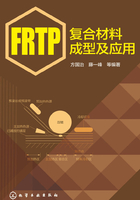
第三节 国外新型复合材料创新与制造能力动态
一、美国建立专门的研究所
美国先进复合材料制造业创新研究所将由以田纳西大学为首组建的联盟承担建设。该联盟由122名成员(包括57家企业、15所大学及实验室、14家其他实体、36家联盟合作成员等)组成,总投资2.59亿美元,其中0.7亿美元来自联邦(美国能源部)、1.89亿美元来自非联邦部门。
该研究所将聚焦于碳纤维等先进复合材料的前沿研究,将开发成本更低、速度更快、效率更高的制造和循环工艺。未来十年内,将致力于降低复合材料总制造成本50%,减少能耗75%,提高再循环能力至95%以上。
该研究所将围绕五大领域分地区开展工作:车辆,风力涡轮机,压缩气体储存,设计、建模和仿真,复合材料及加工技术。
二、美国开发新型复合材料构件自动化检测系统
美国国家国防制造与加工中心(NCDMM)与英格索尔机床公司以及领先军工企业Orbital ATK公司联合宣布,完成美国国防部制造科学与技术(DMS&T)计划资助的三年科研项目的第一期,为美国空军研究实验室(AFRL)成功开发出新型复合材料构件自动检测系统(ACSIS)。该系统在检测通过自动丝束铺放(AFP)设备生产的不同形状飞机零部件的缺陷时,缺陷检出率可高达99.7%。
自动丝束铺放是一种可重复的、具有良好成本效益的复合材料构件成型手段,广泛应用于航空航天领域。虽然自动丝束铺放设备是以在成型过程中实现合适的丝束铺放为目标进行设计和编程的,但复合材料生产过程中固有的一些潜在问题仍可能发生。但当前自动丝束铺放的缺陷检测仍主要采用人工,不仅费时、费力,而且缺陷检出率不高。
一直以来,工业界围绕缺陷自动检测系统开发进行了诸多尝试,但从未实现如此高的缺陷检出率。这套新型自动检测系统的成功研制代表了一次重大进步。利用这套系统可实现复合材料构件成型过程的实时检测,随时提醒操作人员,且可在制造过程中进行修复。所开发的系统还包括电子数据库系统,可实现以电子化的方式记录相关数据,对缺陷进行跟踪。
2015年春,在OrbitalATK公司的F-35联合攻击战斗机发动机舱的生产环境中对这套复合材料构件自动检测系统进行了验证,并与手动检测过程进行了对比测试,主要包括丝束丢失或扭绞、丝束间的缝隙、不准确的丝束铺放、起皱或黏结、异物和碎片等缺陷的识别。8周后,该自动检测系统共检查54层带料,得出缺陷检出率为98.4%~99.7%,误检率为0.1%~0.2%,对于生产环境而言,这两个比率均在可接受的范围内。可以证明,该复合材料构件自动检测系统具备高可靠的缺陷检测能力,这也将有助于提高自动丝束铺放生产效率。
三、Chem Polymer推出一种新型玻纤增强聚酰胺6复合材料
Teknor Apex公司旗下的ChemPolymer于近日宣布推出一种新型的25%玻纤增强聚酰胺6复合材料Chemlon,为注塑成型加工厂商提供了一种可取代含卤素阻燃(FR)材料并符合严格阻燃要求的材料。
该材料在厚度不小于0.8mm时,UL94阻燃性能为V0级。该材料的相对漏电起痕指数为600V,比同类含卤素(一般是含溴)阻燃材料高一倍以上,具有出色的电气性能,可用于汽车、住宅和家用电器,例如卡钩式外壳、断路器、充电器外壳和安全开关。另外,这种新型材料的密度降低了14%,制成的部件更轻。
公司技术经理RichardBarnes指出,这种阻燃材料目前只有黑色配方获得了UL的认可,预计其着色性能会远远超过含溴阻燃材料和基于红磷的不含卤阻燃材料。通常情况下,这些材料只有黑色的才符合规格要求。Barnes说:“长期以来,相比起含溴的阻燃材料,不含卤素的阻燃材料比较难以使用玻纤作为填充材料,因此不含卤素的聚酰胺相对较少,北美市场就更少。对于寻求开拓世界阻燃性零配件市场的厂商,我们的新型Chemlon材料提供了一种性能更好的替代材料。”
