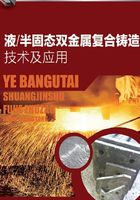
1.4 双液双金属铸造复合技术现状
目前矿山用金属耐磨材料多采用钢铁及其合金材料,在复杂工况下,由于耐磨性及抗冲击性能较差,导致材料的使用寿命较低[66~69]。双液铸造复合金属耐磨材料,为传统金属材料在耐磨工业领域的应用提供了新的制备工艺手段。但是,由于双液双金属复合界面形成机制尚未明确[70~73],使得该技术的应用受到极大约束。
双液异种金属复合材料的界面是应力传递的中枢,在满足使用要求的前提下,复合界面的厚度、成分过渡及组织结构的演化,直接影响材料的综合性能[74~76]。只有揭示复合材料界面、组织与性能的关联机制,才能真正体现复合材料的优势互补,优化异种金属复合界面结构设计。显然,如何调控双液金属复合界面及近界面的组织、成分、形貌,揭示双液金属复合材料的复合界面形成及作用机制,建立行之有效的复合材料组分设计准则和有效调控双液金属复合材料的结构与性能,成为这个领域非常重要且具有挑战性的一项前沿课题。
双液双金属复合过程中高温重熔区的存在易于实现异种材质的冶金结合,同时也能够有效地扩大异种金属材料的复合面积,解决传统单一金属材料的应用瓶颈[77~79]。然而,异种金属间的复合界面的结合性能严重地影响到复合材料的使用寿命,在保证双液金属复合铸造材料界面实现良好的冶金结合的前提下,调控界面层的冶金结合质量和揭示界面层的形成机理成为研究的焦点。在双金属铸造复合材料制备过程中,无论哪种复合方法都存在三个关键问题,分别为材质相容性、界面结合强度和复合准则[80~82]。
1.4.1 材质相容性
金属复合材料制备方法是建立在两种或多种金属材料能够实现复合的基础之上,因而材料之间的结合性能和发挥不同部位的应用功能是复合材料设计成功的关键,具体应用与研究涉及不同材料制备金属复合材料时的相容性关系。
(1)材质相容性
金属复合材料至少是两种材料间的复合,既要考虑到耐磨材料的高硬度和一定程度的抗冲击韧性,又要顾及基体材料具有适当的硬度和较好的断裂韧度。实际应用研究中,考虑到材质的相容性,硬度较高的金属主要有铬系耐磨铸铁、硼系铸铁和硬质合金等,用来充当耐磨层材料;硬度相对较低,但具有较好断裂韧度的金属材料主要有低碳钢、中碳钢、低合金钢和高锰钢等,用来充当基体材料[83,84]。根据实际生产工况条件,选择合适的耐磨材料和基体材料制备金属复合耐磨产品,要发挥材料的最佳力学性能,就要分析材料功能之间的相容性,同时定量表征相容性也需要相应的手段,目前采用显微硬度或抗拉强度作为功能相容性的主要评价指标[85]。
(2)工艺相容性
经过生产全过程后,双金属复合材料的性能应满足使用要求,特别是耐磨材料工作面,不能因铸件整体热处理等高温过程而丧失其高抗磨性[86]。在工作面和基体材料同步工艺处理后需要给出两者工艺相容性的定量评价[87],具体的定量关系还有待于深入研究。
(3)工艺性能相容性
金属复合材料内存在着化学成分、热膨胀系数差异等特征,可以采用热膨胀系数差综合表征材料内部的差异性。在复合铸造产品中表现的热膨胀系数差越大,相应的产品出现的开裂现象越严重[88,89]。现有研究表明,不同的金属材料在材质相容性上已形成一定的材质匹配模式。通常使用韧性好的低碳钢、中碳钢或低合金钢充当基体材料;工作端则选用硬度较高和抗磨性较好的高铬铸铁、硬质合金、髙硼铸铁和高锰钢等[90]。这种匹配模式主要是建立在应用研究基础上,更深层的相容性问题还有待深入研究。
