是聚合物的端羟基在聚合催化剂NaOH的作用下,又发生了分子链间的缩合,使聚合物黏度进一步提高。
因聚合物的末端硅羟基是一高活性基团,在一定的条件下会同时发生分子间或分子内的缩合反应,而这两个反应的比例呈无规律的变化,致使控制黏度困难,因此,不可能通过调节配方来达到控制黏度的目的,为此,我们采取直接方法。即直接测定反应过程中的黏度确定反应终点的办法,达到控制聚合物及其保持足够量交联活性端羟基的目的。实践证明,用直接法控制分子量,经过后面严格的后处理,可以得到所需黏度的聚合物,其分子量分布也较合理。
③聚合反应催化剂的选择。有机硅高分子聚合物的开环聚合一般都使用阴离子型催化剂,即碱性催化剂如季磷碱、季铵碱、碱金属的氢氧化物及其硅醇盐。其碱性强弱顺序如下:季磷碱>季铵碱≥氢氧化铯(CsOH)>氢氧化钾(KOH)>氢氧化钠(NaOH)>氢氧化锂(LiOH)。一般来说,碱性越强,开环聚合的温度越低,达到平衡的时间越短。采用氢氧化锂、氢氧化钠、氢氧化钾、四甲基氢氧化铵作为选择催化剂,为了使聚合反应能平稳地进行,一般都使用比较温和的催化剂如氢氧化锂或氢氧化钠。
以前都使用MOH作为碱性催化剂,此时使用的反应单体为纯度超过99%,由于氢氧化锂使开环聚合的温度为125~145℃,在此温度及负压下,
及其他单体极有可能被部分抽出,如果单体纯度再差一点,极有可能不聚合或生成低聚物。因此,在随后的实验中,选用NaOH作聚合催化剂组分,降低了聚合反应温度(聚合温度100~120℃),降低成本,节约能源。
为了提高催化剂在中的分散性,使聚合物的分子量分布比较均匀,便于精确和方便计量,通常把所述催化剂组分制成具有下列通式的硅醇盐形式:
上述硅醇盐化合物可按如下反应方程制得:
上述硅醇盐化合物是将高纯度(纯度>99.5%)的氢氧化钠细粉与化学计量的经脱水处理的相混合,在90℃/10mmHg(1mmHg=133.322Pa)的条件下聚合5~30min制得的。
从表2-18可见,(CH3)4NOH的用量最少,聚合时间最短,NaOH和KOH,虽然聚合时间相近,但KOH的聚合温度要比NaOH的聚合温度低20~30℃。LiOH的聚合温度最高,聚合时间最长。这四种催化剂的聚合速率以下列顺序递增:LiOH<NaOH<KOH<(CH3)4NOH,而它们的碱性也以同样的顺序递增。虽然(CH3)4NOH属于暂时性催化剂,但是它的聚合速率太快,聚合物的黏度难以控制,因此弃用;LiOH、NaOH、KOH均属永久性催化剂。LiOH反应时间长,温度较高,而KOH活性相对较高,聚合物黏度较难控制,因此,选择NaOH作为PTFPMS的聚合催化剂。
表2-18 催化剂的用量、聚合温度和聚合时间之间的关系(聚合物黏度200Pa·s)

(6)产品性能指标 本产品为羟基封端的聚(3,3,3-三氟丙基甲基)环三硅氧烷,俗称液体氟硅橡胶,(简称PTFPMS)化学结构式为:
①外观:透明无色或淡黄色黏稠液体,无明显可见的外来杂质。
②挥发分:不大于3%。
③黏度:
A型 1~40Pa·s
B型 60~250Pa·s
④拉伸性能:
(A型)硫化后不同条件下的拉伸性能应符合以下要求
⑤腐蚀性:对铝合金LY-12CZ去包铝不腐蚀。
2.4.7 亚苯基硅橡胶和苯醚基硅橡胶
(1)亚苯基硅橡胶 亚苯基硅橡胶是在聚硅氧烷主链上引入亚苯基的一类硅橡胶。其结构可表示为:
式中,Ar为亚苯基或联亚苯基,x:y=1:(2~5),(x+y):z=1000:3
亚苯基硅橡胶可用缩聚法生产,首先,甲基苯基二氯硅烷用乙醇醇解制成甲基苯基二乙氧基硅烷,然后甲基苯基二乙氧基硅烷用水/醇混合物在醋酐存在下催化水解,制得甲基苯基硅氧烷二醇;同时,用相近的方法制取乙烯基苯基硅二醇;最后用甲基苯基硅氧烷二醇,1,4-双(羟基二甲基硅烷)苯和乙烯基苯基硅二醇在(CH3)4NOH作用下催化缩聚。
由于亚苯基的引入,因而使硅橡胶的耐辐射性能大大提高,同时因芳环的存在使分子链的刚性增大,柔顺性降低,玻璃化温度提高,耐寒性能下降,而拉伸强度则有所增高。亚苯基硅橡胶具有优良的耐高温、抗辐射性能,耐高温可达250~300℃,且有良好的介电性能和防潮防霉耐水蒸气等特性。在亚苯基硅橡胶的生胶组成中,当亚苯基含量为60%、苯基含量30%、甲基含量10%(乙烯基含量0.6%)时是适宜的,在这种情况下,硫化胶具有良好的综合性能。
室温硫化亚苯基硅橡胶是硅亚苯基硅氧烷聚合物,可适用原子能工业、核动力装置以及宇宙飞行等方面作为耐高温、耐辐射的粘接密封材料以及电机的绝缘保护层等。
亚苯基硅橡胶的突出优点是具有优异的耐高能射线性能。试验证明经受1×109Rγ射线或1×1018中子/cm2的中子照射后,仍可保持橡胶弹性,比通用的甲基乙烯基硅橡胶大10~15倍,比高苯基硅橡胶大5~10倍。因此,可用于宇宙飞行、原子能工业和核动力装置等作为耐高温、耐高能辐射的粘接密封材料、电机的绝缘保护层、电缆、护套、垫圈以及热收缩管等。国产亚苯基硅橡胶于20世纪70年代由晨光化工研究院研究成功并投入中试。
