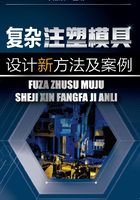
2.4 注塑模最终结构方案与注塑件上缺陷痕迹综合整治技术
注塑件在成型加工的过程中,除了会出现注塑模结构成型痕迹之外,还会产生注塑件成型加工痕迹,即缺陷痕迹或弊病痕迹。注塑件上缺陷痕迹是不允许出现的痕迹,因为注塑件上缺陷痕迹不仅会影响制品的美观性;也会影响到注塑件力学性能和非力学性能;还会影响到注塑件的机械性能、化学性能、电性能和光学性能以及其他的性能;更会影响到注塑件的强度和刚性,进而影响注塑件的使用性能。存有缺陷痕迹的注塑件被视为废品,所以存有注塑件上缺陷痕迹制品的模具,要通过缺陷整治达到注塑件合格后才能判断模具的合格。换句话说存在注塑件上缺陷痕迹的制品,注塑模也被视为待合格模具。所以,只有通过试模加工出合格的制品,才能确定模具的合格。
造成注塑件上缺陷痕迹的原因有很多,最为关键的是要排除因模具结构不当所产生的注塑件上的缺陷痕迹。注塑件上出现的缺陷存在着多种形式,整治起来十分困难。有时整治好了这个缺陷,另外又冒出其他的缺陷。还有些缺陷可以称作是顽症,在反复试模与修理模具之中,就是得不到有效的根治,甚至就是模具多次重新制造仍然整治无效。因此,因模具结构的不当会造成模具的返修和报废,模具的返修和报废会造成模具交付日期的延误和经济上的损失。
在制订注塑模结构可行性方案时,一定要考虑到注塑件上缺陷痕迹预期分析的结果,这便是注塑模最终结构方案的可行性分析。要将注塑件上缺陷痕迹消灭在注塑模方案可行性分析阶段,确保注塑模结构方案不存在因模具结构不当产生注塑件上的缺陷痕迹。对于非注塑模结构缺陷痕迹,通过试模找出产生的原因之后,便能很容易地达到根治缺陷的目的,这样便于注塑模结构方案与模具结构缺陷痕迹得到统一的解决。这就是注塑件上缺陷痕迹以预防为主、整治为辅的策略。
注塑件成型的目的,不外乎是要确保注塑件的形状、尺寸和精度的合格;确保注塑件的性能符合使用的要求;确保注塑件不出现次品和废品。前者主要是依靠模具结构和制造精度来保证,中间主要是依靠高分子材料的性能和质量及加工来保证,而后者主要是依靠注塑件缺陷的综合整治来保证。不管是热塑性塑料还是热固性塑料,也不管是注射成型还是压塑成型。注塑件和压塑件在成型的过程中,都会存在着各种各样的缺陷(弊病),这是不争的事实,这也不是以个人客观的意志所转移的。注塑件上的缺陷综合整治技术,就是应用辩证方法论来综合整治塑料件上缺陷的一种理论。
2.4.1 注塑件上缺陷痕迹的识别与分析
注塑件上缺陷痕迹,可以根据注塑件上缺陷的痕迹进行识别,有如医生对病症的诊断。如果有缺陷痕迹规范文本(行业标准),可以通过实物比对文本的图片和说明进行分辨;也可以根据实际经验进行分辨。注塑件上的缺陷痕迹除了小部分是隐藏在注塑件内部或是以应力分布的形式,用眼睛观察不到,大部分的缺陷痕迹都显现在注塑件的表面上,是很容易被观察到的。但是,要整治这些缺陷痕迹确实不太容易。在整治这些缺陷痕迹之前,必须对这些缺陷痕迹的产生原因进行详细的分析,再找到产生缺陷痕迹的真正原因后才能够确定整治的措施。
2.4.2 注塑件上缺陷痕迹的综合论治
注塑件上产生缺陷的因素有多种,能够迅速而准确地找到缺陷产生的原因,并制订出整治的措施,就是我们必须要做的事情。因此,寻找这种治理注塑件上缺陷的方法就显得特别重要。整治注塑件上的缺陷是个涉及多门学科和多种技术的综合性技术,而缺陷产生原因的分析及整治方法,更是属于一种科学的辩证方法。只有将缺陷产生与整治的因果关系科学地处理好了之后,才会有完善的缺陷痕迹处治成果。有了注塑件缺陷的综合辨证论治的理论,便可以对缺陷的形成有清晰的认识,这样就为后面的注塑件缺陷的综合辨证施治创造有利的条件。
整治注塑件上的缺陷(弊病)有如医生治疗人的疾病一样,疾病产生的病因和治疗的机理存在着多套的辨证治疗的理论。成型件有注塑件、压塑件、压铸件和铸锻件等多种的形式,同样它们生成的缺陷和整治也存在着多套的辨证整治理论。因为对应有成型加工缺陷便存在着对应形成的因素,而对应有产生的因素就有对应的整治措施,这样整治注塑件上缺陷(弊病)就需要我们用辨证的方法科学地去根治。
2.4.3 注塑件缺陷综合整治方法的分类
注塑件缺陷的综合辨证论治和辨证施治,存在着先期预防和后期整治两种方法。先期预防是在试模之前,或者说是在制订模具结构方案的同时,甚至是在注塑件设计的同时,就需要预先对注塑件缺陷进行预期分析。这样才可以有效地避免模具结构设计的失败,这是一种主动的整治方法。后期注塑件缺陷的整治,是指在试模时对所发现的注塑件上的缺陷进行再整治。这种方法不能够有效避免模具结构设计的失败,是一种被动的整治方法。
注塑件缺陷预期分析可分成两种:一种是注塑模计算机辅助工程分析(CAE)对注塑件缺陷的预期分析方法,简称CAE法;另一种是注塑件缺陷图解预期分析的方法,简称图解法。注塑件缺陷的整治是在注塑件试模之后,对形成的缺陷进行整治的方法。注塑件缺陷的整治也有两种方法:一种是排查法或排除法,另一种是痕迹法。不管是CAE法和图解法,还是排查法和痕迹法,都需要具有丰富的缺陷分析和整治的经验。
注塑件上的缺陷预期分析方法和试模之后的缺陷整治方法,统称为注塑件缺陷综合辨证整治的方法,可称为注塑件缺陷综合辨证论治,简称为缺陷综合论治。缺陷综合辨证整治法由CAE法、图解法、排查法和痕迹法组成,这样就可以形成系统而全面整治缺陷的方法。
CAE法和图解法,主要是针对注塑件或成型件进行缺陷的预测分析,通过预测分析预先去除注塑件因模具结构产生的缺陷,进而根据分析的结论改进注塑件的结构,并还能影响到模具浇注系统的形式、尺寸、位置和数量以及模具结构方案的制订。
(1)CAE法
注塑模计算机辅助工程分析(CAE)方法,简称CAE法。CAE法是通过计算机利用已有的注塑件三维造型,对熔体注射的流动过程进行模拟操作。该法可以很直观地模拟出注射时实际熔体的动态填充、保压和冷却的过程,并定量给出注塑件成型过程中的压力、温度和流速等参数,进而为修改注塑件和模具结构设计以及设置成型工艺参数提供科学的依据。
CAE法可以确定模具浇口和浇道的尺寸和位置,冷却管道的尺寸、布置和连接方式。还可以通过反复变换分型面的形式和浇注系统的形式、尺寸、位置和数量,得到不同的熔体流动和充模效果,从而找出对应模具的结构。也可以预测注射后注塑件可能出现的翘曲变形、熔接痕、气泡和应力集中的位置等潜在缺陷,并代替部分试模工作。
该种方法存在着某些不足和局限性,并且不能主动调整注塑件在模具中的位置、分型面形式和浇注系统形式、尺寸、位置和数量,需要人为地进行调整。此外该技术还在不断地完善之中。但是,只要掌握了操作方法,其运作很简单,当然还需要有一定缺陷分析的具体经验。注塑模计算机辅助工程分析(CAE)方法,目前只能够运用在注塑件翘曲变形、熔接痕、气泡和应力集中的位置的分析。对于其他类型的缺陷和成型工艺方法,目前的软件还不能进行分析。现今开发的该类软件较多,使用者应根据自己的条件适当地进行选择。
