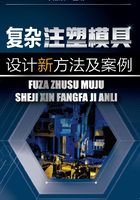
3.1 注塑模结构方案常规可行性分析与论证
注塑件的形体“六要素”分析之后,不能立即转入注塑模的结构设计,中间还需要有一个过渡的部分,这就是注塑模结构方案可行性分析与论证、注塑模最佳优化方案可行性分析与论证以及注塑模最终结构方案分析与论证。通过这个步骤可以从注塑件的形体“六要素”分析衔接到注塑模的结构设计,从而使这两者有机地联系起来。注塑模结构设计的正确与否,关键是注塑模结构方案可行性分析与论证、最佳优化方案可行性分析与论证以及注塑模最终结构方案分析与论证正确与否。当分析与论证充分彻底了,注塑模结构和机构的设计才能到位,从而可以避免注塑模结构设计的失误,也可减少试模的次数和时间。注塑模结构设计的成功与否,包含两个方面:一是注塑模是否可以顺利地进行注塑件的成型加工;二是成型加工后的注塑件上是否存在着各种形式的加工缺陷。通常注塑模设计和制造人员重点关注的是注塑模的形状、尺寸、精度和使用性能,而会忽视注塑件上加工缺陷的存在。如何将注塑模结构设计与注塑件加工的缺陷有机联系起来,一直是注塑成型行业中存在的问题。
对于复杂和高精度的注塑模设计而言,在注塑件形体“六要素”分析与注塑模结构设计之间,必须着手进行注塑模结构方案的可行性分析与论证。注塑模结构方案的可行性分析,主要是采用痕迹分析、要素分析和综合分析三种方法,来初步确定注塑模的结构方案。
3.1.1 注塑模结构方案的常规(要素)可行性分析法的种类
注塑模结构方案的常规可行性分析法,也可称为要素可行性分析法,是一种以注塑件单一要素对模具结构方案进行可行性分析的方法,也是最基本的一种分析方法。这种分析方法,是对简单的模具结构方案进行可行性的一种分析方法。对复杂的注塑模结构方案进行可行性分析,也是要采用这种分析方法。因为任何复杂的事物都是由简单的事物组成。同理,任何复杂注塑模也是由各种基本的机构和构件组成。具体的模具结构可行性方案,是要根据注塑件具体形体分析的要素,找到解决相应要素所要求的具体措施,这种措施就是模具结构方案。当然,这些措施是针对相应的要素,但解决的措施是有多种形式。对于需要解决的复杂模具结构可行性方案,有时对于单个解决的措施之间会存在着矛盾或产生冲突的现象,这就需要对这措施进行适当的调整。经过调整后,以达到最佳的组合。常规(要素)可行性分析法种类如下。
①注塑件上“形状与障碍体”要素的模具结构方案可行性分析法;
②注塑件上“孔槽与螺纹”要素的模具结构方案可行性分析法;
③注塑件上“变形与错位”要素的模具结构方案可行性分析法;
④注塑件上“运动与干涉”要素的模具结构方案可行性分析法;
⑤注塑件上“外观与缺陷”要素的模具结构方案可行性分析法;
⑥注塑件上“塑料与批量”要素的模具结构方案可行性分析法。
只有对常规(要素)可行性分析法应用熟练了,并且积累了一定的经验之后,再进行复杂注塑模结构方案的可行性分析就易如反掌、手到擒来了。
3.1.2 注塑件上“形状与障碍体”要素的模具结构方案可行性分析法
从注塑件形体分析中找到了“形状与障碍体”要素后,就应该分别对找到的“形状与障碍体”要素采取实际的措施来化解要素提出的要求,这种化解要素的措施即模具结构方案。
(1)注塑件上“形状”要素的模具结构方案可行性分析法
注塑件内形是依靠模具型芯成型,利用模具开、闭模运动完成注塑件的成型与脱模。注塑件外形与外螺纹(含螺杆)也是属于注塑件“形状”要素的内容之一。外形是包括整体与局部轮廓线均为平行开、闭模运动方向的注塑件,外螺纹包括外部螺纹和内形螺纹两种形式。
①注塑件形状要素的规避方法 注塑件内外形与内外螺纹形式的形状要素成型方法如表3-1所示。
表3-1 注塑件内外形与内外螺纹形式的形状要素成型方法