亚苯基硅橡胶的缺点是低温性能不佳,脆性温度为-25℃,影响了它在某些方面的应用,亚苯醚基硅橡胶的低温性能则远,较亚苯基硅橡胶为好,脆性温度为-64~70℃。
(2)苯醚基硅橡胶 苯醚基硅橡胶是分子主链引入苯醚基和亚苯基基团的聚硅氧烷。其分子结构可表示为:
苯醚基硅橡胶具有良好的力学性能,一般拉伸强度可达150~180kgf/cm2(即14.7~17.7MPa)远高于乙烯基硅橡胶强度,同时具有优良的耐辐射性能并优于亚苯基硅橡胶。它可耐长时间250℃热空气老化,老化后仍具有较高的强度。苯醚基硅橡胶的低温性能虽然比乙烯基硅橡胶差,但却远优于亚苯基硅橡胶。其介电性能与乙烯基硅橡胶接近,但苯醚基硅橡胶的耐油差,既不耐非极性的石油基油,也不耐极性的合成油(如4109双酯类合成润滑油、磷酸酯液压油)。总之,苯醚基硅橡胶与乙烯基硅橡胶相较具有较高的强度和抗辐射性能,相似的耐高温性能和介电性能,较差的低温性能、耐油性能和弹性。苯醚基硅橡胶具有良好的加工工艺性能,可用于制造特殊要求的模型制品和压出制品。国产苯醚基硅橡胶于20世纪70年代由武汉化工研究所研究成功并投入中试。
2.4.8 腈硅橡胶(NVMQ)
腈硅橡胶是无色透明高黏滞塑性线型高分子化合物,分子量在50万~80万之间,主链由硅和氧原子组成,与硅相连的侧基为甲基、乙烯基和氰基烷基。氰烷基可以是β-氰乙基或γ-氰丙基,前者可由甲基(2-氰乙基)环硅氧烷与八甲基环四硅氧烷及少量四甲基四乙烯基环四硅氧烷及少量封端剂在催化剂存在下,进行催化聚合来制取;后者可以由丙烯腈与含氢氯硅烷催化加成制得甲基氰烷基二氯硅烷,然后甲基腈硅烷二氯硅烷和二甲基二氯硅烷进行共水解,生成含腈烷的环状化学物,再在碱性催化剂作用下开环缩合成高聚物。含甲基、氰烷基和乙烯基的硅橡胶其结构式可表示如下:
腈硅橡胶的技术指标如表2-19所示。
表2-19 腈硅橡胶的技术指标

腈硅橡胶除具有一般硅橡胶耐高温、耐低温、耐气候、耐老化、耐臭氧等性能外,还具有耐油、耐非极性溶剂等特性,是一种耐高低温、耐油弹性体。
配合各种添加剂,腈硅橡胶可混炼成均相的胶料,在有机过氧化物作用下,可硫化成弹性橡胶制品。其硫化胶拉伸强度7.0MPa;伸长率200%;硬度(邵尔A)60;拉断永久变形0~1.5%;脆化温度-75℃;耐油性(TC-1#油180℃×24h)增容50%。可用作在-60~+180℃下长期工作的耐油橡胶制品。
由于聚合物分子侧链中含有β-氰乙基或γ-氰丙基强极性基团,大大增加了分子链间作用力,除具有硅橡胶的耐光、耐臭氧、耐潮、耐高低温和优良的电绝缘性能外,腈硅橡胶的主要优点是耐油和耐溶剂的性能优异,提高了耐油、耐非极性溶剂性能,如耐脂肪族、芳香族溶剂的性能好,其耐油性能与普通耐油丁腈橡胶相接近,可用作油污染部件及耐油电子元件的密封灌注料。同时,由于引入一定量的氰烷基,破坏了聚合物结构的规整性,也大大改善了耐寒性。
氰烷基的类型及其含量,对性能影响很大,如含有7.5%(摩尔分数)γ-氰丙基的硅橡胶,低温性能与低苯基硅橡胶相似(其玻璃化温度为-114.5℃),耐油性比苯基硅橡胶好。随γ-氰丙基含量增加至33%~50%时,则耐寒性降低,耐油性能提高,耐热为200℃。用β-氰乙基代替γ-氰丙基能使腈硅橡胶的耐热性进一步提高,可耐250℃热空气老化。因此,可做成耐油橡胶制品用于航空工业、汽车工业和石油工业上;也可作为高性能飞行器的环境密封剂及油箱密封剂,在-54~200℃以上能保持密封。腈硅橡胶可用普通设备进行加工。国产腈硅橡胶于20世纪70年代由中科院化学所和吉林化工研究院共同研制成功并投入中试。
2.4.9 羟基封端的硅橡胶
羟基基封端的硅橡胶是指羟基封端的聚二有机硅氧烷,是一种新型的直链状高分子量的聚有机硅氧烷合成材料,其物理形态通常为可流动的液体或黏稠的膏状物,结构式为:
式中,R为甲基、苯基、三氟丙基等,分别对应甲基羟基硅橡胶、甲基苯基羟基硅橡胶和羟基氟硅橡胶。
化学名称为α,ω-二羟基聚二甲基硅氧烷,习惯上将黏度为2500mPa·s以上的羟基聚硅氧烷称107硅橡胶。
本品为无色透明液体,具有优异的电绝缘性和耐高低温性,闪点高,凝固点低,可在-50~+250℃条件下长期使用,黏温系数小、压缩率大、表面张力低、憎水防潮性好、化学惰性、生理惰性。
羟基硅橡胶技术指标,表2-20为固化前,表2-21为固化后。
表2-20 固化前技术指标

表2-21 固化后技术指标

本品除具有甲基硅油的一般性能外,还具有羟基的反应活性,可用它制成一些新的材料,或交联成弹性体(或膜体)。
羟基封端的硅橡胶是由硅氧烷单体聚合而成的、其分子两末端带有羟基的有机硅材料。即用八甲基环四硅氧烷(D4)在酸或碱作用下开环加水降解而成;也可用硅橡胶在高压釜同加水、碱催化降解而成。近年来主要羟基硅橡胶的制备方法如下。