(2)图解法
注塑件缺陷痕迹图解分析法,简称图解法。注塑件缺陷预期分析图解法是在绘制了注塑件2D零件图的基础上,根据浇口形式、尺寸、位置和数量,绘制出熔体料流充模和排气的路线、熔体流量和流速分布图以及熔体汇合图、内应力和温度的分布图。据此可以分析出缺陷形成的形式、特征和位置的一种方法,被称为图解法。该法可以进行塑料温度分布预期分析、塑料收缩的预期分析、排气时气体流动状态预期分析、内应力分布的预期分析,从而可以进行各种缺陷的预期分析。对外露的缺陷痕迹应绘制注塑件的缺陷痕迹分析图,而对注塑件内部的缺陷痕迹应采用解剖的方法或进行X光透视的方法,并绘制注塑件内部的缺陷痕迹分析图来进行分析。
图解法原理与CAE法相同,区别只是运用了2D图形进行缺陷的分析。CAE法不能进行分析的缺陷和成型加工方法,图解法都能进行有效的分析,当然,CAE法能分析的缺陷,图解法也能进行有效的分析。故其分析范围宽、不受程序和软件的限制、分析方法灵活,但需要丰富的分析经验。CAE分析方法和图解分析法两者相结合,才是很好的缺陷预案分析方法。缺陷预期图解分析法,可以运用在注塑件、压塑件、压铸件及所有型腔模成型的成型件缺陷分析中,还可以分析成型件所有的缺陷。该法为新创的方法,还有待于推广和开发,只不过没有运用到计算机进行编程而已。
(3)排查法
缺陷排查法或排除法是先制订出影响缺陷产生的各种因素,然后用排查的方式,一项一项地梳理产生缺陷的因素,最终找出真正产生缺陷的原因的一种方法,简称排查法或称排除法。因为影响注塑件产生的缺陷因素是多种的,可以通过缺陷的排查法,逐步清除掉不会影响缺陷产生的因素,留下的便是产生影响缺陷的因素。排除过程中为了提高效率,可以采用优选法进行,再通过对比的方法,找出真正产生缺陷的因素,从而确定整治缺陷的措施。这种方法是应用一项一项地排查和试模,再排查再试模的方法。其效果缓慢、过程长、对经济和试模周期会产生不良的影响。具体排除过程是根据对注塑件上所出现的缺陷,先列出可能产生缺陷的所有原因,然后再对原因逐项排查。
(4)痕迹法
缺陷痕迹法是利用注塑件上的缺陷痕迹,再通过注塑成型痕迹技术的切入直接找出产生缺陷原因的一种方法,简称痕迹法。俗话说得好:“事出有因”,塑料件上生成的缺陷,不是无缘无故地凭白产生,一定是有其原因的。于是可以追踪这些缺陷痕迹的线索,顺藤摸瓜找出产生缺陷的原因,从而制订出整治的措施。注塑件上的缺陷,一般是以痕迹的形式表现出来,故可以根据痕迹的形状特征、色泽、大小和位置上的区别,再通过痕迹法的准确识别,就可以迅速地找出产生缺陷的原因,进而可以很快地确定整治缺陷的措施。痕迹法的针对性强、准确,并且查找迅速,可以极大地减少试模的次数。
但是需要掌握大量的丰富缺陷痕迹的经验才能使用痕迹法,为了使缺乏缺陷痕迹的经验人也可以运用痕迹法,这就需要制订出注塑成型痕迹技术规范文本或行业标准。规范文本中有产生各种缺陷痕迹的图片或照片,规范出各种缺陷痕迹的定义、形式和特征以及整治的方法,只要人们对照规范文本就能立即辨认出注塑件上的缺陷,找出缺陷产生的原因和整治的措施。规范文本有如中医的“本草纲目”一样,根据书中图样便可以识别中草药和所能治理的病症。这是利用注塑件上的缺陷痕迹,再通过注塑成型痕迹技术的切入直接找出产生缺陷原因的一种方法,它可以准确而迅速地查找到缺陷的成因及确定整治的措施。该法是新创的方法,目前还不够成熟,特别是在还没有制订出注塑件缺陷规范文本的情况下,会造成读者不能很容易地运用痕迹法。
上述四种缺陷整治的方法,显然CAE法和图解法是在缺陷的预测分析时使用,通过预期分析,可以在确定模具结构预案的同时就能剔除注塑件上因模具结构所产生的缺陷。一般对注塑件可能出现的翘曲变形、熔接痕、气泡和应力集中缺陷,可以用CAE法进行预测分析,是因为这几种缺陷用CAE法分析比较成熟。而其他缺陷就必须运用图解法来进行分析,是因为CAE软件没有其他缺陷分析的软件。又由于缺陷的预测分析不可能将所有缺陷都剔除掉,这是因为人们的主观意识和实际情况总是存在着出入。这样只有通过试模才能发现塑料件上现存的缺陷,有了缺陷就必须整治。因为缺陷痕迹技术分析法是从注塑件上的缺陷痕迹入手,针对性强,并且准确迅速,因此,应该先使用痕迹技术分析法进行整治。当缺陷痕迹技术分析法无法解决时,才可以使用缺陷排查法。
通过上述,可以说综合缺陷分析法是一项全面而科学的技术分析辩证的方法,它们可独立进行缺陷的分析,也能联合进行缺陷的分析和整治,更能相互验证分析的结论。这些分析方法切实可行,并具有实际的可操作性。注塑件上缺陷的问题是件十分困扰人们的事情,有些人不是积极主动地去解决问题,而是消极被动地掩盖问题,这是不可取的。如在注塑件上存在着流痕,先是用砂纸将流痕打掉,再喷上油漆。又如遥控器盒上的熔接痕处治不了,用油漆一喷了事。如此的做法,不仅增加了工序、浪费了资源,还污染了环境。喷油漆表面上是掩盖了问题,但由于熔接痕是注塑件强度最薄弱的地方,而该处如果正好是受力最大的位置,那注塑件就会出现破裂的现象。更重要的是欺骗了消费者。可见注塑件上的缺陷问题不是一个小问题,解决缺陷问题需要一种切实可行的方法,综合缺陷分析法就是这种方法。
2.4.4 注塑件上成型加工痕迹的应用
注塑件上缺陷痕迹不会无缘无故地产生,注塑件在成型加工过程中哪一方面的因素与实际加工出现不适应的情况,注塑件上就会出现相应的缺陷痕迹。注塑件上缺陷的痕迹为我们整治缺陷提供直接的线索,只要我们沿着注塑件上缺陷痕迹的线索,就能找到整治缺陷的办法。注塑件在试模中产生的缺陷肯定是要整治的,试模的目的就是要暴露出缺陷,发现了缺陷才好采取措施去整治。这和治病一样,人有了病要治病。治病最重要的原则是以预防为主、治病为辅。同样缺陷整治原则也是以预防为主、整治为辅。这样就可以尽量避免缺陷的产生,尽量提高试模合格率,以防止产生注塑模报废重做的后果。预防的办法是先对注塑件的缺陷进行缺陷预测,就是应用缺陷论证的方法预先测定注塑模设计时可能会产生的缺陷,从而采取适当的措施去提前预防缺陷的产生。对试模或加工过程中已经出现的缺陷,则要采用“辨证施治”的方法,采用针对缺陷症状的措施去根治缺陷。
[例2-2] 壳体分型面为螺纹根部的端面,浇口为分型面上侧浇口,壳体的材料为聚乙烯。
(1)壳体缺陷类型
如图2-22所示。外表面存在明显的流痕,流痕为存在于壳体外表面上深颜色的凸起斑块状物体。半球形外壳表面还存在明显的缩痕,从壳体投影方向上,还容易发现轮廓线呈凹陷的现象;在壳体侧浇口的背面还存在熔接痕(图中没有表示出来);半球形外壳表面还存在过热痕。

