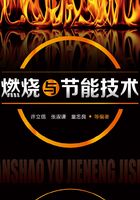
第二章 燃烧设备及其节能燃烧新技术
第一节 概 述
燃烧是人类获取能源的主要途径,世界上80%以上的能源都来自于燃烧。而人类通过燃烧获得能量的同时,也产生了大量温室气体和酸性气体,这些气体是造成当今生态环境恶化的重要影响因素。
随着煤、石油及天然气等矿物质能源的不断减少,如何有效和环保地利用现有能源已成为世界普遍关注的大事。
现在,我国已经将保护环境、造福人民作为一项基本国策。而公民的环保意识也是促使环境向有利方向转化的一支强大的力量。那么,当今我们对环境生态问题的节能燃烧新技术感知度和关注度如何呢?此次,我以“公民的环境生态意识及其测评研究”为主题,对话了一位六零后和一位九零后,从几个方面初步了解公民的环境生态意识。并且通过查阅相关的文献资料对公民的环境生态意识及其测评研究有了更加深刻地了解。
一、辉焰燃烧
当煤粉进入分解炉后,悬游于气流中,经预热、分解、燃烧发出光和热,形成一个个小火星,无数的煤粉颗粒便形成无数的迅速燃烧的小火焰。这些小火焰浮游布满炉内,从整体看,看不见一定轮廓的有形火焰。所以分解炉中煤粉的燃烧并非一般意义的无焰燃烧,而是充满全炉的无数小火焰组成的燃烧反应。有人把分解炉内的燃烧称为辉焰燃烧,这主要指分解炉内将料粉或煤粉均匀分散于高温气流中,使粉料颗粒受热达一定温度后,固体颗粒发出光、热辐射而呈辉焰。但并不能看到有形的火焰而只见满炉发光。分解炉内无焰燃烧的优点是燃料均匀分散,能充分利用燃烧空间,不易形成局部高温。燃烧速率较快,发热能力较强。
由于分解炉内的煤粉为无焰燃烧,不会形成高温集中的“火焰”,因而煤只能靠迅速分散与炉内气流密切接触,得到所需的氧气和着火的温度,才能较好地着火和燃烧。因此煤粉分散性不好或在炉内分布不均是导致煤不能着火或仅部分着火的主要因素。
1. 分解炉内的温度分布
煤粉喷燃温度可达1500~1800℃,分解炉内气流温度之所以能保持在800~900℃之间,主要是因为燃料与物料混合悬浮在一起,燃料燃烧放出的热量,立即被料粉分解所吸收,当燃烧快,放热快时,分解也快;相反,燃烧慢,分解也慢。所以分解反应抑制了燃烧温度的提高,而将炉内温度限制在略高于CaCO3平衡分解温度20~50℃的范围。
①分解炉的轴向及平面温度都比较均匀。
②炉内纵向温度由下而上逐渐升高,但变化幅度不大。
③炉的中心温度较高,边缘温度较低。主要是炉壁散热、中心料粉稀、边缘浓所致。
2. 分解炉内的燃烧速率
分解炉内的燃烧速率,影响着分解炉的发热能力和炉内的温度,从而影响物料的分解率。燃烧速率快,放热多,炉内温度就高,分解速度将加快。反之,分解率将降低。因此加快燃料燃烧的速度,是提高分解炉效能的一个重要问题。
分解炉内的燃烧温度通常在860~950℃,燃烧过程的性质处于低温化学动力学控制范围与高温扩散控制范围的交界,因此,影响这两种过程的影响因素,均对分解炉内的燃烧速率有重要影响。其中影响燃烧速率的化学动力学因素有燃料的种类、性质、温度、压力及反应物浓度等,影响扩散燃烧速率的主要因素有炉气的紊流程度、燃料与气流的相对速度、燃料的分散度等。
为适当加快燃烧速率,控制好炉温,一般应注意下列几个方面。
①选择适当的燃料加入点并分成几点加入。
②适当控制燃料的雾化粒度或煤粉细度。
③选择适当的燃料品种,例如煤粉中含有适当的挥发物,使挥发物与焦炭先后配合燃烧,以达到好的热效应。
④选择适当的一次、二次风速以及合适的加料点的位置。
⑤调节燃料加入量以改变燃烧的空气过剩系数。
3. 分解炉的容积热负荷
一些分解炉的容积热负荷见表2-1。由表可见,各类分解炉的容积热负荷相差较大,它与分解炉中的燃烧速率、气体速度及炉的结构有关。
表2-1 一些分解炉的容积热负荷

4. 分解炉内的传热
在分解炉内,由于料粉分散在气流中,燃烧放出的热量在很短时间内被物料吸收,既达到高的分解率,又防止了过热。