①碱催化Me2SiCl2水解物平衡聚合法。采用价格较低的Me2SiCl2水解物替代DMC(二甲基环硅氧烷)制备107胶(高摩尔质量的羟基甲基硅油),可降低室温硫化硅橡胶的生产成本。将3500g Me2SiCl2水解物置于反应瓶中,在90℃脱水1h,升温至120℃时加入氢氧化钾,140℃聚合4h,加入磷酸中和15min,最后脱除低沸物可得107胶。
②低摩尔质量HO(Me2SiO)nH催化缩聚法。Me2SiCl2水解物由低摩尔质量HO(Me2SiO)nH与环硅氧烷组成,首先在减压条件下,蒸除环硅氧烷,使两者分离,然后将剩余的低摩尔质量HO(Me2SiO)nH在KOH催化下进行缩聚可制备高摩尔质量的107胶。
③环硅氧烷与水的调聚反应。D4或DMC在碱性催化剂下发生聚合反应到一定程度后,将雾化水喷洒于聚合产物表面使之发生降解反应,得到羟基甲基硅油。将D4加至反应釜,脱水后加入Me4NOH,在110℃聚合20min,待高聚物黏度达530Pa·s时,将液态水经雾化器雾化后在8s内喷洒于高聚物表面使之降解,继续搅拌5min,真空脱除低沸物,即得267kg高摩尔质量的羟基甲基硅油。
④烷氧基硅烷水解缩合法。由Me2SiCl2直接水解缩合制低聚合度(n<10)的HO(Me2SiO)nH比较困难,但由Me2Si(OR)2(R为Me、Et)水解可得到良好收率的低聚合度HO(Me2SiO)nH。采用烷氧基硅烷和水为原料,通过盐酸调节体系pH值为3~4。水解反应结束后,向体系中加入Na(K)H2PO4/Na(K)2HPO4水溶液调节体系pH值为5~7。减压蒸除醇和水后,过滤,得到羟基封端硅油。产品的稳定性好,在25℃下放置7天后,平均聚合度变化不大。Me2Si(OMe)2在MgO催化下水解可得到羟基质量分数为11.5%的甲基羟基硅油,且不含有二甲基环硅氧烷。Me2Si(OMe)2在pH=4.2的酸性条件下水解,采用MgO中和,也可得到低摩尔质量的羟基甲基硅油。
⑤羟基甲基苯基硅橡胶的制备可通过二羟基甲基苯基硅烷[MePhSi(OEt)2水解物]、D2和Me4NOH按比例加入反应瓶中,聚合结束后,通入一定量水蒸气,并保持反应物温度在120~130℃,降解后即得。
⑥羟基氟硅橡胶主要通过甲基三氟丙基环硅氧烷在碱催化下与水反应而得。在LiOH及邻苯二甲酸二甲酯作用下,使[—Me(CF3CH2CH2)SiO]3与水在80℃下开环聚合,得到黏度(25℃)为17Pa·s的HO[—Me(CF3CH2CH2)SiO—]nH。将[—Me(CF3CH2CH2)SiO]3、H2O、KOH及助催化剂MeO(CH2CH2O)3Me在35℃下反应3h,而后加入硅基磷酸酯中和,得到黏度(25℃)为1.36Pa·s的HO[Me(CF2CH2CH2)SiO]nH。
实例:直接使用四甲基氢氧化铵溶液作催化剂的改进工艺生产室温硫化硅橡胶,工艺流程如下:
将计量的DMC抽入反应釜中,升温至85℃,真空脱除反应物内水分。直接向反应物中加入适量的四甲基氢氧化铵溶液催化剂,控制反应温度(95℃),使之发生聚合反应,当聚合物达到一定聚合程度后,向其中加入降解水降解,实现聚合物羟基封端,待聚合物达到预期分子量后,常压升温至160℃,破坏催化剂;在真空度0.096MPa下,N2鼓泡,升温至200℃,脱除反应物系中低沸物。冷却后出料包装。
改进前后工艺参数对比如表2-22所示。
表2-22 改进前后工艺参数对比

由于四甲基氢氧化铵是强碱,属极性物质,与反应单体不互溶,原生产时需制成硅醇盐使用,但硅醇盐的质量波动,直接影响聚合过程的操作,造成生产工艺难控制,且费时费工,操作控制要求高。为此,把四甲基氢氧化铵配成一定浓度的溶液,适时直接加入反应物中,加快搅拌速度,使其在体系内充分分散,起到均匀催化的作用,其优点主要有:简化工艺,省略了制作硅醇盐的过程;避免了因硅醇盐质量的波动而导致聚合反应的波动,使整个反应更易控制并方便了操作;能更好地发挥四甲基氢氧化铵的催化活性。因直接用四甲基氢氧化铵作催化剂,是在较高的反应温度下进行,充分发挥了其催化活性,聚合反应速率更快,加之反应过程比较易控制,因而可缩短生产周期。
实际生产表明,聚合阶段反应体系所能达到的聚合程度,对转化率影响最大。如果聚合程度不够,则转化率偏低;而聚合程度太高,降解反应又较难进行。因此,在反应中既要获得适宜的聚合程度,又要使转化率达到相应的较高水平是本项控制的关键。在实际操作中,通过搅拌电机的电流大小来控制转化率完全可行,搅拌电机的电流与反应转化率的关系如图2-4所示。当聚合程度增加时,搅拌电机的电流逐渐增大,当聚合程度达到反应的最佳点时,设定热继电器保护装置自动断开,以此作为控制聚合程度的控制点,此时进行下一步的降解反应。由于聚合度适宜,反应较易进行,可获得相对较高的转化率。此方法简单可靠,可以较容易地将反应的转化率控制在82%左右。