②注塑件上形状要素的模具结构方案可行性分析法 单一注塑件形状要素,是指具有与开闭模方向轮廓线一致内外形的注塑件。由于注塑件在设备中所处的安装、连接方式和功能及作用的不同,导致注塑件的形体和结构出现了千变万化,注塑件一般具有盒状、盘状、盖状、桶状、筒状、柱状、环状、球状、块状、板状、片状和异形状等形式。针对不同形状和批量的注塑件,成型注塑件的型腔可以采用不同数量和排列形式及浇注系统的形式。针对注塑件上述的各种形式几何形状要素,应该选取注塑模型腔与型芯的形状、尺寸与腔数来决定注塑模面积大小和闭合高度;应选取分型面的位置和形式来决定模具动模与定模型腔以及注塑件抽芯、镶嵌件和脱模的形式与位置的模具结构分析方法。
这些注塑模结构特点是成型注塑件的外形是依靠动模或定模的型腔,成型注塑件的内形是依靠动模或定模的型芯。模具结构要点是要设计好注塑件的分型面,主要是需要考虑使注塑件在模具开启之后能够滞留在动模部分,这样便于注塑件的脱模。其次是需要根据注塑件的形状特点和批量,设计好浇注系统的形式和位置,以防注塑件产生一些缺陷。
(2)注塑件上“障碍体”要素的模具结构方案可行性分析法
注塑件上存在的各种形式和数量的“障碍体”要素,均应采用有效避让“障碍体”要素的措施,使得注塑件能够正常地成型、分型、抽芯和脱模。这些避让“障碍体”要素的措施,主要体现在选取注塑模分型面、抽芯和脱模方案的分析方法上。
①注塑件“障碍体”要素的规避方法 有一些注塑件上存在着各种形式和数量的“障碍体”,这些注塑件上的“障碍体”会影响注塑模的分型面、抽芯机构和脱模机构的选取,从而影响注塑件正常的成型加工。如何根据注塑件“障碍体”的形式和数量,采取有效避让各种形式和数量“障碍体”的措施,是制订注塑模结构可行性方案的重要方法和技巧,也充分体现了从注塑件形体分析到注塑模结构方案分析的因果关系。注塑件上“障碍体”要素的模具结构方案可行性分析法如表3-2所示。
表3-2 注塑件上“障碍体”要素的模具结构方案可行性分析法




②注塑件“障碍体”要素模具结构方案可行性分析法 注塑件上“障碍体”要素存在着多种形式和多个数量,但对于常规的注塑模结构方案可行性分析方法来说,是指仅有一种单一“障碍体”要素。即使是注塑件上出现了多种形式和多个数量的“障碍体”要素,也需要一个一个地去解决,最后再集中加以协调以达到统一处理的目的。
3.1.3 注塑件上孔槽与螺纹要素的注塑模结构方案可行性分析法
孔槽与螺纹要素分析法:是针对注塑件上各种形式孔槽要素,如何实现孔槽要素成型和抽芯方案的一种分析方法。注塑件在大多数的情况下都是具有孔槽与螺纹要素,孔槽与螺纹要素概念不相同,并且所采用措施也不相同。在一般情况下,主要是按孔槽与螺纹要素在注塑件上走向与注塑模开闭模方向来进行区分,一种是平行注塑模开闭模方向的,另一种是垂直和倾斜注塑模开闭模方向的型孔和型槽。孔槽与螺纹要素是注塑件上常见的几何形状结构,注塑模的抽芯机构、镶嵌件和活块结构的设计,主要是取决于注塑件的孔槽与螺纹要素的形状、位置、方向及其尺寸精度。并且注塑件的孔槽与螺纹要素是影响注塑模开闭模、抽芯和脱模运动及其机构的因素。注塑件孔槽与螺纹要素是注塑件形体分析的六大要素之一,也是注塑模的结构方案分析和设计中避不开的因素之一。
注塑件上孔槽与螺纹的形状,就是注塑模抽芯机构型芯的形状;注塑件孔槽与螺纹的位置,就是注塑模型芯的位置;注塑模型芯的尺寸,就是在注塑件孔槽与螺纹的尺寸再加上塑料的收缩量的尺寸;注塑模型芯运动的走向,取决于注塑件上孔槽与螺纹的走向;注塑模型芯运动的行程、运动起点和终点,取决于注塑件孔槽与螺纹的深度、孔的外端面和内端面。可见注塑模型芯的内容,完全取决于注塑件孔槽与螺纹要素的内容。注塑模的抽芯机构、型芯和嵌件杆的结构,主要取决于型孔或型槽在注塑件上的位置、方向和孔或槽的形式。注塑件上若有型孔或型槽,可以应用抽芯机构的型芯复位后完成注塑件型孔或型槽的成型,型芯抽芯后让出足够的空间以便于注塑件的脱模。也可以使用型芯、嵌件杆和活块复位后,完成注塑件型孔或型槽的成型,还可以利用动、定模的开、闭模运动完成抽芯。小螺孔只能采用型芯、嵌件杆成型;大的螺孔既可采用活块成型,也可采用齿条、齿轮与锥齿轮副垂直抽芯机构及其他脱螺孔机构完成螺孔的成型与脱螺孔动作。
(1)注塑件正、背面孔槽与螺纹的成型与规避方法
注塑件正面及背面孔槽与螺纹及小螺纹孔走向若是平行于开、闭模方向,一般是采用型芯或螺纹型芯或螺纹嵌件杆来成型;可以利用动模开、闭模运动,使得动模与定模上的型芯或螺纹型芯或螺纹嵌件杆完成孔槽与螺纹成型与抽芯及小螺纹孔成型与脱螺孔。对注塑件中成型螺纹孔螺纹型芯或螺纹嵌件杆而言,螺纹型芯或螺纹嵌件杆则是需要用人工来安装和取出。即注塑模开启时,人工来取出和安装螺纹型芯或螺纹嵌件杆。动、定模合模时,完成螺纹型芯或螺纹嵌件杆的复位。特别是对于注塑件上沿周孔槽与螺纹要素,如果处理不当,将会影响到注塑件的脱模。注塑件的正、反面孔槽与螺纹的成型与规避方法如表3-3所示。
表3-3 注塑件的正、反面孔槽与螺纹的成型与规避方法

