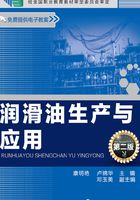
第三节 润滑
一、润滑的作用原理
1.润滑的定义
在摩擦副表面之间加入一些介质(润滑剂),用润滑剂的液体层或润滑剂中的某些分子形成的表面膜将摩擦副表面全部或部分地隔开,变固体表面间的干摩擦为润滑油分子间的摩擦。由于润滑油分子间的摩擦系数比金属表面的干摩擦系数要小得多,从而达到降低摩擦、节省能耗、减小磨损、延长机械设备使用寿命的目的,这一过程称为润滑。
2.润滑的作用
润滑剂最重要的功能是减小摩擦与磨损,但在不同的应用场合除具备这两项最重要的润滑功能外,还具备其他不同的功能。润滑剂也因具有动力媒介、热传导与绝缘等性能而可作为用于非相对运动体的一种纯功能性油。润滑剂的作用具体表现在以下几个方面。
(1)降低摩擦 在摩擦副表面加入润滑剂后形成的润滑油膜将摩擦表面隔开,使金属表面间的摩擦转化为具有较低抗剪切强度的油膜分子间的内摩擦,从而降低摩擦阻力和能量消耗并使摩擦副运转正常。
(2)减小磨损 在摩擦副表面形成的润滑膜可降低摩擦并支撑载荷,因此可以减小表面磨损及划伤,保持零件的配合精度。
(3)冷却降温 采用液体润滑剂的循环润滑系统可以把摩擦时产生的热量带走,降低机械运转摩擦发热造成的温度上升。
(4)防止腐蚀 摩擦表面的润滑剂膜覆盖在摩擦面上有隔绝空气、水蒸气及其他腐蚀性气体的作用,可防止摩擦表面被腐蚀或生锈。
(5)传递作用力 某些润滑剂(如液压油)可以作为力的传递介质,把冲击振动的机械能转变成液压能。
(6)减振作用 吸附在金属表面上的润滑剂由于本身应力小,在摩擦副受到冲击时能够吸收冲击振动的机械能起到减振和缓冲作用。
(7)绝缘作用 矿物油等润滑剂有很高的电阻,因此可作为电绝缘油和变压器油。
(8)清洗作用 随着润滑油的循环流动,可把摩擦表面的污染物和磨屑等杂质带走,再经过滤器滤除。内燃机油还可以把活塞上的尘土和其他沉积物分散去除,保持发动机的清洁。
(9)密封作用 润滑剂对某些外露零部件形成密封,防止冷凝水、灰尘及其他杂质入侵,并使汽缸和活塞之间保持密封状态。
在润滑剂的这些作用中,降低摩擦和减小磨损是润滑剂最主要的功能。
3.润滑的分类
用润滑剂来隔开摩擦表面,防止它们直接接触,就是通常所说的“机械的润滑”。根据润滑油在摩擦表面上所形成润滑膜层的状态和性质,润滑分为流体润滑和边界润滑两大类型。
(1)流体润滑 流体润滑又称液体润滑,它是在摩擦副的摩擦面被一层具有一定厚度并可以流动的流体层隔开时的润滑。此时摩擦面间的流体层,称为流体润滑的润滑膜层。
流体润滑膜层具有三个特点:一是具有流动性,可以流动,摩擦阻力小,但容易流失;二是具有一定的流体压力,可起到平衡外载负荷的作用;三是流体层需达到一定的厚度,保证摩擦面间的微凸体相互之间不发生接触。
流体润滑的摩擦系数很小,在0.001~0.01之间,磨损也非常低,是润滑中一种最理想的状态。其缺点是流动液体层的形成较困难,需特定的条件,同时所形成的流体层易于流失,承受负荷的能力有限。
流体润滑根据流体润滑膜产生的方式,分为流体静压润滑、流体动压润滑及弹性流体动压润滑三种类型。
①流体静压润滑。通过外部油泵提供的压力实现流体润滑的方式称为流体静压润滑。润滑中,油品在高压油泵的作用下通过油路输送到轴承底部的油腔中,利用油的压力和流动的冲力将支承的轴顶起,以此形成轴与轴套之间的流体油层。由于这种润滑油层的形成与轴承的运转状况无关,无论轴承的转速高或低,即使在静止状态时也可以保证摩擦面上有着足够厚度的流动油层,因而称之为流体静压润滑。这种润滑方式的缺点是设备昂贵、复杂。