图2-4 搅拌电机的电流与反应转化率的关系
在室温硫化硅橡胶生产过程中,直接使用四甲基氢氧化铵溶液作催化剂,并增加了反应的投料量,从而简化了生产过程,提高了产品的稳定性。以搅拌电机的电流来控制反应的转化率,可以较容易地将反应的转化率控制在82%左右。改进后的生产工艺与原生产工艺相比较,缩短了生产周期,降低了设备损耗,提高了生产效率,使生产成本降低,操作更加简便,产品质量稳定可靠,收到了理想的效果。国产羟基封端二甲基硅橡胶于20世纪60年代分别由上海树脂厂和沈阳化工研究院研究成功并投入生产;国产羟基封端的二甲基二苯基硅橡胶于20世纪70年代由上海树脂厂研究成功并投入生产,产品牌号为108-1、108-2。
室温硫化硅橡胶主要用于无线电,电子仪器,半导体元件,医疗器械的填孔嵌缝,涂布密封,浇铸定型和生产特殊用途的硅橡胶制品:
①在RTV模具硅橡胶、消泡剂、聚硅氧烷玻璃胶中作主要原料;
②室温硫化硅橡胶由于具有优异的仿真性,脱模性和极低的收缩率,并具有加工成型方便,以及耐热老化的特点,因此用来生产制模硅橡胶,俗称模具胶,特别适于制造精密模具和印模材料;
③由于硅橡胶具有高强度,低模量,高伸长率和高压缩强度,以及在恶劣环境中能保持优良的粘接力,因此用来生产建筑行业的嵌缝密封材料;
④利用硅橡胶优良的介电性能,良好的粘接强度,优良的化学稳定性,来生产硅橡胶密封/胶黏剂;
⑤硅橡胶具有良好的电气绝缘性和防水剂,可在无线电、电子仪器、半导体、电子计算机等电子元器件及组合件方面作绝缘防潮、防震、耐热的灌注密封材料;
⑥在汽车、机械、纺织、塑料、印刷行业方面作橡胶辊筒材料。
2.4.10 乙烯基聚硅氧烷
端乙烯基聚二甲基硅氧烷(Vi-PDMS)与端乙烯基聚甲基乙烯基硅氧烷(Vi-PMVS)是制备加成型硅橡胶的主要原料。其制备原理是利用四甲基二乙烯基二硅氧烷(双封头)、八甲基环四硅氧烷(D4)、乙烯基环体()在催化剂、加热或辐照作用下发生开环聚合反应,使D4和
开环后的—Si(Me)2—O—链节插入到双封端的两乙烯基之间,从而增加了含乙烯基硅油的分子量,合成了端乙烯基聚二甲基硅氧烷(Vi-PDMS)和端乙烯基聚甲基乙烯基硅氧烷(Vi-PMVS),其反应方程式如下:
其中改变双封端与D4/MViDnMVi的投料比,可以制得不同分子量的乙烯基硅油;改变D4和MViMVi的投料比可以制得不同乙烯基含量的乙烯基硅油。
环硅氧烷在催化剂、加热或辐照作用下,可以开环聚合得到高摩尔质量的线型硅氧烷,其中以按离子型机理进行的催化聚合反应最为重要。在催化剂催化下通过阳离子或阴离子开环聚合反应而成。常用的阳离子开环聚合反应的催化剂为强质子酸(如H2SO4、HCl、HNO3)及路易斯酸(如AlCl3、FeCl3、SnCl4等);常用的阴离子开环聚合反应的催化剂有:碱金属K、Na、Li的氢氧化物或季铵氢氧化物等。
采用酸催化平衡法,产物需要多次水洗去酸,工艺过程烦琐复杂,在工业上应用不多,因此,多采用工艺相对简单的碱催化法。其中四甲基氢氧化铵[(CH3)4NOH]因催化活性高且反应后可通过加热的方法除去而得到广泛的应用,聚合过程就是阴离子催化的开环聚合反应,即碱性催化剂(亲核试剂)的OH—与[(CH3)2SiO]4中硅原子的3d轨道配位,导致[(CH3)2SiO]4内电子云密度重新分布,在加热条件下引起Si—O—Si键的断裂开环,生成链端含阴离子的线状硅氧烷低聚体,后者进一步与[(CH3)2SiO]4反应,使硅氧烷链逐步增长:
乙烯基硅油的制备:将新蒸馏的D4加入到带搅拌器、回流冷凝管及温度计的三口烧瓶中,加热到95℃(或110℃),加入计量的端乙烯基硅油和;搅拌数分钟后,在常压且氮气保护下加入催化剂碱胶(碱胶的用量:以Me4NOH计,为D4、
和双封端质量的200×10-6);加大通氮量,将温度维持在95℃(或110℃)至黏度不变为止;然后,迅速升温至180℃,分解碱胶(CH3)4NOH,通氮气以带走碱胶分解产生的三甲胺,直至体系呈中性为止;最后在150℃、-0.098MPa条件下脱低沸物,剩下的即为产物乙烯基硅油。
图2-5为乙烯基硅油红外光谱表征。在波数为1000~1100cm-1处的强双吸收峰是—SiOSi—的特征峰;1601cm-1和1598cm-1为—CH=CH2的伸缩振动吸收;3056cm-1、3059cm-1和3020cm-1为—CH=CH2中C—H的伸缩振动吸收:波数为1260cm-1附近尖锐的单吸收峰、800cm以附近强的单吸收峰,说明有—CH3基团;在3500~3700cm-1处有吸收峰,说明有羟基存在,这可能是由乙烯基硅油在放置过程中吸湿所造成的,从图上可以看出,该处吸收峰的强度很小,说明羟基的含量很少。

图2-5 乙烯基硅油的红外吸收光谱
