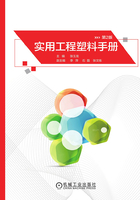
第二节 改性技术
聚碳酸酯可与聚酯类树脂(如PET、PBT等)、丙烯腈-丁二烯-苯乙烯共聚物(ABS)、(改性)聚苯乙烯(PS)、聚甲醛(POM)、聚氨酯(PU)、某些丙烯酸树脂等均匀熔混。
聚碳酸酯虽可与聚氯乙烯(PVC)均匀熔混,但在聚碳酸酯熔融温度下PVC会发生显著降解。聚碳酸酯可与少量低密度聚乙烯(LDPE)熔混均匀;也可与氯化聚醚部分熔混,类似于橡胶改性PS的情况。
聚碳酸酯与聚丙烯(PP)、高密度聚乙烯(HDPE)及聚酰胺(PA)熔混不均匀,有严重分层现象,但似乎不会引起聚碳酸酯降解。例如,可把PA与PC熔混挤出的条撕成许多很细的长丝,折曲多次也不易断裂。
聚碳酸酯除可以进行共混合金改性外,还可进行增韧改性、填充增强改性、纳米改性等以提高其综合性能。
一、增韧改性
(一)光盘级PC的增韧改性
1.选材
1)光盘级PC:相对分子质量18000,密度1.15g/cm3,回收料。
2)马来酸酐接枝聚乙烯(PE-g-MAH):清华大学高分子研究所产品。
3)(甲基丙烯酸甲酯/丁二烯/苯乙烯)共聚物(MBS):C-100,日本三菱人造丝公司产品。
4)(甲基丙烯酸甲酯/甲基丙烯酸丁酯)共聚物(ACR):355P,美国Romhass公司产品。
2.制备方法
将PC回收料在80℃下干燥12h,增韧剂在70℃下干燥12h,然后按一定比例将两者混合均匀,用双螺杆挤出机在各段的机筒温度分别为220℃、240℃、250℃、250℃、240℃(口模),螺杆转速为100r/min的条件下熔融共混,自来水冷却,直接牵引切粒,所得粒料在80℃下干燥12h,备用。
将干燥后的粒料用塑料注射机在250℃下注射成拉伸试样和冲击试样。
3.结构与增韧机理分析
从纯PC及PC/PE-g-MAH合金冲击断面可见,纯PC的断裂面平整光滑,为典型的脆性断裂;PE呈分散相分散在PC基体中,PE粒径为2~5μm,颗粒较大,试样断裂时有拔出现象,断面留下很多孔穴,断裂方式趋于脆性断裂。之所以有明显的相分离现象,原因可能是PC用苯酚封端,没有可与接枝的马来酸酐(MAH)反应的基团,不能形成强的界面结合;同时PE的接枝率不高,极性没有得到明显的改善,而PC为极性聚合物,根据相似相容原理,PC与PE-g-MAH的相容性并不好。增韧剂粒子尺寸较大及界面作用力较弱,导致PC/PE-g-MAH合金试样脆性断裂。
从不同MBS含量下的PC合金冲击断面可知,当MBS含量为5%时断口表现为脆性断裂的微观特征,且基体有空洞化现象,PC与MBS在断裂过程中没有明显的分层现象,说明两者之间有较好的界面相互作用,但两者之间并无化学键作用,因此当试样受到冲击时,破坏从界面开始,造成分散相与基体的分离,即分散相粒子的空洞化。由于MBS粒子相距较远,粒子周围的应力场受其他粒子的影响很小,基体中的应力场只是这些孤立的MBS粒子应力场的简单加和,不能导致基体的剪切屈服,冲击能量主要由粒子空洞化损伤吸收。当MBS的含量增加到10%时,基体呈现剪切屈服表现为韧性断裂。
从PC合金呈韧性断裂(MBS含量为15%)处可知,在起裂区,基体发生了剪切屈服,且剪切带与断面约呈45°角。而在断口中心区域基体也表现为剪切屈服,只是剪切带方向与冲击方向相同。在剪切带内部可以看到许多空洞,该空洞沿冲击受力方向被拉伸,断裂表面的应力发白就是由于试样的空洞化和剪切屈服造成的。可以确定韧性断裂时PC/MBS合金的断裂过程为:冲击时首先形成粒子空洞化,空洞化的结果阻止了基体内部裂纹的产生,同时由于MBS粒子充分接近,应力场不再是孤立的MBS粒子应力场的简单加和,粒子周围的应力场有明显的相互作用,这些相互作用使MBS颗粒聚集体附近的基体PC变形时所受的约束减小,使之产生剪切屈服,PC/MBS合金表现为韧性断裂。即核-壳共聚物增韧PC的增韧机理为共聚物粒子的空洞化引发基体的剪切屈服,冲击能量由粒子空洞化和基体剪切屈服吸收,而且后者吸收的能量是主要的。
从MBS含量为8%时PC合金可可以看到,在起裂区试样断裂的微观形态为粒子空洞化和基体剪切屈服的共同作用,而在失稳区则只表现为粒子空洞化。
从不同ACR含量下PC合金冲击断面可看出,ACR含量为5%时呈脆性断裂,为8%时合金呈韧性断裂。ACR颗粒与PC间界面模糊,这表明ACR与PC的相容性好于MBS与PC的相容性。因此,ACR对PC的增韧效果优于MBS。
4.性能
(1)PC合金的冲击性能 加入PE-g-MAH后,PC合金的韧性有所提高,PE-g-MAH含量为10%时其冲击强度为纯PC的5倍,但PC合金仍呈脆性断裂。MBS与ACR均为以甲基丙烯酸甲酯(MMA)为壳的核-壳共聚物,它们的加入,使PC的韧性有了明显的提高。当MBS含量为15%时PC合金的缺口冲击强度为纯PC的30倍以上。而发生脆-韧转变时PC/ACR合金所需的ACR比PC/MBS合金所需的MBS少,且PC/ACR合金的冲击强度可达到纯PC的38倍以上。
(2)PC合金的拉伸性能 由于纯PC的相对分子质量太小,并未达到屈服点即脆断,加入增韧剂后,合金均开始产生屈服,拉伸强度得到提高。随着增韧剂含量的增加,合金的屈服强度下降,但下降的幅度不大。由于增韧剂与PC的相容性不同、增韧剂自身性质差异等因素导致屈服强度提高的幅度不同。研究表明,ACR的加入使PC的屈服强度提高幅度最大。
5.效果
PE-g-MAH与PC的相容性不好,增韧效果不显著。而MBS与ACR能很好地改善PC的冲击性能,且由于ACR与PC的相容性好于MBS,因此ACR对PC的增韧效果优于MBS。对PC合金损伤机理的研究表明,核-壳共聚物增韧PC的增韧机理为共聚物粒子的空洞化引发基体的剪切屈服。
(二)PC/ABS的弹性体增韧改性
1.原材料与配方(质量份)