②流体动压润滑。通过轴承的转动或摩擦面在楔形间隙中的滑动而产生油压自动形成流体油膜的方式叫做流体动压润滑。流体动压润滑广泛应用于滑动轴承和高速滑动摩擦部件之中,是机械设备中应用最普遍的润滑方式。
滑动轴承在运转过程中,由于轴和轴套间隙中润滑油受到高速转动轴的摩擦力作用,随同轴一起转动,在转动中油进入轴承底部相接触的摩擦区域时,由于轴与轴套间呈楔形间隙,油流通道变小,使油受到挤压,因而产生油压。油压的产生使轴受到一个向上的作用力,当轴承的转速足够高,产生的油压达到一定值时,就可以将轴抬起,在摩擦面间形成一层流动的油层。
③弹性流体动压润滑。弹性流体动压润滑是一种比较复杂的情况,它是在流动油层已存在的前提下,摩擦面对油层挤压并伴随着金属表面和润滑油性质发生变化的过程。弹性流体动压润滑主要存在于齿轮和滚动轴承的润滑中。在齿轮和滚动轴承中,摩擦件的运动方式及摩擦面的接触方式同滑动轴承完全不同。滑动轴承中摩擦件的相对运动和摩擦面的接触都是滑动的方式。而在齿轮部件和滚动轴承中,摩擦副的运动方式是一个摩擦件相对于另一个摩擦件的滚动,摩擦面的接触是从分离到接触,接触后再分离的“离合”过程。在这个“离合”过程中,如果摩擦部位存在着润滑油,则会形成对油的挤压。由于在接触点上负荷压力的作用会使金属面产生形变,接触面积增大,同时油受到挤压而使得黏度增大,变得黏稠,因此在机械高速运转的摩擦过程中,则往往在润滑油尚未从摩擦面完全挤出的瞬间,就已经完成了一个“离合”挤压的过程,摩擦面上仍保持着一层呈流体状态的油层。
流体润滑膜的形成与油品的性质关系密切,从以上几种流体润滑膜形成过程的讨论可以看出,流体油膜形成的起因是流体油压的产生,而油压的产生则与流体在摩擦面上的流动阻力的大小,即油品的黏性有关。试验证明,油品的黏度越大,油品越黏稠,在摩擦面保持流体润滑层的能力就越强。因此,在大负荷尤其是低转速形成流体润滑膜困难的条件下,应尽量选用黏度大的油品,而在小负荷、高转速的条件下,则可使用低黏度的润滑油。
(2)边界润滑 摩擦表面被一层极薄的(约0.01μm)、呈非流动状态的润滑膜隔开时的润滑称为边界润滑。与流体润滑相比,边界润滑中的润滑膜层呈非流动状态,能稳定地保持在摩擦表面,它的形成不需要类似流体润滑的种种条件,并具有很高的承受负荷的能力。因而在机械润滑中也得到了广泛的应用。在所有难以形成流体润滑的摩擦机件上,润滑形式往往是边界润滑。
在边界润滑状态下,摩擦力要比流体润滑状态大得多,摩擦表面的金属凹凸点的边界可能发生直接接触,液体的润滑已不完全是由它的黏度起作用,而主要是靠往润滑剂中加入某些活性化合物。这些化合物能与摩擦表面的金属起物理或化学作用而在凸点峰顶处形成边界膜,正是这层边界膜起到主要的润滑作用。如果只靠提高所用润滑油的黏度,是不能适应边界润滑状态要求的。
边界润滑是一类相当普遍的润滑状态,如汽缸与活塞环、凸轮与挺杆等处都可能处于边界润滑状态。在一般情况下,边界润滑的摩擦系数小于0.1,高于流体润滑而低于干摩擦。所以,相对干摩擦来说,边界润滑能有效地减少机器零件的磨损,延长使用寿命,较大幅度地提高承载能力,扩大使用范围。
