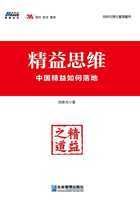
6.丰田倡导的两个精益原则是什么
企业走精益之路,说到底是企业全体员工通过精益改善行动,朝着理想的目标不断修炼意识、思维和能力的过程。企业领导有必要从自己开始转变观念,影响和带领全员一起,信奉精益,实践精益,把企业带向更美好的未来。那么在走向精益的过程中,丰田倡导的两个精益原则至今仍然适用,必须长期坚持,一个是自働化,另一个是准时化。
(1)自働化。
所谓自働化,是那些保障不做不良品或不让不良品流出的机制或方法的总称。因为这些机制或方法拥有判断和自动停止的功能,所以丰田喜一郎坚持使用有单人旁的“働”,意指有人的智慧。
关于自働化,有这样一个美好的故事。年轻时的喜一郎每每看到织布的母亲晚上收工的时候,总会检查出不良品,不良品需要打折出售,觉得很是可惜。不良品大多是中途有经线断线所致。他动脑筋想办法,终于开发出了一个小小机构,每当有经线断线的时候,就会有一个小铁片落下并卡住脚踩动力系统。喜一郎告诉母亲,以后遇到脚踩不动的时候,就停下织布工作,戴上老花镜查看并接上断掉的经线,然后再接着织。从此之后,他母亲就不再生产不良品了,减少了折价损失。这是一个经典改善事例,源于喜一郎的一片孝心。
在管理实践中,为了降低产品不良率,人们花了大量功夫,而且往往吃力不讨好。比如,为了防止设备产出不良品,我们会安排一名设备看护人守在设备旁边,一边看设备,一边查产品;又比如,为了防止不良品流入下工序,我们会在工序间增加检查人员对半成品进行逐一检查;还比如,产品生产结束之后,我们还要进行最终检查。所有这些检查其实都不产生客户价值,检查越多,浪费越大,但又不得不检查。不仅如此,经检查发现不良品时,还要返工,有些甚至需要直接废弃,造成更多的浪费。更可怕的是,所有的检查终究无法保证能够排除所有的不良品,一旦有不良品流到客户或市场,就将造成客户索赔和信誉的损失。可见,通过加强检查来降低产品不良率的做法,终究不是高效益的好办法。
与各种检查相比,自働化就要高明得多。它通常从两个不同层面来实现,一个是研究一次就能做对的“防呆”办法(傻瓜都不犯错),不做不良品;另一个是实在不能保证一次做对时,设法找到能够防止不良品流出的“纠错”办法(出错后被强制纠正)。喜一郎发明的办法,属于纠错范畴。为了与人们崇尚的“制度”进行有效区分,笔者将这些结构化的好办法统称为“机制”,可见机制比制度更可靠。
那么到底什么时候需要研究自働化改善呢?回答是越是靠近品质的源头,自働化改善越有价值。
首先,如果能在产品设计阶段就遵循自働化原则进行改善的话,效果最佳。比如,我们常用的钢笔,从前的做法是,笔身和笔套配套尺寸公差要求较高,加工过程中容易出现尺寸不良,造成返工,而且在钢笔使用过程中还会因为磨损出现松脱现象,造成客户投诉。现在的设计有了改善,即在笔身和笔套间加了一个卡环(或点),然后做大配套尺寸公差,这样做不仅不再产生尺寸不良,还可以保障使用中不会因为磨损造成松脱问题。
其次,可以通过加工工艺、工装夹具或加工设备的自働化改善来消除产品不良。
最后,通过进行自働化检出方法改善,杜绝不良品流出。在网上广为流传的一个使用电风扇检出不良品(检出漏装产品的盒子)的例子就是一个很好的自働化改善案例。
从以上分析得知,通过自働化改善来解决品质问题,是机制导向,而非制度或责任心导向,更能引导我们进行系统思考和方法改善。通过自働化改善,不仅能够降低产品不良率,还能够极大地提高生产效率,减少各类品质损失,值得我们持续坚持。
(2)准时化。
