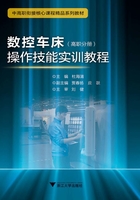
任务二 数控车床的规范操作和安全保障
任务导入
数控车床的规范操作,不仅是保障人身和设备安全的需要,也是保证数控车床能够正常工作、达到技术性能、充分发挥其加工优势的需要。因此,在数控车床的使用和操作中必须严格遵循数控机床的规范,这样才能够对设备和操作人员提供必要的安全保障。
一、任务布置
本任务以卧式经济型数控车床操作规范为主要对象,学习数控车床操作安全注意事项和数控车床发生碰撞安全事故的一般规律以及有关碰撞的预防和解决方法。
【知识目标】
(1)熟悉数控车床规范操作流程。
(2)熟悉数控车床操作安全注意事项。
(3)熟悉数控车床发生碰撞安全事故的一般规律和预防措施。
【技能目标】
(1)会依据操作流程规范操作数控车床。
(2)会正确处理数控车床发生碰撞的解决方法。
二、知识链接
(一)数控车床的规范操作流程
1.安全操作基本注意事项
(1)工作时请穿好工作服、安全鞋,戴好工作帽及防护镜,不允许戴手套操作车床。
(2)不要移动或损坏安装在机床上的警示标牌。
(3)不要在机床周围放置障碍物,确保工作空间足够大。
(4)绝不允许两人同时操作同一台数控车床。
(5)操作人员必须在完全清楚操作步骤的情况下进行操作,遇到问题应立即向指导教师询问,禁止在不知道规程的情况下进行尝试性操作。
2.开机前的注意事项
(1)机床通电前,先检查电压、气压、油压是否符合工作要求。
(2)检查机床可动部分是否处于可正常工作状态。
(3)检查工作台是否有越位、超极限状态。
(4)检查电气元件是否牢固,是否有接线脱落。
(5)检查机床接地线是否和车间地线可靠连接(初次开机时特别重要)。
(6)已完成开机前的准备工作后方可合上电源总开关。
3.开机过程注意事项
(1)严格按机床说明书中的开机顺序进行操作。
(2)一般情况下开机过程中必须先进行回机床参考点操作,建立机床坐标系。
(3)开机后让机床低速空运转10min以上,使机床进行预热。
(4)关机以后必须等待3min以上才可以再次开机,没有特殊情况不得随意频繁进行开机或关机操作。
4.调试过程注意事项
(1)编辑、修改、调试好程序。若是首件试切必须进行空运行模拟,确保程序正确无误。
(2)按工艺要求安装、调试好夹具,并清除各定位面的铁屑和杂物。
(3)按定位要求装夹好工件,确保定位正确可靠。不得在加工过程中发生工件松动现象。
(4)安装好所要用的刀具,必须使刀具在刀库(刀架)上的刀位号与程序中的刀号严格一致。
(5)按工件上的编程原点进行对刀,建立工件坐标系。
(6)设置好刀具半径补偿值。
(7)确认冷却液输出通畅,流量充足。
(8)再次检查所建立的工件坐标系是否正确。
(9)以上各点准备好后方可加工工件。
5.程序运行注意事项
(1)刀具要距离工件200mm以上。
(2)光标要放在主程序头。
(3)检查机床各功能按键的状态是否正确。
(4)启动程序时一定要一只手按开始按钮,另一只手按停止按钮,程序在运行当中手不能离开停止按钮,如有紧急情况立即按下停止按钮。
6.加工过程注意事项
(1)加工过程中,不得调整刀具和测量工件尺寸。
(2)自动加工中,自始至终监视运转状态,严禁离开机床,遇到问题及时解决,防止发生不必要的事故。
(3)定时对工件进行检验,确定刀具是否磨损等情况。
(4)关机时或交接班时对加工情况、重要数据等做好记录。
(5)机床各轴在关机时远离其参考点,或停在中间位置,使工作台重心稳定。
7.加工结束后注意事项
(1)清除切屑、擦拭机床,使机床与环境保持清洁状态。
(2)注意检查或更换磨损坏了的机床导轨上的油擦板。
(3)检查润滑油、冷却液的状态,及时添加或更换。
(4)依次关掉机床数控系统操作面板上的电源和机床总电源。
(二)数控车床的安全保障
随着科技的发展和社会的进步,数控机床技术不断发展,其功能越来越完善,性价比也越来越高,在机械行业中已得到广泛应用。而随着数控车床在企业中越来越普及,数控车床教学也在职业学校中普遍开展起来。在数控车床的学习、使用过程中,编制程序和操作加工要尽量避免碰撞安全事故的发生。
1.掌握一定的编程技巧
程序编制是数控加工至关重要的环节,提高编程技巧可以在很大程度上避免一些不必要的碰撞安全事故。