边界润滑根据润滑膜的性质和形成的原理不同,分为吸附膜边界润滑和反应膜边界润滑两种。其中,吸附膜又可划分为物理吸附膜和化学反应膜。对于在高温高压下形成的反应膜边界润滑(即条件最苛刻的边界润滑),也称为“极压润滑”。现将吸附边界润滑膜和反应边界润滑膜的形成和特点介绍如下。
①吸附膜边界润滑。依靠金属表面的吸附作用所形成的润滑油膜层称为边界吸附膜。吸附膜由于吸附在金属表面,已失去流动性,因而能稳定地保持在金属摩擦件的表面。
边界吸附润滑膜在重负荷、低转速或低滑动速度的摩擦部件上都能够保持稳定,起到比流体润滑膜更为稳定和可靠的润滑作用。当机械的转速很低、负荷很高,使得摩擦面间的流动油层受到破坏,被挤压出去时,金属面上所吸附的油层往往还能保持,起到润滑的作用。一般情况下,边界吸附膜的厚度为0.1~1μm,仅为流体润滑膜层的1%左右,其摩擦系数约为干摩擦的1/10。在机械设备的润滑中,例如发动机中汽缸与活塞环、凸轮与挺杆以及重负荷齿轮的润滑,同时也包括各类摩擦部件在启动瞬间的润滑,往往处于吸附膜边界润滑状态。
金属表面边界吸附膜依靠金属晶格分子对油分子的吸附而形成。通常,金属晶格的引力场可使金属表面形成数十到数百层的油分子吸附层。这种引力场对油品中的极性分子有着更强的吸附作用。现代研究表明,金属面上的吸附膜是一种由多层分子定向排列的层状结构。与金属表面接触的分子,其极性端吸附于金属的表面晶格,非极性端则朝向着外部,和相邻分子的非极性端相连,而相邻分子朝外的极性端又与更外一层分子的极性端相连,直至金属力场的衰减不能再吸附油品分子为止,以此构成分子层与层之间的定向排列。这种定向的排列与吸附分子的极性有密切关系。通常,极性强的分子有利于分子层之间排列结构的牢固结合和减缓金属引力场的衰减,从而增大吸附膜的强度和厚度。
由于吸附膜边界润滑时,摩擦发生在吸附膜内部分子层与层之间,因此,其油膜的性质与油品的黏度无关,而取决于吸附分子的极性。润滑油的这种在金属表面形成边界吸附润滑膜的性质通常称为“油性”。它与油品中极性分子的极性、相对分子质量以及含量有关。而这些极性分子往往就是为提高油性而加入的酯类结构的油性添加剂。
吸附膜的油膜强度优于流体油膜,但在更高的负荷和高温条件时,它也会失效。这些通过分子吸附作用而形成的膜层,具有吸附的可逆性,低温时可形成较稳定的吸附层,而在高温时则会发生解吸现象。据研究,金属表面的各类吸附膜能保持的温度通常不超过200~250℃。因此,在高温的工作条件下,或者是在一些会产生大量摩擦热量的极高负荷的部件中,仅依靠润滑油的黏度和油性则是不够的,这时还需要润滑油具有极压润滑的性质,通过金属表面的化学反应膜层实现润滑。
②化学反应膜边界润滑。即使是高强度的吸附膜,在温度超过200~250℃时也会失效。同时,润滑油在这样的高温下还会发生氧化反应。因此,在高温、高压的苛刻条件下,就需要考虑采用其他的方式来实现机械设备的润滑。为解决这个问题,一个有效的方法就是采用极压润滑,也就是在摩擦表面形成化学反应边界润滑膜。
a.化学反应膜的生成。化学反应边界润滑膜的形成依赖于油品中的极压添加剂,即含有硫、磷和氯等元素的有机化合物(如硫化烯烃、亚磷酸二正丁酚和氯化石蜡等)。这些化合物在高温、高压工作条件下,在相互滑动的摩擦表面上,由于摩擦面上微凸体在高负荷下的大面积接触,摩擦热量聚集,因而在摩擦面接触点区域出现高温,使这些有机化合物分解出活性元素,与金属表面起化学反应,从而生成相应的金属化合物,例如硫化铁、氯化铁等,这层通过反应生成的化合物膜层被称为边界润滑反应膜。
