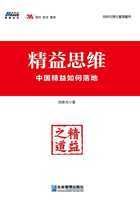
4.剖析丰田TPS与丰田软实力
在日本流传着这样一个故事,美国三大汽车之一克莱斯勒的前CEO罗伯特·伊通先生在1994年初的记者会上骄傲地表明,“我们已经达到了与日本汽车同等的生产效率,从此不再惧怕和丰田竞争。”理由是克莱斯勒在1993年花巨资请美国“熟知”丰田TPS(TOYOTA Pro-duction System即丰田生产方式)的某顾问公司引进丰田生产方式,生产效率得到了大幅度提高。半年之后,克莱斯勒派出了一名干部前去丰田考察,通过整整一天时间的观摩学习之后,这位干部唏嘘不已,其实克莱斯勒公司根本就没有学到真正的东西。
这样的故事在中国也在发生着。据媒体报道,1978年丰田TPS公布后不久,当时的一汽厂长刘守华就带队去日本丰田公司学习,回厂后组织二级干部学习,然后又请TPS的创始人大野耐一来厂讲课,并在生产线上搞试点,建设TPS样板线,一时全厂掀起了学习TPS的热潮,但是不久便销声匿迹。
20世纪90年代,一汽变速箱厂再次尝试引进TPS,在没有增加多少设备、人员和资金的情况下,生产能力由每年8万辆提高到12万辆,但是后来也没有了风声。
接下来就是2002年,一汽成立了引进丰田生产方式领导小组。当年9月,一汽轿车公司由副总经理刘树华带领20多个车间领导和生产骨干花一个多月的时间去日本继续学习TPS。看起来学习获得了相应的成效,一汽轿车最终利用现有资源高效率地生产出了高质量的马自达6型轿车,成了一汽学习TPS的样板。但是内部人士表示,“我们学到的,只不过是丰田生产方式的皮毛。”
人们不禁要问,为什么TPS这么难学?回答这个问题,需要深刻认识丰田竞争力的两个方面:一是有形的硬实力;二是无形的软实力。至今为止,丰田只公布了一个近乎完美的思想体系和方法架构,而对于改善哲学和改善文化的逐步形成与如何走向未来的问题,丰田人并没有或者并不想说清楚。
在笔者看来,丰田外在的硬实力是“末”,内在的软实力是“本”。在学习丰田的时候,人们自觉不自觉地出现了严重的本末倒置现象。人们更多地关注丰田外在的东西,比如高效的生产线、兢兢业业的员工、低缺陷率的产品、整洁有序的现场及灵巧便利的工具设备等,并被这些美好的事物打动。
一说学习丰田,人们首先想到的是学习、模仿甚至复制这些美好的“结果”,很少有人透过表象看本质,很少了解这些美好的“结果”是怎样被创造出来的,丰田的员工为此付出了多少汗水和智慧。人们也很少研究,丰田的改善哲学是怎样形成和被深深植入企业员工体内的,改善文化及丰田员工的改善习惯又是怎样养成的,丰田的领导和员工又走过了一个怎样艰辛的过程。在学习TPS的时候,对于改善哲学和改善文化建设的问题,人们或者不够重视,或者无能为力。
我们应该清楚,通过模仿或者照搬一些TPS做法,确实可以获得生产效率的提高,但是,这样的学习只能带来一时的效果,并不能给企业带来可持续的能力,即不能最终形成全员参与的改善文化。舍本逐末的后果是显见的,绝大多数企业只学到了皮毛,却学不到精髓。克莱斯勒是这样,一汽是这样,更多的企业也是这样。
我们还应该清楚,在丰田所看到的一切,在丰田人看来并不是最好的。即使你能够复制今天丰田所有有形的东西,你也不能与之抗衡,因为丰田人每一天都在不断改进着这里的一切。