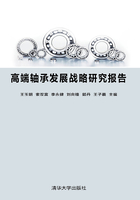
高端滚动轴承状况与发展战略研究(简要版)
轴承是关键的机械基础件产品,俗称机械装备的“关节”,是一个国家的战略性基础产业。轴承性能对机械产品的性能、寿命、可靠性影响巨大,轴承技术发达国家无一不是工业技术先进国家,德国、日本、美国等几乎垄断了当今先进轴承技术和高端轴承市场。
滚动轴承是轴承产业中的主要产品。高端滚动轴承技术是工业核心基础技术之一,体现了一个国家的高端制造能力和制造水平,是国民经济和国防安全重大装备的核心部件,几乎制约着一个国家装备制造业整体关键技术的发展水平。高端滚动轴承制约着高精密机床的精度、刚度和生产效率,制约着高速轨道交通、风电、盾构机等重要装备的可靠性和寿命,制约着汽车工业轮毂单元的升级换代,制约着航空飞行器、航空发动机和地面燃机的推重比、可靠性和寿命,制约着卫星、空间站、运载工具等空间飞行器的长期工作稳定性、可靠性和对极限环境的耐受性,制约着导弹等武器装备的高速性能和极限精度,制约着潮汐、海流、海浪等新型能源发电装备的长期免维护和环境友好性等,还制约着重大装备健康状态管理、智能化、视情维护、结构集成化等先进技术的发展。一句话,高端滚动轴承技术广泛应用于高速铁路机车、精密机床、风电、精密轧机、核泵、航空发动机以及其他国防装备,是提高这类尖端技术产品工作能力、运转精度、稳定性、使用寿命和可靠性最关键和最直接的部件之一。
滚动轴承技术直接或者间接影响着一个庞大的工业产业链。2013年,我国滚动轴承工业的年产值达到了1500亿元,而与此相关的工业年总产值高达10万亿元。但我国目前高端滚动轴承供应严重依赖进口,精密机床、高速列车、风电、盾构、航空装备、核电、轧机、高档汽车轮毂等的新机配套和二级维修市场基本依赖进口,严重制约了装备工业水平的自主升级和转型发展,对国家安全造成了巨大的安全隐患。高端滚动轴承就是高性能滚动轴承,所谓高性能,即要求高转速、高负载能力、长寿命、高可靠性、低振动等,并可耐受极端工况条件(如高低温、腐蚀)等。
由于高端滚动轴承对重大装备的极限性能具有“一票否定”的重要影响力,我国16个重大科技专项中大飞机、高档数控装备等多个专项受轴承技术影响或制约亦日趋明显,高端滚动轴承技术也是西方国家对中国实行禁运的核心技术之一,瑞典SKF公司、德国Schaeffler公司、美国的TIMKEN公司、日本的NSK、NTN等通过收购、重组等,逐步形成垄断局面和技术壁垒,一方面占领中国高端轴承产品民品市场,限制出口高端军品轴承,另一方面长期坚持关键技术不离开自己国家,牢牢占据技术优势,实现高额垄断利润。
据估计,中国高端滚动轴承技术与国际先进水平普遍存在20年以上的技术差距,且由于基础研究薄弱、高端人才匮乏、轴承厂家过于分散、严重陷于价格竞争等,这个差距正在逐年扩大。与国际上高端轴承技术的差距主要体现在先进的材料体系、可靠的设计和验证手段、配套的表面特种处理和改性技术、精准制造工艺和技术等方面,对国际高端轴承领域在结构集成化设计制造、智能化、免维护或者视情维护等相关发展趋势,国内才刚刚开始。
我国对高端滚动轴承的需求日益迫切,技术要求也越来越苛刻,其战略性和基础性特征日益凸显出来。自“六五”开始,国家对滚动轴承开展了连续布局和支持,取得了整体技术的发展,但这些发展成果多半源自技术先进的轴承制造装备的引进和水平提升,由于轴承价值在日益复杂的主机装备整体价值中占比极少,以及长期对材料研究、制造工艺研究、基础数据积累等不足的影响,其战略性和基础性特征长期被忽视,造成了我国高端滚动轴承今天的被动发展局面和恶劣的发展环境。
针对我国高端轴承产业面临的形势和任务,应以航空航天轴承、精密机床轴承、高速轨道交通轴承、大型风电轴承等主要技术为突破口,分类实施相关发展战略。
(1)对于量大面广的工业产品,轴承需求量大,涉及面广,如按照我国年产2000万辆汽车,汽车轴承的年需求量高达10亿套,对于这种数量庞大的工业产品,遵循现代工业的生产规律,鼓励积极采用工业工程技术,以提高产品的稳定性。产品的发展战略应以市场调节为主,在市场机制下,鼓励合理的竞争,建立完备的技术体系为主要指导思想。
(2)对于航空、航天这类批量小、关系国家安全、需要高度定制的小批量多品种产品,要以建立完备体系,走自主化发展的道路为基础,应鼓励资源整合、自主研发、长期积累、突破并集成核心技术,推进工程应用转化,鼓励以点带面,推动滚动轴承整体水平的提高。