图2-22 壳体缺陷痕迹的识别
(2)缺陷痕迹与塑模结构成型痕迹的区别
这些缺陷痕迹的特征与注塑件的注塑模结构成型痕迹有着形状和性质的天壤之别,因此,注塑模结构成型痕迹与缺陷痕迹是十分容易进行区分的。如果有缺陷痕迹规范文本即行业标准,缺陷痕迹的整治就会变得简单多了;如无缺陷痕迹规范文本,则需要依靠经验进行辨别。
(3)缺陷形成分析与整治
从壳体表面上缺陷痕迹的辨认入手,可以得出壳体表面上存在着流痕、熔接痕、缩痕和过热痕,再在壳体2D图绘制塑料熔体充模图的基础上进行缺陷形成分析。
①壳体浇口与熔料填充分析 壳体如图2-23(a)所示,壳体痕迹的分析如图2-23(b)所示。由于侧浇口处在半球形外壳与螺纹相连接的端面上,在注射机的压力下,熔融的料流先直对着型芯,再从型芯与模腔之间分别由两侧并向上逆向絮流失稳和向下顺流呈稳流状态逐层的进行填充。
②缺陷形成分析 有了塑料熔体充模图,就可以对塑料料流和气体充模进行缺陷的形成进行分析。
a.流痕。如图2-23(b)所示,先进入型腔中的料流遇到低温的型芯,料温迅速下降后,两股料流前锋薄膜所生成的冷凝分子团撒布在料流的流程上。随着料流温度的降低,冷凝分子团逐渐长大便形成了流痕。流痕分布的区域,是在以浇口作为分界线的整个料流填充的面上。
b.熔接痕。如图2-23(b)所示,是因从浇口处充模的塑料熔体直接冲击注塑模型芯产生了降温,低温的分流料流在侧浇口的背面汇合后形成的熔接不良。
c.缩痕。如图2-23(b)所示,缩痕也是很明显,这由于壳体壁厚δ=3mm,冷却时收缩量较大。一般情况是远离浇口处熔料先冷却先收缩,近距浇口处后冷却后收缩。因此,从半球的球冠处开始先冷却先收缩,浇口处后冷却后收缩。故壳体从浇口至半球的球冠表现为逐渐增大收缩的倾向,在远端得不到补充塑料情况下,呈现如图2-23(b)所示的缩痕。
d.过热痕。如图2-23(b)所示,由于熔体是自下而上填充,注塑模中的气体也是自下而上被压缩后,在球冠处所产生的热量上升。当压缩到一定的压强时,便从某一薄弱环节喷射出来。压缩气体的温度又进一步提高,炽热的气体使塑料过热产生炭化而出现过热痕。过热痕是壳体外表面上黑颜色的部位,这是该部位因高温压缩空气喷出而产生炭化的原因。