(2)注塑件上沿周侧面孔槽与螺纹的成型与规避方法
注塑件上沿周侧面孔槽与螺纹成型和抽芯,一般采用各种形式侧向抽芯机构的型芯或活块进行成型和抽芯。注塑件上沿周侧面孔槽与螺纹成型与规避方法如表3-4所示。
表3-4 注塑件上沿周侧面孔槽与螺纹成型与规避方法



(3)注塑件螺纹的成型与脱螺孔方法
注塑件上的螺孔在螺纹底孔成型之后,再进行补充加工螺孔的方法和用螺纹型芯成型的方法。而脱螺孔的方法有手动脱外螺和螺孔,也有采用机械脱外螺纹和螺孔的方法。当注塑件四周存在着水平的侧向螺孔或斜向螺孔的时候,可以有四种成型加工方法。注塑件上螺纹成型与脱螺纹方法如表3-5所示。
表3-5 注塑件上螺纹成型与脱螺纹方法




①螺孔的补充加工方法 当注塑件四周存在着水平侧向螺孔或斜向螺孔时,可以先采用水平侧向抽芯或斜向抽芯来成型螺纹底孔,在注塑件脱模后,再采用补充加工的方法,即用螺纹丝锥或自攻螺钉直接加工出螺纹孔。这种螺孔补充加工的方法既简便,又比较实用,故在实际工作中经常会采用。另一螺孔补充加工的方法,就是用钻模加工出螺纹的底孔,再用螺纹丝锥加工出螺纹孔。这种螺孔补充加工的方法,除了要设计和制造出加工螺纹底孔的钻模之外,还要增加钻孔和攻螺纹的工序,因而要影响注塑件的加工效率,实际工作中很少采用。
②金属镶嵌件成型螺纹孔的方法 是在注塑件成型加工中埋入螺纹金属镶嵌件的方法。此法是在注塑模中以型芯或嵌件杆来支承金属镶嵌件,型芯或嵌件杆需要利用注塑模的开闭模运动进行抽芯与复位的动作,而在型芯或嵌件杆上制有螺纹。一般情况下,是型芯或嵌件杆随注塑件一起脱模后,由人工取出。该种方法除了会增加注塑件的重量之外,还会影响注塑件几何形状和尺寸的设计,更会使注塑件产生成型加工的熔接不良和增加熔接痕等缺陷。但金属镶嵌件使螺纹的强度和刚性增加了,耐磨性也得到提高。
③螺纹型芯成型螺纹孔的方法 可以采用螺纹型芯成型注塑件水平方向、垂直方向、侧向螺孔或斜向螺孔。螺纹型芯通过齿轮和齿条副的传动和油压缸等的驱动进行脱螺纹。
④螺纹型芯的水平机动抽芯成型螺纹孔的方法 可以采用斜销、螺旋杆和齿轮进行机动螺孔抽芯的方法。
螺纹包括外螺纹与螺孔两种形式,外螺纹时而是“形状”要素,时而是“孔槽与螺孔”要素,而螺孔只能是“孔槽与螺孔”要素。
3.1.4 注塑件上“变形与错位”要素的模具结构方案可行性分析法
注塑件上的“变形与错位”要素,是影响注塑模结构的因素之一,也是注塑件形体 “六要素”分析之一。注塑件的变形与注塑件的分型形式、脱模形式、抽芯形式、注塑模的浇注系统的设置、塑料熔体的流动性和收缩率、成型加工的参数等有着因果的关系。但是对“变形与错位”要素的分析,就注塑模结构方案分析来说,只是局限于模具结构设计和浇注系统的设置。对于“变形与错位”要素的分析,要注意两者具有一定的隐蔽性,看似不易找到,却有着明显的规律,主要是从注塑件的几何误差和技术要求中去寻找。对“变形”要素来讲,就是要找到注塑件上的平面度和直线度的要求,特别要注意细、长、薄的注塑件和具有多齿形与凸凹不平的注塑件。对“错位”要素而言,不仅要找到注塑件上的对称度的要求,还需要注意薄壁件。然后,再寻找解决注塑件“变形与错位”的注塑模的措施。
(1)注塑件上“变形”要素的模具结构方案可行性分析法
注塑件变形的发生,绝大部分是脱模方式选取不当和内应力的作用产生的。
①注塑件“障碍体”要素的规避方法 是针对注塑件上各种形式的“变形”要素,如何避免注塑件发生翘曲、变形和裂纹的模具结构方案的一种分析方法。防止注塑件“变形”的方法如表3-6所示。
表3-6 防止注塑件“变形”的方法