2.共混物的制备
将ABS和PC分别在90℃和120℃下在热风循环干燥箱中干燥5h后,将各组分按配方称好,在ϕ58mm双螺杆挤出机上挤出造粒,加工温度为235℃,螺杆转速为140r/min。
3.性能
弹性体增韧效果优于增容剂,其中马来酸酐接枝三元乙丙橡胶好于苯乙烯丁二烯嵌段共聚物。如对表3-20中2号组合,当PC/ABS质量比为60/40时,弹性体的增韧使拉伸强度在下降约14MPa的前提下,缺口冲击强度升高了约29kJ/m2,断裂伸长率由24%提高到41%。由此可表明,与拉伸强度的损失相比,增韧效果尚不十分理想。
表3-20 增容剂及其质量分数

对PC/ABS质量比为60/40的组分,与未加以改性的PC/ABS合金相比,拉伸强度下降约14MPa时,缺口冲击强度升高了约37kJ/m2,断裂伸长率由24%提高到53%。对8号组合,同样就PC/ABS质量比为60/40的组分,其拉伸强度下降约6MPa时,缺口冲击强度升高了28kJ/m2,断裂伸长率提高到39%,与前述2号组合比较,显示出更好的综合性能,另一对组合的作用则不明显。
适当的弹性体与增容剂组合改善了组分之间的溶混性,对PC/ABS合金增韧出现协同作用,优于单独的增韧效果,且可减小材料在强度方面的损失,因此可优化材料综合性能,降低材料成本,扩大材料应用范围。
(三)增韧聚碳酸酯
1.原材料与配方(质量份)

2.制备方法
先将干燥好的PC、增韧剂和各种助剂在高速混合机中混合均匀,然后将混合均匀的物料投入双螺杆挤出机中进行熔融挤出造粒,PC增韧挤出加工温度范围为240~250℃,将挤出的粒料在100℃下干燥8h,用注射机将改性PC颗粒注射成标准试样,注射温度为240~250℃,挤出机主机转速为900r/min。
3.性能
表3-21是不同用量的KT-30对PC力学性能的影响。
表3-21 KT-30用量对PC力学性能的影响

