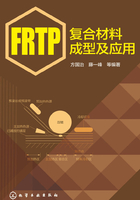
第六节 复合材料生产过程中关键技术与工艺参数的确定方法及评价
一、关键技术与工艺参数的确定
在复合材料产品制造中,生产人员经常依据实验来选择工艺参数,即在加工实际产品之前先试加工小的样件来估计产品的可能加工质量并确定工艺参数。这种以实验为依据的方法存在有许多难以克服的缺点:首先,为了加工一个特定的产品而需要一整套额外的实验,但实验结果并不一定与实际生产情况相符合;其次,对某一种材料通过实验得到的符合一定要求(体积、壁厚、构型)的加工工艺参数在变化了的条件下往往无法使用;最后,通过实验得到的加工参数往往并不是最优化的,即不能保证材料在最短的时间达到最佳加工质量。
现在在复合材料生产工艺研究中,着重于发展制造过程的计算机模拟技术和基于专家系统的计算机辅助复合材料成型技术。它们可以有效地克服实验方法的不足,已成为复合材料设计/制造一体化技术中的关键基础技术。
二、复合材料生产过程的计算机模拟
已提出的关于复合材料成型过程的数学模型,包括了对成型过程多个方面的描述和分析,如成型过程中复合材料内部温度的空间分布及其随时间的变化,成型过程中复合材料内部压力的空间分布和随时间的变化,树脂的加工程度值的空间分布和随时间的变化,树脂的动力黏度值的空间分布和随时间的变化,已压实的材料层数值随时间的变化,吸收体中的树脂的含量随时间的变化,复合材料产品的厚度和重量的值随时间的变化,空隙的尺寸、内部温度和压力的空间分布和随时间的变化,加工过程完成之后的残余应力值等。
仿真实验数据和生产实践表明,各个理论模型可以在不同程度上与实际情况相符合。在复合材料薄板的加工研究中理论模型与实验数值具有很好的一致性,因此可以为优化工艺参数、提高生产水平发挥重要的作用。对工艺过程的仿真研究显示出许多有益的结果。如在传统的工艺参数下,仅有部分种类的复合材料能被完全固化;在较厚材料的成型中,材料不能被充分压实,而且材料中心会产生过热。通过仿真优化的工艺参数还可以大大缩短生产时间从而提高生产效率,即便对很薄的材料的加工也是如此。
在复合材料厚板的成型过程中,复合材料本身固有的难加工特点表现得十分突出。复合材料的低导热率特性使得复合材料厚板在成型过程中难以在其内部维持一个均匀的温度场,而其成型工艺规律又很难通过实验方法得到。通过理论模型仿真和生产与试验,研究人员对复合材料加工的成型机理和相关性质有了丰富的认识,为不同形状尺寸的复合材料构件制造提供了重要指导。
三、基于专家系统的计算机辅助复合材料成型
与传统制造工艺和工艺优化方法相比,基于专家系统的计算机辅助复合材料成型系统具有许多优点,包括对工艺过程的控制不受产品具体形状影响;不需要关于材料性能的详细数据;可以适应不同种类材料的加工以及可以对制造过程提供实时控制。
一个典型的专家系统将包括对材料的温度特性、压实特性、残余应力和空隙等方面实时的综合控制能力,而仿真方法对实际固化成型时的材料性质异常变化和工艺过程异常波动都无能为力。在专家系统中,控制策略和决策规则的选择和使用对建立一个有效的专家系统很重要。可以采用不同的控制策略来满足加工过程中的技术要求。现有方法中比较典型的有两种。一种是McDonnellDouglas公司和一些研究人员使用过的方法——将传感器输出的数据与理论分析模型产生的数据相比对混合来产生控制信息。但这一方法需要关于固化成型的模型和材料性质的数据等先行信息。另外一种方法是美国空军材料试验室所提出的,即将传感器输出的测量值直接与控制规则相结合,不需要关于材料方面的先行信息。所建立的决策规则包括温度、压实(压力与树脂动力黏度)、空隙、残余应力和判断加工结束等各个方面。在实际应用中,各决策规则同时控制加工设备的加热、冷却和压力等各个执行单元;可以通过采用制定优先准则的方法来解决不同控制规则之间的冲突。这种方法的适应性强,得到了广泛研究。