1.4.2 界面结合强度
复合材料的界面结合强度是衡量相关工艺可行性的重要标志,通常以实现界面冶金结合来界定复合质量,实际应用中可用于复合材质的种类较多,耐磨工况也较为复杂,如何评定最佳界面结合状态,现有研究尚无统一标准[91]。
目前,判断复合材料是否结合良好,评定界面结合强度,主要是依据界面间的冶金结合或机械结合状态进行分析的,而且实际生产中获得的产品通常是冶金结合和机械结合的产物。界面的结合强度通常采用形成冶金结合区域的总面积与界面面积的比值来表征,并定义为冶金结合率。不同的工况条件下应用的复合产品,可根据实际情况给定不同的冶金结合率临界值,用以表征相应复合产品的界面结合良好。按照冶金结合率大小可以具体分为三类。
① 机械结合为主,冶金结合为辅,主要特征为界面平直清晰,观察不到过渡层,可看到界面呈现凹凸变化,冶金结合率相对较低;
② 冶金结合为主,机械结合为辅,主要特征是界面区域形成了较为明显的元素扩散,冶金结合率大于一定的需求临界值;
③ 完全冶金结合,主要特征是界面区域元素扩散充分,可以观察到完整的过渡层。对于冶金结合率的判断是建立在实际生产应用基础上的,结果往往带有更多的主观性,给出简便直观的定量表征方式,更好地判断界面结合强度仍需要更为深入的研究。
通过界面结合率的给定,可以在一定程度上表征界面结合状态,如果能引入力学测试标准,将会更好地对界面结合状态进行定量表征。将剪切强度引入固-液复合界面进行力学性能评定,目前还没有统一标准,而且研究者将固-液界面结合强度测试方法用来直接表征液-液复合界面。一些科研人员按照自身的科研条件和表征目的,采用了不同的力学测试方法。刘耀辉[92]等制备的45号钢/高速钢铸造复合材料,其界面剪切强度为50~300MPa。刘清梅[93]等制备了45号钢/高铬铸铁双金属复合材料,测量了45号钢/高铬铸铁复合界面剪切强度范围为80~320MPa。
1.4.3 复合准则
经典的复合材料中对复合工艺已经进行了较为系统的研究,同时也形成了相应的复合准则。但对于双液双金属复合材料而言,也应当有这样的复合准则指导应用研究与生产实践。因此,建立双液双金属复合准则,可以为双液铸造复合材料设计过程提供可靠依据[94]。如何表示双液双金属复合材料复合准则将是值得研究的一个重要课题[95]。
1.4.4 存在的问题
多年来,关于双液铸造成型方法进行了大量的研究,提出了不同的成型方法和观点[96],思路主要集中在定量浇注法上,通过在型腔内部开设溢流口来控制先浇入的金属液质量,保证后浇入的金属液充型平稳且与第一种金属不发生混料,为双液铸造复合材料提出了一个可行的成型技术[97]。只有利用该技术制备的复合耐磨产品厚度≥50mm时,才能确保相关铸件界面的冶金复合质量和较好地控制界面氧化夹杂量,但在较薄的耐磨复合铸件上的应用受到了严重制约。
目前,双液铸造复合工艺仍然比较复杂,主要在于金属液浇注时机很难掌握,没有切实可行的量化研究思路与具体的参数依据作为指导,尚未形成成熟的理论支持,多凭经验生产。大多数研究者对双液铸造金属复合材料界面结合机制都是直接按照“固-液”复合方法分析界面形成机理的。主要问题如下。
① 传统双液铸造复合技术在大平面耐磨薄板的制备与应用研究仍为空白;
② 双液铸造复合耐磨产品基底材质在完全凝固末期,为了保证基底材质的表面重熔,后注入的耐磨层金属液量较大,导致界面结合区混料严重,而且基底材质在前期凝固过程中表面形成的氧化夹杂容易滞留在界面区域,恶化耐磨产品使用性能。