图2-23 壳体缺陷痕迹的分析
③消除缺陷措施 可见,壳体缺陷痕迹产生的原因是:侧浇口的位置和形式不当,只有改变浇口的位置和形式才能消除缺陷。如图3-23(c)所示,将侧浇口改成点浇口,点浇口设置在半球的球冠顶部,这样塑料熔体料流是自上而下顺流平稳填充,模腔中气体也是自上而下从分型面顺利地排出。并在半球形外壳与螺纹相连接的端面上设置适当数量的冷料穴,上述的缺陷便可迎刃而解。但是,原来侧浇口的注塑模方案是二模板的标准模架,改成点浇口后要采用三模板的标准模架,为此注塑模的修理要颇费周折。如果在注塑模设计之前进行了注塑件缺陷的预期分析,就能完全避开产生的这些缺陷而改动注塑模的后果。
可见主浇道和分浇道的截面大小对注塑件上的缺陷痕迹有着直接的影响,但影响最大是浇口的形式、截面大小、数量和位置。
注塑件上存在着各种缺陷痕迹,是我们观察这些缺陷痕迹的实物,我们可以对症分辨,再进而分析这些痕迹产生的原因,最终制订出处治这些缺陷的办法。这种从观察到分析再处置这些缺陷的技术称为缺陷痕迹技术。可见对注塑模结构成型痕迹和成型加工痕迹这两种痕迹表象的同时观察和分析及处治,是对注塑模结构形式的判断和整治缺陷的最有效的方法。
注塑件上成型加工痕迹是一种语言,它们会向我们陈述缺陷痕迹产生的原因。但是,我们必须要熟悉这种语言,才能剖析和整治缺陷痕迹。一般某一种缺陷痕迹是由某一至两种原因造成的,最多不会超过三种,这样我们排查的范围就会缩小。
注塑件成型加工工艺人员重点关注是加工缺陷的存在,虽然注塑件成型加工工艺人员能够采用注塑件成型加工工艺参数去整治某些加工的缺陷,但是,运用成型加工工艺参数去整治加工的缺陷存在着两种不足:一是通过提高熔体温度和注射压力的措施,增加了能耗和塑料用料。二是有些是因为注塑模浇注系统和结构的不合理性所产生的缺陷,通过调整注塑件成型加工工艺参数是无法到达整治缺陷的目的。只要注塑模结构方案是合理的,包括浇注系统和温控系统的合理性,就不会产生缺陷。缺陷只是因注塑件成型加工工艺参数和非注塑模结构不合理所产生的,通过调整注塑件成型加工工艺参数值和其他影响因素,整治就会变得简单多了。
[例2-3] 注塑件资料:名称为片,如图2-24(a)所示。材料为聚乙烯,型腔处整体在定模部分。
(1)问题件的缺陷
片的正、反面都产生了明显的流痕,如图2-24(b)所示,还存在着不同程度的缩痕。
(2)问题件痕迹的识别
从浇口痕迹的辨别,可以得出浇口为侧浇口,浇口为长方形,浇口位于定模型腔的下侧。
(3)产生缺陷原因的分析
注塑模为一模四腔,脱件板脱模(无顶杆痕迹)结构,浇口是在靠近动模方向。由于模腔内存在着五个型芯,浇口又处在外周圆的两型芯之间。料流从浇口流出就会遇到中间和两旁的三个型芯的阻挡,呈射线状并自下向上逆向絮流失稳填充型腔。高温的料流与低温型芯接触后,料流迅速地降温而形成冷凝分子团。冷凝分子团随着料流撒落在熔体的流程中,并逐渐地增大,待熔体冷硬后,便形成了具有对称性的流痕,如图2-24(b)所示。
(4)整治方案
存在着对现有注塑模修理和重新制造两种方案,出于经济考虑,现有注塑模报废后,才能着手重新制造注塑模方案。
①整治方案一 如图2-24(c)所示。可将矩形的侧浇口改成扇形浇口,改变料流填充的流动方向。从而可以避免高温的料流在碰到低温的型芯后,迅速地降温,再填充注塑模型腔的流动状态所形成的低温分子团,因而可以减缓流痕和缩痕的程度。
②整治方案二 片的型腔设置在动模部分,将扇形浇口设置在靠近定模的方向,使熔体的料流自上而下顺流呈稳流状态填充型腔,流痕和缩痕将会全部消失,但注塑模的结构将要重新改制,但存在着经济损失。

