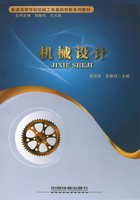
3.2 磨损
3.2.1 磨损对零件的影响
摩擦副表面间的摩擦造成表面材料逐渐损失的现象称为磨损。零件表面磨损后不但会影响其正常工作,如齿轮和滚动轴承的工作噪声增大,承载能力降低,同时还会影响机器的工作性能,如工作精度、效率和可靠性降低,噪声与能耗增大,甚至造成机器报废。通常,零件的磨损是很难避免的。但是,只要在设计时注意考虑避免或减轻磨损,在制造时注意保证加工质量,而在使用时注意操作与维护,就可以在规定的年限内,使零件的磨损量控制在允许的范围内,就属于正常磨损。另一方面,工程上也有不少利用磨损的场合,如研磨、跑合过程就是有用的磨损。
3.2.2 磨损的过程
工程实践表明,机械零件的正常磨损过程大致分为三个阶段:初期磨损阶段(磨合磨损阶段)、稳定磨损阶段和剧烈磨损阶段,如图3-7所示。

图3-7 机件的磨损量与工作时间的关系(磨损曲线)
1.初期磨损阶段
如图3-7所示,机械零件在初期磨损阶段的特点是在较短的工作时间内,表面发生了较大的磨损量。这是由于零件刚开始工作时,表面微凸出部分的曲率半径小,实际接触面积小,造成较大的接触压强,同时曲率半径小也不利于润滑油膜的形成与稳定。所以,在开始工作的较短时间内磨损量较大。
2.稳定磨损阶段
经过初期磨损阶段后,零件表面磨损得很缓慢。这是由于经过初期磨损阶段后,表面微凸出部分的曲率半径增大,高度降低,接触面积增大,使得接触压强减小,同时还有利于润滑油膜的形成与稳定。稳定磨损阶段决定了零件的工作寿命。因此,延长稳定磨损阶段对零件工作是十分有利的。工程实践表明,利用初期磨损阶段可以改善零件表面性能,提高零件的工作寿命。
3.剧烈磨损阶段
零件在经过长时间的工作之后,即稳定磨损阶段之后,由于各种因素的影响,磨损速度急剧加快,磨损量明显增大。此时,零件的表面温度迅速升高,工作噪声与振动增大,导致零件不能正常工作而失效。在实际中,这三个磨损阶段并没有明显的界限。
在机械工程中,零件磨损是一个普遍的现象。尽管,人类已对磨损开展了广泛的科学研究,但是从工程设计的角度看,关于零件的耐磨性或磨损强度的理论仍然不十分成熟。因此,本书仅从磨损机理的角度对磨损的分类作介绍。
3.2.3 磨损的分类
根据磨损的机理,零件的磨损可以分为黏附磨损(胶合)、磨粒磨损、疲劳磨损(点蚀)、流体磨粒磨损、流体侵蚀磨损(冲蚀磨损)、机械化学磨损(腐蚀磨损)和微动磨损(微动损伤)。
1.黏附磨损(胶合)
当摩擦表面的不平度凸峰在相互作用的各点产生结点后再相对滑移时,材料从运动副的一个表面转移到另一个表面,便形成了黏附磨损。例如:滑动轴承中的“抱轴”和高速重载齿轮的“胶合”现象。在黏附磨损中同类摩擦副材料比异类材料容易黏附;脆性材料比塑性材料抗黏附能力高,在一定范围的表面粗糙度越高抗黏附能力越强,此外黏附磨损还与润滑剂、摩擦表面温度及压强有关。
2.磨粒磨损
落入摩擦副表面间的硬质颗粒或表面上的硬质凸起物对接触表面的刮擦和切削作用造成的材料脱落现象,称为磨料磨损。磨粒磨损造成表面呈现凹痕或凹坑。硬质颗粒可能来自冷作硬化后脱落的金属屑或由外界进入的磨粒。加强防护与密封,做好润滑油的过滤,提高表面硬度可以增加零件耐磨粒磨损的能力。
3.疲劳磨损(点蚀)
受变应力的摩擦副,在其表面上形成疲劳点蚀,使小块金属剥落,这种现象称为疲劳磨损。常发生在滚动轴承、齿轮、凸轮等零件上。影响疲劳磨损的因素主要有摩擦副材料组合、表面光洁程度、润滑油黏度以及表面硬度等。
4.流体磨粒磨损和流体侵蚀磨损(冲蚀磨损)
流体磨粒磨损是流动的液体或气体中所夹带的硬质物体或硬质颗粒冲击零件表面所引起的机械磨损。利用高压空气输送型砂或高压水输送碎石时,管道内壁所产生的机械磨损是实例之一。
流体侵蚀磨损是指由液流或气流的冲蚀作用引起的机械磨损。近年来,由于燃气涡轮机的叶片、火箭发动机的尾喷管这样一些部位的破坏,才引起人们对这种磨损形式的特别注意。
5.机械化学磨损(腐蚀磨损)
在机器工作时,摩擦副表面会与周围介质接触,如有腐蚀性的液体、气体、润滑剂中的某种成分,发生化学反应或电化学反应形成腐蚀物造成的磨损,称为腐蚀磨损。腐蚀磨损过程十分复杂,它与介质、材料和温度等因素有关。
6.微动磨损(微动损伤)
微动磨损是指摩擦副在微幅运动时,由上述各磨损机理共同形成的复合磨损。微幅运动可理解为不足以使磨粒脱离摩擦副的相对运动。微动作用不仅要损坏配合表面的品质,而且要导致疲劳裂纹的萌生,从而使零件的疲劳强度急剧降低。
3.2.4 减少磨损的主要方法
为了减少磨损带来的危害,可以参考以下方法:
(1)选用合适的润滑剂和润滑方法,用液体摩擦取代边界摩擦。
(2)按零部件的主要磨损类型合理选择材料。易产生黏附磨损时,不要选择互溶性强的材料作摩擦副的材料;易产生磨料磨损时,一般应选择硬度较高的材料。
(3)合理选择热处理和表面处理方法,如表面淬火和表面化学处理(渗碳,渗氮等)及喷涂、镀层、变形强化等。
(4)适当降低零件表面粗糙度值。
(5)用滚动摩擦代替滑动摩擦。
(6)正确进行结构设计,使压力均匀分布,有利于表面膜的形成和防止外界杂物(如磨粒、灰尘)进入摩擦面等。
(7)正确维护、使用,加强科学管理,采用先进的监控和测试技术。