②注塑件“变形”要素的模具结构方案可行性分析法 注塑件上的“变形”要素存在着多种形式,但对于常规的注塑模结构方案可行性分析方法来说,是指仅有一种的单一“变形”要素。即使是注塑件上出现了多种形式和多个数量的“变形”要素,也得一个一个地去解决,最后再集中协调以达到统一。
(2)注塑件“错位”要素的模具结构方案可行性分析法
“错位”要素分析法 针对注塑件上各种形式的“错位”要素,如何制订避免注塑件形体发生错位的模具结构方案。对成型高精度注塑件的模具来说,仅仅依靠这些通用导向及定位机构是不够的,还需要另加注塑模精确定位和二次定位的导向及定位机构,才能确保注塑模导向及定位的精度。这些机构主要应用在动模、定模的二次定位和精密定位;型腔与型芯的精确定位;滑块精确导向等方面。当然,精密注塑模除了具有精确的导向及定位机构之外,还要有高精度的模具零件的加工、模具的装配精度、足够的刚性和耐磨性、良好的温控系统、合理的浇注系统和塑料品种的选择以及协调的模具运动机构等。
①型腔与型芯的精确定位 如表3-7所示。一般是采用凸、凹锥体或锥孔进行无间隙的二次定位和精密定位,从而确保注塑件成型构件精密导向和定位。
表3-7 型腔与型芯的精确定位

②滑块和型芯的精确定位 注塑件上会有多种形式的外形和内孔,并且内、外形的尺寸精度、同轴度和壁厚的均匀性都有一定的要求。注塑模若采用滑块形式对开模结构不能确保注塑件的质量时,则需要对成型注塑件孔和槽的滑块和型芯进行精确的定位。此时仅靠注塑模架上的导向装置,是不能满足精密注塑模的定模型腔和动模型腔或型芯相对位置的准确性,还需要采用二次定位系统;如采用分型面两端的二次定位装置,仍然不能避免动、定模型腔的错位时,则应该采取动、定模的四面带锥形面的无隙二次定位装置。如锁扣应用Cr12MoVA钢材制造,硬度58~62HRC,扣公与扣母的配合间隙应在0.005mm之内,滑块和型芯的精确定位方法如表3-8所示。
表3-8 滑块和型芯精确定位方法