图2-24 片浇口痕迹
(5)实际效果
按方案一的整治,基本上能达到产品的质量要求。其方法是用锉刀将长方形浇口修成扇形浇口即可,从而可以避免采用方案二的措施。
浇口的形式颇多,应该根据塑料成型特性、注塑件形状、尺寸、要求、注塑件生产批量、成型条件及注射机结构等因素,综合考虑选用合理的浇口形式、截面的大小和浇口位置及数量。
[例2-4] 有关注塑件成型加工时出现亮痕的整治,亮痕可分成两种类型:一是ABS/PC料;二是PA料。在成型后注塑件表面会出现白色或光亮的表面,将这种光亮表面称为亮痕。
(1)长条盒亮痕
材料:ABS/PC料类型的亮痕如图2-25所示,长条盒如图2-25所示。1、2和3三处的侧浇口在注塑件同一侧的长边框上,注塑模结构为动模脱模。因为注塑件的转角均为圆角,亮痕就出现在圆弧处与圆弧相邻的两平面上。

图2-25 长条盒
①亮痕 如图2-26(b)所示,在注塑件R圆弧外表面和R的两邻边外平面上均存在着亮痕,内表面上则不存在亮痕。
②亮痕分析 首先要排除注塑模在亮痕部分型腔的表面粗糙度是否过小的因素。那么,为什么亮痕只出现在注塑件R弧形面及R的两邻边平面上?而其他地方就没有亮痕?
如图2-26(b)放大图所示,因为中心层料流的流程是不变的,因此,中心层料流的流速v中保持不变。而外层的流程增长,内层的流程减小,在填充过程中,外层流速v外增大,与注塑模型腔壁的摩擦也就加大了,产生的热量便增加了。由于料流R弧形面与R的两邻边平面上料温的增加及高分子拉升后变细,于是产生了这种亮痕,这就说明了料流由径向流动是产生亮痕的原因。料流内层的流程和流速都减少了,但是料温和高分子大小不会有变化,所有不会产生亮痕。
③整治方法 既然料流R向流动是产生亮痕的原因,那么就应该将料流方向由R向流动改成轴向流动,这样就不会存在料流的流程和流速变化的状况,也就消除了注塑件亮痕产生的因素,如图2-26(c)所示。为了不改变原来注塑模的结构,两处浇口Ⅰ—Ⅰ的具体设置,可采用二次潜伏式点浇口,如图2-26(a)左剖视图所示。将点浇口设置在内壁处,并且是多组对称浇口的浇注系统。如此改动后,还可以消除三处侧浇口所产生的熔接痕问题。

图2-26 料流流向对亮痕分析
(2)PA料类型的亮痕
整个内外表面上都存在着亮痕,特别是凹圆弧面内亮痕更为严重。另外,敲击存在着亮痕注塑件发出声音是沉闷的,而敲击没有亮痕的注塑样件所发出的声音是清脆的。
亮痕分析:注塑件亮痕的缺陷问题,在许多黑色注塑件或多或少都存在着这种现象,其中以聚酰胺(尼龙)料表现得更为严重一些。其原因是与水有关,尼龙具有吸水的特性。我们知道水遇热后会出现雾化现象,遇冷会结成霜,水分干涸之后的水迹是白色的。脱模后热的成型注塑件遇冷干燥返白,其实平面上也有,只是曲面上更为突出而已,这是因为曲面上返白物质的密度较平面大一些。可以做一个试验,将有亮痕的PC注塑件,全部浸泡在水中煮一个小时后取出,自然冷却,这种亮痕就会消失,就说明了只要在注塑件成型之后增加一个后处理工序就可以解决问题。这样,自然是吸水的注塑件声音沉闷,脱水的注塑件声音清脆。
[例2-5] 锥台盒如图2-27(a)所示,材料为ABS,收缩率为0.3%~0.8%。缺陷:处于锥台盒开口端厚壁与薄壁交界处的外表面上,出现了收缩痕,如图2-27(b)所示。不管如何进行收缩量计算,都是无法解决缩痕的缺陷。
(1)缩痕分析
塑料收缩率在一般的情况下,是顺着熔体流动方向的收缩率大于垂直方向的收缩率,这就是塑料的收缩率各向异性。先忽略ABS收缩率的各向异性,将收缩率设定为0.6%。在同一种收缩率的状况之下,对厚薄壁缩痕的深度进行计算。如图2-27(b)放大图I所示,3mm壁厚的收缩量为3×0.6%=0.018mm,1.5mm薄壁的收缩量为1.5×0.6%=0.009mm,缩痕的深度为t=0.018-0.009=0.009mm。即使将收缩率各向异性的因素考虑进去,缩痕也是客观存在的。

图2-27 锥台盒与缩痕
(2)熔接痕形成原因分析
根据上面的计算结果,可以判断是由于锥台盒壁的厚薄不同所致,因为不同壁厚的塑料,其收缩量不同,从而产生了缩痕。
(3)缺陷的论治
物质具有热胀冷缩的特性,壁厚薄不一致,是产生收缩量不一致的原因,这也是不以人的意志为转移的。那么整治缩痕就没有了办法吗?我们应辩证地看待缩痕的两面性问题:一方面是物质具有热胀冷缩的特性;另一方面可以通过创造适当的条件来整治缩痕。如果注塑件在冷却的过程中一方面是收缩,另一方面如能及时补充注塑,就不会出现注塑件的缩痕。因此,必须抓住这种可以操作的条件,既要解决注塑件壁厚不一致的问题,又要解决物料在冷却收缩时材料补充的问题。
(4)整治方案
要解决根治注塑件缩痕的问题,就要从产生注塑件缩痕的本质着手。
①整治方法之一 如图2-28(a)所示,将注塑件壁厚设计成一致,是解决注塑件缩痕的根本方法之一。为了提高注塑件的刚性,可设计加强筋。为了使锥台盒的盖能够进行定位,设计的加强筋至锥台盒端面应保留有一定的距离S。由于锥台盒的所有壁厚相同,它们的收缩量也就相同,故不会产生缩痕。缩痕主要出现在加强筋的背面,此时只要采用保压补塑的办法就能解决缩痕的问题。
②整治方法之二 为了缓解缩痕的程度,可以采用收缩率较小的塑料或采用添加了填充料(玻纤)的增强塑料去成型,收缩率小了收缩量自然也小。也可以在缩痕的位置上设置b×t装饰槽,这样可掩盖缩痕,如图2-27(b)所示。这些措施都可减缓缩痕的程度或掩盖缩痕,但不能根治缩痕。
③整治方法之三 采用延长注塑成型时间、冷却时间和保压时间,增大注射压力和背压压力,使注塑件能得到充分的补塑,缩痕也会小一些,甚至可以消除一些微小的缩痕。另外浇口可开深一些,使浇口融料冷凝慢一些,从而可以充分地进行保压补塑。
④整治方法之四 可采用补偿法来消除缩痕,就是利用补料槽或冷料穴中的物料,在注塑件冷却收缩时进行物料的补充,从而消除注塑件的缩痕。
a.补偿法一,如图2-27(c)所示。在注塑件收缩处,将缩痕用激光扫描生成一个三维造型后,再镜像生成三维电极造型。然后做成电极,在模腔壁上打出和缩痕同样的补料凹槽。料流填充时,在缩痕处多出了一个与缩痕一样的物料,注塑件收缩时,会得到同等收缩量的补偿。自然可消除缩痕。但用电极打制凹槽时的深浅要控制好,只要有差异,在注塑件不是留有凸台就是还存留有很小的缩痕。当然,为了消除缩痕,采用补料凹槽补偿法实在是没有必要。
b.补偿法二,如图2-28(b)所示。在注塑件壁厚不能改动的情况下,注塑模设计时,在厚壁与薄壁交界沿周面处设计成冷料穴,由于冷料穴存有的物料多,冷凝固化慢。开始时可通过浇口保压补塑缓解缩痕,当浇口熔体冷凝硬化之后,停止补塑,并消除了注射压力。注塑件收缩的补充物料,可由冷料穴中的物料得到补充,从而可以起到根治缩痕的作用。

