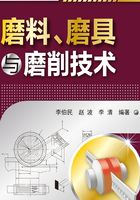
2.4 橡胶结合剂磨具
橡胶结合剂磨具简称橡胶磨具,它是以天然橡胶或合成橡胶和配合剂为结合剂,与磨料混匀并成形,经过加热硫化而得到的橡胶制品。这种制品既有磨具的一般磨削特性,又有橡胶制品的性能特点,是磨削加工中不可缺少的磨具,约占磨具总量的5%。
橡胶磨具具有以下特点。
①机械强度高 橡胶磨具属于硬质硫化橡胶制品,有很高的机械强度,其物理力学性能:抗拉强度为576~720MPa,抗冲击强度为0.05MPa,密度为1.1g/cm3,伸长率为5%~705%,软化温度为60℃。
②富有弹性,抛光性能好 橡胶为具有大分子量、可变形的高弹性体,在常温下表现出高弹性的独特性能。在磨削加工中,受磨削热影响,磨具与被磨工件的接触处于弹性状态,受磨削力作用,磨具表面磨料可以被压入弹性结合剂橡胶中,因而,被磨工件表面留下较浅的划痕,工件表面可获得较低的表面粗糙度值。
③磨具组织紧密,气孔率低 橡胶结合剂原料生胶是一种高黏度的液体,受热软化流动,成为黏弹性物质。橡胶磨具成形加工是在热塑性状态下进行加热硫化,因而制成的磨具坯体组织紧密,气孔率低甚至无气孔,故在磨削过程中排屑和散热性能差,易摩擦生热,烧伤工件,因此影响了橡胶磨具的广泛使用。
④耐热性较差 软质橡胶磨具不耐油,易老化。硬质橡胶磨具则耐油、耐酸、耐碱,可在常温下存放。橡胶磨具耐热性差,60℃开始软化,100℃以上放出H2S气体,产生恶臭气体。温度超过200℃开始炭化分解,达到250~280℃燃烧。故橡胶磨具仅在湿磨中使用。
橡胶磨具的特性决定了其用途,主要制成硬质磨具,如磨轴承砂轮、磨螺纹砂轮、无心磨削导轮;用于精密磨削,在轴承行业广泛应用;还可制成硬质橡胶薄片砂轮,其厚度可薄至0.08mm,对仪表、量具、精密零件进行刻槽与开沟,对贵重金属材料进行切割与切断。所加工出的沟槽有较高的表面质量。另外,制成柔性抛光轮,对精密零件及工具进行抛光和修饰。
橡胶磨具按制造工艺分为滚压法砂轮、模压法砂轮;按结合剂性状分为软质胶砂轮、半硬质胶砂轮、硬质胶砂轮;按用途分为精密砂轮、导轮、切割砂轮、抛光砂轮。橡胶磨具形状、尺寸、材质、粒度的标准代号和表示方法可参考GB/T 2484—1994。
橡胶磨具生产工艺流程如图2-12所示。

图2-12 橡胶磨具生产工艺流程
2.4.1 橡胶磨具的原材料
橡胶磨具所使用的原材料种类繁多,大体上分为磨料、橡胶及配合剂三个部分。
(1)磨料
橡胶磨具常用磨料是棕刚玉、白刚玉。少量磨具使用微晶刚玉、绿碳化硅、黑碳化硅。原料粒度号为F80~F120,少量磨具使用F40~F60和F150~F240,个别使用F280、F400及F800。