极压润滑中形成的边界反应膜可在高温下稳定地存在,即使在摩擦过程中会出现部分损耗,也能有新的成分及时生成,因而总能在摩擦面上始终保持有一层反应膜润滑层,保证高温高压苛刻条件下可靠的润滑。
b.化学反应膜的特点。反应膜形成和稳定保持的温度可达数百度至上千度。与边界吸附膜相类似,边界反应膜也具有较低的抗剪切阻力,并能承受更高的载荷。这类由添加剂与金属生成的硫化物、磷化物、氯化物薄膜,具有比金属低得多的硬度和剪切强度,并且熔点较低,还可在摩擦过程中的高温高压下产生部分变形流动,对表面起到化学抛光作用,使摩擦表面更加光滑,使单位面积承受载荷下降,这些对表面的润滑效果都起到一定的改善作用,从而使摩擦副的摩擦阻力降低,材料的磨损减小。
化学反应膜比吸附膜稳定得多。它的摩擦系数与膜的抗剪切强度有关,当抗剪切强度低时,摩擦系数也低,通常摩擦系数为0.1~0.25。反应膜要能在重载、高速、高温情况下保证有效的边界润滑,就应具有一定的厚度,一般要求反应膜的厚度为一至数十纳米,曾记录到厚度为100nm的硫化铁膜。
极压添加剂能在金属表面产生低熔点反应膜已为实践所证明。研究者曾在使用含硫、含氯润滑油的汽车准双曲面齿轮表面上发现了硫化铁及氯化铁的存在。
除了含硫、磷和氯的有机物外,还可采用含氟和氮等元素的有机物作极压添加剂。此外,有机金属化合物如环烷酸铅、二烷基二硫代磷酸锌等也可用来作极压添加剂。
极压反应膜比吸附膜稳定,适用于重载和高温下的润滑。但由于其形成的温度高,低温下发挥不了作用,因而不适合于较低温度下的润滑。另外,反应膜在形成时,添加剂反应能力也不能过强,否则会加快材料的损耗而造成腐蚀。
二、润滑剂的分类
润滑剂按照其物理状态可分为液体润滑剂、半固体润滑剂、固体润滑剂和气体润滑剂四大类(见表1-1),每类各有其性能特点和适用范围。
表1-1 现代润滑材料的分类和构成

1.液体润滑剂
液体润滑剂是用量最大、品种最多的一类润滑材料,包括矿物润滑油、合成润滑油、动植物油和水基液体等。
液体润滑剂的特点是具有较宽的黏度范围,为不同的负荷速率和温度条件下工作的运动部件提供了较宽的选择余地。
(1)矿物润滑油 矿物润滑油的产量约占润滑油总产量的90%,一般由矿物基础油和添加剂调和而成,不含添加剂的矿物润滑油只占矿物润滑油总产量的15%左右。矿物润滑油的原料充足,价格便宜,质量能满足各种机械设备的使用要求。
矿物润滑油基础油一般选用适合于润滑油性能要求的石油,经分馏、精制、脱蜡等工艺加工而成。依据原油性质或加工方法的不同,矿物润滑油基础油可分为石蜡基基础油、中间基基础油和环烷基基础油;按黏度指数不同,分为超高黏度指数基础油、很高黏度指数基础油、高黏度指数基础油、中黏度指数基础油和低黏度指数基础油。
(2)合成润滑油 为了满足某些在低温、高温和高真空等条件下工作的飞机、火箭等机械的要求,人们利用人工合成的方法合成化合物作为润滑油的原料。以合成原料为基础油制成的润滑油统称为合成润滑油。
合成润滑油种类较多,根据化学结构不同分成酯类油、聚醚、聚硅氧烷、硅油、硅酸酯、含氟油、磷酸酯和聚烯烃。
与矿物润滑油相比,合成润滑油具有优良的黏温性能和低温流动性、良好的热氧化安定性、低挥发性,以及其他一些特殊性能,如化学安定性和抗辐射性等。但合成润滑油的成本比矿物润滑油的成本高得多,目前合成润滑油大部分用在矿物润滑油不能满足使用要求的某些特殊润滑场合。