3.1.5 注塑件上运动与干涉要素的模具结构方案可行性分析法
注塑件在模具成型加工过程中,存在着多种运动形式,有多种运动就存在着运动干涉可能性。运动与干涉要素是注塑件形体分析的六大要素之一,它不仅影响注塑模的结构,还会影响注塑模的正常工作,甚至会因为模具的构件相互撞击而使模具和设备损坏。运动与干涉是注塑模结构设计时不可避免的因素,也是注塑模结构设计的要点。在模具设计时,要去除各种运动机构所能产生运动干涉的隐患。其具体方法就是应用注塑件的运动与干涉要素,去分析注塑模的各种运动机构能否产生运动干涉,并且采取有效措施去避免运动干涉现象的发生。注塑模结构设计时,一定要使模具动作有序地进行。
(1)注塑模的基本运动形式
运动要素分析法是针对注塑件上各种形式的运动要素,制订出机构间运动的规律、路线和节奏的模具结构方案分析方法。为了完成注塑件成型加工的要求,注塑模的结构必须能够完成一定的运动形式。注塑件的形体是千变万化的,注塑件结构越简单,模具所需要的运动形式就越简单;注塑件结构越复杂,模具所需要的运动形式也就越复杂。应该说注塑模本身是不可能产生运动的,注塑模的运动形式都是从注塑机的运动机构中派生的。模具运动机构的选择对注塑模的运动形式影响很大。模具运动机构已经有很多种,随着注塑件的结构和精度不断地发展,模具运动机构还将不断地创新。就是简单的注塑模,也需要有三种基本的运动形式。
①注塑模的开、闭模运动 开、闭模运动是模具在分型面处的定、动部分沿着模具中心线进行开启和闭合的运动。模具闭合后可以形成封闭的型腔,熔体才能够充模成型;模具开启后,冷凝硬化的注塑件才能够从模具型腔中脱模。注塑模的开、闭模运动是注射机消耗功率的主要运动形式。模具许多的运动是由其派生的,如型孔的抽芯运动、注塑件定模的脱模运动、脱模机构的复位运动和脱浇口运动等。注塑模的开、闭模运动是从注射机移动的动模板获得的,因此是独立的运动。
②注塑件的脱模运动 注塑件的脱模运动是通过注射机的顶杆,把运动传给模具的脱模机构,再将注塑件顶出动模型腔或型芯的运动。注塑件的动模脱模运动也是独立的运动;注塑件的定模脱模运动,则是通过模具运动的转换机构,将模具的开、闭模运动转换成定模脱模机构的运动,再把注塑件顶出定模型腔或型芯的运动,因此是派生运动。
③注塑件的抽芯运动 在注塑件上有沿周侧向孔槽与螺纹时,注塑件需要有沿周侧向分型运动,模具就需要有型孔或型槽的抽芯运动。成型注塑件型孔或型槽的型芯,则需要有型芯的复位动作,成型后需要有退出型孔与型槽的抽芯动作,如此才能进行注塑件的脱模。注塑件抽芯机构有很多形式,其中运用最多的是斜销滑块抽芯机构,是利用模具开、闭模运动时的斜销插入与退出滑块的斜孔而完成抽芯机构抽芯和复位运动。这种抽芯运动也为派生运动。弹簧抽芯、气压和液压抽芯,则是由弹簧、气缸和油缸完成的独立运动。
(2)模具的辅助运动
模具除了具有三种基本运动形式之外,其他机械传动形式为模具的辅助运动。另外,有时还需要一些附属运动,所谓附属运动就是可以用手工操作来代替机械运动。如机械抽芯、气动和液压抽芯,可以作为基本运动形式;注塑件抽芯运动也可以用手工进行,但只能是附属运动。附属运动一般是在注塑件批量少、生产效率低和模具结构简单的情况下采用。
①脱浇口冷凝料的运动 塑料熔体在填充模腔的过程中,浇注系统也充满了熔体,冷凝的熔体需要及时地清除,否则堵塞浇注系统后会妨碍下一次熔体的充模。故在模具合模之前一定要将浇注系统中的冷凝料清除掉,这种清除动作称为脱浇口冷凝料的运动,简称脱浇口运动。一般情况下是应用拉料杆先将主浇道中的冷凝料拉出来,再通过脱模机构将浇道中浇口的冷凝料顶出,同时,也要切断浇口中的冷凝料。可见,脱主浇口冷凝料的运动是依靠模具的开模运动实现的,而脱浇口冷凝料的运动则是靠脱模机构的顶出运动而实现的。脱浇口冷凝料的复位运动,可以依靠回程杆的复位运动来实现。
②脱模机构的复位运动 注塑件脱模之后,脱模机构需要复位到注塑件脱模之前的位置,以便进行下一次注塑件的脱模,我们将这种运动称为脱模机构的复位运动,简称复位运动。模具合模时,脱模机构的复位运动是在回程杆接触到定模板后,定模板推动回程杆而实现脱模机构的复位。
③脱模机构的先复位运动 模具的复位运动与模具的合模运动是同步进行的,模具抽芯机构的复位运动需要先于脱模机构的复位,否则将会产生抽芯机构的型芯与脱模机构的推杆发生运动的干涉现象。因此脱模机构的推杆必须先于抽芯机构的型芯复位,这就是脱模机构的先复位运动,简称先复位运动。先复位运动可依靠弹簧进行,但长时间使用后弹簧会失效,故需要经常更换弹簧。此外还可采用先复位机构以实现脱模机构的先复位运动。先复位运动也是由模具的开、闭模运动所产生的派生运动。
④限位运动 限位运动可分成为中、定模开模时的限位运动、抽芯机构的限位运动和脱模机构的限位运动。限位可以通过限位销或限位螺钉或限位机构来实现,运动的形式则可由弹簧独立产生或由模具的开、闭模运动产生。
⑤开模运动 模具需要进行二次及二次以上的开、闭模时,需要利用模具的开、闭模运动,使得开模机构转换成二次的开、闭模运动。
(3)特殊的模具运动
特殊的模具运动包括模具二次开闭模运动、二次脱模运动、二级抽芯运动、脱螺纹运动、齿轮齿条副的抽芯等运动。这些运动都需要根据注塑件形体结构和精度以及所采用的运动机构来确定。
(4)模具各机构间的运动干涉要素
干涉要素分析法是针对注塑件上各种形式的运动干涉要素,制订出运动构件间出现碰撞的模具结构方案的分析方法。注塑模工作时,模具的开、闭模运动是主要的运动,并派生出注塑件的抽芯运动,还有由注塑机顶杆所产生的注塑件脱模独立运动。模具这些机构之间的运动,都有可能产生多种形式的运动干涉现象。
①模具机构之间的运动干涉 注塑模工作时,模具各种运动机构的构件之间所发生的相互碰撞现象称为运动干涉。
②模具机构运动干涉的种类 模具机构包括“障碍体”类型、抽芯类型和抽芯脱模类型三种运动干涉。
a.“障碍体”类型的运动干涉。注塑模在工作中,由于注塑件的形体上存在着“障碍体”,“障碍体”与模具各运动机构之间相互碰撞的现象称为“障碍体”类型的运动干涉。
b.抽芯类型的运动干涉。注塑模上存在着注塑件多种型孔或型槽的抽芯运动,如果这些型孔或型槽的轴线相交或相错,便会引起抽芯机构的构件之间相互碰撞,这种碰撞现象称为抽芯类型的运动干涉。
c.抽芯脱模类型的运动干涉。在注塑模抽芯机构与脱模机构的构件之间相互碰撞的现象称为抽芯脱模类型的运动干涉。防止注塑模运动干涉的方法及特点如表3-9所示。
表3-9 防止注塑模运动干涉的方法及特点


