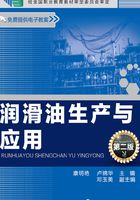
第一节 矿物润滑油基础油原料的制备
物润滑油基础油的原料由烷烃、环烷烃、芳烃、环烷芳烃和少量含氧、含氮、含硫有机化合物以及胶质、沥青等非烃类化合物组成。带长侧链的单环和双环烷烃类是润滑油的理想组分。沥青、胶状物质、带短侧链的多环烷烃、带短侧链的多环芳香烃、环烷酸类和具有高熔点的大分子固态烃类(蜡)以及某些含硫、氮、氧的化合物对润滑油的性能有不利影响,称为非理想组分。
矿物润滑油基础油原料制备阶段的工艺结构比较固定,不因原油种类不同而改变,一般由常压渣油的减压蒸馏和减压渣油的溶剂脱沥青工艺组成,分别制备馏分润滑油料和残渣润滑油料,见图2-3。

图2-3 矿物润滑油原料的制备工艺
图2-3中,利用常压渣油中各种组分沸点不同的特点,通过减压蒸馏装置从常压渣油中分离出减压馏分油作为馏分润滑油原料。减压渣油中含有重质润滑油料和大量胶状物质,将减压渣油中的重质润滑油料和沥青质、胶质分开的工艺过程称为渣油脱沥青,常用的脱沥青方法是丙烷脱沥青法。
一、常压渣油减压蒸馏
1.减压蒸馏的基本原理
原油蒸馏是将原油加热,其中轻组分汽化,将汽化的轻组分导出进行冷凝,使原油中轻、重组分得以分离的过程。原油是由烃类和非烃类组成的混合物,原油中各组分的沸点不同,分离时的产物为沸点范围不同的馏分。
原油蒸馏依据蒸馏塔的操作压力不同分为常压蒸馏和减压蒸馏。通过常压蒸馏,可以把原油中350℃以前的汽油、煤油、轻柴油等直馏产品分馏出来。
在常压下进行分离,如果要将沸点高于350℃的馏分分离出来,必须使操作温度达到四五百度以上。高温可能导致重质油中的胶质、沥青质等不安定组分发生裂解和缩合等化学反应,不仅会降低产品的质量,而且会加剧设备的结焦而缩短生产周期。
常压渣油在减压加热炉中被加热,部分组分汽化,加热的最终温度取决于减压塔的拔出率和重质组分的热分解温度。减压塔的残压一般在8.0kPa左右或更低,它是由塔顶的抽真空系统造成的。从减压塔顶逸出的主要是裂化气、水蒸气以及少量油气,馏分油则从侧线抽出。减压塔底产品是沸点很高(500℃以上)的减压渣油,原油中绝大部分的胶质、沥青质都集于其中。
依据生产的产品不同,减压蒸馏可分为润滑油型减压蒸馏和燃料油型减压蒸馏,本书中提到的减压蒸馏特指润滑油型减压蒸馏,减压塔顶的残压为5~8kPa。
2.润滑油型减压蒸馏的工艺特点
以生产润滑油基础油原料为主的减压蒸馏的分馏效果的优劣直接影响到其后的加工过程和润滑油产品的质量。润滑油基础油原料的质量要求黏度合适、残炭值低、色度好和馏程窄。因此,对润滑油型减压塔的分馏精确度要求高,不仅要求有高的拔出率,而且应具有足够的分馏精确度,实现的关键是尽可能提高汽化段的真空度。
(1)塔底采用较大的汽提蒸汽量 塔底采用较大的汽提蒸汽量的目的是降低减压蒸馏塔汽化段的油气分压。
(2)塔板间距大,进料段和塔顶有较大的气相破沫空间 减压塔处理的原料较重、黏度大,而且还可能含有一些表面活性物质,加之塔内的蒸汽流速大,因此蒸汽穿过塔板上的液层时形成泡沫的倾向比较严重。为了减少携带泡沫,减压塔的塔板间距比常压塔的大,而且在塔的进料段和塔顶都设计了很大的气相破沫空间,并设有破沫网等设施。
(3)塔板数少,每层塔板的压降小 减少减压塔塔板数和降低气相通过每层塔板的压降的目的是为了在满足分离要求的基础上,降低从汽化段到塔顶的压降。
减压塔在很低的压力(几千帕)下操作,各组分间的相对挥发度比在常压条件下大为提高,比较容易分离。因此,有可能采用较少的塔板而达到分离的要求,而且减压塔内采用较大的塔板间距,通常在减压塔的两个侧线馏分之间只设3~5块精馏塔板就能满足分离的要求。
为了降低每层塔板的压降,减压塔内应采用压降较小的塔板,常用的有舌形塔板、网孔塔板、筛板等。近年来,国内外已有不少减压塔部分或全部地用各种形式的填料以进一步降低压降。例如在减压塔操作时,每层舌形塔板的压降约为0.2kPa,用矩鞍环(英特洛克斯)填料时每米填料层高的压降约0.13kPa,而每米填料的分离能力约相当于1.5块理论塔板的分离能力。
(4)塔顶不出产品 采用塔顶循环回流而不采用塔顶冷回流,塔顶不出产品,以减少通过塔顶馏出管线的气体量,从而降低塔顶馏出管线的流动压降。
(5)塔顶、塔底采用缩径,中段塔径较常压蒸馏塔塔径大 塔顶不出气体产品,所以塔顶气体流量小,采用较小的塔径。塔底采用较小的塔径是为了减小减压渣油在减压塔底的停留时间,从而减少减压渣油结焦反应的发生。
气相组分在减压条件下,油气、水蒸气和不凝气的比容大,比常压塔中油气的比容要高出十余倍。尽管减压蒸馏时允许采用比常压塔高得多(通常约两倍)的空塔线速,减压塔的直径还是很大。为了使沿塔高的气相负荷均匀以减小塔径,减压塔一般采用多个中段循环回流,也有利于回收利用回流热。
(6)采用低流速的转油线 采用低流速转油线的目的是减小减压加热炉出口到减压塔进料处的压降,从而提高汽化段的真空度。
(7)侧线设置汽提塔 侧线设置汽提塔的目的是为了保证侧线抽出馏分中的轻组分含量满足要求。
3.减压蒸馏的工艺流程
(1)湿式润滑油型减压蒸馏 为了满足在最高允许温度和汽化段能达到的真空度的限制条件下尽可能地提高减压塔的拔出率,在减压塔底使用水蒸气汽提,并且在加热炉管中注入水蒸气,这种减压蒸馏方式称为“湿式减压蒸馏”,是传统的润滑油减压蒸馏方式,图2-4为湿式减压蒸馏工艺流程图。