橡胶磨具中不同品种磨料对磨具使用性能有一定影响。在相同结合剂的生胶中加入粒度和数量相同的磨料,但磨料品种不同,制成相同规格的磨具,在相同磨削条件下使用,白刚玉(WA)和铬刚玉(PA)磨具强度最低;单晶刚玉(SA)磨具对工件表面烧伤最严重,微晶刚玉(MA)和铬刚玉(PA)烧伤最轻。不同磨料品种对磨具生产中生胶的可操作性有一定影响。棕刚玉(A)与生胶料的黏附性比白刚玉(WA)好;细粒度磨料与生胶的黏附性比粗粒度磨料好。含刚玉磨料的生胶料,对磨料的包辊性能远比SiC磨料好。生胶中含磨料量大时,则胶料性能发脆,易断裂散碎,压片成形困难,但压出的磨具坯体尺寸稳定,硫化变形小。磨料含量少时,压出的坯体尺寸膨胀大,胶料粉碎性差。磨料含量大,结合剂含量相对减少,则会降低磨具强度,耐用度下降,但磨削能力增加且不易烧伤工件。
对于软弹性抛光砂轮、超薄砂轮等特殊用途的橡胶磨具的磨料,需要对磨料的表面涂覆一层酚醛树脂薄膜,制备成包涂磨料(俗称树脂砂),再投入混料,以提高磨料与结合剂的黏结强度,提高磨具的抛光性能,所涂覆的酚醛树脂是极性有机物,容易与磨料的极性表面产生较好的物理吸附力并在受热固化后,能牢牢地把持磨粒。而橡胶受热硫化时,酚醛树脂与橡胶也能与橡胶分子发生交联反应,成为网状硫化橡胶结构,磨粒表面的酚醛树脂薄膜层便与硫化橡胶结合,牢固地连接起来。在生产中,粗粒度软弹性橡胶磨具,细粒度或刚性的硬质硫化橡胶磨具都在使用涂覆磨料,以提高橡胶磨具的耐磨性能和磨削效果。
(2)橡胶
橡胶是生产橡胶磨具的主要原料。按质量计,橡胶占磨具的10%~15%。橡胶的物理化学性能,直接影响磨具的使用性能。
橡胶是高分子化合物,分天然橡胶和合成橡胶,把未经硫化的橡胶称为生胶。按生胶形态分为固体胶(粉末、片状、粒状)和液体胶与胶乳。橡胶弹性高,可塑性强,能够硫化和降解,在室温下长期存放会发生老化现象。
橡胶磨具生产中所用橡胶有天然橡胶、丁苯橡胶、固体丁腈胶、液体丁腈胶等。天然橡胶主要来源于三叶橡胶树。天然橡胶密度为0.9~0.95g/cm3,无固定熔点。加热到50℃开始分解,270℃则急剧分解,300℃以上完全炭化。天然橡胶主要用于制造无心磨削导轮,柔性抛光砂轮等系列产品,并可与合成橡胶并用制成有特殊要求的磨具。丁苯橡胶是合成橡胶中应用最广的一个胶种。它由单体丁二烯和苯乙烯共同聚合而成。按单体配比可分为丁苯-10、丁苯-30、丁苯-50(数字为苯乙烯含量)。丁苯橡胶具有较好的耐热、耐老化性能和较高的耐磨性能,加工工艺性不如天然橡胶,硫化速度也较慢。丁苯橡胶主要用来制造硬质胶磨具。所制成的磨具磨削力强,耐热,耐磨;可用于制作薄片砂轮,在干磨条件下具有优异的磨削性能。丁腈橡胶是由丁二烯和丙烯腈两种单体经乳液或溶液聚合而成的一种高分子弹性体。丁腈橡胶种类繁多。硫化丁腈橡胶对矿物油及其他油类具有高的稳定性,耐磨性、热稳定性比天然橡胶、丁苯橡胶好,丁腈橡胶工艺性能比丁苯橡胶差,可用软化剂或增塑剂,提高可塑性和黏结性能。丁腈橡胶可制成硬质薄片切割砂轮。
(3)配合剂
未经硫化的生胶,分子之间没有交联,不能制作橡胶制品,在生胶中必须加入配合剂,使生胶硫化交联成具有一定物理力学性能的硫化胶。配合剂是多种化学物质。配合剂种类繁多,根据这些化学物质在生胶中的主要作用,分为硫化剂、硫化促进剂、防焦化剂、防老剂、填充剂、增塑剂、软化剂或专用的配合剂等十几个大类。
