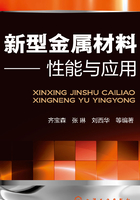
2 新型机械结构用钢——性能“强韧化”
2.1 高效节能的微合金非调质钢
2.1.1 微合金非调质钢概述
众所周知,调质是机械制造行业常用的热处理工艺,中碳钢零件的良好综合力学性能通常通过调质工艺获得。据统计,调质件数量约占热处理件总量的1/3。调质处理消耗了大量能源,对环境造成一定污染。若省略调质处理,可消除热处理造成的废品,节约材料1%~10%,节省工具费30%~40%,缩短生产周期25%~30%,节约工时10%~20%。而微合金非调质钢无淬火和高温回火工序其性能即能达到中碳调质钢的水平,同时也省去了热处理设备,简化了生产工艺并降低了能耗,使制造成本相比调质钢降低了25%~38%,具有良好的经济和社会效益,因此是一种高效节能钢。
(1)非调质机械结构钢的概念
何谓“非调质机械结构钢”?如图2-1所示为调质钢[图(b)]和非调质钢[图(a)]这两类钢典型的生产工艺流程。可见,非调质钢由于取消了淬火回火等工序,从而简化了生产工艺流程,提高材料利用率,改善零件质量,降低能耗和制造成本(25%~38%),减少污染,绿色环保。因此,通过微合金化、控制轧制(锻制)和控制冷却等强韧化方法,取消了调质处理,达到或接近调质钢力学性能的一类优质或特殊质量结构钢称为非调质机械结构钢,即微合金非调质钢,简称“非调质钢”。

图2-1 非调质钢(a)与调质钢(b)典型生产工艺流程比较
(2)微合金非调质钢的分类
①按用途分类 除表2-1所列的热锻用、冷作强化(冷锻)用非调质钢外,还有直接切削用和高韧性非调质钢等。热锻用非调质钢用于热锻件,如热锻螺栓等紧固件;冷作强化非调质钢主要用于标准件如螺栓、螺母等;直接切削用非调质钢是用热轧钢直接加工成零部件;高韧性非调质钢用于要求韧性较高的零部件。
表2-1 非调质钢按用途分类

②按化学成分分类 如表2-2所示,可分为两大类。
表2-2 几种非调质钢的化学成分

a.低碳非调质钢 此类非调质钢的碳含量一般控制在0.25%以下,即在低碳钢的基础上,加上微合金元素如V、Nb、Ti、N等。
b.中碳非调质钢 而此类非调质钢的碳含量一般控制在0.25%~0.55%之间。在此基础上加入微合金元素V、Nb、Ti、N、Al等,有的还要加上Cu、Si等。
③按显微组织分类 如表2-3所示。
表2-3 非调质结构钢按显微组织分类

a.F-P型 其在非调质钢中占据的比重最大,除满足某些特殊用途而采用其他组织为基的非调质钢外,一般非调质钢均为P-F类非调质钢。这是由其化学成分和加工状态所决定,当然也与其使用性能(状态)有关。
b.晶内铁素体(F)型 这是一种高强度高韧性的新型非调质钢。
c.低碳贝氏体(B)型 在锻后空冷状态下,可获得低碳贝氏体,借以进一步改善钢的强度、韧性和可焊性。组织中除B外,有时也夹杂有P和F,形成一种混合组织。
d.低碳马氏体(M)型 利用锻造余热进行淬火、回火,获得低碳M来增加强韧性。
④按产品形状分类 可分为:微合金非调质钢棒材、板材、管材及线材等。
⑤按新国标分类 可分为:直接切削加工用钢,其强调购进的钢材,不经任何加热、加压等处理而直接进行切削加工;热压力加工用钢。
常用非调质钢的分类及牌号表示方法如表2-4所示。
表2-4 非调质钢的分类及牌号表示方法