Chemlon现已投入商业应用,用于制造车辆发动机的空气过滤器外壳。
四、AGY新型PCB用玻璃纤维
为应对高速数字电子器件的迅速发展,美国AGY公司近日推出一种用于印制电路板(PCB)的低损耗玻璃纤维——L玻璃纤维。这种玻璃纤维的介电常数和损耗因数都很低,故极适用于要求比E玻璃/环氧材料更高信号速度和信号完整性的电路板。
具有低介电常数和低损耗因数的基体材料已成为高速数字体系如移动通信基站、高端路由器和服务器、高速存储网络的核心条件。随着这些体系的高速化,必须使用低损耗的基体材料来保证信号速度和信号完整性。
在10GHz频率下,L玻璃纤维的介电常数为4.86、损耗因数为0.0050,而E玻璃纤维的介电常数为6.81、损耗因数为0.0060,因此L玻璃纤维的低损耗性能使其成为高信号速度作业的理想材料。此外,L玻璃纤维的热膨胀系数为3.9×10-6℃-1,而E玻璃纤维的热膨胀系数为5.4×10-6℃-1,这使得L玻璃纤维成为IC封装基板的佳选。因为在此用途中如果玻璃纤维的热膨胀系数与硅的不适配,会因热环境致使电路板产生缺陷。
AGY的L玻璃纤维纱将以多种纱线密度规格供应,它们可按106、1080、2113/2313和2116织物牌号织造低损耗的玻璃布。另外,根据市场需要,还可生产更多规格的纱线。
五、Fiber SIM 5.5增强复合材料制造能力
Vistagy宣布推出复合材料工程软件Fiber SIM 5.5 最新版本。Fiber SIM和商业化CAD系统整合在一起,为航天、高性能汽车、船舶、F1赛车和风能工业设计制造复合材料部件和组件。
新推出的软件有一些改进的工具,用于解决在使用纤维铺放技术时所遇到的问题。早期确认过程所需最短时间将有助于使产品开发周期更加顺畅。该版本还将扩大支持服务,有更多的分析包,向客户提供分析师、设计人员,是下游制造业之间传递重要信息的渠道。
随着Fiber SIM5.5的发布,设计人员将使用一种增加生产率的引擎,它将提高速度,减少整个设计模拟时间。同样将有一个像电子表格一样的界面,提高设计人员编辑区域积层技术说明和铺层次序的能力。其他改进的地方包括使用颜色把不同积层的技术要求可视化,提高设计部件的能力等。
六、RTM用树脂及其注射设备
美国3M公司最近开发出一种新的单组分RTM专用环氧树脂PR500。该树脂比常用的RTM环氧树脂有较高的力学性能,并且有较长的室温贮存期。由于它的交联密度较低,因此玻璃化转变温度较高,属于耐久性树脂之一。由于该树脂吸湿性较小,因而可在热湿状态下成型。固化树脂的抗弯模量为3496MPa,短臂剪切强度为83~90MPa,高于常用RTM树脂的剪切强度62~69MPa。
PR500树脂在室温下呈团糊状,在160℃温度下黏度急剧下降,与水样相接近,可供RTM设备注射使用。该树脂的固化温度和时间为180℃,2h。温度因素对交联密度的影响比压力因素更甚。该树脂室温下的贮存期为6个月。PR500树脂特别适用于生产复杂的飞机零部件,例如螺旋桨叶片,喷气引擎门,引擎叶片罩等。
目前,PR500已应用于ATR42/72运输机的螺旋桨叶片,这是由美国叶片制造商哈密尔顿标准件公司和法国RatierFigeac公司共同合作完成的。另悉,美国Graco公司,已为PR500树脂生产了RTM专用泵。
该公司为适应使用3M公司的PR500RTM树脂,专门设计了一种新型的RTM注射成型机。该设备的特点,是加热系统设计安置在树脂贮存器的后面,这样可以缩短预注射加热浸渍而后压入树脂容器所需的时间。该设备的气动泵位于机器的上端,并设有一个电热平台。由于PR500树脂在室温下的黏度较高,且难以控制,因此该设备采用在平板上进行注射,再经过电加热室后,才进入模具之中。