3.1.6 注塑件上“外观与缺陷”要素的模具结构方案可行性分析法
我国三项专利中有一项是外观设计,可见人们对产品外观的重视。可是注塑件外观设计得再美观,而注塑模结构设计却不能保证加工出外表美观的注塑件,那么注塑件的价值将会大打折扣,甚至失去市场。对注塑件来讲,外观的设计越来越重要。作为注塑件的“外观”要素,对模具结构的影响也很大。“缺陷”要素分析法是针对注塑件上各种形式“缺陷”要素,制订出适应注塑件无缺陷模具结构方案的分析方法。注塑件上的“缺陷”要素,不仅是影响注塑件外观的因素,还是影响注塑件使用性能的因素。只要注塑件上存在着缺陷,这个注塑件就是次品或废品。对注塑件上存在的缺陷,需要整治以消除缺陷。注塑件上缺陷产生的原因有很多,模具结构不当是注塑件产生缺陷的主要因素之一。
外观要素分析法是针对注塑件上各种形式的外观要素,制订出适应注塑件外表美观性的模具结构方案的一种分析方法。注塑件的外观要素是指在注塑件表面上应该消除的模具结构成型的痕迹和成型加工的痕迹,这里主要是指应该消除注塑件上分型面、抽芯、注塑件脱模和模具镶嵌的成型痕迹。当然,缺陷的痕迹更是不允许存在的。
①去除注塑件上分型面痕迹的方法 去除注塑件上分型面的痕迹,主要应用在圆柱形注塑件和侧面无“障碍体”的注塑件,应尽量避免在影响注塑件外观的型面上进行分型。外观要素对注塑件上分型面选用的影响如表3-10所示。
表3-10 外观要素对注塑件上分型面选用的影响

②减少或隐蔽浇口痕迹的方法 注塑件成型加工时,注塑模不可能没有浇口,否则塑料熔体无法填充模具的型腔。但是,可以通过改变模具浇口的位置将设置在注塑件敏感表面的浇口改变到隐蔽位置上,从而不影响注塑件外表面的美观性。
[例3-1] 以二次浇口改变浇口在注塑件上的位置,如图3-1所示。图中三种浇口均采用辅助流道的潜伏式二次浇口,有效地将浇口设置在注塑件背面或侧背面上。熔体通过潜伏式浇口和圆弧形或倾斜式或直通式辅助流道流入模具型腔。二次浇口主要设计在矩形推杆上,开模后,辅助流道和浇口的冷凝料与注塑件一起被推杆顶出。注塑件与辅助流道及浇口冷凝料的分离,可以依靠人工进行剥离。

图3-1 以二次浇口改变浇口在注塑件上的位置
[例3-2] 注塑件有“外观”美观性的要求,点浇口痕迹虽较小,但毕竟还是存在着痕迹。为此,可将点浇口放置到注塑件的内表面上,如图3-2所示。分型面Ⅰ—Ⅰ开启时,注塑件外形被打开。注塑件脱模时,在推板10的作用下推件板7将注塑件推落。同时,浇口冷凝料也被拉断。随后由差动顶出机构打开流道板9,即分型面Ⅱ—Ⅱ开启时,动模型芯 5与分浇道型芯6分离。在推板10中的推杆8作用下,可将分浇道中的冷凝料顶出。需要注意的是流道板9打开的距离应能使浇注系统中的冷凝料自动脱落。由于分浇道的长度长,可采用装有流道板电加热圈3的加长型热流道的浇口套。

图3-2 注塑件内表面上设置的点浇口
1—定位圈;2—热浇口套;3—电加热圈;4—定模板;5—动模型芯;6—分浇道型芯;7—推件板;8,11—推杆;9—流道板;10—推板;12—弹簧
③改变浇口的形式 在模具的浇口形式中,辅助浇口和潜伏浇口设置的位置是很灵活的,应避免浇口设置在注塑件比较敏感的表面上,而要将浇口设置在注塑件较隐蔽的表面上。为了确保注塑件“外观”的美观性,也可以改变浇口的形式,见表3-11。
表3-11 改变浇口的形式


④消除注塑件上脱模痕迹的措施 在对注塑件上模具结构成型痕迹进行分析时,有时找不到注塑件上存在的推杆的脱模痕迹。不是注塑模没有脱模机构,而是采用了不会在注塑件上存在脱模痕迹的模具结构。消除注塑件上脱模痕迹的措施如表3-12所示。
表3-12 消除注塑件上脱模痕迹的措施