图2-4 湿式减压蒸馏工艺流程图
湿式减压蒸馏过程中吹入水蒸气起到了汽化剂的作用。由于水分子量小、冷凝温度高、来源广、经济安全,又与油品有很好的分离性,因此水蒸气是很好的汽化剂。在深度减压和吹水蒸气的条件下可大大降低蒸馏温度,使被分离的渣油尽可能地缓解分解。
减压塔中使用水蒸气虽然起到提高拔出率的作用,但也带来了一些不利的影响。首先,湿式减压蒸馏过程消耗蒸汽量大。当减压塔顶残压约8kPa时,每吨进料所需水蒸气的用量约为5kg,而在塔顶残压为13.3kPa时则需水蒸气约20kg。其次,采用水蒸气汽提后,塔内气相负荷增大。塔内水蒸气虽只占塔进料的1%~3%(质量分数),但对气相负荷(体积流量)却影响很大,因为水蒸气的相对分子质量比减压瓦斯油的平均相对分子质量小得多。例如以拔出率为35%(质量分数)、减压瓦斯油的相对分子质量为350计算,则当水蒸气量为进料量的1%(质量分数)时,在气相负荷中,水蒸气的份额约占1/3。从而增大了塔顶冷凝器负荷,而且装置含硫污水的量也增大。
如果能够提高减压塔顶的真空度,并且降低塔内的压力降,则有可能在不使用汽提蒸汽的条件下也可获得提高减压拔出率的同样效果。
(2)干式润滑油型减压蒸馏 不依赖注入水蒸气以降低油气分压的减压蒸馏方式称为干式减压蒸馏。图2-5为干式减压蒸馏工艺流程图。