2.4.11 有机硅橡胶乳液
相对于传统的RTV硅橡胶,水基硅橡胶的发展比较缓慢。与传统的室温硫化硅橡胶不同,水基硅橡胶是硅橡胶的水分散体,它通过固化剂交联,水分蒸发后这些粒子不可逆地聚结成有机硅橡胶弹性体。
早在1948年,就出现了采用机械法制备聚硅氧烷乳液的报道;然而此方法只适合于乳化低摩尔质量的聚硅氧烷。1959年,Hyde J F等人报道了通过乳液聚合方法,将硅氧烷环状低聚物在强酸作用下聚合成高摩尔质量聚硅氧烷的方法;1966年,Findlay D E等人用具有乳化功能的烷基磺酸乳化硅氧烷环状低聚物,制成了高摩尔质量的聚硅氧烷乳液,同时还制备出交联的硅乳胶;1967年,Cekada Jr J制成了拉伸强度达5.3MPa,伸长率达1000%的硅乳胶,其组分包括聚硅氧烷乳液、烷氧基硅烷交联剂、有机锡催化剂和硅树脂。20世纪70年代,水基硅橡胶基本没有什么进展。1980年,Johnson R O等人通过向聚硅氧烷乳液加入胶体SiO2和有机锡催化剂,制成性能较好的水基硅橡胶;由于过程简单,且获得的硅橡胶具有相对较高的拉伸强度(3MPa)和伸长率(500%~1000%),于是很快实现了商业化。水基硅橡胶产品先是以涂料形式出现,接着又以密封剂形式出现。
有机硅乳液的合成方法主要有两种:一种是本体聚合,继而用合成出的有机硅大分子与乳化剂和水作用,得到有机硅乳液。其优点是操作简单,生产方便,适于大规模生产。但对于高分子质量的有机硅大分子,因其本身黏度大而难以乳化,常会引起体系的不稳定。另一种是乳液聚合,即利用硅烷单体通过一步法来直接合成,通常用D3或D4、乳化剂、催化剂、水等原料,在一定条件下进行乳液聚合而成。由于聚合和乳化是一步完成的,因而耗时短、效率高,对设备要求简单,操作方便,且所得的乳液稳定、颗粒均匀。此外,还可通过聚合反应条件的控制来实现合成产物的分子量可控,或通过共聚引入可进一步反应的活性基团或聚合物,赋予产物特殊的性能。这2种方法合成出的有机硅乳液,可分为常规有机硅乳液和功能有机硅乳液。常规有机硅乳液又可根据乳化体系的不同,分为阳离子型、阴离子型、非离子型、复合离子型等几种乳液;功能有机硅乳液则可根据功能基团种类的不同,分为氨基硅乳、羧基硅乳、环氧基硅乳、聚醚硅乳等。
2.4.11.1 机械乳化法
机械乳化法又称剪切乳化法,这种方法是先合成有机硅聚合物,然后将有机硅聚合物、乳化剂、增稠剂和水等物质在适当的生产设备中经剪切分散而制得聚合物乳液的一种方法,使有机硅聚合物分散到连续水相中,即成为一种外观乳白色的稳定乳液。
有机硅乳液的稳定性与所用乳化剂、乳化设备、温度、有机硅聚合物含量和规格等有关。机械乳化法得到的乳液,一般讲,稳定性较差。特别是对于摩尔质量较高的硅油,难以用机械方法使之变成稳定的乳液。
机械乳化法是用胶体磨、均质机或超声波等把油相打碎成小液滴均匀地分布到水相里。乳液的稳定性取决于微粒的直径、防止油相凝结的乳化剂、油相的黏度及比例。机械乳化法所用乳化剂主要是非离子型的。如:①脂肪醇聚氧乙烯醚;②烷基酚聚氧乙烯醚;③吐温(聚氧乙烯失水山梨醇单硬脂酸酯、单油酸酯等);④聚硅氧烷-环氧丙烷环氧乙烷嵌段共聚物等。通过乳化含氢硅油试验,作为乳化剂效果,①较好,②尚可,③较好,④好。使用混合型乳化剂时,①+②尚可,①+③好。因此以脂肪醇聚氧乙烯醚和吐温组成的复合型乳化剂乳化效果为好,较为常用。近年来,通过特殊的乳化剂或乳化技术,经机械乳化法也获得了非常稳定的、性能优良的有机硅乳液。
将一定摩尔质量反应性聚硅氧烷乳化,然后加入固化剂、催化剂及填料等,混合均匀,水分蒸发后即得弹性体。
机械乳化法制备有机硅乳液的过程如下。
(1)有机硅橡胶乳液 过去,将有机硅橡胶用作脱模剂、防黏剂或其他涂层时,先将有机硅橡胶以5%~10%的浓度溶解在95%~90%的如甲苯、汽油和石油醚等中,然后涂抹或喷涂在基材上,待溶剂挥发后,形成有机硅橡胶薄层,方能起到脱模或防黏等作用。这种使用方法不仅麻烦,而且由于用了大量的有机溶剂,因而产生了有毒有害气体,污染了环境,危害人体健康,并且也容易引起火灾。
工艺配方:
制备工艺:
配方1、2的制备工艺:分别按配方1、2,将硅橡胶溶解在汽油中,与烷基酚聚氧乙烯醚和脂肪醇聚氧乙烯醚的水溶液一起加入到静态混合器和胶体磨中混合均化,在其强剪切力作用下,得油包水型的膏状物,然后将此膏状物加水至1000%稀释,在(25±5)℃下,机械搅拌2h,得到水包油型的有机硅橡胶乳液。室温稳定六个月。
配方3、4的制备工艺:分别按配方3、4,将硅橡胶与烷基卤化铵水溶液一起加入到静态混合器和胶体磨中混合均化,待成油包水型的膏状物后,取出加水稀释至1000倍,在(25±5)℃下机械搅拌2h,制得水包油型的有机硅橡胶乳液。室温稳定六个月。
(2)涂覆玻璃纤维布用水性硅橡胶乳液 涂覆玻璃纤维布用水性硅橡胶乳液由分子量为50万~80万的线型聚硅氧烷硅橡胶、非离子型表面活性剂、非离子型浸润型分散剂和有机溶剂汽油等组成。
