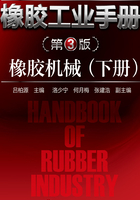
第1篇 力车胎机械
第1章 力车胎机械总述
1.1 概述
力车胎是橡胶产品的一个重要种类,包含摩托车轮胎、自行车轮胎、手推车轮胎和多种用途的小轮径充气轮胎,即除汽车轮胎以外的各种充气轮胎。按中国橡胶工业协会力车胎分会的统计,主要会员企业2011年生产摩托车外内胎26864.1万条,自行车外内胎63443.1万条,手推车外内胎2010万条,估计全国的产量是此统计数的2倍。按我国海关总署的统计,2011年出口自行车外内胎34249.27万条,出口摩托车外胎19925.5万条。据中国橡胶工业协会力车胎分会的调查,我国有力车胎生产企业300家以上,生产力车胎专用设备的企业有近20家。
1.1.1 用途和分类
生产力车胎产品使用的机械设备分两大部分:一部分是橡胶工业通用机械,如切胶机、开放式炼胶机、密炼机、压延机、过滤机、挤出机等;另一部分是力车胎专用机械,如钢丝圈制造机械、胎面挤出生产线、胶帘布裁布机械、外胎成型机械、内胎挤出成型生产线、内胎接头机、内外胎硫化机等。本篇集中介绍的机械主要是力车胎专用机械。
1.1.2 力车胎制造工艺过程与加工设备的关系
力车胎生产工艺流程与加工设备的关系如图1-1所示。

图1-1 力车胎生产工艺流程与加工设备的关系
1.2 力车胎机械的技术进步和发展趋势
1.2.1 钢丝圈机械
(1)钢丝圈是力车胎的重要部件 力车胎行业制造钢丝圈有两种工艺:一种是由ф1.83~2.40mm的冷拉钢丝定长裁断、两头搓丝、套入小套管后冲压压牢而成圈;另一种是将ф0.83~1.0mm的镀铜钢丝经过压出机包胶后,成圈、裁断、缠纱而成。前种工艺制成的钢丝圈称为单根钢丝圈,后种工艺制成的钢丝圈称多根钢丝圈。
(2)单根钢丝圈 单根钢丝圈的制造最早是将盘卷的钢丝调直,定长裁断、碰焊对接成圈,然后在接头处包薄铁皮、上焊锡加固。因包铁皮和上焊锡工艺复杂且质量不易保证,后来改为裁断后将钢丝两头搓出棱形花牙扣,再弯接成圈,在对接处套上小钢管套,用小冲床压实。将来的发展方向是调直、定长裁断、碰焊对接成圈一机化,其技术关键是碰焊对接接头强度要达到钢丝本身强度的80%以上。
(3)多根钢丝圈 多根钢丝圈的生产最早是钢丝调直后经酸洗除锈、蒸汽加热去油,然后挤出机包胶再成圈、裁断、用胶布包扎钢丝头,最后在缠纱机上缠纱而成。后将酸洗除锈改为砂洗除锈。由于自行车外胎的钢丝圈是1×3结构(1根包胶钢丝绕3圈),很多企业一条包胶挤出线配套2个或3个成圈工位。多根钢丝圈包胶成型生产线的发展趋势是电加热取代蒸汽加热,自行车外胎钢丝圈改为2×2结构,摩托车胎钢丝圈3×3、3×4结构,不再包钢丝头,成圈后自动推出,一线多工位的全自动生产线。也可以同时并排挤出9根钢线,同一成圈鼓成型3个3×3或3×4的钢丝圈,推出冷却后再分为3个钢丝圈,以提高生产效率。
1.2.2 胎面成型机械
(1)胎面成型 力车胎产品的胎面成型主要有挤出机挤出成型和多辊压延机压延成型两种。一般截面面积小的胎面成型用多辊压延机,截面面积大的胎面成型用挤出机。压延机压延胎面的工艺简单、投资小、效率高。挤出机挤出成型胎面,品种规格转换快捷,胎面的致密性好,挤出的多色胎面质量好,是力车胎胎面成型的发展趋势。
(2)用压延机压延成型胎面 用压延机压延成型胎面最早是两辊机,由于致密性不够,胎面夹带气泡多,后来都改为三辊或四辊压延机。双色胎和多色胎出现后,又有了五辊、甚至七辊压延机。从发展趋势看,今后将是两台四辊压延机串联,后面加上喷淋冷却线,最后是自动卷取装置。做到一线多用,既能压出单色又能压出双色、三色的胎面。