如航空及地面燃机轴承(以下统称航空轴承),包括航空发动机轴承、传动系统轴承、飞机机体轴承和附件轴承,同时包含地面燃机相应部位的轴承,由于使用条件极为苛刻,对航空武器装备的正常运转至关重要,是一个国家的战略性工业基础部件,也是航空装备的核心部件,尤其应该如此。
(3)对滚动轴承的共性关键技术,应及早进行行业布局,实施技术联盟战略,尽快开展专项技术研究和工程化应用攻关。
轴承制造的主要工艺过程包括套圈锻造、车削、热处理、磨削及轴承装配等工序。轴承套圈各部位的磨削加工、滚道表面的超精研加工以及滚动体的加工是轴承生产过程中的关键工序,其质量直接影响产品的精度、动态性能及使用寿命。用于这些工序的加工设备约占整个轴承生产设备的40%以上,且以轴承专用设备和特种工艺为主。
在轴承套圈精加工方面,通过引进消化吸收及大量的改进,国内开发了液压驱动自动化磨削、超精加工机床,我国中小规格轴承套圈超精加工设备的加工精度和效率接近国外同类设备,一些精度指标已达到或接近国外先进水平,轴承行业开始逐步采用数控化装备和自动化联线装备,轴承磨加工、超精加工装备基本实现数控化、自动化,促进了产业集中度进一步提高。
国内大规格轴承的加工设备起步较晚,但也取得了良好的业绩,研制出一批高精度数控车床,数控磨床等关键加工设备,打破了国外在该类高、精、尖设备方面的垄断局面,将有力地推动我国在大型、特大型精密、超精密轴承制造领域的快速发展,需要进一步发展配套装备技术。
在高品质钢球加工方面,瞄准当前国际钢球最先进的质量水平,开发钢球加工新工艺,推广钢球树脂砂轮磨研(以磨代研)新工艺,国内主要钢球生产企业开始采用树脂砂轮磨研钢球并实现了批量生产,使钢球批质量稳定性大幅度提高,表面质量明显改善,钢球单粒振动进一步降低且轴承合套率明显提高,进口设备几乎全部实现了国产化,且实现了批量出口。近年来由于滚子轴承的精度、寿命要求越来越高,带有凸度的圆锥滚子、带有凸度的圆柱滚子、球面滚子的加工设备也有较大的发展,国内已能够批量加工Ⅱ级精度的滚子,应该鼓励继续攻关,开展新型材料如陶瓷材料滚动体的制造工艺技术攻关,进一步提升滚子的综合制造技术水平。
国内对于滚动轴承的设计,目前仍以经验设计和仿研为主,近年逐步采用静力学、拟静力学、拟动力学以及动力学等设计方法。应该鼓励在引进Romax、Cobra等国际分析软件和辅助设计软件的同时,积极发展基于中国轴承的材料水平、工艺水平、设计水平、应用水平的自主设计手段,积累自己的基础数据库,并开展设计应用试点和验证工作,支撑从方案开始的完全自主设计技术的发展。
我国在高端滚动轴承领域存在的差距,除了综合技术水平较低外,最主要的两大瓶颈问题就是原材料和制造技术。在制造技术中,装备和工艺都需要有所突破,必须以精良设备和先进工艺的完美结合来保证高端滚动轴承的高精度及保持性,进而保证其高性能及稳定性、长寿命及可靠性等特征质量的实现。国际著名轴承公司都将装备和工艺作为其“技术宝典”之一,从另一个侧面说明了制造技术是其企业的核心竞争力。
为了有效保障高端滚动轴承技术发展战略的实施,在以完善和建设工程技术人员队伍为基础,加大科研项目资金支持力度,构建先进的技术研发平台的总体架构下,采取以下保障措施:
(1)轴承品质的提升,需要长时间的努力,国家需要制定一个长期(10~20年)的战略,选定某几个国家需要解决问题的轴承产品,以点带面,实现轴承行业的全面提升。
(2)面向航空轴承全寿命周期,建立产学研用四位一体国家级航空轴承工程技术中心,形成协同创新平台,统筹基础研究、技术攻关和应用服务;通过技术辐射和转化,带动滚动轴承技术的整体水平提升。
(3)建立进口高端滚动轴承采购、检测、鉴定、服务四位一体的集中化协作模式,促进先进轴承技术的消化吸收和再创新,规范对外合作途径和口径,加速进口轴承的国产化步伐。
(4)建立高端轴承发展战略联盟,培养和建立相对稳定的国家级轴承人才梯队和专家团队,促进专业配套、年龄结构合理,覆盖基础研究、技术攻关、产品研发和应用服务。
(5)进一步加强重点轴承产品的研发体系建设、产品开发、关键技术攻关、产品攻关,根据高端轴承面向的主机行业不同,将高端滚动轴承技术明确纳入国家有关计划或者重大科技专项,适度超前布局核心技术的基础研究。
(6)在国家985、211等高等院校相关专业委托培养滚动轴承、摩擦学、材料科学、表面工程及相关专业的后备人才。
(7)以高端轴承技术联盟为基础,建立数字化和信息化平台,形成先进的能够支撑产品协同研制、全寿命周期管理、质量迭代改进、生产和应用全过程质量控制以及安全保障的系统运行能力。