①硫化剂 在一定条件下能使橡胶发生硫化交联的物质称为硫化剂。硫化剂类型按化学结构可分为硫、硒、碲等元素,含硫化合物,有机过氧化物,金属氧化物,胺类化合物,合成树脂等。其中使用硫磺作为天然橡胶与丁苯橡胶硫化的主要硫化剂。在橡胶磨具生产中除硫磺外,还需加入一定量的促进剂、活性剂等。所以橡胶磨具老化过程是一个多组分体系的平行和依次进行的许多双分子反应的总和。硫磺的硫化过程是硫磺分子在常态下为8原子的环状结构,生胶料中硫磺在硫化温度下及约30J/mol分子能量作用下,环状结构产生开环,生成链状的双基性硫。根据不同条件,硫环断裂后可生成自由基或离子基的双基性硫。双基性硫与橡胶大分子在双键处或α-碳原子处反应时,可在一根分子链上生成“分子内的化合物”,也可在两根分子链之间生成“分子间的化合物”即产生交联。随硫磺用量增加,结合硫量也增加,硫化胶的强度、硬度、耐热性提高,弹性下降,耐溶剂性、耐水性提高,橡胶发脆,冲击强度下降,故硫磺用量不是无限的,有一个最大限量,即100g生胶的最大硫磺含量(g),称为硫化系数(%)。天然橡胶的硫化系数为47%,丁苯橡胶硫化系数为44.5%。
②硫化促进剂 凡能促进硫化反应的物质均称为硫化促进剂,简称促进剂。促进剂可提高和改善硫化胶的物理力学性能,减少硫化剂用量,缩短硫化时间,提高生产率,能促进硫化的适宜温度,保证胶料有相当的焦烘时间,保证胶料的混料、压延及压出过程中的操作安全。
常用的有噻唑类、2-硫磺醇基苯并噻唑(商品名:促进剂M)、二磺化二苯并噻唑(促进剂DM)、胍类(二苯胍)。
③活性剂 能增加促进剂活性,发挥促进剂的硫化效能,减少促进剂用量,缩短硫化时间。硫化活性剂分有机活性剂与无机活性剂。有机活性剂常用硬脂酸,无机活性剂常用氧化锌。
④填充剂与补强剂 在橡胶生产中增大产品体积,节约生胶,改善生胶工艺性能的填充料称为非活性填充剂,简称填充剂。在橡胶生产中可显著提高硫化橡胶的抗冲击、抗伸长、抗撕裂等强度及耐磨耗性能的填充料称为活性填充剂或补强填充剂,简称补强剂。两者均为填料。根据填料的化学组成和形状,可分为粒状填料、树脂填料、纤维填料三大类。粒状填料在橡胶工业中应用最广泛,主要有炭黑、白炭黑及其他矿物。树脂填料中有改性酚醛树脂、聚苯乙烯树脂,主要用于补强。纤维填料主要有石棉、玻璃纤维、有机短纤维等,可用来补强。橡胶磨具制造中常用填料有炭黑、氧化锌、氧化镁、氧化铁、氧化钙、黏土、酚醛树脂等。软质磨具如柔性抛光砂轮,主要采用炭黑、氧化锌。硬质磨具主要采用MgO、ZnO、Fe2O3、CaO、酚醛树脂、橡胶粉。
⑤增塑剂 橡胶进行混炼、压延、压出前,必须先使其具有塑性。加入一些助剂,增加胶料的塑性流动,易于加工,改善制品某些性能。增塑剂分为化学增塑剂与物理增塑剂两类。化学增塑剂加入生胶后能切断橡胶分子链,降低生胶分子量,从而降低橡胶弹性,提高塑性,可称为橡胶塑解剂。物理增塑剂也称软化剂,加入生胶后使生胶产生溶胀,增大生胶分子间的距离,降低生胶分子间的相互作用力,从而使弹性降低,塑性提高。常用化学增塑剂有硫酚、过氧化苯甲酰、硫化苯甲酸等。物理增塑剂有:石油类软化剂,如机械油、锭子油、重油、沥青、石蜡等;松油类软化剂,如松焦油、松香等。