(3)动植物油 作为润滑剂的动植物油脂主要是植物油如菜籽油、蓖麻油、花生油和葵花籽油等,目前仍作为某些金属切削液的重要组分。动植物油作为润滑油的优点是油性好、生物降解性能好,缺点是氧化安定性和热稳定性较差,低温性能也不够好。
随着石油资源的逐渐短缺和环保要求的日益严格,人们又开始重视动植物油脂作为润滑材料的开发应用,并希望通过化学方法改善它的热氧化安定性和低温性能,使之成为未来替代矿物润滑油的重要润滑材料。
(4)水基液体 水基液体是含水的润滑剂,有溶液型和乳化型两类。由水、油、乳化剂及添加剂组成的乳化液,有水包油和油包水两种形式。由于水具有无毒、不燃、不污染环境、价格低、来源丰富和储存方便的优点,作为润滑油成分又有冷却性能好和抗氧化安定性好等特点。
用水代替油使用不仅可以节约资源,而且使用安全,有利于保护环境,但水作为润滑剂有表面张力大、黏度低、润滑性能差、摩擦系数大、倾点高、冻结后膨胀、适用温度范围窄、易腐败变质、易使金属锈蚀等缺点,因此使用范围受到限制。目前乳化液主要用于液压油及金属加工油液。水包油型水基液压油最早作为耐燃液压油,大量用于冶金和矿山机械,目前作为液压油已广泛用于冶金、矿山、玻璃、陶瓷、塑料和纤维等行业的机械上,乳化汽缸油也大量用于船舶机械及火车上。由于乳化液具有良好的冷却性能,因而被广泛用作切削、研磨、压延、冲压和拉拔等场所作为金属加工液。
2.润滑脂
润滑脂又称为半固体润滑剂,是在常温常压下呈半流动状态并且具有胶体结构的润滑材料。按使用的稠化剂种类不同,润滑脂分为皂基脂、烃基脂、无机脂和有机脂四类。皂基脂中的锂基脂具有多方面的优良性能,产量一般占润滑脂总产量的60%以上。目前使用的润滑剂主要是液体状态的润滑油,润滑脂的产量只占润滑剂总产量的2%左右。润滑脂由具有良好润滑性能的润滑油与具有良好亲油性的碱土金属皂类、膨润土、硅胶脂、有机高分子聚合物等稠化剂形成具有安定网架结构的胶体。
在一些特殊条件下,要求使用润滑脂作润滑剂,例如:某些开放式的润滑部位要求有良好的黏附性,防止润滑剂流失或滴落;在有尘埃、水分或有害气体侵蚀的情况下,要求有良好的密封性、防护性和防腐蚀性;由于运转条件限制要求长期不换润滑油的摩擦部位,以及摩擦部位的温度和速度变化范围很大的机械,往往需要使用耐负荷能力强的润滑脂。
3.固体润滑剂
(1)作用特点 固体润滑剂是一类新型润滑剂,具有耐高温、耐低温、抗辐射、不污染环境等优点,主要用于宇航工程等高温、低温、高真空、强辐射、高化学腐蚀的特殊条件下的润滑,特别适合于给油不方便、装拆困难的场合。固体润滑剂的缺点是摩擦系数较高,冷却散热性能差。
固体润滑剂的润滑作用有三种类型:
①能在摩擦表面形成固体润滑膜,润滑机理与边界润滑相似;
②软金属固体润滑剂利用软金属抗剪切强度低的特点起到润滑作用;
③具有层状结构的物质(如石墨)利用其结构特点起到润滑作用。
(2)常用的固体润滑剂 常用的固体润滑剂包括以下四类。
①软金属,如铅、锡、铟、锌、银、金等;
②金属化合物,如氧化铅、氟化钙、硫化锰和各种技术脂肪酸皂等;
③无机物,如石墨、氮化硼、滑石、云母等;
④有机物,如石蜡、聚四氟乙烯、聚酰胺、酚醛树脂等。
4.气体润滑剂
气体润滑剂的优点是摩擦系数小,在高速下产生摩擦热少,温升低,运转灵活,工作温度范围广,形成的润滑膜比液体薄,气体支撑能保持较小间隙,在高速支撑中容易保持较高的回转精度,在放射性和其他特殊环境中也能保持正常工作,而且能在润滑表面普遍分布,不会产生局部热斑,不存在密封、堵塞和污染等问题。