所谓准时化,是指生产过程中通过采用后工序拉动的方法,实现工序间无停滞的快速和及时的流转,即我们常说的JIT。据说喜一郎在创办丰田汽车之前曾前往美国福特公司观摩学习,看到每个车间都堆放着大量中间库存,随问福特人,这是怎么回事。福特人告诉喜一郎,这是大批量生产必须保有的缓冲库存,否则生产就难以顺利进行。喜一郎接着问,这是为什么?回答是,要是没有这些库存作为缓冲,当设备故障、作业失误、不良产生及供料不及时等任何一项异常发生的时候,生产就会因此停止,造成人力等的巨大浪费。喜一郎心想,如果以后做汽车的话,无论如何要反其道而行之,就是以准时化为原则,减少中间库存,减少因为库存造成的大量浪费。
至今还有人说,库存式生产适用于大批量时代,如今是小批量多品种,必须采用准时化JIT生产。而丰田人认为,不管是大批量生产,还是小批量多品种生产,准时化都是一个必须坚守的基本原则。如果不能实现准时化,库存就成了必须。而库存是万恶之源,库存本身是浪费,它占用资金、耗费利息、占用场地、耗费空间资源,还可能带来降价风险等;库存还会派生出许多问题,如搬运、保管、寻找、防护等无价值作业;库存更会掩盖大量的管理不善问题,使得产能不清晰,产出不稳定,停机、停线及物料延迟等异常无人关注,造成工作现场涣散,没有紧张感和节奏感,效率低下。
当然有人会说,我也想做准时化,消除库存。但现实是,如果没有了库存的缓冲,我们将发现到处都会发生停工待料的问题,可能浪费更加严重,得不偿失。抱有此等想法的人绝不在少数,问题出在,他以为追求准时化是一个非此即彼的选择题,要么有库存,要么没库存。而事实是,追求准时化是一个动态平衡的过程,是一个通过改善让库存不断减少的过程。
我们要清楚,现状的库存不管是多少,它都是一种“合理”的客观存在,是自然形成的结果。根据笔者的经验,对于一个没有追求准时化的企业来说,谁也说不清楚,库存为什么是这么多,而不是更少。之所以说它“合理”,是说如果一切都不加以改变或改善,那么库存通常不能少于它,如果少于它,生产就可能停顿,就会造成更多的损失。当然,说它“合理”,并不是说要放任它的存在,而是要从现状出发启动一个持续减少它的循环。
那么该如何启动这个循环呢?如果没有专家指导,绝大多数情况下,企业会让相关部门从研究库存的合理性开始,结果肯定是不了了之,因为现状的库存总是相对“合理”的。在管理实践中,库存只是结果,追求准时化既是原则,也是减少库存的手段。所以要减少库存,必须从准时化改善入手。所谓准时化改善,说到底就是那些与产品生产相关的所有部门,动脑筋想办法,缩短工作或作业周期的过程。
明白了这个逻辑之后,事情就变得相对简单了。
销售部门要设法缩短客户订单的处理周期,并以更快的速度把订单信息告知计划(制造)和采购部门;
采购部门要改善部门工作和供应商能力,更快捷地保障物料供应;
制造部门要持续进行改善,消除制造过程的各种异常,提高设备、工艺、品质的可靠性和稳定性等,最终达到缩短制造周期的目的;
检查部门要改善检查方法,最好实现与制造并行工作,在物料或产品流转中完成检查……
如此这般改善的结果是,整个生产周期越来越短。对应生产周期的缩短,就可以安心地把库存降下来,理论上讲,每缩短一天生产周期,就可以减少一天的库存。许多时候我们发现,越是库存少的企业其订单交付越好,是因为其生产周期足够短;而越是库存多的企业其订单交付越差,是因为生产周期太长所致。
也就是说,以零库存为目标,以准时化为原则,倒逼所有前工序,包括销售、采购、检查和制造等部门进行全面改善,追求设备零故障、工作无差错、无不良产生及无延迟供料等,极大地缩短生产周期。
综上所述,丰田倡导的两大精益原则对于企业经营来说意义重大,值得我们持续坚持。