⑥按力学性能分类 可分为普通强度非调质钢和高强度非调质钢等。
(3)非调质机械结构钢的发展历程
1972年德国蒂森特钢公司首先研发了49MnVS3(F49MnVS)非调质钢,法国研发的含V、Nb的45Mn6等均属微合金非调质钢。以49MnVS3为代表的沉淀硬化铁素体-珠光体钢,称为第一代非调质钢。因其韧性差,只能用于受冲击负荷小的部件,限制了其应用范围。
第二代非调质钢开发于20世纪80年代初,主要有铁素体-珠光体(F-P)和贝氏体(B)型两大类,是当前用量最大的非调质钢,为提高F-P型非调质钢的韧性,开发了一系列新技术:晶粒细化法、促进晶内铁素体(IGF)形成技术、氧化物冶金技术;贝氏体(B)型非调质钢具有良好的强韧性,适合于代替合金调质钢;为改善非调质钢切削性能,各国又研制了直接切削非调质钢。
1998年美国的Wright提出第三代非调质钢概念,特点是碳含量低,组织为回火马氏体,具有较高强度和良好韧性,称为低碳马氏体型高强度高韧性非调质钢,现已在汽车、机械行业得到应用。
第一代至第三代非调质钢,使钢的综合性能得到很大提高,尤其是第二代、第三代复合微合金化非调质钢,大大拓展了非调质钢的应用范围。德国、瑞典和日本等几个国家在对非调质钢研究与应用方面取得了较好的成果。非调质钢以其性能优良、高效节能、使用成本较低,并且有利于环境保护等突出优点,在国际和国内得到大力推行,已被誉为“绿色钢材”,尤其是在汽车零件中的应用更为突出。近年来,日本在非调质钢的推广应用和新钢种、新技术的开发方面已占据世界领先地位。日本55%的轴类零件、75%的锻造结构件均已采用非调质钢制造,其中三菱汽车公司的转向系统和传动系统所用的热锻调质件几乎全部非调质化,还有丰田、住友等公司有90%的曲轴、75%连杆用非调质钢制造,如住友金属已经采用S43CV、S45CV、S50CV非调质钢制造汽车连杆。目前,日本80%以上的汽车企业都开始采用非调质钢,绝大多数企业已完全取消了热处理工厂。近几年,日本汽车用非调质钢每年用量约在200万吨,占日本汽车用特殊钢总量的64%。采用的零部件主要以汽车结构件为主,汽车底盘、部分重要传动系统、动力系统、排气系统中主要零部件都开始使用非调质钢。
我国非调质钢的研究工作始于20世纪80年代初,起步相对较晚,20多年时间已研发了十多种非调质钢,应用于汽车以及拖拉机、机床等行业,取得显著的经济成效。传统调质钢,如45、40Cr等中碳钢需经淬火和高温回火才能达到较理想的力学性能,消耗能源多,生产周期长。而非调质钢的力学性能则取决于基体显微组织和析出相的强化,不经调质处理。因此,具有节能、环保特点,可降低能耗和制造成本25%~38%。如国产V系、Mn-V系非调质钢、包括微Ti处理的非调质钢,经常规力学、工艺、疲劳断裂韧性性能测定,基本可与相同碳含量的优碳钢(35钢、45钢)及低合金钢(40Cr钢)调质态相当或接近。相关企业采用非调质钢代替调质钢生产零部件可大幅降低生产成本。非调质钢已广泛应用于汽车工业锻件、热处理件,并在工程结构、输送管线等领域得到应用。近年来随着精炼工艺、微合金化、控轧-控冷、氧化物冶金技术(晶内铁素体析出、铁素体-贝氏体及-马氏体)等技术的采用,其应用领域涉及建筑、重型机械、高压输送管道、桥梁等。
近年来,我国自行开发的铁素体-珠光体、贝氏体、低碳马氏体型等微合金非调质钢已成功应用于汽车发动机曲轴、连杆、汽车前桥等零部件。其中,一汽公司先后应用35MnVS,38MnVTi、42MnVS、40MnVS代替55钢、40MnB、45钢、40Cr钢在CA6102连杆、CAl41半轴、滑动叉、轻型车扭臂等零件进行了试验研究;二汽公司自1978年开发应用微合金非调质钢以来,已先后对东风系列汽车的20余种零件采用微合金非调质钢进行了试制,采用35MnV代替40MnB生产EQ6100发动机连杆、采用48MnV代替40Cr生产康明斯发动机曲轴等,部分已实现大批量生产。另外,江铃汽车、南京汽车、天津汽车等汽车制造厂的微合金非调质钢用量也逐年大幅度增加。从用材工艺技术分析,在汽车车身、变速箱总成、驱动桥总成、悬挂减震器、离合器部件、转向系统及零件中有15%的钢结构零件可用微合金非调质钢代替。目前,我国非调质钢的年用量约100万吨。
现阶段国内非调质钢还存在性能不稳定、韧性较低、材料成本较高等缺点。如何获得高强度与高韧性相匹配的非调质钢是国内外科技工作者研究的热点课题。
2.1.2 微合金非调质钢的特点
(1)强韧化特点
①优化成分,提高强韧性
a.“降C增Mn”在一定范围内,钢的强度随着碳含量的增加而提高,但碳含量的增加在提高强度的同时也降低了钢的韧性。因此,降C可明显提高钢的韧性,其强度损失可由增加Mn含量补偿,同时通过细晶强化、沉淀强化和固溶强化进一步提高强度。
b.“多元适量,复合加入”的合金化基本原则 微合金化元素V、Ti、Nb和N等,以细晶强化和沉淀强化等方式同时提高材料的强度和韧性。但最常用的是V,通常V的质量分数在0.06%~0.13%;N是十分有益的元素,N以化合物的形式存在,其主要作用是促进V的析出,提高沉淀析出强化效果,细化晶粒,提高TiN的稳定性用和节约V合金等。S可细化晶粒,促进晶内F析出,提高强韧性,同时也可改善切削加工工艺性能。
c.均含有一定量Mn元素 含0.60%~1.00%或1.00%~1.50%的Mn(因>1.5%时,将降低其韧性)。Mn、Cr以固溶强化方式强化基体组织,提高淬透性,增加钢的强韧性。
②晶粒细化法 常加入Al、Ti等,通过析出AlN、TiN等来钉扎奥氏体晶界,在加热时起到阻止晶粒长大的作用;细化晶粒。如用Ti-V复合合金化,控制晶粒尺寸更好。
③沉淀强化法 微合金元素(如Nb、Ti、V和N等)在钢中除细化晶粒外,还有很强的沉淀强化作用,取决于这些合金化合物在奥氏体中的固溶度、沉淀析出速度及沉淀析出物的数量、尺寸和分布等。
④正火、回火 正火和回火是非调质钢常用的强韧化工艺,用以调整轧件或锻件的力学性能。正火、回火工艺比较简单、操作方便,对提高(调整)非调质钢零件的强韧性有事半功倍的效果。通过选择不同的化学成分和相应的轧制(锻造)工艺,非调质钢可达与经调质处理的碳钢及合金结构钢相当的强度。虽其韧性稍差,但在采取某些韧化措施后,也可达到较高的韧性水平。
正火可使中碳非调质钢的显微组织进一步细化,改变F-P的组织形态,有效地提高钢的冲击韧度,最大限度地改善非调质钢的性能。表2-5列出了0.46C-1.04Mn-0.084V(质量分数,%)非调质钢不同状态的力学性能,图2-2是不同状态的显微组织。
表2-5 0.46C-1.04Mn-0.084V非调质钢的力学性能