气体润滑剂可用在比润滑油脂更高或更低的温度下,如在10000~600000r/min高速转动和-200~2000℃温度范围内润滑滚动轴承,其摩擦系数可低到测不出的程度。使用在高速精密轴承(如医用牙钻、精密磨床主轴及惯性导航陀螺)上可获得高精度。但气体润滑剂密度低,因此承载能力低,只能用在30~70kPa的空气动力学装置和不高于100kPa的空气静力学装置中,对使用的设备精度要求很高,需要用价格较高的特殊材料制成,而且排气噪声高。
常用的气体润滑剂有空气、氦气、氮气、氢气等。空气适宜在650℃以下使用,氮气和氦气等惰性气体可用在1000℃以上的润滑温度。
气体润滑剂要求清净度很高,使用前必须进行严格的精制处理。目前气体润滑剂在高速设备中的应用有所增加,如在精密光学仪器、牙医的钻床、测定仪器、电子计算机、精密的研磨设备中,以及在制药、化学、食品、纺织和核工业这类低负载而要求避免污染的领域。
三、润滑油的构成
润滑油一般由基础油和添加剂两部分组成。基础油是润滑油的主要成分,也是润滑油添加剂的“载体”,决定着润滑油的基本性质;添加剂则可弥补和改善基础油性能方面的不足,赋予其某些新的性能,是润滑油的重要组成部分。
1.润滑油基础油
润滑油基础油在润滑油中所占的比例为70%~99%,其品质的高低直接影响成品润滑油质量的好坏。
(1)润滑油基础油的分类 按来源不同,润滑油基础油可分为矿物型基础油和合成型基础油两大类。随着环保意识的加强,具有生物降解性的绿色基础油也有一定的发展。
①矿物型基础油。矿物型基础油是指天然原油经过常减压蒸馏和一系列精制处理而得到的基础油,目前是润滑油基础油的主要部分。
迄今为止,国际上尚未对矿物润滑油基础油制定统一的分类标准。早期的标准是按照生产矿物润滑油基础油原料所用原油的类别分为石蜡基、中间基和环烷基三类不同黏温性能的基础油。然而,随着炼油技术的发展,润滑油加氢裂化、加氢降凝技术的应用,即使用黏温性不好的中间基和环烷基原油也可生产出高黏度指数的基础油。因此,目前基础油标准的划分已广泛采用按黏度指数及适用范围划分的方法。
a.根据基础油的黏度分类。每一类基础油按黏度等级可分为不同牌号。国外通常用赛氏黏度(S)来划分基础油的黏度等级。中性油的黏度较低,用100F(37.8℃)时的赛氏通用黏度表示。光亮油黏度较高,用210F(98.9℃)时的赛氏通用黏度表示。我国则分别用40℃和100℃赛氏通用黏度表示,并取通用黏度整数的近似值作为牌号,但在实际生产中仍多采用运动黏度作为操作控制指标。运动黏度与赛氏通用黏度及基础油牌号的对应关系见表1-2。
表1-2 运动黏度与赛氏通用黏度及基础油牌号的对应关系

①中性油为40℃运动黏度和赛氏通用黏度范围,光亮油为100℃运动黏度和赛氏通用黏度范围。
②运动黏度和赛氏通用黏度的换算关系见ASTM D2161。
b.根据黏度指数和适用范围划分。20世纪80年代以来,随着内燃机油等油品的快速发展,对润滑油基础油在黏度指数、氧化安定性、抗乳化性和蒸发损失等方面提出了较高的要求。随着加氢工艺技术的提高和应用,已可从中间基和环烷基原油中制取高黏度指数的中性油,从石蜡基原油中制得低凝点的中性油,因此根据原油属性的分类方法已失去意义。目前,国外普遍改用根据黏度指数的分类方法。
中国石化总公司1995年按照国际目前通用的分类方法,提出了我国润滑油基础油新的分类方法和规格标准Q/SHR001—95,见表1-3。