⑥防老剂 橡胶制品在使用和存放中,常变硬、变脆或软化发黏,失去弹性,不能使用,这称为老化现象。老化的主要原因是氧化作用。为防止老化,常在生胶料中加入防老化添加剂。有物理防老剂和化学防老剂。制造软弹性磨具使用化学防老剂A(防老剂甲)及防老剂D(防老剂丁)。物理防老剂是在生胶料中加入石蜡等物质,可在橡胶制品表面生成薄膜,保护橡胶制品不被氧化。
2.4.2 橡胶磨具的配方
橡胶磨具的配方是决定磨具性能的重要因素。它反映成形料的成分及量的关系。配方合理才能使磨具具有所需的性能。配方内容包括各种原材料的品种、数量、硫化条件(压力、温度、时间)。橡胶磨具配方表示方法常用两种形式,即以橡胶为基准,其他组分相对所占的质量比例列出的表示法和以磨料为基准,其他组分相对所占的质量比例列出的表示方法。
橡胶磨具配方设计的基本原则要根据磨具使用中对磨具的弹性、强度、硬度、耐热、耐磨等使用性能要求,选择不同种类、数量的原材料进行合理配方;橡胶胶料(结合剂及成形料)在磨具制造中工艺性好坏,对磨具产品质量和生产效率有很大影响,这就要求胶料既不能过硬也不能过软,既不能包辊也不能粘辊。胶料必须具有良好的工艺性。配方决定磨具制品的成本和效益:配方应能达到使磨具具有良好的使用性能;结合剂和成形料应具有良好稳定的工艺性能,使磨具产品有较低的成本,较高的经济效益,所用原料具有良好的环境友好性。生产软质橡胶磨具,由于所用合成橡胶机械强度较低,必须加入大量的填料,炭黑是具有补强作用的填料,是合成橡胶不可缺少的补强材料,又因为软质胶交联度小,易裂解,故加入适量的防老剂。硬质橡胶磨具在常温下是坚固的固状物,要求具有较高的弹性系数和抗拉强度。结合剂的配方决定磨具硬度、耐热性及弹性。加入硫磺的数量增加,会增加磨具硬度。调整磨具硬度可通过调整结合剂中含硫填料树脂及软化剂量来实现。表2-6所列是橡胶磨具常用材料用量范围。
表2-6 橡胶磨具常用材料用量范围

注:除含胶率和砂结比外,各项用量范围均以橡胶为100计算。
2.4.3 橡胶结合剂的原料加工准备
制造橡胶磨具所用原料有磨料、橡胶、配合剂三大类。原料进入车间后,需根据生产工艺过程及磨具质量要求,对其进行加工处理后,才能用于混料。
①包涂磨料的制备 对于软质弹性砂轮及特别薄的砂轮所用磨料需包涂酚醛树脂,制备成树脂砂,才能用于混料,其他橡胶磨具所用磨料不需再处理,可直接用于混料。
②生胶加工 包括切胶、破胶、塑炼等处理。塑炼是把橡胶从弹性状态变为具有可塑性状态物体的过程。塑炼后的橡胶分子结构受到一定程度的破坏,长链分子断裂成较短的分子,分子量降低,产生降解反应,使弹性降低,可塑性增加。塑炼方法有机械塑炼法,此法是对生胶进行反复碾压,使生胶分子在机械力的挤压和剪切下,分子链断裂,即发生降解作用,使弹性降低,可塑性提高;还可使用热氧化塑炼法,用机械塑炼不能达到所需可塑性要求时,必须再用热氧化塑炼法,此法是把生胶放在空气中加热到相当温度(在120~170℃温度进行),使生胶分子与空气中的氧反应产生氧化,从而断裂为较小分子,使弹性降低,并提高可塑性。