3.1.7 注塑件上塑料与批量要素的模具结构方案可行性分析法
塑料品种不同,塑料的性能就不同,特别是塑料熔体加热的温度范围、流动充模状态和冷却收缩性能,对模具的结构影响较大。如模具是设置冷却装置,还是设置加热装置。在很多情况下,还可利用塑料的弹性采用强制性脱模的形式。那么,模具是否可以进行强制性脱模,还有模具型腔与型芯尺寸的确定等,这些均取决于注塑件的塑料品种。
注塑件的批量要素取决于注塑件成型加工效率的因素,即决定注塑模结构是采用注塑件的手动抽芯或手动脱模,还是采用自动抽芯或自动脱模。自动抽芯可以是机械形式的抽芯,还可以是气动或液压形式的抽芯。自动脱模可以是机械形式的脱模,也可以是气动形式的脱模。可见注塑件塑料与批量要素是影响模具结构的重要因素。在确定了注塑件塑料与批量要素后,就要根据要素的情况,采用针对要素的措施来确定注塑模的结构方案。
(1)注塑件的塑料要素
塑料要素分析法是针对注塑件上各品种的塑料要素,制订出适应塑料品种的模具结构方案和模具用钢及热处理的分析方法。对于塑料要素,只要在注塑件的图纸上找到塑料的名称或代号就可以了,然后根据该塑料的收缩率就可计算出模具型腔与型芯的尺寸。至于模具是采用冷却装置还是加热装置,一般来说,模温低于成型工艺要求的塑料品种应设置加热装置,而模温高于成型工艺要求的塑料品种应设置冷却装置。在通常情况下,热塑性塑料,模具常常需要进行冷却;热固性塑料压注成型时则必须加热。有些塑料弹性体如橡胶一样具有弹性,如聚氨酯弹性体(T1190PC),就特别适用于强制性脱模。
①模温控制系统的设置原则 模具应根据成型不同的塑料品种,设置模具冷却或加热装置的模温控制系统。
a.对于黏度低与流动好的塑料,如聚苯乙烯(PS)、聚氯乙烯(PVC)、聚乙烯(PE)、聚酰胺(又称尼龙PA)和聚丙烯(PP)等黏度低的塑料,需对模具加装冷却装置。一般情况下是采用温水冷却;为了缩短冷硬固化的时间,也可采用冷(室温)水冷却。
b. 对于黏度高与流动差的塑料,如聚碳酸酯(PC)、聚砜(PSF)、聚甲醛(POM)、聚苯醚(PPO)和氟塑料等黏度高的塑料,为了提高流动性,需要对模具进行加热。对于热性能和流动性好的塑料,但成型厚壁的注塑件(壁厚在20mm以上)时,也必须增设加热装置。
c.对于热固性塑料,模具工作温度应该是150~200℃,因此,必须对模具进行加热。
d.结晶型和非结晶型塑料。由于结晶型塑料具有冷却时施放热量多、冷却速率快、结晶度低、收缩小和透明度高的特点,成型时需要充分冷却。结晶度与注塑件壁厚有关,注塑件壁厚小时冷却快、结晶度低、收缩小和透明度高;反之,注塑件壁厚大时冷却慢、结晶度高、收缩大以及物理性能和力学性能好,所以结晶性塑料必须按照要求控制模温。一般结晶型塑料为不透明或半透明,如聚酰胺(PA)。非结晶型塑料为透明的,如有机玻璃。但也有例外,如结晶型塑料聚(4)甲基戊烯却具有很高透明度,而非结晶型塑料ABS却不透明。
e.对成型注塑件主浇道长的模具,需要采用加深型浇口套和热流道来提高熔体充模的温度,用于改善塑料熔体的流动性。
f.对于流程长的厚壁或成型面积大的注塑件,为了保证塑料熔体的充分填充,应考虑设置加热装置;而对薄壁注塑件,可依靠模具自身的散热而不需要设置冷却装置。
②模具冷却装置的设置原则 模具设置冷却装置的目的:一是防止注塑件脱模变形;二是缩短成型周期;三是使结晶性塑料在冷凝时形成较低的结晶度,以得到柔软性、挠曲性和伸长率较好的注塑件。冷却一般是在型腔和型芯的部位设置通入冷却水的水路,并通过调节冷却水的流量及流速来控制模温。冷却水一般为室温,也有采用低于室温的冷却水来加强冷却的效果。
模具设置冷却装置的考虑因素:首先,应根据模具结构形式,如普通模具、细长型芯的模具、复杂型芯的模具及脱模机构多或镶块多的模具,考虑设置冷却系统;其次,应根据模具的大小和冷却面积因素,考虑设置冷却系统;第三,应根据注塑件的形状和壁厚因素,考虑设置冷却系统。
冷却系统的设计对注塑件质量与成型效率有着直接的关系,尤其在高速和自动成型时更为重要。冷却水道的布置方式如表3-13所示。
表3-13 冷却水道的布置方式



③无浇道和热浇道浇注系统的设计原则 节省塑料,有利于高速自动成型并缩短成型周期,提高生产效率和便于操作。在注塑模设计时,可以考虑采用无浇道和热浇道结构,以保证浇注系统的熔体处于常熔融状态。使得在每一次成型注塑件之后,不必再设置用于取出浇道中的冷凝料及清理浇口的工步。
a.对于能够应用无浇道和热浇道的塑料及其要求。该结构形式很大程度上与塑料成型特性有关。各种塑料适应无浇道和热浇道的情况如表3-14所示。
表3-14 各种塑料适应无浇道和热浇道的情况