图2-28 注塑件缩痕整治方案
1—上型芯;2—下型芯;3—圆柱销;4—型腔;5—连杆;6—楔紧块
由于冷料穴设置在厚壁与薄壁交界沿周面处,冷料穴中的冷凝料需要取出,才能进行下次注塑件的注射成型加工。这样成型注塑件型腔的型芯,可由上型芯1和下型芯2组成,通过连杆5和锲紧块6可将上型芯1和下型芯2连接在一起。连杆5装有圆柱销3,以便于上型芯1和下型芯2的连接和连杆5的定向。楔紧块6可以通过斜导柱滑块抽芯机构(未画出)进行连接和拆卸。
[例2-6] 垫片如图2-29(a)所示,材料为低密度聚乙烯,特点为薄壁件。
(1)存在的缺陷
填充不足、熔接痕和流痕等缺陷。
(2)缺陷分析
由于型芯Ⅰ为长方形,型芯Ⅱ为正方形与半圆形的组合体。熔体料流的流动状况如图2-29(a)所示。熔体料流充模绕过型芯Ⅰ时,其前锋经过长方形型芯Ⅰ汇合后形成了三角形的涡流区。三角涡流区内容易储存气体,加之是冷凝熔体的涡流形成了熔接痕,熔接痕的强度和刚度是注塑件上最差的部位。而型芯Ⅱ的料流形成的喇叭区,所产生的熔接痕也很明显。矩形侧浇口所喷吐的熔体,在料流碰到型腔壁后,便改变流向进行填充。因为注塑件型孔的形状无法改变,故料流在型芯Ⅰ和型芯Ⅱ处的流动状态和熔接痕也无法改动。浇口处的熔体的流速v1变化较大,加之型腔较长,容易生成震荡流而形成流痕。好在垫片只是起到了衬垫的作用,无强度和刚度要求,熔接痕的问题也就可以剔除掉。
(3)整治措施
根据熔体充模的分析,缺陷产生的原因,主要是三处型芯分流作用和熔体料流充模的状态所造成。
①改进方案一 将矩形侧向浇口改成扇形浇口,如图2-29(b)所示。由于熔体料流喷射的范围扩大而形成了喷射流,浇口处熔体的流速变得平缓,便不易产生流痕。如果出现了填充不足的现象,可适当地修宽浇口,再在产生熔接痕的位置上设置冷料穴,让料流前锋的冷凝料进入冷料穴,便可减缓熔接不良的程度。
②改进方案二 若将浇口改成多个点浇口,并分布在如图2-29(c)所示的位置上形成局部扩散流,可减少熔体流动的流程,熔体的温度降低得极少,有利于料流平稳填充,填充不足、熔接痕和流痕等缺陷都可以消除,还可以进一步提高垫片成型的质量。但因注塑模的改动量过大,注塑模需要从二模板改成三模板,整个浇注系统要推翻重新制造,存在着经济损失。这种情况只有在注塑模重新制造时,才可以采用。这也从一个侧面说明了注塑模结构方案制订阶段,就能对注塑件的缺陷作预期分析,便能有效地避免这些缺陷的产生。

图2-29 垫片缺陷分析
这说明只要注塑模结构方案合理,就不会出现因注塑模结构不合理的缺陷,这样就不用会出现需要修理和重新制造的风险。
[例2-7] 注塑件资料:名称为耳罩圈,如图2-30所示。材料为ABS,形状特点为平边为逐渐抬高的环形薄壁件。

图2-30 耳罩圈
注:A到B处的高度由4mm增至10mm ,B到C处的高度由10mm减到4mm,其余为4mm。
(1)问题件的缺陷
填充不足的缺陷如图2-31所示。如图2-32(a)所示,熔接痕可以根据Ⅰ、Ⅱ和Ⅲ处的浇口位置和熔体在注塑模型腔中流动状况的分析来确定。如图2-32(a)所示,该注塑模有三处浇口,三处浇口流动的熔体必定存在着三处汇交处,1、2及3处便是熔接痕所在位置。

图2-31 耳罩圈填充不足的缺陷
(2)问题件的缺陷分析
三处浇口Ⅰ、Ⅱ和Ⅲ均为侧向浇口,三处浇口都是直对着型芯,如图2-32(a)所示。高温熔体在压力作用下,熔体的前锋直接冲击着型芯再分流填充,熔体前锋的温度迅速降低,从而形成了冷凝薄膜。由于型腔仅有1mm的空间,加之流经汇交1处的流程长,料流在流动的过程中,熔体前锋的温度进一步下降,以致还未流到汇交1处时,便凝固出现填充不足的缺陷。汇交2和汇交3处因流程短,虽然不会出现填充不足的缺陷,但熔体的前锋冲击着型芯降温后的熔接,必将导致汇交处产生熔接痕。
(3)整治方案
鉴于耳罩圈出现填充不足和熔接痕数量较多缺陷的事实,又根据缺陷分析的根源是由于浇注系统的结构形式、位置和浇口数量所产生的,整治方案主要是针对浇注系统进行整改。
①整治方案一 整治方案一是在原注塑模结构的基础上进行经济型整改的方案。该方案只是对注塑模的浇注系统稍作修改,修改所发生的费用极少,并且该整改方案能达到立竿见影的效果。整改措施如图2-32(b)所示。
a.由于有三处侧向浇口,便存在着三处熔体料流的汇交处,即三处熔接痕。要减少熔接痕的数量,就必须减少侧向浇口的数量。可以暂不管浇口是采用什么样的形式,先只保留两个侧浇口,将中间的浇口给封死。又因矩形侧向浇口中的熔体在填充注塑模型腔时,会直接冲击着型芯而降温,故应该将矩形侧向浇口改成两个扇形浇口。利用转角R,可以避免大部分熔体直接冲击着型芯降温而提高其流动性。同时,熔接痕的数量也可以减少一处。
b.考虑到熔体的前锋,直接冲击着型芯后的温度产生突降的原因,将3×2mm×3mm的侧向浇口改成2×(3mm×1mm)×90°的扇形浇口。使熔体呈扇形填充注塑模的型腔,可以避免熔体直接冲击型芯降温。同时在产生熔接痕的地方设置冷料穴,让已降温了熔体的前锋进入冷料穴,从而减缓熔接痕处熔接状况,增大熔接痕处的强度。
c.预测整改效果。填充不足的缺陷肯定会彻底消失;熔接痕的数量将减少一处;熔接痕也会变得不明显,熔接痕处的强度也会大幅度提高,应该说能够满足注塑件的使用要求。
②整治方案二 从完善注塑件质量的角度来评价,该方案是理想型方案,它的实施将会获得较方案一更好的成型效果。但要将现有的注塑模报废,会产生经济损失。
只设一个扇形浇口,将(3mm×1mm)×120°的扇形浇口放置在如图2-32(a)所示的右端熔接痕1的位置上,这样一个浇口只产生一处熔接痕。因为右端1的位置模腔宽度为2mm,而左端1的位置模腔宽度为1mm。根据浇口应设置在宽模腔的原则,扇形浇口应该设置在右端1的位置。为减少熔接痕的程度,可在熔接痕处设置冷料穴。扇形浇口的角度采用120°后,可使熔体沿扇形填充型腔,避免熔体直接冲击型芯后降温。填充过程中,熔体的前锋又进入冷料穴,从而达到减缓熔接痕处熔接状况的目的。