图2-2 0.46C-1.04Mn-0.084V非调质钢不同状态的显微组织
回火一般用于贝氏体非调质钢。具有优良韧性的贝氏体型非调质钢可通过回火进一步显著提高韧性。表2-6系12Mn2VB贝氏体非调质钢锻态及锻后经中温回火后的力学性能。表2-7为0.28C-1.9Mn-1.2Ni-0.15V(质量分数,%)贝氏体(B)非调质钢热轧件及热轧后经220℃回火的力学性能,图2-3是其回火后的显微组织。
表2-6 12Mn2VB贝氏体非调质钢回火后的力学性能

表2-7 0.28C-1.9Mn-1.2Ni-0.15V贝氏体型非调质钢的力学性能


图2-3 贝氏体非调质钢热轧后经220℃回火后的显微组织
⑤促进晶内铁素体(IGF)组织的形成 非调质钢锻件在冷却过程产生相变时,铁素体沿奥氏体晶界析出呈网状分布,损害钢的韧性。现在通过控制冶金工艺(如先进的TMCP技术),在奥氏体晶内提供大量铁素体形核位置,使其不仅在晶界,而且在晶内析出,分割奥氏体从而形成细小、均匀的等轴铁素体组织,能显著改善钢的韧性。
如图2-4所示,螺栓用钢的细晶强化可通过TMCP技术,轧后施以适当冷却工艺,获得细晶F+P组织,从而达最佳强韧性配合,对MFT8非调质钢采用TMCP工艺,其组织以细化F+P为主,F的晶粒度13级,平均晶粒直径5μm左右。

图2-4 非调质钢MFT8组织结构的SEM图
⑥非调质钢的表面强化 与调质钢制零件相同,许多非调质钢零件也可进行表面强化以满足使用要求。
a.感应淬火 图2-5是几种非调质钢的感应淬火(250kHz)后的硬度分布曲线。