(3)用挤出机挤出胎面 用挤出机挤出胎面早期都是热喂料挤出机,长径比较小。现在都是长径比较大的挤出机,或冷喂料挤出机,挤出双色胎面或压出顶胶与侧胶配方不同的胎面都用内复合双螺杆挤出机。将来的发展趋势是冷喂料挤出机生产线,单螺杆机或多螺杆内复合机组。挤出机用无级变速电机,挤出胎面由红外线测量仪测量尺寸,并将有关数据反馈并指令电机调整速度以保证挤出胎面的尺寸符合工艺要求。挤出机配上喷淋冷却输送带和自动卷取装置,将胎面成型冷却后卷成长卷待用。
1.2.3 胶布裁剪机械
(1)力车胎产品所用的胶布 力车胎产品所用的胶布有胶帘布和细布。胶帘布是经线较密、纬线较疏,用作外胎的骨架加强层,用立式或卧式裁布机裁剪。细布是指经线和纬线密度基本相同的平纹布或帆布,用作外胎胎趾包边或内胎气门嘴加强的垫布。平纹布用撕布机撕成布条,帆布用卧式裁布机裁成45°角的布条。
(2)平纹布 平纹布早期是卷在木轴上用车床车成胶布条卷,现在是用撕布机撕裂成布条后再卷成胶布卷。用车床车的优点是布条边缘整齐美观,但效率低;用撕布机正好相反,效率高但布边不整齐。将来的发展趋势是把切割胶丝的刀具移植到撕布机上,胶布靠刀具切割成纵向胶布条后再自动卷成布卷。生产效率高,布边又整齐美观。
(3)胶帆布 胶帆布的裁剪从手工到机械裁剪均采用卧式裁布机,几十年来没有多少改进。将来的发展趋向是在现在机型上改进切割胶布的机构,使胶布条的宽度尺寸更精确;改进传输带,使胶布条运行更平稳,利于与人工接头自动成卷的机构组为一体。一个人即能操作一台机,提高胶布卷质量、提高劳动生产率。
(4)胶帘布 胶帘布的裁剪有立式和卧式两种裁布机。立式裁布机由胶帘布导开传送机构和夹持裁布装置组成。胶帘布由传送机构拖上2m高处,然后向下垂落进入裁剪区,裁布装置夹紧胶帘布后裁刀沿轨道快速将帘布按一定的角度切割。立式裁布机占地面积小,裁剪机构简单、成本低、效率高,但被裁下的胶布片尺寸不够精确。
卧式裁布机又有老式和新式两种机型,老机型同现用的胶帆布裁剪机相似,只是工作面的宽度和裁剪胶布片宽度大些。老式机与新式机的胶布导开传动部分没有太大差别;老式机是靠链轮带动刀片切割胶帘布,新式机是用同步带带动电动旋转的圆盘刀片沿着轨道切割胶帘布;新式机裁布后的胶布片有卷取装置。新式机较老式机调整胶帘布裁切角度更简便和精确,裁切的胶布片尺寸更精确,胶布运送平稳,胶布片搭接和卷取由一个人操控一台机,生产效率高。将来的发展方向是提高精度和效率,如两片或多片胶布联裁,或两片一次裁切,待胶布搭接后进入卷取前再一分为二,裁成两片进行卷取,提高劳动生产效率。
1.2.4 外胎成型机械
(1)力车胎外胎成型机械 从工艺方法或机械结构形式可分为双鼓包叠式成型机、折叠式单鼓成型机和胀鼓式单鼓成型机。
(2)双鼓包叠式成型机 双鼓包叠式成型机主要由两个成型鼓(一个主动鼓、一个从动鼓)、包边装置和传动装置组成,用于硬边自行车胎和断面较小、层级较低的其他充气轮胎的成型。按双鼓的布局形式,又可分为水平(卧式)双鼓包叠式成型机和倾斜(立式)双鼓包叠式成型机。双鼓包叠式成型机是从双鼓缠绕式成型机革新改进而成。缠绕成型的轮胎帘布搭接接头多,使轮胎在运转中产生跳动,轮胎充气后也存在藕状膨胀的外观疪病。双鼓包叠成型的轮胎,胎冠处的帘布是三层,而圆周上的帘布搭接头可减少到1~2个,不但提高了轮胎运转时的平稳性,而且提高了轮胎的耐刺性能和耐磨性能。水平(卧式)双鼓包叠式成型机一般只用于成型胎壳,贴铺胎面胶为另一台设备完成;倾斜(立式)双鼓包叠式成型机一般是成型胎壳和贴铺胎面胶同机完成,倾斜(立式)双鼓包叠式成型机是真正意义的外胎胎坯成型机。
(3)折叠式单鼓成型机 折叠式单鼓成型机是一种较古老的成型机。用于软边结构的轮胎成型时,成型鼓为平鼓;用于硬边结构的轮胎成型时,成型鼓是半鼓,单鼓折叠结构便于成型的胎坯从鼓上取出。摩托车轮胎已经淘汰了折叠式单鼓成型机而代之以胀鼓成型机,软边轮胎和6in(1in=25.4mm)以下的小轮胎或28in以上的大轮胎还使用折叠式单鼓成型机。折叠式单鼓成型机结构简单、价格便宜,但手工作业多、生产效率低。