由于贮存器内的环氧树脂并没有被加热,因而完成注射过程后树脂不会固化,其回流部分还可以被再利用。该机器的PR500设计注入量为4.45L树脂,足以制造飞机上用玻璃钢部件。当注射温度和压力超过某一限度时,该机器将自行关闭,并进行自动调整。
当超过预先设定的温度极限时,自控线路的传感器将自动关闭。生产时的设定温度,一般为82℃,还可以根据用户需要进行调整。控制屏上的记录装置,可同时显示出平板上和模塑室内的温度数值。设备预设压力为2.8MPa,也可以随用户的需要而改变。当超过极限压力时,泵机将自动关闭。其最大注射压力为5.9MPa,在72℃温度下,最大的瞬时流速和连续流速,分别为340g/s和54g/s。
七、超轻碳纤维复合材料制备一体式设计自行车
据悉,世界上第一台真正意义上的一体式设计自行车于2016年问世,其框架采用了超轻碳纤维复合材料。众筹平台Kickstarter上线了这款没有轮毂和辐条的智能自行车(如图1-2)。

图1-2 一体式设计自行车
该智能自行车乍一看颇有点像《创光速战记》里面的LightCycle光轮,它有个十分高端上档次的名字——Cyclotron(回旋加速器)。
这款自行车装备了自充电电池、无轮毂车轮、非充气轮胎、自动光传感器等,更重要的是,它的框架使用的是超轻碳纤维复合材料,整车不含脚踏的重量在11.5kg左右。车身搭载两个无辐条空心轮胎,外围是一圈由固体聚合物制成的轮圈,带有强烈的未来气息。
据该公司在众筹页面的介绍,为了达到超轻复合材料结构,他们在中央超轻核结构外包裹两层碳纤维,如此可以使用更少的碳纤维和树脂,同时也不降低稳定性。设计者声称这款自行车上已经拥有超过15项科技专利了。
八、制造聚氨酯复合材料的纤维复合喷射技术
德国克劳斯玛菲公司制造聚氨酯复合材料的FCS(纤维复合喷射)技术是一种新颖的解决方案。它面向大型纤维复合材料制品市场。典型应用是用于制造一般用途车辆(如公共汽车、拖拉机等)的车身部件和卡车的导风板、驾驶室等。在建筑和基础设施行业中也有很多潜在市场。
1.复合喷射技术工艺
把连续的玻璃纤维无捻粗纱喂入切割机,切成规定长度,同时聚氨酯组分在混合头中混合,通过专用喷嘴送出。被切短的玻璃纤维被喷入一喷射器,在此被聚氨酯混合料浸渍。形成的玻璃纤维增强聚氨酯配混料按照预定的铺层构型逐层喷覆在模具上。
纤维含量和纤维长度可经调节来适配产品要求,也可指定一些不含玻璃纤维的喷射层。例如,在配用模内涂饰工艺的时候,这两种工艺的结合可在一道工序中做成高光泽的表面。不含玻璃纤维的喷射层可防止纤维与涂层接触,从而形成无瑕疵的表面。
2.同轴喷射可提高设计自由度
在第一代FCS系统中,切割机就位于混合头旁边,切短的玻璃纤维从侧部滑落到一流槽中,进入喷射器。该系统有一些缺点:其一是敞开的流槽引起的飞丝问题;其二是喷射方向只能垂直向下。因此第一代系统不适合生产具有复杂三维形状的制件。
为此,克劳斯玛菲公司完全重新设计了玻璃纤维到达混合头的方式。这种第二代系统更灵活,更清洁。纤维通过文丘里喷嘴和一密闭管同轴进入喷射器,这就可使喷射器摆动运行,最大可摆动90°,把玻璃纤维与聚氨酯的配混料喷射到竖直面上。这为设计人员提供了很大的设计自由度。
密闭的喂料系统尽量减少了飞丝,同时纤维能被聚氨酯均匀浸渍。同轴喂纤还意味着切割机不必紧靠混合头,这使操作人员到达混合头更加方便。
3.四组分混合头拓宽用料范围
FCS工艺中采用的四组分混合头提供了选用多种材料的可能性。例如,选择不同的多元醇(最多达3种),就可在同一产品中兼容致密层和泡沫层。泡沫层可减轻产品重量,还可改善声学性能。另一变异方法是使用两种不同的多元醇和两种异氰酸酯。换句话说,该系统可做成两种完全不同的聚氨酯体系,例如产品外层是用聚氨酯制成的耐紫外线皮层,而内层则是普通的聚氨酯。