图2-5 几种非调质钢感应淬火后的截面硬度分布曲线
b.氮碳共渗 几种非调质钢及42CrMo钢经10h气体氮碳共渗后的结果见表2-8。非调质钢的氮碳共渗化合物层较薄而扩散层较厚。
表2-8 非调质钢及42CrMo钢经10h气体氮碳共渗后的表面硬度和渗层厚度

c.离子渗氮 40MnSiV、48MnV、38MnVS6、12Mn2BV非调质钢经540℃×8h离子渗氮后的结果见表2-9。
表2-9 非调质钢的离子渗氮效果

d.激光淬火 38MnVS6、48MnV、40MnSiV非调质钢圆柱试样激光淬火后表面硬度及淬硬层深度见表2-10。激光淬火设备为带控温装置的半导体激光器,加热温度1200℃。
表2-10 非调质钢激光淬火后的表面硬度和淬硬层深度

(2)成分与组织特征
①珠光体(P)-铁素体(F)型非调质钢 其碳含量一般为0.3%~0.5%,又称中碳非调质钢。其组织主要是:F+P或F+P+弥散析出的碳化物K。图2-6为化学成分(质量分数,%)为0.37C、0.22Si、1.43Mn、0.048S的F-P型非调质钢的轧后空冷组织。由图中可看出,F呈网状,F的形态取决于碳和微合金元素的含量、形成温度、时间和晶粒尺寸等。强化的主要作用是细化组织和相间沉淀析出。其典型钢种是49MnVS3,其σb>770MPa,σs>540MPa,室温U形缺口冲击吸收功AK>31J。

图2-6 某F-P型非调质钢的显微组织
②贝氏体(B)型非调质钢 亦称低碳贝氏体非调质钢。其显微组织有2种,B或B+少量(F+P)。该类钢的特点是不但有高强度,而且有较好韧性,σb≥830MPa,σs≥540MPa,室温U形缺口AK>47J。
③马氏体型非调质钢 低碳马氏体非调质钢的组织为板条状马氏体,具有更优良的强韧性匹配、高的疲劳强度以及异常好的韧性,强韧性达优质调质钢的水平,-30℃时的韧性是第二类钢的5~6倍,-60℃时的AK>16J。
这三类非调质钢也可被认为是非调质钢发展的三个阶段。
(3)冶金工艺特点
①冶炼 冶炼非调质钢时,均要首先充分脱氧,然后再进行合金化。保证钢中含有稳定和适量的N,对控制微合金非调质钢的性能是十分重要的。非调质钢在冶炼时常加入Al、Ti等元素,通过析出AlN、TiN来钉扎奥氏体晶界,提高奥氏体晶粒长大激活能量,在加热时阻止晶粒长大,在形变过程中抑制奥氏体再结晶,细化晶粒。微合金元素的复合加入比单独加入作用更大。
a.窄成分范围和成分偏析的稳定控制技术 非调质钢因其省略调质热处理工序,对钢的化学成分及成分偏析控制有很高的要求。化学成分微小波动就会使非调质钢的微观组织产生较大的变化,从而影响锻件性能的稳定性和零件服役的安全性。早期的非调质钢主要釆用电炉流程(电炉→炉外精炼→连铸→控轧控冷)生产,近年来为进一步降低成本而逐渐采用转炉流程(转炉→炉外精炼→连铸→控轧控冷)生产非调质钢。但采用转炉冶炼由于周期短(约30min)而增大了成分精确控制的难度;另外,由于出钢下渣量大,精炼十分困难。对此,通过选用精料、稳定出钢量、优化脱氧方式、规范过程准确取样和成分调整规范等方法以及低过热度浇注、电磁搅拌及优化连铸工艺参数等全系统的精确控制技术,在困扰多年的非调质钢窄成分范围和成分偏析的稳定控制技术方面取得重要进展。大量的生产统计数据表明,成分波动范围显著收窄(降低幅度在30%以上),达到了国外同类产品的先进水平(表2-11)。此外,对于含氮非调质钢,开发出一种直接采用氮气部分取代氩气底吹的工艺,可以在满足氮含量稳定控制及对洁净度的要求条件下,以较低的成本增加钢液中的氮含量。
表2-11 非调质钢窄成分和偏析控制效果(近千炉次的统计结果)

b.硫化物细化和均匀分布技术 为改善非调质钢的切削加工性能,钢中通常要求加入较高含量的硫(一般质量分数为0.04%~0.06%)并形成细小且均匀分布的硫化物。对此,国内外开展了硫化物细小及均匀分布技术的大量研究。然而,为保证非调质钢零部件的服役寿命,对钢材的洁净度提出了越来越严格要求。为此,开发出含硫非调质钢的新型脱氧工艺、增硫技术和硫含量稳定控制技术,并通过降低浇注过热度、加大坯材压缩比及优化控轧工艺等措施,获得了细小且均匀分布的硫化物,从而保证了含硫非调质钢具有较低的硫化物级别和高的洁净度,如硫质量分数0.04%~0.06%的非调质钢棒材中的硫化物夹杂级别由原3.5~4.5级降低到2.5~3.0级,硫化物长宽比低(约2)且分布较均匀,达到国外同类进口材料的水平(图2-7和表2-12)。