图2-32 耳罩圈缺陷分析与注塑模整改方案
1—型芯;2—浇口;3—分流道;4—主浇道;5—冷料穴
(4)方案评估
该方案可在新设计或现有注塑模复制时运用,由于使用方案二将会报废现有的注塑模,从而产生经济损失,不在万不得已的情况下是不能轻易采用的。
通过以上介绍,说明对注塑模浇口形式和数量作出调整之后,就能达到整治流痕、填充不足和熔接痕数量等缺陷的目的。
(5)浇口的位置对注塑件缺陷痕迹的影响
浇口的位置主要是影响熔体的流动状态和流动方向,会造成料流失稳流动,还会造成料流交叉流动。其结果会使注塑件产生流痕、填充不足、缩痕、气泡和变色等缺陷。
[例2-8] 垫圈如图2-33(a)所示。材料为尼龙1010;特点为厚度只有0.5mm,属于特薄型注塑件。
(1)缺陷与分析
①缺陷 圆形的垫圈变成了三菱弧形垫圈,厚度方向成为波浪形的翘曲变形。
②缺陷分析 熔体料流从外圆周三等分的浇口处填充,如图2-33(b)所示。料流从浇口处直接冲击着中间的型芯,再回弹后分成两股进行失稳填充。三处浇口有六股料流,造成三处交汇,存在着三处熔接痕。同时,浇口Ⅱ、Ⅲ的流程相等,但与浇口Ⅰ的流程不等,造成了料流的压力、流速和流量的不同。浇口料流的冲击存在着反作用力的影响,加之浇口处与其他部分塑料收缩不一致,导致垫圈成为三菱弧形和厚度方向波浪形的翘曲变形。处置方法是,只能用电熨斗熨平翘曲变形,但是却解决不了圆形为三菱弧形的缺陷。
(2)缺陷整治方案
①整治方案之一 如图2-33(c)所示,将侧向浇口改成单一切向侧浇口,熔体料流从圆形注塑模型腔的切向进行填充,从而避免了料流直接冲击中间的型芯而产生的熔体降温,且料流是平稳的进行填充。这样使得料流对垫圈的流向、压力、收缩和熔接的影响减少,从而可以达到控制圆周和厚度方向变形的目的。料流只有一处汇交处,熔接痕也就只有一处。其实采用这种切向浇口,使得塑料熔体从切向浇口进行充模是最为简便可行的填充形式。
②整治方案之二 如图2-33(d)所示,由于是外圆周三侧浇口形式,必定会导致料流的流程不一致而影响填充的平衡性。将外圆周三侧浇口的形式改为内圆周三切向侧浇口的形式,内三切向侧浇口的料流便可以得到充分的平衡,从而可以改善垫圈外圆周三侧浇口形式的缺陷。由于存在着三股料流,便会产生三处熔接痕。由于三股料流的流程短,熔接不良不会很明显。
③整治方案之三 如图2-33(e)所示,若将内圆周三切向的侧浇口的形式改成盘形浇口,那就不是三点式填充而是整个内圆周进行填充,确保了填充和收缩的绝对均匀性。不仅可消除变形的缺陷,还可消除熔接痕。只是切除盘形浇口冷凝料的工作量增加了,还会在修饰时损伤注塑件的内孔。为了不损伤注塑件的内孔,可用手工冲孔模去除盘形浇口冷凝料。

图2-33 垫圈浇注系统缺陷分析图解法
④评估 就此改成单一的内切向侧浇口或外切向侧浇口的形式,是这种特薄型注塑件浇注系统的最好选择。
[例2-9] 卡板座如图2-34所示。材料为PC/ABS合金。由于该注塑件中间具有较深的凹槽,如图2-34中A—A剖视图所示。其形状如π字形,特点是注塑件呈凸凹形,两侧的形体较厚,中间的形体很薄。
①缺陷分析 卡板座脱模后易产生向两外侧张开的变形,如图2-34(a)所示。虽然可以延长注塑件成型时冷却时间来减缓变形,但这样做就会牺牲生产的效率,而且也无法确保注塑件的变形不超差。在无法采用注塑模相应结构来实现注塑件不变形的情况下,可以采用注塑件脱模后使用辅助工具强制校正,使得注塑件不变形。由于其形状特点所决定,无论采用什么样的注塑模结构都很难避免卡板座的翘曲变形。因为注塑件脱模之后,仍有余温,注塑件的收缩和变形仍会继续进行。