在生产实践中,专家系统控制下的成型方法与传统成型方法相比有明显的优点:生产时间明显缩短,生产效益提高,而产品的力学性能指标没有降低。但专家系统技术一般只适用于制造过程的实时控制,而难以用于对制造过程进行评价。
四、FRTP同种及FRTP与铝合金异种材料搅拌摩擦焊的评价
对于纤维增强热塑性复合材料(FRTP)的连接及其与铝合金的连接,目前常采用的方法有胶接、机械连接和熔融连接,但是各有局限性。笔者所在研究团队在FRTP同种材料搅拌摩擦焊方面,研究了工艺参数对焊缝成形、微观形貌及力学性能的影响,并对断口进行SEM分析;在FRTP与铝合金异种材料搅拌摩擦焊方面,重点研究了两种材料相对放置位置、偏移量和下压量对焊缝成形的影响。主要研究结果如下:
FRTP搅拌摩擦焊试验表明,当下压量、旋转速度和相互匹配时,焊核区的塑性材料才能够充分塑化并流动,能够获得成形良好的焊缝;FRTP接头拉伸性能结果表明,当下压量0.15mm、旋转速度750r/min、焊接速度38mm/min时,接头的拉伸强度最大,为45.56MPa,是母材强度的44.23%。观察断口的横截面形貌可知,接头均在前进侧热力影响区与母材区界面上发生断裂,反映该区域为整个接头最薄弱部位。SEM电镜观察分析可知,母材微观断裂机制主要是碳纤维断裂和纤维-基体界面脱粘,接头的微观断裂机制主要为基体剪切断裂和纤维-基体界面脱粘。FRTP与铝合金进行搅拌摩擦焊搭接试验表明,当铝合金为下板时,接头成形较差,未能得到有效连接;当铝合金为上板时,能够得到成形美观,形成有效连接的搭接接头。当下压量0.16mm、旋转转速750r/min、焊接速度30mm/min时,接头的拉剪强度最大,为18.65MPa,达到胶接强度的71.46%。搭接接头的断口形式主要有沿界面的剪切断裂和在树脂基材处的正断,SEM照片中可以看到在界面处存在微裂纹。FRTP与铝合金进行搅拌摩擦焊对接试验表明,未能得到成形良好、实现有效连接的接头。
五、碳纤维增强热塑性树脂复合材料的研究前沿
碳纤维(CF)增强高性能热塑性聚合物基复合材料在国际上公认为先进复合材料,是国内外复合材料领域的研究重点和发展方向。
有学者对高性能热塑性树脂——杂萘联苯聚醚酮(PPEK)和杂萘联苯聚醚砜(PPES)及其复合材料的高低温力学性能和界面性能进行了研究。
结果表明,在高温和低温环境下,PPES和PPEK及其复合材料均具有很好的弯曲性能,且彼此性能差别不明显,表明其均具有良好的综合力学性能和耐高低温环境性能。
有人采用动态力学热分析(DMA)方法对基体PPES和PPEK及其复合材料CF/PPES和CF/PPEK进行了动态力学研究,得到基体PPEK和PPES和复合材料CF/PPEK和CF/PPES在连续温度下的弯曲模量和损耗角正切值的曲线。研究结果表明,在玻璃化温度(263℃)以下材料的黏性非常小,在玻璃化转变温度区间内黏性表现得很大,同时PPEK和CF/PPEK具有很高弯曲模量并且具有很好的耐热性。
有人基于动态力学热分析(DMA)的研究结果,通过能量方法及Zorowski和Murayama理论,对CF/PPEK的界面剪切强度进行了计算与分析。计算结果表明,DMA的测试结果可以计算-50℃到260℃左右的界面剪切强度,界面的剪切强度随温度的升高逐渐下降,到了260℃左右趋于零。计算得到的常温的界面剪切强度为70MPa,与试验结果吻合较好,因而对先进复合材料(CF/PPEK)界面性能的预测具有理论意义和较高实用价值。