表1-3 润滑油基础油新的分类方法和规格标准

其中代号均为英文字头缩写。VI为黏度指数;L、M、H、VH、UH分别为低、中、高、很高、超高。根据适用范围分为通用基础油和专用基础油两类。专用基础油包括低凝点基础油和深度精制基础油,分别在代号后加W和S表示,W表示低凝特性,S表示深度精制。
②合成型基础油。合成润滑油基础油一般是由低分子组分经过化学合成而制备的较高分子的化合物。与矿物型基础油相比,合成型基础油具有优良的性能,可以满足矿物型基础油和天然油脂所不能满足的使用要求。合成油的用量尽管只占润滑油总量的3%左右,但因性能优异,在航空和航天等润滑条件特殊的重要场合发挥了重要作用。
根据合成润滑油基础油的化学结构,已工业化生产的合成润滑油分为酯类油、聚醚、合成烃、硅油、含氟油和磷酸酯六大类。
(2)润滑油基础油的规格
①润滑油通用基础油的规格(Q/SHR 001—95)
a.高黏度指数基础油(HVI),黏度指数一般不小于95,适用于配制黏温性能要求较高的润滑油。黏度牌号分为:HVI-75、HVI-100、HVI-150、HVI-200、HVI-350、HVI-400、HVI-500和HVI-650八个中性油以及HVI-120BS、HVI-150BS两个光亮油。
b.中黏度指数基础油(MVI),黏度指数一般不小于60,适用于配制黏温性能要求不高的润滑油。黏度牌号有:MVI-60、MVI-75、MVI-100、MVI-150、MVI-250、MVI-500、MVI-600、MVI-750和MVI-900等九个中性油以及MVI-90BS、MVI-125/140BS和MVI-200/220BS三个光亮油。
c.低黏度指数基础油(LVI),没有规定最低黏度指数,可用于调配不要求黏度指数的润滑油,如变压器油、冷冻机油等低凝点润滑油。黏度牌号有:LVI-60、LVI-75、LVI-100、LVI-150、LVI-300、LVI-500、LVI-900和LVI-1200八个中性油以及LVI-90BS、LVI-230/250BS两个光亮油。
②润滑油专用基础油的规格(Q/SHR 001—95)
a.高黏度指数深度精制油(HVIS),除黏度指数大于95外,还规定了较优良的氧化安定性、抗乳化性和一定的蒸发损失等指标。适合于调配高档汽轮机油和极压工业齿轮油。包括八个中性油和两个光亮油品种,其黏度牌号与HVI相对应。
b.高黏度指数、低凝点、低挥发性中性油(HVIW),除黏度指数大于95以外,还规定较低倾点、较低蒸发损失、较好的氧化安定性等指标,主要用于配制高档内燃机油、低温液压油、液力传动油等。有七个中性油和一个光亮油品种。
c.中黏度指数深度精制基础油(MVIS),除黏度指数不小于60外,还规定有较好的氧化安定性、抗乳化性等指标,适用于配制汽轮机油,有八个中性油品种。
d.中黏度指数、低凝点、低挥发性中性油(MVIW),除黏度指数不小于60外,还规定有好的抗氧化安定性、抗乳化性和低蒸发损失等指标,适合于配制高档内燃机油、低温液压油。
抗氧化安定性、抗乳化性、蒸发损失等新规格指标的建立,反映了内燃机油等油品自20世纪80年代以来对于使用性能的新要求,只有用具有这些规格指标的基础油才能配制成高档的内燃机油等工业润滑油。
2.润滑油添加剂
(1)添加剂的定义 添加剂是在油中添加极少量(百分之几到百万分之几),就能显著改善油品的一种或几种使用性能的油溶性化合物。