图2-34 卡板座
②注塑件模外变形的校正 如图2-35(b)所示。可以用两根校正圆柱棒1和圆环2,其中一根圆柱棒1中装有圆环2。将两根圆柱棒1插入卡板座的两个对称的孔中,再将圆环2套住另一根圆柱棒1上。将装有校正圆柱棒1和圆环2的卡板座放进具有室温的水中数分钟定形后,再取下圆柱棒1和圆环2,卡板座的翘曲变形便可得到校正。圆柱棒1的长度和圆环2直径要经过试验后才能够确定,以防校正过头。

图2-35 卡板座的校正过程
1—圆柱棒;2—圆环
对于“变形”要素而言,可能会因为所取的分型面上存在着“障碍体”而使注塑件产生变形;也可能会因为浇注系统选择不合理而产生变形;还可能会因为抽芯机构和脱模机构设计不妥而产生变形;还可能会因为注塑工艺或工艺参数设置不当而产生变形。注塑件变形是由多方面因素造成的,具体情况应具体分析,最后才能作出判断。
采用成型加工之外的校正方法:注塑件产生了翘曲变形之后,还可以采用成型加工之外的校正方法进行翘曲变形的校正,如采用机械校正注塑件的翘曲变形。卡板座模外变形的校正,就是采用机械构件夹持已翘曲变形的但仍有余温的注塑件,然后,整体放置在水中冷却定型来校正翘曲变形。
[例2-10] 护盖如图2-36所示。材料为聚甲醛,简称为POM,密度为1.41~1.43g/cm3,喷嘴温度为170~180℃,注塑模温度为90~120℃,注射压力为80~130MPa,螺杆转速为28r/min,注射时间为20~90s,高压时间为0~5s,冷却时间为20~60s,总周期为60~160s,收缩率为1.2%~3.0%,设备为螺杆式注射机。

图2-36 护盖
标注:矩形框内的区域相对于平面D下沉0.3mm,材料标记“<POM>”在矩形框内平面上凸起0.2~0.3mm,字体采用Word文档中SANS SERIFP,字体字母大写,字号为4。
①存在的问题 护盖型腔的分布为一模六腔,如图2-37所示。在六浇口尺寸相同的情况之下,六腔中只有中间的两腔是合格的,两侧的四腔都存在着缩痕,为不合格件。在保持主浇道和分浇道尺寸不变的情况之下,为了能够成型一模六腔合格的注塑件,只有将两侧四腔的浇口给堵住,只使用中间的两腔,这样造成生产效率的降低。

图2-37 护盖型腔分布
②缩痕分析与整治 由于中间的两腔分浇道的流程短,其熔体的压力和流量较大,熔体是先充满这两个型腔。两侧的四腔分浇道的流程长,在与中间的两腔点浇口直径和长度相同的条件下,其熔体的压力和流量较小,不可能充满型腔,此时,应扩大两侧的四腔点浇口直径。
③多型腔流量平衡计算 方法一:通过多型腔流量平衡计算的方法;方法二:通过试模修理点浇口直径的方法,以到六腔流量的平衡。
一模多腔,当多条分浇道的流程不同,而注塑模的浇口又相同时,流入注塑模模腔熔体的压力、流速、流量、温度、剪切作用和摩擦作用都会不同,从而会产生注塑件的缩痕和填充不足等缺陷。通过调整注塑模浇口的宽度和厚度的尺寸,可以达到调整流入注塑模型腔熔体各种物理量平衡的目的,进而达到消除注塑件缺陷的目的。
2.4.5 注塑模结构设计和注塑件缺陷整治网络服务
注塑件上的痕迹可以通过缺陷的预测来分析,确定注塑模浇注系统和注塑模结构方案达到预防的目的。即使是产生了缺陷,也可以通过整治的方法加以根治。成型痕迹和成型痕迹技术是一门新创立的技术,由于该技术还不够成熟和规范,实践性很强,牵涉的知识面广与专业多,工作难度极大,处理问题时极为棘手,若无综合的专业知识和丰富的实践经验,是很难解决成型技术上的许多问题的。注塑件上成型痕迹处理过程是:通过对问题件进行观察和分析,找出问题产生的原因之后,再给出处治的措施就可以了。这样少数专业人员便可以通过网络进行注塑件缺陷整治的咨询。其方法是:将注塑件缺陷视频或照片,通过网络传给成型加工缺陷医院或诊所中的专家,也可以邮寄实物,由专家作出诊断,并提出处治的措施。这样在全国甚至在世界范围内建立的这种网络,可以服务许多注塑件成型加工的企业。
2.4.6 痕迹学
注塑成型痕迹学是由多学科(流体力学、热力学、高分子材料学、工艺学、成型工艺学、注塑模设计、模具材料和热表处理)和痕迹技术组成的一门新型的理论学科。它可以从更深的层次上解释痕迹技术所遇到的问题,从而解决全部的成型加工过程中问题;同时,对深化注塑件的成型痕迹技术也起到了促进的作用。
从成型痕迹和成型痕迹技术及其运用的一些入门的基础知识,可以看出成型痕迹技术是一门实用的专业基础技术。成型痕迹技术是从注塑件成型加工时的实际症状出发,应用某些行之有效的方法去解决问题;从注塑件成型加工本质和深层次上去解释问题的实质,这就是痕迹学需要解决的问题。成型痕迹是成型件在成型加工过程中所形成的客观的事实,若能将成型痕迹上升到成型痕迹技术和成型痕迹学的理论高度,再用其去指导和解决成型技术的实践,其价值和意义就更大了。痕迹学和成型痕迹技术是成型缺陷“医生”整治成型件弊病的专业性理论和技术,成型缺陷规范文本即行业标准是成型件弊病辨别和处治的基础性文件。
注塑件上的成型痕迹与成型痕迹技术,就是利用注塑件在成型加工过程中,注塑件上烙印的注塑模结构成型痕迹,来解决注塑模克隆、复制和修理的技术;还可以利用注塑件产生的成型加工痕迹来整治注塑件上缺陷。可见注塑件上的成型痕迹与成型痕迹技术,是注塑成型加工技术中十分有用的技术。我们应该深入地进行注塑件上的成型痕迹与成型痕迹技术的研究,找出更多和更好的方法应用于注塑模设计和注塑件的成型加工。