③配合剂加工处理 配合剂种类繁多,形状不一,有粉状、无定形状和黏性流体状,因此加工处理方法也不相同。鉴别不同形态常分别经过粉碎、过筛、干燥、蒸发等处理方法。
2.4.4 成形料的配制
(1)配料
按照市场配料单(市场配方)规定的各种材料的用量进行称量与盛放的过程就是配料。配料量的计算要根据混料机的容量,确定一次混料量;根据砂结比分别计算磨料和结合剂的用量;根据配方计算出结合剂中生胶用量;由生胶的含量计算出各种配合剂的用量。配料时,必须对各种原材料的称重严格控制,误差不超过0.5%。
(2)混料
用一定的设备和方法把配合剂、磨料均匀地混入橡胶中的过程称为混料。将磨料与配合剂均匀地混合在生胶中,所得到的混合料称为成形料。成形料的质量好坏,受到生胶的黏度,生胶对磨料与配合剂的浸润性,配合剂的分散性,纯度、温度和细度,加料的顺序及混料时间等因素影响。
混料方法根据生胶形态和性质分为两类:一类是对液体胶来说,混料方法为松散混料;另一类是对固体胶来说,是采用开放式炼胶机,先使生胶发热软化,再混入配合剂与磨料。
①开放式炼胶机的混料 开放式炼胶机混料分三个阶段进行:结合剂混合、成形料混制(加砂)、成形料辊碎(松散料制备)。
结合剂的混合按开放式炼胶机操作顺序分为包辊、吃粉、翻炼三个阶段。将生胶或塑炼胶、促进剂加入开炼机两辊缝中,控制前后辊辊距,经辊压3~4min,胶料均匀、连续地包于前辊上,形成光滑无隙的包辊胶。形成包辊胶后,先加入硬脂酸等助剂,随后加入ZnO等难分散的助剂,再加入填料,加入填充剂粉料,徐徐进入胶中,将粉料全部吃入后,辊压4~5min后,加入硫化剂,待硫磺全部混入胶中,完成全部吃粉过程。加料的顺序是:生胶→固体软化剂→小料(促进剂、助促进剂、防老剂等)→补强剂与填充料→液体软化剂→硫磺→翻割混匀→下料。翻炼包括割切和翻动。割切与翻动方法有拉刀法、八字刀法与三角包法等多种。
成形料的配制在结合剂包辊胶形成后,调整辊距,使之在辊缝上形成一定的堆积胶,在堆积胶上方均匀不断地加入磨料,随着磨料进入结合剂的数量增多,逐步加大辊距,并开冷却水,使料温下降至82℃以下,待磨料加入2/3后,再加大辊距,继续加入全部磨料,再辊炼一定时间,然后加大辊距使成形料自动脱辊,冷却后等分为若干份,并分别压成长块,撒上滑石粉,停放待用。
②松散料混料机的混料 松散料混料机主要用于混制模压法成形的固体橡胶成形料。该混料机主要工作部件是两个带辊旋突棱的椭圆空心辊子,以不相等的速度对向转动,在混料时起挤压、搓揉、上下左右翻动、撒裂等作用,既把成形料混匀,又把成形料打成松散状态。其工艺过程为:破胶成胶团→软化→结合剂混料→软化→混磨料→打散与过筛→松散成形料。
2.4.5 橡胶磨具成形
将混分好的成形料,用一定的成形方法把其制成各种形状和尺寸的磨具坯体的过程称为成形工序。橡胶磨具坯体成形方法分为:固体生胶成形料,常用辊压法和叠压法成形;松散料,用模压法成形。
(1)辊压法成形
辊压法成形只适用薄片(<20mm)制作。这种成形方法包括出片、剪切、压延、冲型等工序,其工艺流程如图2-13所示。

图2-13 辊压法成形工艺流程