例1.操作步骤:
①将9%GF-141甲基乙烯基硅橡胶加入到24%120#汽油中,用高速搅拌器进行高速搅拌,得到油溶性的有机硅橡胶;
②将油溶性的有机硅橡胶溶液静置10min,再依次加入2%烷基酚聚氧乙烯醚(OP-10)、3%过氧化苯甲酰、3%气相白炭黑(A-200)、1.5%脂肪醇聚氧乙烯醚(AEO-9)、1.5%硅烷偶联剂(南大-42),用低速搅拌器搅拌0.5~1h;
③最后加入56%工业用水,再搅拌30min,制得稳定、均匀、水包油型的硅橡胶乳液。
例2.操作步骤:
①将10%120-1苯基硅橡胶加入到26%120#汽油中,用高速搅拌器进行高速搅拌,得到油溶性的有机硅橡胶;
②将油溶性的有机硅橡胶溶液静置10min,再依次加入2%烷基酚聚氧乙烯醚(OP-10)、5%过氧化苯甲酰、5%气相白炭黑(A-200)、2%脂肪醇聚氧乙烯醚(AEO-9)、2%硅烷偶联剂(南大-42),用低速搅拌器搅拌0.5~1h;
③最后加入47%工业用水,再搅拌30min,制得稳定、均匀、水包油型的硅橡胶乳液。
(3)球形有机硅橡胶乳液 一种球体形状、不同外观形状的球形有机硅橡胶乳液的制造方法,其包括以下步骤:
①甲基含氢硅油与端乙烯基硅油按2:100(质量比)混合得到硅油混合物;非离子表面活性剂与水按1:90(质量比)混合得到乳化剂液;所述甲基含氢硅油是指结构为Me3Si—[OSiMe2]m—[OSiMeH]n—OSiMe3、m=40、n=40的化合物,所述端乙烯基硅油是指结构为ViMe2Si[OSiMe2]nOMe2Vi、n=140的化合物,所述非离子表面活性剂是脂肪醇聚氧乙烯醚;
②步骤①制备的硅油混合物与乳化剂液按1:1的比例加入反应釜中,投入硅氢化催化剂Pt-四甲基二乙烯基二硅氧烷络合物10×10-6(以铂计),在40℃下聚合反应24h,降至常温,加入占总反应物质量1%的乳化剂液,在30℃搅拌3h,得到预聚物乳液;
③步骤②得到的预聚物乳液与阴离子表面活性剂按100:1.35(质量比)混合,在30℃下搅拌2h,用盐酸或氢氧化钠10%水溶液调节反应物的pH值为7,得到球形有机硅橡胶乳液,上述阴离子表面活性剂是指具有亲水基团和亲油基团的阴离子化合物聚氧乙烯月桂醚硫酸钠。得到的球形有机硅橡胶乳液的主要单元链节是[R1=甲基;R2=甲基;a+b=2,a=1,n=30000~60000];
④其一般特性指标如下:
外观 乳白色液体
固体含量/% 50
固体形状 球形
固体粒径分布0.8~16μm 不定形物为0.3%~0.4%
存放期 6个月
机械乳化法不仅解决了硅橡胶的乳化问题,而且设备简单,乳化效率高,操作方便,适合大规模生产。由于使用大量的水为溶剂,不用或少用有机溶剂,所以大大减少了有毒有害气体,既减少改善了劳动保护条件,消除了生产安全隐患又减轻了对周围环境的污染,具有良好的经济效益和社会效益。
但一般说来,通过乳液聚合制备的乳液,其稳定性优于由机械乳化法制备的乳液。
2.4.11.2 乳液聚合法
在催化剂的作用下,以六甲基环三硅氧烷、八甲基环四硅氧烷或甲基环硅氧烷混合物和活性低聚物为原料,采用阴离子型、阳离子型、非离子型及两性离子型等多种不同的乳化剂,在一定的温度下发生聚合反应,制备高摩尔质量的反应型聚硅氧烷乳液,然后用碱或酸中和,再加入固化剂、催化剂、填料及颜料等,混合均匀;使用过程中,通过水分蒸发即得弹性体。所用固化剂、催化剂、填料等与传统的RTV硅橡胶大致相同。
以八甲基环四硅氧烷开环乳液聚合过程为例介绍。
八基环四硅氧烷环体中硅的电负性小,易被碱性物质进攻,而氧的电负性大,易被酸性物质进攻,所以八甲基环四硅氧烷可以被酸或碱引发开环聚合。但由于硅氧键发生均裂形成自由基所需要的能量很高,所以至今未见有自由基开环聚合。
八甲基环四硅氧烷在酸的催化下,进行阴离子乳液开环聚合的过程中,首先是八甲基环四硅氧烷在酸的作用下开环,在末端形成活性中心,即链引发:
然后八甲基环四硅氧烷与含有活性中心的硅氧烷低聚物反应,实现链的增长,即链增长:
随着反应的进行,低聚物的浓度增大,它们相互碰撞的概率增大而发生缩合反应,形成高分子量的聚硅氧烷。
在八甲基环四硅氧烷乳液开环聚合反应中,链引发反应和链增长反应决定了硅氧烷的转化率,聚合物的最终分子量则取决于低聚物之间的缩合反应。链引发和链增长的反应速率比低聚物之间的缩合反应要快得多,在八甲基环四硅氧烷转化率达到平衡以后,低聚物之间的缩合反应继续进行,最后不同分子量的聚硅氧烷之间达到平衡。
在反应过程中,硅羟基和乳化剂分子的亲水端基占据乳胶粒表面,硅羟基既可起助乳化作用,同时又是反应的活性中心,聚合反应是在接近乳液颗粒表面进行的。八甲基环四硅氧烷水解开环生成硅羟基后,有两条可能的途径使聚合物分子量增加:硅羟基之间直接缩合,或先和八甲基环四硅氧烷加成以后再彼此缩合成高聚物。