(1)分解炉内传热的特点 分解炉内的传热方式主要为对流传热,其次是辐射传热。炉内燃料与料粉悬浮于气流中,燃料燃烧,燃料中的潜热把气体加热至高温,高温气流同时以对流方式传热给物料。由于气固相充分接触,传热速率高。分解炉中燃烧气体的温度在900℃左右,其辐射放热性能没有回转窑中燃烧带的辐射能力大。然而由于炉气中含有很多固体颗粒,CO2含量也较多,增大了分解炉中气流的辐射传热能力,这种辐射传热对促进全炉温度的均匀极为有利。
(2)悬浮态传热 分解炉内传热最主要的因素是传热面积大大增加,料粉与气流充分接触,其传热面积即为料粉的比表面积。因此,气流与料粉的温度差很小,使料粉的升温(如750~900℃)瞬间即可完成。也是由于这个原因,燃料放出的大量热量,能迅速地被碳酸盐分解吸收而限制了气体温度的提高。传热(及传质)速率的提高,使生料的碳酸盐分解过程由传热、传质的扩散控制过程转化为分解的化学动力学控制过程。这种极高的悬浮态传热、传质速率与边燃烧放热、边分解吸热共同形成了分解炉的热工特点。
(3)分解炉内的气体运动 分解炉对气体运动的要求是分解炉内的气流具有供氧燃烧、浮送物料及作传热介质的多重作用。为了获得良好的燃烧条件及传热效果,要求分解炉各部位保持一定的风速,以使燃烧稳定;物料悬浮均匀;为使在一定炉体容积内物料滞留时间长些,则要求气流在炉内呈旋流或喷腾状态,以延长燃料燃烧及物料分解的时间;为提高传热效率及生产效率又要求气流有适当高的料粉浮送能力,在加热分解同样的物料量时,以减少气体流量,缩小分解炉的容积,并提高热的有效利用率。在满足上述工艺热工要求的条件下,要求分解炉有较小的流体阻力,以降低系统的动力消耗。概括来说,对分解炉气体的运动有如下要求。
①适当的速度分布。
②适当的回流及紊流。
③较大的物料浮送能力。
④较小的流体阻力。
分解炉要求一定风速的目的如下。
①保持炉内有适当的气体流量,以供燃料燃烧所需的氧气,保持分解炉的发热能力。
②使喷入炉内的燃料与气流良好混合,使燃烧稳定、完全。
③使加入炉中的物料能很快分散,均匀悬浮于气流中,并使气流有较大的浮送物料的能力。
④使气流产生回旋运动,使其中的料粉及燃料在炉内滞留一定时间,使燃烧、传热及分解反应达到一定要求。
二、燃气燃烧器结构分析与特点
燃气燃烧器具有热效率高、安全性能好、可靠性强、自动化程度高、操作简单、维护方便、噪声低等优点。燃气燃烧器分为:扩散式燃气燃烧器;部分预混(大气式)燃气燃烧器;动力式燃气燃烧器。其中大气式燃烧又分为自然引射式和鼓风式。
1. 燃气燃烧器特点
①热效率高:能适应压力波动,自行调节一次配风(即燃气压力大,吸入一次风多;燃气压力小,吸入一次风少),燃烧充分,热效率高。
②安全性高:该燃烧器配备小火。锅炉启动时,先点小火,当小火正常稳定燃烧时,自控系统才打开主燃气阀门,燃料才能进入锅炉正常燃烧,不会产生爆燃现象。
③燃料适应性强:该种燃烧器只需更换少量部件就能适用于天然气、液化石油气、煤气、液化石油混合气以及其他类燃气。
2. 燃气燃烧器燃气阀门组
本锅炉可直接接入低压力燃气管道,不需要调压站。其燃气阀门为低压阀门。燃气阀门由三部分组成:
①手动阀门;
②24V电动阀门;
③燃气压力调节阀(某些型号锅炉电动阀门与压力调节阀门为同一个阀)。
可根据用户要求另外设置燃气最高压力开关、燃气最低压力开关;燃气压力调节阀要求阀前压力127~279.4mmH2O,阀门压力不低于88.9mmH2O。液化石油气阀门压力要求279.4mmH2O。
三、燃气燃烧器断气保护装置
燃气管道上设置有最高压力开关和最低压力开关,当断气或燃气压力降低到某一值时,最低压力开关启动,系统自动关闭;当燃气压力过高时,最高压力开关启动,系统自动关闭。燃气燃烧器断气保护装置是如燃气燃烧器一般保持烧结工序的热量平衡(见图2-1)。

图2-1 烧结工序的热量平衡
四、富氧燃烧器