图2-5 干式减压蒸馏工艺流程图
与湿式减压蒸馏相比,干式减压蒸馏有如下四个方面的优点。
①塔内及加热炉管内不吹水蒸气,使减压塔的负荷大幅度减少。减压塔底吹入水蒸气,虽然能起到降低油气分压的作用,但由于水的分子量比减压馏分油小得多,水汽在减压塔的气相体积负荷中占很大比例,造成减压塔内线速高、精馏段压降大、抽真空设备负荷大等问题。
②降低了塔板压力降及汽化段压力,从而降低所需减压炉出口温度,提高减压拔出率。干式减压塔用填料或填料与塔板混合代替压降较大的塔板,使塔顶残压和汽化段压力都比湿式减压法低。加热炉则采用低速转油线和炉管逐级扩径,以减小转油线温降和压降,使炉出口温度和进塔温度相差不太大,以便在不致引起油品裂解的前提下,取得较高的拔出率。
③在保持液相均匀分布和正常喷淋的情况下,使用填料代替塔板,既有压降小的优点,又可保持相当的精馏作用,故不但能用于洗涤段、取热段,也可用于分馏段。新型高效填料的压降,平均为0.13kPa/m填料,并有较好的分馏效果。对于填料型塔,推荐使用英特洛克斯与格里希格栅混合床。清洗油则采用轻洗和重洗分开设立的措施,这样有利于提高产品质量,降低其残炭值和比色号。
④提高拔出率,降低能耗。由于干式减压分馏塔汽化段压力低,在相同的汽化段温度下,干式比湿式拔出率提高1%~2%。湿式减压蒸馏需要炉管注汽、塔底和侧线吹汽提蒸汽、抽空消耗高压水蒸气;而干式减压则只需要抽空用蒸汽,节省了蒸汽,同时降低了加热炉热负荷以及降低抽真空系统的冷却负荷等,使常减压蒸馏装置能耗降低。表2-1列举了两种减压蒸馏的对比数据。
表2-1 干式减压蒸馏与湿式减压蒸馏操作数据对比

4.减压蒸馏的操作条件
(1)操作压力 高真空是减压蒸馏操作的关键,减压塔的真空度越高,塔内不同馏分间的相对挥发度越大,越有利于油品的汽化及分馏,提高馏分油的收率。另一方面,真空度高,还可以适当降低减压炉温度,减少油品裂解,改善馏分油质量。
①减压抽真空系统。抽真空系统的作用是将塔内产生的不凝气(主要是裂解气和漏入的空气)和吹入的水蒸气连续地抽走以保证减压塔的真空度的要求。图2-6是常减压蒸馏装置常用的采用蒸汽喷射器的抽真空系统的流程。

图2-6 间接冷凝式二级抽真空系统流程
减压塔顶出来的不凝气、水蒸气和由它们带出的少量油气首先进入一个管壳式冷凝器。水蒸气和油气被冷凝后排入水封罐,不凝气则由一级喷射器抽出从而在冷凝器中形成真空。由一级喷射器抽来的不凝气再排入一个中间冷凝器,将一级喷射器排出的水蒸气冷凝。不凝气再由二级喷射器抽走而排入大气。为了消除因排放二级喷射器的蒸汽所产生的噪声以及避免排出的蒸汽的凝结水洒落在装置平台上,常常再设一个后冷凝器将水蒸气冷凝而排入水封罐,而不凝气则排入大气。图2-6中的冷凝器是采用间接冷凝的管壳式冷凝器,故通常称为间接冷凝式二级抽真空系统。
②抽真空极限。间接冷凝式二级抽真空系统中在一级喷射泵前的冷凝器为水冷器,因而在水冷器的操作温度下,水的饱和蒸气压是这种类型抽空装置所能达到的极限残压,再加上管线及冷凝系统压降,减压塔顶残压还要更高些。当水温为20℃时,冷凝器所能达到的最低残压为2.3kPa。冷凝器中的水温决定于冷却水的温度。在炼厂中,循环水的温度一般高于新鲜水的温度,因此,抽真空系统多采用新鲜水作冷却水。
③三级抽真空系统。在一般情况下,20℃的水温不容易达到,因此,间接冷凝式二级抽真空系统很难使减压塔顶的残压达到4.0kPa以下。如果要求更高的真空度,就必须打破水的饱和蒸气压限制。为此,可以在减压塔顶馏出物进入第一个冷凝器以前再安装一个蒸汽喷射器使馏出气体升压。这个喷射器称为增压喷射器或增压喷射泵。设增压喷射器的抽真空系统为三级抽真空系统,图2-7为三级抽真空系统的流程。