影响注塑模无浇道和热浇道结构的因素,取决于塑料的热性能和流动性。用于无浇道和热浇道结构的塑料有PE、PP、PS和ABS,而较少采用PVC、PC和POM等热敏性塑料。对能够适用于无浇道和热浇道结构的塑料,应具有下列要求。
• 成型温度范围广,在低温下也有较好的流动性,而在高温下又有较好的稳定性,即便是在低温下也易成型。
• 熔体在低温时的流动性对压力敏感,即不加压力时不流涎,略加点压力就能够流动。
• 导热性能好,即熔融的塑料能快速地将热量传给注塑模并快速冷却。
• 使成型后的注塑件能够迅速地从注塑模中脱模,塑料的热变形温度要高。
• 塑料比热容低,就是熔融容易而凝固也容易。
b.无浇道浇注系统的采用。因为过长的浇道在熔体料流接触室温注塑模的距离长,熔体降温过大后,会降低熔体的流动性,同时会造成注塑件的各种缺陷。为了避免注塑件各种缺陷的产生,当主浇道的长度超过60mm时,应采用无浇道或热延长喷嘴等措施。
c.井式喷嘴。井式喷嘴是把进料的浇口制成蓄料井坑的形式,是采用点状浇口的另一种形式。
• 井式喷嘴浇注的特点。蓄料井坑中的塑料在注射时,井坑中心的塑料保持着熔融的状态,而接触到注塑模外层的塑料,由于受到冷却作用成为半熔凝状态。这种半熔凝状态的塑料起到了隔热的作用,使得注塑机的喷嘴在不离开注塑模浇道套的情况下就可以连续进行注射成型。这种喷嘴常用于单型腔注塑模。
• 井式喷嘴的形式。可分成一般形式、延长形式、弹簧形式和扩面积形式四种,见表3-15。
表3-15 井式喷嘴的形式

④延长喷嘴的设计 延长喷嘴是为了使注塑机的喷嘴能延长至直接接触到注塑模型腔的一种特殊喷嘴,见表3-16;其延长部分代替了浇道,对于防止蓄料井熔料的凝固和浇口的堵塞,要优于井式喷嘴。
表3-16 延长喷嘴

(2)注塑件的批量要素
批量要素分析法是针对注塑件上各种批量要素,制订出适应注塑件批量模具结构方案的分析方法。注塑件批量要素是影响模具用钢的品种和热处理以及模具结构的因素之一。注塑件批量不同,对模具制造的成本和寿命的要求就不同。因此,对模具用钢的品种和热处理,以及模具结构的生产效率的要求也不同。
①注塑件生产的批量 注塑件生产批量可分成小批量、中批量、大批量和特大批量。对于生产大批量和特大批量注塑件的模具,尽量采用群腔模具及两套动模的群腔模具,以实现高生产效率。生产小批量注塑件模具型腔一般采用单腔,即使是小型注塑件,最多也只采用四腔的模具。注塑件批量与模具用钢、热处理及模具结构之间的关系详见表3-17。
表3-17 注塑件批量与模具用钢、热处理及模具结构之间的关系

②注塑件批量要素与模具结构 注塑件批量不同,模具结构就不同。注塑件批量要素与模具结构之间的关系详见表3-18。
表3-18 注塑件批量要素与模具结构之间的关系


③型腔数量取决于模具的结构和注塑件“批量”要素 有的模具型腔数量因模具抽芯的结构限制,只能是一模一腔或一模两腔。但就注塑件“批量”要素而言,总的原则是:小“批量”的注塑件只能是一模一腔,中等“批量”的注塑件可以是一模两腔到一模四腔,大“批量”的注塑件可以是一模四腔以上。因为模腔越多,所需模架面积就越大,模腔之间的间隔尺寸就越小,制造精度就越高,模具制造成本也就越高。因此采用多模腔的小“批量”注塑件,其模具制造成本高。
④注塑件“批量”要素与模具造价及制造周期 通过对注塑件“六要素”和注塑模结构方案的“三种分析方法”,就可以确定注塑模的结构、模具腔数、模具用钢和热处理。这样注塑模的结构设计、零部件制造工艺及模具材料明细表都能制订出来,模具的造价及制造周期也就能估算出来。模具制造价格的精确计算要在模具的零部件设计和工艺规程编制好之后,根据模具零件的毛坯的体积,计算模具零件重量来确定零件材料的价格;根据零件工艺确定零件的工时和制造价格与工序外协价格,以及标准件采购价格;所有零件价格汇总后,包括模具装配和试模在内的价格就是模具制造的成本。模具制造商就能据此与模具的采购商签订详细的商业合同。当然,模具的造价及制造周期也是影响模具结构方案的因素,但本书不将它们作为影响模具结构方案的要素,其原因是模具的复杂与简易程度可以通过“六要素”和“三种分析方法”确定下来,保证了注塑模结构方案、模具的造价及制造周期制订的科学性与严谨性。若将模具的造价及制造周期定为影响模具结构方案的要素,就容易出现为了利益制假,为了商业利益随便改动模具结构方案和偷工减料的行为。
注塑件的“塑料”要素不同,模具温控系统和喷嘴的结构及模具结构就不同。注塑件的“批量”要素不同,不仅模具的型腔数量和模具的结构不同,模具用钢和热处理也有所不同。所以要设计好注塑模,注塑件的“塑料与批量”要素在注塑件形体分析时,也是不能缺少的内容之一。