在硅氧烷乳液开环聚合初期,链引发反应和链增长反应是主要的,颗粒中的八甲基环四硅氧烷要扩散到颗粒表面和硅羟基进行加成,且体系中大多数乳液颗粒大小基本上是一样的,每个颗粒表面上硅羟基的数目和内部能容纳的八甲基环四硅氧烷的量或二甲基硅氧烷链段的数目大体上也一样,由于每个聚合物分子都有两个硅羟基,当一个乳液颗粒内部的八甲基环四硅氧烷以加成反应几乎完全消耗后,加成反应即停止了,颗粒内部的聚合物几乎有相同的分子量,且分子量分布比较窄,体系中聚合物物质的量的增加是由于新的乳液颗粒不断产生所致。
缩合反应发生在乳液颗粒表面的硅羟基之间,如图2-6所示,在反应过程中始终存在,反应初期聚合物链的端硅羟基被乳化剂的端基隔离开,不易发生缩合反应,随着聚合物数目的增加,乳化剂分子不足以将聚合物的端基完全隔开,因此邻近的两个聚合物的端硅羟基发生缩合反应,致使聚合物分子量剧增,分布也变宽。反应后期,缩合反应占主导地位,直到聚合物的分子量达到平衡。

图2-6 聚硅氧烷在乳液表面缩聚模型
乳液的制备方法有许多种。
方法1:将2.46%的RQBr和1.23%的OP(非离子表面活性剂)装入反应瓶中,加入定量的蒸馏水(约总投料量的70%),然后加入D4(约总投料量的30%);搅拌下程序升温:60℃×8h,70℃×3h,80℃×1h;最后加入醋酸,停止反应,制得二羟基封端聚硅氧烷乳液。
方法2:章基凯等人采用功能性高分子——强碱性苯乙烯系阴离子交换树脂与十二烷基苄基二甲基溴化铵,以它作为乳液聚合的催化剂与乳化剂,可制得半透明状呈蓝光稳定性甚好的乳液,即使不添加非离子表面活性剂也是如此,基本上不受十二烷基苄基二甲基溴化铵质量的影响。首先制备季铵碱溶液:配制3.5%十二烷基苄基二甲基溴化铵水溶液,然后加入一定量的强碱性阴离子交换树脂(离子交换树脂与十二烷基苄基二甲基溴化铵为3:1),在一定温度下搅拌2h,再重复一次,交换结束后,滤去离子交换树脂,即得季铵碱溶液。使用过的离子交换树脂可反复再生套用,但每一次使用前要测其交换量,当交换量下降多时,说明已污染,不可再用。其次是在装有搅拌、冷却器、温度计的三颈瓶中加D4400g,交换液200g,快速搅拌升温至50℃维持1.5h后,升温至70℃维持1.5h,再升温至85℃维持4~5h,反应结束后,用HAC中和,制得半透明状呈蓝光稳定性甚好的乳液。
方法3:章基凯、孙纯中等人采用DBDA作乳化剂,D4在碱催化剂下开环聚合,制得稳定、高摩尔质量的聚二甲基硅氧烷阳离子乳液。其方法需通过如下4步操作。
步骤1:预制大小均匀的RQBr和R+OH-二元球形混合胶束。将计量2/3的RQBr装入反应瓶中,加入40mL蒸馏水;搅拌溶解后,加入能形成RQ+Br-和RQ+OH-二元混合胶束的NaOH,加热至50℃,反应1~1.5h;再补加去离子水(加水量按阳离子乳液固含量为33%计),搅拌0.5h,放置过夜。
步骤2:制备含HO(SiMe2O)nSiMe2O-Q+R活性链的三元混合活性增溶胶束。步骤1完成后,搅拌下加入占D4总投料量2%~4%的D4,并在1h内升温至60℃左右再反应30min。
步骤3:控制反应温度和D4加料速度,合成稳定的聚二甲基硅氧烷阳乳(固含量为33%)。完成步骤2后,保持反应温度,搅拌下于0.5h内逐步加入余下的D4,再反应4h左右;最后加入余下的1/3RQBr,搅拌下逐步升温至高于反应温度20~40℃,历时2~3h后降至反应温度,中和后停止反应。
步骤4:在碱催化剂存在下,合成稳定的高摩尔质量聚二甲硅氧烷阳离子乳液。按步骤3合成聚二甲基硅氧烷阳离子乳液,但不进行升温中和操作;然后将其分装于五个塑料瓶(编号为1~5)中,放在恒温水槽中,在相同反应温度下进行缩合反应;每隔24h取出一瓶进行中和、破乳、分离、干燥,按常规方法用GPC测定其分子量及分布,其结果见表2-23。由此可知,通过延长放置时间,可制得高摩尔质量有机硅阳乳。该方法的优点是可根据需要在一定范围内任意合成不同摩尔质量的有机硅阳乳;方法易行,可用于生产。
表2-23 聚二甲基硅氧烷的分子量及其分布

方法4:使用十二烷基苯磺酸钠为乳化剂、十二烷基苯磺酸(DBSA)为催化剂,对D4在50~100℃的水体系中开环乳化聚合,可以得到颗粒度为500~5000Å(1Å=10-10m)的阴离子羟基有机硅乳液。同样对于聚合物分子量的控制则比较容易,由温度来控制,只要通过硅氧烷、水和硅醇之间的平衡,控制温度即可,在25~90℃之间可得到不同分子量(49000~172000)的羟基有机硅乳液(表2-24)。
表2-24 在乳液聚合中羟基硅油的黏度和分子量与反应温度的关系

①Brookfield黏度计测量。②用Barry公式计算。