图2-7 三级抽真空系统流程
由于增压喷射器的上游没有冷凝器,直接与塔顶馏出线相连,因此减压蒸馏塔顶真空度能摆脱水温的限制。但由于直接与减压塔顶馏出线相连,增压喷射器所吸入的气体,除从减压塔来的不凝气以外,还有减压塔的汽提水蒸气,因此负荷很大。这不仅使增压泵要有很大的尺寸,而且使得增压泵的工作蒸汽耗量很大,使装置的能耗和操作费用大大增加。只有在采用干式减压后减压塔顶负荷大幅度下降的情况下,才适宜用三级抽空来产生高真空度。
(2)操作温度 为了提高减压馏分的质量和收率,要求减压炉具有“低炉温、高汽化率”的特点。当油品加热温度过高时就会发生裂解和缩合反应,而这些反应产物中会含有不凝气体、不饱和烃和胶质、沥青质等。这些物质混入馏分油中就会使馏分油的氧化安定性变差,色度变深,残炭值升高,而且反应生成的裂解气进入减压塔,会增加塔顶抽真空系统的负荷,影响真空度,因此操作过程中一定要严格控制炉温低于400℃。
二、减压渣油溶剂脱沥青
减压渣油中含有相当一部分高黏度的大分子烃类,这部分烃类是宝贵的高黏度润滑油组分,但由于含有大量沥青和胶质这些润滑油基础油生产的不理想组分,因此必须在润滑油基础油原料制备过程中除去。
利用选择性溶剂脱除胶质和沥青质,实现胶质、沥青质与高沸点残渣润滑油分离,是目前最有效的生产工艺。
1.溶剂脱沥青的工艺原理
溶剂脱沥青是广义的溶剂抽提过程。在石油醚和低分子液态烷烃中,渣油内烃类和非烃类成分溶解度有明显差别,这种溶解性能差别被称为溶剂的选择性。在一定温度范围内,溶剂对烷烃、环烷烃和少环芳烃溶解度大,对多环芳烃溶解度小,对胶质溶解能力更小,对沥青质基本不溶,因此可利用溶解度差异将胶质、沥青质与润滑油理想组分分开。在不溶于溶剂的胶质、沥青质组分中,减压渣油中的沥青质聚集成沉淀分离出来。
2.丙烷脱沥青的工艺流程
溶剂脱沥青装置广泛采用的溶剂是一些低分子烃类,如丙烷、丁烷、戊烷及其混合物等。本书中特别介绍以丙烷作为脱沥青溶剂的丙烷脱沥青流程。
溶剂脱沥青工艺流程包括抽提和溶剂回收两部分。图2-8是丙烷脱沥青工艺原理流程图,其主要特点是以生产高黏度润滑油基础油为目的,抽提塔在低于临界点的条件下操作,溶剂回收在接近临界点条件下进行。

图2-8 丙烷脱沥青工艺原理流程图
(1)溶剂抽提 抽提的任务是把丙烷溶剂和原料油充分接触而将原料油中的润滑油理想组分溶解出来,使之与胶质、沥青质分离。
抽提部分的主要设备是抽提塔,工业上多采用转盘塔。抽提塔内分为两段,下段为抽提段,上段为沉降段。原料油(减压渣油)经换热降温至合适的温度后进入抽提塔的中上部,循环溶剂由抽提塔的下部进入。由于两相的密度差较大(油的密度为0.9~1.0kg/L,丙烷的密度为0.35~0.4kg/L),二者在塔内呈相向流动和逆流接触,并在转盘搅拌下进行抽提。减压渣油中的胶质、沥青质与部分溶剂形成的重液相向塔底沉降并从塔底抽出,送去溶剂回收部分。脱沥青油与溶剂形成的轻液相经升液管进入沉降段。沉降段中有加热管提高轻液相的温度,使溶剂的溶解能力降低,其目的是保证轻液相中的脱沥青油的质量。
在此流程中设有两个抽提塔,由第一个抽提塔底来的提余液在第二个塔内进行抽提。由第二抽提塔塔底出来的是提余液溶剂与沥青组成的沥青液,塔顶出来的提取液称为重脱沥青油(也含溶剂),重脱沥青油中主要是相对分子质量较大的多环烃类。从第一抽提塔塔顶出来的提取液则称为轻脱沥青油,溶剂的大部分存在于此提取液中。这种采用两个抽提塔,得到两个含油物流的流程称为两段法。如果只用一个抽提塔,只生产一种脱沥青油和脱油沥青,则称为一段法。两段法的优点是能比较容易地同时保证抽提塔顶和塔底产品的质量,而且还能多得到一个有用的产品,而一段法难以同时生产低残炭值的脱沥青油和高标号沥青。
(2)溶剂回收 溶剂的绝大部分(约占总溶剂量的90%)存在于脱沥青油相中。轻脱沥青液经换热、加热后进入临界回收塔。加热温度要严格控制在稍低于溶剂的临界温度1~2℃。在临界回收塔中油相沉于塔底,溶剂从塔顶(液相)出来,再用泵送回抽提塔。
从临界回收塔分出的轻脱沥青油和从抽提塔分离出来的重脱沥青油中仍含有丙烷,需用蒸发的方法回收,一般是先用水蒸气加热蒸发后再经汽提以除去油中残余的溶剂。由汽提塔塔顶出来的溶剂蒸气与水蒸气经冷却分离出水后,溶剂蒸气经压缩机加压,冷凝后重新使用。沥青相蒸发时必须加热至200~250℃以防止产生泡沫,所以一般用加热炉加热。加热后的沥青相同样是经过蒸发和汽提两步来回收其中的溶剂。
3.丙烷脱沥青的操作条件
影响丙烷脱沥青过程的主要操作条件有温度、溶剂组成、溶剂比、压力和原料油的性质。
(1)温度 温度对溶剂脱沥青过程的影响很大,调整抽提过程各部位的温度常常是调整操作的主要手段。改变温度会改变溶剂的溶解能力,从而影响抽提过程。温度升高时,溶剂密度减小、溶解能力下降,脱沥青油收率下降而质量则提高,脱油沥青收率增大而软化点提高。操作温度越靠近临界温度,则温度影响越显著。操作温度对产品收率和性质的影响见表2-2。
表2-2 操作温度对产品收率和性质的影响