通常空气中氧的含量为20.93%、氮为78.1%及少量惰性气体等,在昆明地区空气中氧的含量约为20.8%,在燃烧过程中只占有空气总量的1/5左右的氧参与燃烧,而占空气总量约4/5的氮和其他惰性气体非但不助燃,反而将随烟气带走大量的热能。而含氧量大于21%的富氧空气参与燃烧给燃烧提供了足够的氧气,使可燃物充分燃烧,减少了固体不完全燃烧的排放,减少了氮和其他惰性气体随烟气带走的热能。将具有明显的节能和环保效应。
变压吸附富氧技术是非常适合各种锅炉、窖炉做助燃用途的高新技术,它具有流程简单、体积小、自身能耗低、使用寿命长、投资较少等特点,被工业发达国家称之为“资源的创造性技术”。
1. 富氧燃烧分析
助燃空气中氧浓度越高,燃料燃烧越完全,但富氧浓度太高,会导致火焰温度太高而降低炉膛受热面的寿命,同时制氧投资等费用增高,综合效益反而下降。因此国内外研究均表明,助燃空气富氧浓度一般在26%~30%时为最佳。
(1)据测试氧含量增加4%~5%,火焰温度可升高200~300℃。火焰温度的升高,促进整个炉膛温度的上升,炉膛受热物质更容易获得热量,热效率大幅提高。
(2)燃料在空气中燃烧与在纯氧中的燃烧速率相差甚大,如氢气在空气中的燃烧速率最大为280cm/s,在纯氧中为1175cm/s,是在空气中的4.2倍,天然气则高达10.7倍。富氧助燃,可以使燃烧强度提高、燃烧速率加快,从而获得较好的热传导,使燃料燃烧得更完全。
(3)燃料的燃点温度不是一个常数,它与燃烧状况、受热速度、富氧用量、环境温度等密切相关,如CO在空气中为609℃,在纯氧中仅388℃,所以用富氧助燃能降低燃料燃点,提高火焰强度、减小火焰尺寸、增加释放热量等。
(4)用普通空气助燃,约4/5的氮气不但不参与助燃,还要带走大量的热量。一般氧浓度每增加1%,烟气量约下降2%~4.5%,从而能提高燃烧效率。
(5)如用普通空气助燃,当炉膛温度为1300℃时,其可利用的热量为42%;而用26%的富氧空气助燃时,可利用热量为56%,热量利用率可增加14%。
(6)排烟温度每降低12~15℃,可降低排烟热损失约1%,用富氧代替空气助燃,可减少一次风量,降低了空气的过剩系数,减少了排烟量,降低了排烟热损失。
2. 节能燃烧器
节能燃烧器是在普通燃气灶具的基础上,大胆创新发明的一种新型燃烧器(见图2-2)。防锈材料,小巧玲珑,重量只有传统灶头的十分之一,大大降低了自身吸热和散热,减少了传统铸铁炉芯炉盘的导热环节,降低了热能的大量损耗。
①减少自身吸热 传统灶具燃烧盘和总成采用铸铁铸造,火焰又是从燃烧盘里射出,自身消耗大量热量(停止燃烧后,滴上几滴水到发热盘上,马上就变成水蒸气,并且发出“哧哧”的响声);而节能燃烧器,采用悬浮式燃烧原理,灶体自身不吸热,热损失几乎为零。

图2-2 一种新型燃烧器
②缩短了火焰的燃烧距离 传统灶具的火焰从燃烧盘喷射到锅底有一定距离,有的长达5cm以上。长距离的燃烧,热能通过空气流失,到达锅底后大打折扣,致使室温升高;节能燃烧器则是将小拇指粗的火焰喷发至锅底后开始散开,火焰到锅底的距离不超过1.5cm,距锅边不超过1cm,通过空气散热很少,能量利用率高,燃烧时厨房室温变化不大。
③控制燃气输出量 原灶具有两个出气风口,属双管供气;而节能灶头只需一个孔,将另一个孔堵上。因为燃烧充分,替代了原灶头的外圈火焰,燃烧时间也相对缩短,所以不用燃气表检测,功效也能一目了然。
a.后混(普通炉头),不节能。
b.预混型(先混合后燃烧),节能20%以上。
c.预混型加后混型,节能25%以上。
d.预混预处理加后混型,节能30%以上。
3. 技术说明
①燃气预混技术,使燃气与氧气按一定比例充分混合后燃烧。
②微火种技术:小气量火种,一点就着,不易熄灭。相当于防空烧。
③仿氧焊切割火焰调节技术:火焰形成倒梯形仿氧焊切割火焰形状均匀地分布于锅底,提高锅底对热能的吸收。
4. 节能燃烧器适用范围
节能燃烧器适用于酒店、餐馆、院校、工厂企业等行业领域,以及对原有传统炉灶节能工程技术改造安装,主要用于:小炒炉、大炒炉、汤炉、烤炉、蒸炉、蒸柜炉灶的安装。其也可适用于天然气、油制气、液化气各种燃气炉具的安装。