(4)胀鼓式单鼓成型机 胀鼓式单鼓成型机是较先进的一种机型,用于硬边结构轮胎的胎坯成型。由可收缩或胀大的成型鼓、翻包机构、供布供胎面胶机构、压实装置、定中灯和传动机构组成,自动化程度高、生产效率也高。按不同的翻包机构可分为弹簧翻包成型机和胶囊翻包成型机。其中用于自行车轮胎成型的弹簧翻包机构与用于摩托车轮胎、沙滩车轮胎的弹簧翻包机构有所不同,前者的翻包行程要超过胎坯宽度的50%,翻完一边再翻另一边,后者翻包行程较短,可两边同时翻包。
胶囊翻包成型机的翻包是可充气的胶囊推移变形完成胶帘布的翻包,由于翻包的行程较短,只适用于摩托车、沙滩车轮胎的成型。
胀鼓式弹簧翻包单鼓成型机是目前应用最多的外胎成型机之一,目前最先进的成型机都是由此机型改进而成。将来的发展趋向是更加精确、高效、自动和适应性广。精确是指各部件加工精确,保证了成型机各种动作准确、运转平稳,能达到多色胎、贴边胎的成型要求。成型鼓由两级胀鼓发展到三级胀鼓,符合子午结构轮胎的成型要求。高效与自动化程度总是紧密相连,将来的成型机应尽量减少手工动作,如用机械手夹送钢丝圈和取成型好的胎坯;如将胎面自动定长裁切后按程序送到成型鼓上,也可按工艺要求设定全部的自动控制程序。适应性广是指不但能成型钢丝圈的硬边胎,也可以成型芳纶胎圈的可折叠轮胎或管式胎;不但可以成型黑色胎、单色胎,还可成型多色胎、贴边胎。
1.2.5 外胎硫化机械
(1)外胎硫化机械 外胎硫化机械按动力加压的方式分为电动硫化机、水压硫化机和油压硫化机三类。从硫化工艺方式分为普通硫化机和胶囊硫化机(也称隔膜硫化机)。
(2)电动硫化机 电动硫化机是较早的一种硫化机型,由电机经过减速机后驱动螺杆转动,然后经过连杆推动硫化热板开合或上下运动,达到锁模、加压力。电动硫化机结构简单、安装方便,但维修量大、噪声大,是逐渐被淘汰的一种机型。
(3)水压硫化机 水压硫化机是20世纪末力车胎硫化的主要机型,硫化热板由水压缸推动柱塞作上下运动达到模具开合、加压力。水压硫化机由高压水泵和蓄力器组成的动力站提供动力,是一种制造成本低、维修量少的硫化机,但高压水输送系统较庞大。
(4)油压硫化机 油压硫化机的动力源来自液压站,通过控制阀组控制油缸运动来完成模具的开合和锁模硫化。一般是6~8台机一个动力站,安装十分简便。随着机电一体化技术的不断提高,油压硫化机的优点更显突出,是目前较受欢迎的一种硫化机。
(5)胶囊硫化机 与普通硫化机不同,普通硫化机是用风胎作软芯模进行硫化,胶囊硫化机是用隔膜作软芯模进行硫化。胶囊硫化机在热板中央有一个能上下伸缩的中心机构,提供隔膜上下伸缩的动力,利用中压的气体使隔膜芯模在硫化过程中根据工艺需要进行加压或与胎分离。有电动式胶囊硫化机、水压式胶囊硫化机或油压式胶囊硫化机,将来的发展趋势是三层双向传热的胶囊硫化机。
1.2.6 力车内胎机械
(1)力车内胎机械 力车内胎机械是指内胎胎管挤出、冷却、打孔、装嘴生产线及内胎接头机、内胎硫化机和内胎整理等机械。
(2)内胎胎管挤出、冷却、打孔、装嘴生产线 目前有两种形式:一种是适合于用紧固式气门嘴内胎的大皮带生产线,胎管挤出后,上外隔离剂粉并进行长距离的空气冷却,然后定长裁切,推入2.6m宽慢速传动的大皮带上,由人工在大皮带上对胎管打孔、装气门嘴;另一种是胎管挤出后,进入水喷淋冷却,再吹干表面水分,打孔、贴胶垫式气门嘴、裁切后上外隔离粉(也有上外隔离液再用热风吹干)。