(2)添加剂在商品润滑油中的作用 使用添加剂,可以提高油品质量,降低成本,减少油品消耗量,延长润滑油的使用周期,并且可以满足某些只靠改进石油炼制方法无法达到的要求。加入添加剂已成为合理有效地利用石油资源、节约能源所必不可少的技术措施。但添加剂不是万能的,它不能使劣质油品变成优质油品,只是提高油品质量的主要措施之一,润滑油的质量与基础油的类型和加工手段也有直接的关系。
(3)润滑油添加剂的分类 添加剂的种类很多,根据添加剂的作用大致可分为两大类。一类是改善润滑油物理性质的添加剂,如降凝剂、黏度指数改进剂、消泡剂、破乳剂和油性剂等,它们能使润滑油分子变形、吸附和增溶;另一类是改善润滑油化学性质的添加剂,如抗氧化剂、防锈剂、清净分散剂和极压抗磨剂等,它们本身与润滑油发生化学反应。添加剂从机理来看也可分为两类,第一类是靠界面的物理化学作用发挥其使用性能,分为耐载荷添加剂(油性剂、抗磨剂和极压剂)、金属表面钝化剂、防锈防腐剂、清净分散剂、降凝剂和抗泡剂;第二类是靠润滑油整体性质作用达到润滑目的的添加剂,如抗氧剂和黏度指数改进剂。大部分添加剂都是结构复杂的化合物及其混合物。
国际上没有添加剂的统一分类标准,我国按添加剂作用分为九类:清净分散剂、抗氧防腐剂、极压抗磨剂、油性剂和摩擦改进剂、降凝剂、抗氧剂和金属减活剂、黏度指数改进剂、防锈剂、抗泡沫剂。
(4)添加剂的性能 润滑油添加剂要起到润滑油基础油助剂的作用,自身应具有以下几种性能:
①副作用小,对其他添加剂的作用和润滑油的其他性质没有破坏作用;
②能溶于油品而不溶于水,遇水不乳化、不水解;
③与润滑油使用条件相适应的热安定性;
④容易得到且价格低廉。
四、润滑油生产流程
润滑油一般由润滑油基础油和添加剂两部分组成。润滑油基础油是润滑油的主要成分,决定着润滑油的基本性质;添加剂则可弥补和改善基础油性能方面的不足,赋予其某些新的性能,是润滑油的重要组成部分。在一定条件下,把性质和组成相近的两种或两种以上基础油,按一定比例混合并加入添加剂的过程称为调合。
润滑油生产流程如图1-6所示。第一步,生产润滑油基础油(包括物理法生产矿物润滑油基础油、加氢法生产矿物润滑油基础油和化学法生产合成润滑油基础油);第二步,根据润滑油的使用性能和经济性选择合适的一种或几种润滑油基础油;第三步,根据润滑油的使用性能以及润滑油基础油的物理和化学性能选择一种或几种润滑油添加剂;第四步,将选定的润滑油基础油和润滑油添加剂按要求的比例和操作条件进行调和,一般润滑油要由1~3种基础油和1~5种添加剂调和而成。

图1-6 润滑油生产流程
调和是生产润滑油的最后一道工序。调和的方法分为罐式调和和管道调和两种,我国现阶段大都采用罐式调和。
由于润滑油的品种多、数量少,除了像燃料油采取泵送循环的办法在较大的容器中进行调和外,还同时采取在中、小型容器中用机械搅拌或压缩空气搅拌的办法进行调和。
调和的步骤是按一定的比例先将各润滑油精制组分从原料油储罐中泵入调和罐,然后再加入各种添加剂进行调和。但调和高黏度润滑油时,为了调和均匀,在调和容器内必须装有蒸汽加热盘管,以降低油的黏度。
由此可以看出,商品润滑油的生产包括润滑油基础油的生产、润滑油添加剂的选用、基础油和添加剂的调和三部分。本书中润滑油的生产部分将按照润滑油生产流程来展开,其中第二章和第三章将介绍润滑油基础油的生产,第四章介绍润滑油添加剂的选用,第五章介绍商品润滑油的调和。