(2)叠压法成形
叠压法成形主要由于固体胶的高厚度(>20mm)磨具的成形。叠压法可分为用模子叠压和不用模子叠压。叠压将压出的成形料片趁热叠在一起,在压延机或油压机上进行施压,使数片料片粘在一起。
(3)模压法成形
模压法用于液态胶成形料和固体胶松散成形料成形。模压法成形能控制磨具组织和制造异型磨具及细粒度磨具。采用定密度成形方法,所使用油压机和模具与树脂磨具和陶瓷磨具类似。
2.4.6 橡胶磨具硫化
硫化是制造橡胶磨具中的重要工序,是决定磨具性能的最后一个过程。硫化是在加热条件下,坯体结合剂中的生胶与硫化剂发生化学反应,使橡胶由线型结构的大分子交联成为网状或体型结构的大分子,导致制件的物理力学性能有明显改善。硫化的目的是使磨具坯体固定其形状,并变成符合质量要求的磨具。正常的硫化将使磨具坯体的强度、硬度、耐热性提高,而伸长率下降,对软质胶磨具弹性有所提高,对硬质胶磨具弹性有所下降。对于大多数橡胶磨具采用热硫化法,少量加超速促进剂的磨具采用冷硫化法。热硫化工艺过程包括以下几个工艺环节:码垛装车→炉体预热→升温→冷却→卸车。
橡胶磨具硫化过程分为焦烧、热硫化、平坦硫化、过硫化四个阶段。焦烧阶段为硫化反应前的诱导阶段,胶料在模具中有良好流动性,但交联作用未开始。热硫化阶段为交联反应阶段,交联开始逐渐产生网构。平坦硫化阶段是硫化历程中网构形成阶段的前期,交联反应结束。胶料抗张曲线出现平坦区,这段时间称为平坦硫化时间。过硫化阶段是网状形成阶段的后期,交联键重排、裂解等,胶料抗张性能下降。硫化历程可用硫化仪测定。
硫化过程中胶料综合性能达到最佳值的阶段,称为正硫化。正硫化时间(正硫化点)是指达到正硫化所需最短时间。在正硫化阶段,胶料的物理力学性能保持最高值。对于含硫橡胶胶料的硫化加热温度、加热时间、硫化压力,称为硫化条件或硫化三要素。
(1)硫化温度、硫化时间和硫化压力
橡胶硫化的温度是促进化学反应速度加快的因素:温度升高,硫化速度加快,达到正硫化点所需时间短。硫化时间包括升温时间、保温时间、冷却时间。在硫化过程中,硫化剂与生胶分子的作用是固相反应,压力对反应速度有影响,在加压条件下进行硫化可避免磨具坯体变形、膨胀等现象,提高硫化温度和缩短硫化时间,使产品组织紧密,机械强度、耐磨性、弹韧性提高,磨具抛光性能好,可降低工件表面粗糙度。
硫化所使用的设备有圆形卧式间接热风硫化炉、加压热空气硫化罐。
(2)橡胶磨具硫化规范
①滚压精磨砂轮 采用卧式硫化罐硫化,硫化温度165℃,硫化时间8h(其中升温5h,保温3h)。采用循环热风炉硫化,硫化温度175℃,硫化时间9h(升温5h,保温4h)。
②柔性抛光砂轮 采用卧式硫化罐硫化,硫化温度160℃,硫化时间8h(升温5h,保温3h)。
③松散料砂轮 采用卧式硫化罐硫化,硫化温度180℃,硫化时间15h(升温10h,保温5h)。
④薄片砂轮 采用卧式硫化罐硫化,硫化温度170℃,硫化时间8h(升温3h,保温5h)。
⑤磨螺纹砂轮 采用带压卧式硫化罐硫化,硫化温度135℃,硫化时间6.5h(升温4h,保温2.5h),硫化压力5.1MPa,硫化完毕逐步放压。