(1)编程时,对于换刀要注意留给刀具足够的空间位置(尤其是镗孔刀),要在机床上实际测量确定换刀点坐标。如遇工件较长需顶尖支撑,更应特别注意。
(2)同一条程序段中,相同指令(相同地址符)或同一组指令,前面的指令不起作用,而是执行后面出现的指令。例如:
G01 G02 X30.0 Z20.0 R10;
执行的是G02。
(3)应选择适当的加工顺序和装夹方法,以确保加工的可行性。遵循基面先行、先粗后精、先近后远、内外交叉等一般性加工原则确定加工顺序,编写加工程序。
(4)工件切槽加工,在编程时要注意进退刀点应与槽方向垂直,靠近工件阶台的进刀速度不能以“G00”速度,避免刀具与工件相撞。进退刀时尽量避免“X、Z”同时移动使用,如:进刀定位时先定Z轴,再定X轴;退刀时先退出X轴,再定位Z轴。同时,由于切槽刀刀头有两个刀尖,编程时刀尖点必须与对刀点相同,避免切槽时出现一个刀宽的误差。
(5)加工工件内孔过程中,当镗削完成时,如果需要镗刀快速退出内孔回至工件端面外X100mm、Z100mm处,用G00 X100 Z100编程,这时机床将两轴联动,则镗刀将与工件发生碰撞,造成刀具与工件损坏,严重影响机床精度。这时可采用两个程序段“G00 Z100; G00 X100”,即刀具先退至端面外Z100mm处,然后再返回X100mm处,这样便不会碰撞。
(6)G70、G73等循环指令执行后的最后一刀是从程序终点快速返回程序起点,为了避免车刀从终点快速返回起点时撞向工件,在设置起点时应注意终点与起点的连线必须在工件之外,不能跟工件的任一位置交叉,否则退刀时会出现碰撞。特别是G70精加工循环指令的起点位置更应该注意。在对指令走刀路线不熟悉的情况下,建议将G70的起点坐标设在其他粗加工循环指令的起点位置上。
(7)“G92”指令执行之后,系统默认的走刀速度是每转移动一个螺距的速度,所以“G92”程序段后面若紧跟“G01”或“G02”等指令的程序段,必须重新设置F值。不然,在高速启动主轴的情况下,系统按螺纹加工的走刀速度执行,会出现两种情况:一种是机床不动,伺服系统报警;第二种是刀具移动速度非常快(大于G00),造成撞车事故。同时,普通螺纹加工时刀具起点位置要相同,Z轴的起点、终点坐标要相同,避免乱扣和锥螺纹产生。
总之,掌握数控车床的编程技巧,不但能很好地提高加工效率、加工质量,更能避免加工中出现不必要的错误,这需要在实践中不断总结经验。
2.进行必要的程序安全检查
(1)利用计算机模拟仿真系统。随着计算机技术的发展,数控加工模拟仿真系统功能越来越完善,已能模拟数控车床编程操作的整个过程。因此可用于初步检查程序,观察刀具的运动,判断是否产生碰撞。
(2)利用数控系统自带的模拟显示功能。较为先进的数控系统都带有图形显示功能。当输入程序后,可以调用图形模拟显示功能,详细地观察刀具的运动轨迹,以便检查刀具与工件是否会出现碰撞。
(3)利用数控车床的空运行功能。利用数控车床的空运行功能可以检查走刀轨迹的正确性。当程序输入机床后,可以装上刀具或工件,并进行对刀,对刀完毕,将工件取下,然后按下空运行按钮,此时刀架按程序轨迹自动运行,此时便可以发现刀具是否有可能与工件或夹具发生碰撞。在这种情况下必须保证卡盘上没有安装工件,否则会发生碰撞。
(4)利用数控车床的锁定功能。一般的数控车床都具有锁定功能,当锁住开关为ON时,机床不运动,但位置坐标的显示和机床运动一样,并且M、S、T都能执行。当输入程序后,锁定X轴、Z轴,自动运行加工程序,通过X轴、Z轴的坐标值判断是否会发生碰撞。
3.避免错误操作
(1)操作人员对键盘功能键具体含义不熟悉,操作不熟练,对机床功能参数误修改,易造成撞车等事故。
(2)在输入刀补值时,有时“+”号输成“-”号,“1.50”输成“150”, “X”轴输成“Z”轴,“3”号刀的刀补值输在“2”号刀的位置上等。经常会出现机床启动后刀具在执行刀补时直接冲向工件及卡盘,造成工件报废、刀具损坏、机床卡盘撞毁等事故。
(3)回零或回参考点时顺序应为先X轴后Z轴方向,如果顺序不对,机床拖板就有可能和机床尾架相撞。
解决方法:操作者在没有完全弄懂数控车床功能前尽量不要修改系统功能参数,一定要弄清基本原理,严格按照操作规程进行操作,输入程序或刀补数值后应反复检查后方可操作。