在实际生产中,当生产方案改变而原料不变时,可通过调整操作温度来达到产品要求。表2-2给出了当产品方案改变时,通过操作温度的变化可以达到不同生产方案要求的目的产品。当选用不同溶剂时,应当选择不同抽提操作温度。几种常用溶剂适宜的温度范围为:丙烷50~90℃,丁烷100~140℃,戊烷150~190℃。在最高允许温度以下,采用较高的温度可以降低渣油的黏度,从而改善抽提过程中的传质状况。
在抽提塔内,塔顶温度较高而塔底温度较低,形成了一个温度梯度。适宜的温度梯度对保证脱沥青油的质量和收率非常重要。温度梯度过小或过大都会产生不利影响。除了温度梯度的大小以外,塔内温度还应有合适的温度分布,在进料口以下温度梯度应较小,而在塔的上部温度梯度应较大。
(2)压力 压力对丙烷脱沥青过程也有一定影响,在抽提过程中,必须保持一定的操作压力以保证物系处于液相状态。通常抽提塔内的压力为2.5~4.5MPa。
(3)溶剂比 溶剂比是指溶剂与原料油的比值(一般为体积比)。溶剂比过小,脱沥青油收率低,沥青软化点降低;溶剂比过大,沥青质、胶质等非理想组分可能进入脱沥青油,使脱沥青油的质量变差。一般溶剂比(丙烷/减压渣油体积比)控制为(5~10):1。
4.丙烷脱沥青的主要设备
抽提设备是丙烷脱沥青的核心设备,转盘塔结构简单、效率高、处理量大,广泛用于润滑油糠醛精制和丙烷脱沥青过程。
图2-9为转盘抽提塔示意图。塔中部为抽提段,由转盘、固定环、稳流格栅板和驱动装置组成。上部为脱沥青油沉降段,设有加热盘管。下部为沥青沉降段,转盘的驱动装置可采用在转动轴手部的水轮借助溶剂丙烷来驱动,或将转动轴伸出塔底用变速马达来驱动,由于塔底出轴处的密封泄漏和变速马达防爆问题不好解决,国内仍采用水力驱动方式。丙烷抽提过程中,丙烷溶剂作为连续相由抽提段下部入塔,原料渣油作为分散相由抽提段上部入塔,进行逆相抽提,塔内各层之间的液体由于转盘旋转产生离心力,使重的液体沿转盘面向塔壁流动,轻的液体向塔中心流动,形成横向层流,这种横向流动形成一种剪切应力,使液滴分散成细小粒径,增加了两相的接触表面,从而加快了传质过程,提高了抽提效率。

图2-9 转盘抽提塔示意图
1—翅片管加热器;2—集油箱;3—固定环;4—转盘;5—稳流格栅板;6—驱动水轮