图2-7 非调质钢棒材中硫化物夹杂长宽比统计结果(C70S6钢)
表2-12 C70S6钢棒材的硫化物夹杂统计结果

②先进的TMCP技术 微合金化与TMCP相结合,才能充分发挥微合金化元素的作用,从而达到最佳的强韧化效果。对于轧制(锻制)并经切削加工后使用的非调质钢来说,轧制(锻制)工艺将决定零件的最终性能。制定合适的锻造工艺,如锻造加热温度、始锻温度、终锻温度、锻造比(变形量)、冷却速度(冷却方式)等,以使锻坯力学性能符合零件的使用要求。图2-8系成分为0.37C-0.048S-1.43Mn-0.080V(质量分数,%)非调质钢加热至不同温度快速冷却后的显微组织及其数量,它突出显示了热加工工艺(加热温度)的影响,即随加热温度的提高,所获得的组织由细小变为粗大。

图2-8 非调质钢(0.37C-0.048S-1.43Mn-0.080V)加热至不同温度快速冷却后的显微组织
(4)性能特点
①力学性能 具有与碳素及合金结构钢调质后同样强度。虽其韧性稍差,但采取某些韧化措施后,也可达到相应韧性水平。与调质态使用的机械结构钢相比,微合金非调质钢对尺寸(体积)效应不敏感,使其力学性能尤其硬度值在零件截面上分布较均匀,这一点对大型零、部件尤为可贵和重要。表2-13列出了常用非调质钢的力学性能及其应用。
表2-13 非调质钢的力学性能及其应用

②工艺性能 良好的切削加工性能。在硬度相同情况下,具有F-P组织的非调质钢,其切削加工性能比具有回火S组织的调质钢好。为进一步改善非调质钢的切削加工性,可适量单独添加某易切削元素如S或Pb及Ca、Te(碲)、Se(硒)等,或复合添加这些元素。
③良好的表面强化特性 如前所述,非调质钢具有良好的表面强化特性。为提高其表面耐磨性和疲劳强度,都进行表面强化处理。其具有良好高、中频感应加热淬火特性;与同等强度级别调质钢相比,在同样氮化和软氮化工艺条件下,非调质钢的渗层可得到更高硬度、更深渗层深度,氮化处理后心部硬度也不降低等。
(5)技术经济性能特点
表2-14列出了非调质钢与调质钢零件的大致制造工艺流程比较。可以看出,采用非调质钢制造零件,与调质钢相比,最大的不同就是省去了热处理工序。对于冷拉成形非调质钢,不但省去调质处理,还省去了退火处理。因此,非调质钢的技术经济性能特点可归纳为以下几点。
表2-14 非调质钢与调质钢零件的制造工艺流程比较

①非调质钢的规格(尺寸)效应较小,其强度和硬度沿零件截面的分布较为均匀,提高了零件的整体强度。
②避免了调质过程中因工件畸变、开裂而产生废品的风险,提高了成品率。
③减少了高能耗的热处理工序,节能减排。
④缩短生产周期,提高劳动生产率,节约生产管理费用,即降低制造成本,提高企业的效益。
⑤良好的切削性能和表面强化性能。
2.1.3 典型新型非调质钢品种的研发应用实例
(1)大杆径汽车半轴用高强度中碳非调质钢
传统大杆径载重商用车半轴采用调质钢42CrMo等生产,包括热锻成形、调质处理和感应淬火等工序。为降低热处理成本特别是减少淬火变形,开发出一种大杆径轴类用、适应表面感应淬火的高强度中碳非调质钢FAS2340(Mn-Cr-V-B系)。该钢的各项性能指标与日本生产的同级别材料相当,材料疲劳性能接近调质钢(表2-15)。特别是半轴经表面感应淬火处理后,具有独特的微观组织特征和疲劳性能,静扭转疲劳寿命较调质钢42CrMoH提高了100%以上,可代替42CrMoH钢用于制造52~62mm的大杆径重载商用车汽车半轴,已定型批量应用。
表2-15 汽车半轴用高强度中碳非调质钢的力学性能

