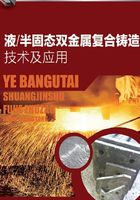
前言
复合材料是20世纪材料科学方面的一大进展,其中铸造铁基复合材料以其独特的制造工艺、优越性能及较低的成本,引起了人们的关注和重视。目前,金属复合材料的制备方法较多,主要应用有表面堆焊法、轧制复合法、连续铸造法、铸造复合法等。其中,铸造复合法制备的产品性能稳定,成本相对较低,一直受到耐磨材料领域的广泛关注。
20世纪80年代中期,焊接工艺和铸造复合法制备的金属复合材料零件被广泛应用,以满足复杂工况和设备对产品的特殊需求。双金属复合铸件发挥了两种材质的优点,有着良好的综合性能和较高的使用寿命,适应工况能力强,成本也较为低廉。随着双金属复合工艺的发展及材料性能的提升,拓展了双金属复合零部件的应用空间,在矿山机械中的应用较为常见,主要有各式破碎机用边护板、衬板、反击板、颚板等抗磨零部件,铸造复合工艺在各类耐磨产品上的应用越加广泛。
本书在传统双液铸造复合技术的基础上,采用了“液/半固态”双金属铸造复合技术,针对复合板材的大平面冶金结合、较薄的使用厚度等特定工况需求,利用基底材质在冷却介质作用下形成较大的温度梯度,促使金属液在凝固过程中趋于层状凝固,当基底材质上表面处于半固态时浇注耐磨层金属,实现两种金属的冶金结合。液/半固态双金属铸造复合板不但可以实现两种材质大面积平面冶金复合,而且能有效避免因表面完全凝固后出现氧化夹杂难以去除的弊端,同时可以有效解决焊接方法出现的焊接残余应力、宏观裂纹及成分不均匀等问题,进而避免综合力学性能受到影响,提高耐磨板的使用寿命。
本书主要通过对液/半固态双金属铸造复合板温度场的分布、凝固厚度的定量分析,比较了不同冷却介质对基底金属凝固过程温度梯度和凝固速度的影响,为确定耐磨层金属液浇注时间提供了依据。本书研究了液/半固态双金属铸造复合板界面层及邻近区域的组织结构与成分分布规律,揭示了复合界面和近界面精细结构及界面层组织的形成机制与演化规律,实现了复合组织的有效调控。利用基底金属重熔区熔化厚度温度场模型,确立浇注温度及浇注时间与重熔层厚度关系。根据工况条件下铸造复合材料的界面、组织与性能演化关系,实现耐磨复合薄板结构、成分及性能设计。
液/半固态双金属铸造复合工艺制备耐磨薄板技术可显著节约资源与能源。铸造复合耐磨板相对于其他方法有着优良的冶金质量,避免了微观裂纹源的产生,直接杜绝了耐磨层宏观裂纹的产生,而且复合板可以通过热处理工艺进一步提高力学性能,并能进行热整形,对磨粒直径和流向无特殊要求。实际生产中可以根据需要一次铸造成所需形状,避免了按需要形状切割和加工导致的板材浪费。液/半固态双金属铸造复合耐磨板具有较高的使用寿命和减少装拆机更换零配件时间的特点,可大幅提高生产效率,为耐磨复合板的生产与应用提供了新途径。
本书为笔者多年的研究成果。本书得到了金属耐磨材料及表面技术教育部工程研究中心的大力支持;得到了国家自然科学基金项目“双液异种金属复合界面凝固行为及梯度复合层形成机理研究(项目编号:51371090)”和黑龙江省教育厅项目“双液铸造双金属复合层凝固行为及形成机制的研究(项目编号:2016-KYYWF-0553)”的资助。
由于时间紧迫和水平有限,书中不当之处难免,恳请读者批评指正。
朱永长