方法5:制备非离子聚硅氧烷乳液。该乳液是由非离子乳化剂型如十二烷基聚氧乙烯基醚、Span、Tween系列,在路易斯酸或碱为催化剂的条件下制得。非离子聚硅氧烷乳液由于不带电荷,比离子型硅乳具有更强的适应性,应用领域更宽,稳定性更好。因此,围绕非离子型有机硅乳液开展了大量的研究工作。如美国道康宁公司的DC-346就是一种非离子型有机硅乳液,不仅能赋予皮革原始的外观和手感,而且增强其防水性能,得到广泛的应用。瑞士汽巴嘉基公司生产的新产品Ultrate FSA,是一种分子质量在20万以上的羟基封头聚二甲基硅氧烷的非离子型乳液,比美国道康宁公司的DC-1111阴离子型硅乳前进了一步。Revis等以脂肪醇聚氧乙烯醚为乳化剂,有机硅醇钠盐为催化剂,进行D4的非离子型乳液聚合,得到粒径为65nm的有机硅乳液。并强调在非离子型乳液聚合中,不能采用脂肪酸酯型非离子表面活性剂;因为在聚合催化剂酸或碱的作用下,它们会发生水解反应,导致乳化性能改变或催化剂失效。Halloran等以月桂醇聚氧乙烯醚为乳化剂,戊醇为助乳化剂,制得有机硅含量为7.6%乳液。南京师范大学研制的非离子羟乳,采用了聚氧乙烯基醚的磷酸酯和HLB值不同的非离子乳化剂聚合而成,稳定性高,可以用作合成纤维和各类纤维及织物的整理剂。但是,非离子型硅乳由于存在与基材作用力弱,容易迁移的缺点,限制了其使用范围。
方法6:制备复合离子聚硅氧烷乳液。传统的乳液聚合得到的聚硅氧烷胶乳粒径较大、易漂油或聚沉,并且阴(阳)离子型有机硅乳液有电荷存在,导致稳定性差,且不耐电解质,有机硅聚合物容易从乳液中分离出来,浮在液面上,俗称“漂油”。为改善阴(阳)离子硅乳的稳定性,控制乳液的粒径,将阴(阳)离子表面活性剂与非离子表面活性剂和乳化助剂进行复配,以提高乳化性能,便可克服离子型乳化剂制备硅乳的缺点,使产物具有良好的耐热性、耐电解质性和耐冷冻性。同时,还可以改善非离子型乳化剂所制得的硅乳与基材结合力弱的问题,以达到综合的效果。如上海树脂厂于20世纪70年代采用阳离子与各种非离子复合乳液聚合方法研制成功并投入生产的SAH-288A、B高稳定性、漂油少的二甲基羟基硅油乳液。又如沈一丁等人在研究D4离子型乳液稳定性过程中发现:单独采用离子型乳化剂,对D4的乳液聚合的乳化效果不理想;加入OP-10非离子表面活性剂和十八醇助乳化剂,可以明显改善乳化效果,久置而不分层、不漂油。
在反应体系中必须加入非离子表面活性剂和助乳化剂,能提高乳液稳定性、防止乳胶颗粒的聚沉的机理为:非离子助乳化剂可显著降低乳胶粒表面的静电张力,同时离子型乳化剂的静电斥力和非离子型乳化剂水化层的体积效应协同作用,使生成的乳胶粒更稳定。
2.4.12 乙基硅橡胶
在聚硅氧烷侧链上引入乙基制得的二乙基硅橡胶,其突出的性能是耐寒性特别好,耐寒性优于二甲基硅橡胶和一般的甲基乙烯基硅橡胶。乙基含量越高,耐寒性越好。但乙基的反应活性比甲基大,因此,随乙基含量越大,耐热性随之下降。作为低温使用的乙基硅橡胶,以在聚合物中含有二乙基硅氧链节为8%(摩尔分数)为宜。乙基硅橡胶的使用温度一般为-70~200℃。
2.4.13 硅氮橡胶
硅氮橡胶的主要优点是具有卓越的热稳定性,在430~480℃不分解,有的甚至能耐500℃以上的高温。硅氮橡胶的突出弱点是水解稳定性差,曾一度被认为没有发展前途。后来发现主链中引入环二硅氮烷的聚合物具有很好的热稳定性。用硅芳基改性的含环二硅氮烷的弹性体,在空气中加热到425℃不失重,570℃时失重仅为10%,且具有较好的水解稳定性。
2.4.14 甲基嵌段室温硫化硅橡胶
甲基嵌段室温硫化硅橡胶是甲基室温硫化硅橡胶的改性品种,它是由羟基封端的聚二甲基硅氧烷(107胶)和甲基三乙氧基硅烷低聚物(聚合度3~5)的共聚体。在二丁基二月桂酸锡的催化下,聚二甲基硅氧烷中的羟基和聚甲基三乙氧基硅烷中的乙氧基缩合生成三向结构的聚合体,经硫化后的弹性体比甲基室温硫化硅橡胶具有较高的机械强度和粘接力,可在-70~200℃温度范围内长期使用。
甲基嵌段室温硫化硅橡胶具有防震、防潮、防水、透气、耐臭氧、耐气候老化、耐弱酸弱碱性能。它的电气绝缘性能很好,还具有很好的黏结性,而且成本低。因此,可广泛用于灌封、涂层、印模、脱模、释放药物载体等场合。用甲基嵌段室温胶灌封的电子元器件有防震、防潮、密封、绝缘、稳定各项参数等作用。把甲基嵌段室温胶直接涂布到扬声器上,可减少和消除扬声器的中频各点,经硫化后扬声器谐振频率性能可降低20Hz左右。在甲基嵌段室温胶中配合入一定量的添加剂后可用作纸张防黏剂。在食品工业的糖果、饼干传送带上涂上一层薄薄的甲基嵌段室温胶后,可改善帆布的防黏性能,从而改善了食品的外观,提高原料的利用率。
在甲基嵌段室温胶中加入适量的气相法白炭黑,可用于安装窗户玻璃、幕墙、窗框、预制板的接缝、机场跑道的伸缩缝。此外,还可作电子计算机存储器中磁芯和模板的胶黏剂,还可作导电硅橡胶和不导电硅橡胶的胶黏剂等。用甲基嵌段室温硫化硅橡胶处理织物可提高织物的手感、柔软和耐曲磨性。