(3)内胎接头机 按切断胎管的进刀方式分,有竖式落刀的接头机和横向进刀的接头机。竖式落刀的接头机是较早的机型,呈八字形的切刀由电加热、气缸推动从上沿燕尾槽向下运动,切断胎管后又按原路线向上复位。被接头的两端胎管分别由左右两边钢质的压槽压盖夹持着进行对接,对接时间由时间继电器控制。左右两边钢质的压槽压盖共四个端面很难调整到同一个平面上,所以对接后的内胎接头会出现一些质量问题。后来被改进为橡胶模口的端面,使内胎接头质量有较大的提高。橡胶模口是在压槽压盖的对接面粘贴一层8mm的橡胶,利用橡胶的变形补偿压槽压盖四个端面不能调到一个平面上的差级。但由于切刀的形式不同,始终不及横向进刀的接头机所接的内胎接头强度高。
横向进刀接头机电加热的切刀不是由上至下垂直切断胎管的上层和下层,而是由胎管平叠的一侧垂直切向另一侧。切刀是步进电机带动丝杠推进,按控制程序慢速切入胎管边缘,然后快速进刀,到快切断胎管另一边缘时又转为慢速,使胎管的切口平整而不带飞边。切刀切断胎管向上提起后再复位,而不是按原路复位。由于以上种种不同,横向进刀接头机所接的内胎接头强度比竖式落刀接头机的接头强度有较大的提高。但横向进刀接头机切断胎管的速度慢,效率低,后经改进为一次接2~4条内胎,提高了生产效率,目前已成为主流的内胎接头机。
内胎接头机的发展趋向是在横向进刀接头机的基础上组成四工位旋转的组合机,一工位为装夹(取出)胎管,二工位是切刀工作,三、四工位是对接延时。一人操控一组机,既利于提高生产效率,又利于进一步提高接头质量。
(4)内胎硫化机 同外胎硫化机一样,按动力方式分为电动内胎硫化机、气动内胎硫化机和液压内胎硫化机三类。电动内胎硫化机是最早的机型,用电机减速后驱动螺杆转动,然后经过连杆推动硫化机热板作蚌式开合、锁模。该机噪声大、开合模速度慢、易烧电机。
气动内胎硫化机的动力来自压缩空气,气缸活塞通过连杆拉动硫化热板作蚌式开合,然后由另一气缸和连杆推动上热板旋转进入卡位,最后由大气缸给内胎模具加压锁模。该机开合模速度快,噪声小,但易撞模,操控安全性不够理想。
液压内胎硫化机是近年采用的最新机型。一般6台机为一组,每台机分上下两层可装两副模具,每组机配有由中低压油泵、油箱组成的动力站,每台机的油缸柱塞推动硫化热板上行锁模,卸压后由热板自重下行开模,上行时由定位开关控制最终的合模速度防止撞模发生,合模速度可任意调节,最快可达2s。该机组占地面积小、噪声低、安装简便、维修量小、节能、省力、生产效率高。将来的发展趋势是进一步提高自动化程度和安全性,当操作工的手不离开热板压合面感应装置将会终止油缸上行合模。液压内胎硫化机发展为导热油为热源硫化内胎,每组机的动力站将有一个能根据导热油温度的波动进行补偿的加热站。确保模具温度的变化在±1℃。
(5)内胎整理机械 目前定型的有上六角机和抽真空机。用紧固式气门嘴的内胎硫化后需把气门嘴的附件,如气门芯、垫片和六角螺母装上,使用的就是上六角机。这种机械由电机通过V带带动一个旋转盘,转盘中央有一个六角孔位能卡着六角旋紧,当旋紧六角的力矩达到规定值时,转盘即转向滑动,防止扭矩过大破坏了气门嘴与内胎的密合,也防止了六角上不紧而使气门嘴与胎身结合处慢漏气。适用弹簧式气门芯的为自动上芯充气机,一般为圆盘式五工位或六工位,一工位装夹内胎并将气门嘴开口朝上,气门芯由振动旋转的圆盘推动从第二工位小轨道的圆孔落入气门嘴内,第三工位将气门芯旋到位,第四工位充气,第五工位将内胎自动推出。
抽真空机是近年研制的内胎整理机械的一种。过去美式气门嘴的内胎充气停放检查后,由人工将气门芯取出抽成真空后再将气门芯装上,不但劳动效率低,而且由于第二次上气门芯易产生气门芯上不到位而出现慢漏气,增加了产生质量问题的机会。抽真空机是不再卸出气门芯直接由机械抽真空。该机四个工位,操作工将胎夹上后开始抽真空,胎由一工位转到四工位时正好是一条胎抽真空的时间,不但提高了生产效率,也提高了内胎质量。将来的发展趋势是内胎抽真空机、卷胎机和自动吸塑包装机联成一条自动化程度较高的作业线。