(2)胀断连杆用高性能中碳非调质钢
目前普遍采用的高碳钢C70S6(欧美目前普遍釆用的胀断连杆用钢是在0.70%碳钢基础上开发的C70S6,其成分特点是低硅、低锰、添加微合金元素V和易切元素S,合金元素范围很窄,洁净度要求严格)虽易发生脆性裂解,适合采用胀断工艺来生产连杆,但仍存在如屈强比偏低、疲劳性能比相同强度水平的调质钢低、较多高硬度脆性片层状渗碳体使钢的切削加工性能较差等明显缺点。因此,国际上开展了改善传统胀断连杆用钢性能的研究,其主要思路是:降低传统高碳钢C70S6的碳含量,以复相的F+P组织代替较单一P组织。然而,传统F+P组织中,F的韧性和塑性较好,缺口根部的F区域容易发生延性断裂,胀断性能很差。
在吸收上述两类非调质钢优点的基础上,通过在中碳钢中复合添加B与P元素而适度增加钢的脆性和降低塑性,开发出一种新型的综合性能优异的胀断连杆用中碳非调质钢ADVANS850FS。该钢不但具有较高的强度水平和屈强比,同时具有远高于C70S6钢的高周疲劳性能(图2-9和表2-16)。此外,模拟实际胀断试验结果表明(图2-10),传统连杆用非调质钢F38MnVS不仅硬度低,而且试样胀断前后的变形量很大,不适宜应用胀断技术制造连杆;开发钢的断口断面平整,断口边沿无剪切唇,呈典型的脆性解理断裂,胀断前后的变形量很小,具有优于C70S6钢的胀断性能,可采用胀断工艺制造对疲劳性能等要求较高的汽车发动机连杆。

图2-9 开发钢ADVANS850FS与传统胀断连杆用钢C70S6的旋转弯曲疲劳试验S-N曲线
表2-16 胀断连杆用高性能中碳非调质钢的力学性能


图2-10 3种非调质钢模拟胀断试样胀断前后大圆孔直径(变形)的变化值的比较
(3)少(无)微合金化,低成本、高品质非调质钢
传统的非调质钢中往往需添加昂贵的V和Nb等微合金元素,为进一步提高非调质钢的技术经济性,近年来国内外开始了少添加或不添加微合金元素的新型低成本非调质钢的研发工作。途径之一是运用组织细化的思路,使碳素结构钢的强度达到微合金非调质钢的强度水平,这样就有可能以碳素非调质钢替代微合金非调质钢。
此外,合理运用Mn、N和Ti等元素应是一未来的发展方向,例如,通过增加N含量提高V的微合金析出强化作用,可起到降低钢中V含量效果;利用Ti的TiN析出控制高温奥氏体晶粒状态,优化Si和Mn含量调整相变动力学,为在少无微合金化非调质钢中获得细小F+P组织提供条件。这种在对合金体系进行系统热力学和动力学分析的基础上,结合现代先进的冶金工艺流程和控轧(锻)技术,利用上述思路开发的一种少无微合金化元素的低成本非调质钢ADVANS800F的轧材和试制汽车锻件的力学性能见表2-17和表2-18。该钢的疲劳性能[疲劳强度与抗拉强度的比值(σ-1/Rm=0.49)]达到了调质钢的水平(σ-1/Rm=0.50),但与V微合金化非调质钢(σ-1/Rm=0.55)仍有一定程度的差距,有待改善。该钢可替代部分含钒非调质钢和40Cr等调质钢来制造部分汽车用锻件。
表2-17 低成本非调质钢ADVANS800F的热轧态力学性能

①正火样品依据GB/T15712—2008。
表2-18 低成本非调质钢ADVANS800F试制汽车锻件的力学性能

(4)非调质钢长疲劳寿命化技术
国内外非调质钢研发工作的侧重点大多是研究进一步提高其强度和改善韧性。然而,由于非调质钢制零件如曲轴和连杆等是在交变应力状况下长时间运转,容易产生疲劳断裂,故提高非调质钢的疲劳性能十分重要。
F-P型非调质钢由于存在F软相,其疲劳裂纹基本上萌生于试样表面的F/P边界,并优先沿着F/P边界扩展,因而强化F、改善F的分布状态和组织均匀化是改善此类钢疲劳性能的关键。对微合金元素V的研究结果则证实了上述思路的正确性。V元素主要通过析出强化和组织细化的机制来改善F-P型非调质钢的疲劳性能。即在热锻态,V(C,N)呈细小弥散分布,且与铁素体间具有特定位向关系,具有明显的析出强化和细化组织作用,铁素体的强化使得疲劳裂纹萌生和扩展的抗力提高,因而38MnVS钢的疲劳性能明显优于38MnS钢;V含量更高的22MnVS钢则具有特别优异的疲劳性能(疲劳极限比高达0.60)。
由此可见,F-P型非调质钢的强度及疲劳极限均明显高于碳素钢正火态的水平,而与碳索钢调质态的水平相当,甚至部分达到了合金结构钢调质态的水平。这表明组织精细控制的F-P型非调质钢的疲劳性能达到了调质钢的水平,可用来代替中碳调质钢制造曲轴、连杆、半轴等汽车运动部件。
(5)高强高韧贝氏体型非调质钢
目前,应用最成功的F-P型非调质钢的抗拉强度低于1000MPa,并且韧性偏低,难以满足汽车轻量化对钢材强韧性的更高要求,因而多用来制造曲轴、连杆等对韧性要求相对较低的部件。因此,设计开发出一种新型的1000MPa级高强高韧贝氏体型非调质钢FAS2225(Mn-Cr-V系),可用来替代传统的Cr及Cr-Mo型调质钢制造汽车前轴等对强度和韧性要求更高的零件。该钢采用较高的Mn含量以获得粒状贝氏体组织(如图2-11所示),从而避免Mo等贵重金属的应用,同时添加适量微合金化元素V来改善钢的强韧性。应用结果表明,该钢具有良好的强韧性配合,同时具有优异的疲劳性能,各项性能指标均达到载重汽车的设计要求,与日本进口的同类调质钢性能相当(表2-19),并且与传统调质钢(45,42CrMo)及非调质钢(16Mn2VB,32SiMnVTiS)等相比,采用该钢生产的汽车前轴的疲劳寿命最高。目前已采用该钢批量生产载重汽车前轴。

图2-11 FAS2225钢的粒状贝氏体组织(热状态)
表2-19 汽车前轴用高强高韧贝氏体型非调质钢的力学性能

研究表明,在同样的碳当量下,贝氏体钢的抗拉强度比F-P钢高200MPa以上,具有明显的优势。安赛乐公司开发的中碳Mn-Si-Cr系空冷贝氏体钢在实验室获得的最佳性能为抗拉强度1150MPa,伸长率20%。韩国浦项制铁公司开发的低成本的空冷微合金化低碳贝氏体钢(0.15%C-1.8% Mn-0.002%B)的抗拉强度为825MPa,伸长率11.1%,完全满足汽车转向节拉杆的技术要求。在汽车产业很发达的日本,贝氏体非调质钢的应用是很常见的。日本新日铁公司研制的贝氏体非调质钢,添加较多的微合金元素,使钢在很宽的冷却速度范围内获得贝氏体组织,且冷却速度越慢,可获得的低温性能越好,适用于要求强度高、韧性好的汽车行走系部件。我国使用贝氏体钢制作的各种车辆、机车、农机等机械的各类弹簧与常用的弹簧钢相比,也具有更长的使用寿命和更高的安全性。而且利用贝氏体钢制作的车辆前桥、转向臂、弯直臂等已在一汽、东风和中国重汽等厂家生产使用,性能稳定。
在工程机械使用到齿板、冲击锤、衬板、护钩、护甲等机械构件的冶金、电力、矿山、化工和建材等行业,仅中国一年的消耗量就达到100万吨以上。在工件磨损方面,我国每年经济损失高达约400亿元人民币。在以上这些领域,由于此类工具都承受着较大的冲击力,因此对钢要求要有好的强韧性配合。例如,我国矿山机械上使用的贝氏体+马氏体复相组织的磨球,其表面硬度达56~62(HRC),心部达54~57(HRC),冲击韧度达到17J/cm2;矿山掘进机和采煤运输机上大量使用的刮板等也为贝氏体钢,硬度为40(HRC),冲击韧度40J/cm2。表2-20归纳总结了可用非调质钢制造的工程机械零部件。
表2-20 可用非调质钢制造的工程机械零部件汇总

超低碳贝氏体非调质钢具有较好的低温焊接性能和高的强韧性配合,常应用在海洋设备、舰艇和运输船上。超低碳贝氏体非调质钢在海洋领域的应用,美国和日本走在世界前列。20世纪,宝钢和武钢已经开发出了该钢种的Cu2Nb2BT系和Mn2Nb2B系非调质钢,随后鞍钢和上钢三厂也相继开发出了此类型的不同型号的钢种。
非调质钢最常见同时用量最多的要数铁路行业。采用贝氏体非调质钢所生产的火车车轮比用常见钢种CL60的强度提高13%,塑性变形能力提高23%,冲击韧度也提高近3倍,因此大大提高了车轮的抗剥离性能。为达到铁轨等铁路设备对钢的高强度、高韧性和高耐磨性的要求,实际用钢一般采用高锰钢,但使用中仍然会出现各种问题。贝氏体非调质钢以其1300MPa的抗拉强度、90J/cm2的冲击韧度和达到20%的断面收缩率使得铁路设备的使用寿命明显提高。
贝氏体非调质钢的优越性能同样也受到石油业的关注。非调质钢的运用使得石油采集和输送过程成本显著降低。日本钢铁公司开发的X70和X80贝氏体钢,屈服强度高于500MPa,脆性转变温度也能够达到零下80℃,并且成本低廉,使用寿命可提高好几倍。唐山钢铁公司也研制出了工艺简单且达到国标GB7229要求的非调质钢FG20。
非调质钢在模具方面也有较大的应用潜力。过去模具钢通常采用45钢、40Cr钢和Cr12MoV钢等,但所生产的模具加工性能和耐磨性差、表面粗糙度高、热处理困难,并且产品外观质量较差。而贝氏体非调质钢可不经过热处理并且性能优越,因此在模具领域具有广阔的应用前景。
(6)钒(V)-铌(Nb)微合金化非调质钢
采用V-Nb微合金化通过微细碳氮化V(Nb)(C,N)的沉淀强化提高钢材热轧态或锻造态的强度水平,是F-P型非调质钢最重要的强化机制。国外已经研制开发生产了大量的V-Nb复合微合金化的非调质钢,在汽车零件的使用率已达60%以上。我国多年来也研发了以V微合金化为主的20余个非调质钢种,用于生产汽车曲轴、连杆、半轴等零件,取得了良好的效果,但由于各方面的原因,至2012年的生产使用量仅为10万吨。
近年来,Nb对珠光体相变的抑制作用受到重视,Nb-V复合微合金化的非调质钢不仅强度水平比V微合金化的非调质钢明显提高,而且由于渗碳体片层间距细化及展弦比的降低,钢材组织形貌更接近于调质状态,从而具有更高的塑韧性。深入研究Nb对珠光体相变的影响规律,使钢材在热轧态或锻造态不仅获得调质态的强度水平,也得到更为接近调质态的组织,是F-P型非调质钢未来发展的重要方向。目前,世界上先进国家研发生产了大量V-Nb复合微合金化的非调质钢,在汽车零件的使用率已达60%以上,在工程机械等领域也获得重要的应用。
例如研究Nb-V复合非调质钢在不同锻造工艺下的组织变化规律,其结果表明:①相对于单独添加V的非调质钢,Nb-V复合非调质钢锻后晶粒细小,F含量增多、呈块状均匀分布,P片层间距减小、且片层分布不规则,如图2-12所示,可改善钢的组织韧性;②如图2-13所示,可看出降低冷却速度有利于先共析F长大,促使网状F向块状F转变,分布更均匀,有利于非调质钢韧性的改善,增大锻后变形量,可使组织细化。

图2-12 850℃变形10%条件下试验钢的显微组织

图2-13 不同变形量下Nb-V复合试验钢的显微组织
总之,近年来随着计算机、控制、传感及精密测量技术等当代高科技与传统钢铁、制造业的结合,微合金钢的开发应用获得新进展,除汽车工业外,应用范围涉及建材、重型工程结构(起重机、载重车辆)、高压输送管道、桥梁、高压容器、集装箱、船舶等。而这些用途钢材一般占社会对钢材总需求量的60%左右。所以非调质钢应用前景广阔,是现代钢铁工业中的主力产品之一。
2.1.4 微合金非调质钢的发展方向
不断提高非调质钢的强韧性,是各国非调质钢研发人员多年来共同追求的目标,并贯穿于整个非调质钢的发展过程之中。为进一步提高非调质钢的技术经济性,非调质钢正向低成本化、化学成分控制高精度与尺寸控制高精度的方向发展。
现国内已成功开发出大功率发动机曲轴用48MnV和连杆用40MnV、35MnVS等非调质钢等,各大型钢厂正在针对非调质钢的韧性改善进行研发,主要冶金措施有氧化物冶金、硫化物冶金、晶内铁素体化等,目的是促进晶粒细化和改善韧性。随着我国市场经济体制的不断完善,有显著节能和环保效果的非调质钢一定能在机械制造行业得到较快发展,并将逐步扩展到其他领域。
综上所述,微合金非调质钢(简称非调质钢)是一种高效节能钢,经热锻或热轧后其力学性能即达到中碳调质钢的水平,省去了淬火、高温回火工序,因而也省去了热处理设备,简化了生产工艺,降低了能耗,提高了材料利用率,改善了零件质量,降低了制造成本25%~38%,具有良好的经济效益和社会效益。