由表3-21可知,增韧剂用量选择5.0%为宜,此时断裂伸长率由53.0%增加到95.8%,提高了80%,冲击强度由8.2kJ/m2增加到40.8kJ/m2,提高了近4倍,拉伸强度由66.1MPa降低到60.0MPa,降低了10%。
表3-22是用量为5%的不同增韧剂和PC共混后的力学性能比较。从表3-22中的数据可以得出,各增韧剂都具有一定的增韧效果。KT-30的拉伸强度、弯曲强度和冲击强度最大,分别达到60.0MPa、72.0MPa和40.8kJ/m2;其次是AX-8900,分别达到了58.8MPa、71.2MPa和39.1kJ/m2;最小的是KM-355P,分别达到57.6MPa、70.2MPa和36.9kJ/m2。AX-8900断裂伸长率最好,达到98.0%,其次是KM-355P,达到96.3%,最小的是KT-30,达到95.8%。相比较而言,双官能化PC增韧剂KT-30的增韧效果优于其他增韧剂,其增韧过的PC拉伸强度和弯曲强度损失相比其他增韧剂最少,且冲击强度提升的最高。
表3-22 不同增韧剂对PC力学性能的影响

由表3-23可以看出,用KT-30改性后的PC的耐应力开裂明显好于其他增韧剂改性过的PC。
表3-23 不同增韧剂对PC耐应力开裂的影响

由于KT-30具有良好的分散性,可直接与PC进行共混注射改性,而且其力学性能与挤出造粒后注射改性相差不大,可节省大量的生产加工时间。而其他增韧剂不具有此功能,比较结果见表3-24。
表3-24 KT-30增韧PC共混注射与挤出注射的力学性能比较

4.效果
1)随着KT-30用量的增加,PC冲击强度明显提高,当增韧剂用量达到5%时,冲击强度提高了近4倍,且其他力学性能损失较小,达到了增韧PC的要求。
2)KT-30在提高PC冲击强度的同时,更好地改善了其耐应力开裂性能,明显优于其他增韧剂。
3)KT-30可直接与PC共混注射,减少了挤出造粒过程,可大量节省生产时间。
(四)马来酸酐接枝三元乙丙橡胶增韧AES/PC
1.原材料与配方(质量份)

2.制备方法
将三种AES树脂和PC树脂干燥后,按AES∶PC=70∶30的比例共混挤出造粒,挤出温度从一区到六区分别为220℃、225℃、230℃、235℃、240℃、235℃,制备了橡胶含量分别为21%、25.2%和29.4%的三种AES/PC共混物(分别记为AES1/PC、AES2/PC、AES3/PC),然后将AES/PC共混物分别与0份、1份、3份、5份、7份、9份EPDM-g-MAH混匀,挤出造粒,挤出温度从一区到六区分别为220℃、225℃、230℃、235℃、240℃、235℃;将粒料在80℃下干燥12h后经注射机注射,注射温度从一区到五区分别为230℃、235℃、240℃、245℃、240℃,制成标准样条以备测试。
3.性能(表3-25)
表3-25 自制AES树脂的基本性能

4.效果
1)EPDM-g-MAH加入AES/PC共混物中后,能与共混物中PC末端羟基反应,从而起到反应性增容作用,改善AES/PC共混物的界面。
2)一定量的EPDM-g-MAH能对低橡胶含量的AES/PC(70/30)共混物起到很好的增容作用,可明显细化其中PC相尺寸,使其分散更均匀,增容后共混物能在保持较高拉伸强度时同时,冲击强度得到明显提升。
3)EPDM-g-MAH引入高橡胶含量的AES/PC共混物中后,反而使得其PC相尺寸粗化。
4)EPDM-g-MAH加入AES/PC共混物中后,对共混物热变形温度的影响不大。
(五)PP-g-MAH增韧PC
1.原材料与配方(质量份)

2.制备方法
将原料PP在80℃烘箱中烘干2h,原料PC在120℃下烘干4h。共混物按照一定的比例确定配方挤出造粒,之后注射成型。
为研究在一定配比下不同改性剂对共混试样的影响,用PC分别与PP-g-MAH、EP-DM-g-GMA共混制得试样,来探究相同配比下PC/PP、PC/PP-g-MAH及PC/EPDM-g-GMA试样的性能。
3.性能(表3-26)
表3-26 不同改性剂对PC力学性能的影响

从表3-26中可明显看出,在质量比为98∶2的共混比下,PC分别与PP、PP-g-MAH及EPDM-g-GMA共混合,PC/PP共混后试样拉伸强度低于接枝物与PC共混所得试样的拉伸强度,而且相差很大,说明用接枝物来改性可提高试样的拉伸强度。共混试样的弯曲强度相对PC/PP有所提高,PC/PP-g-MAH共混试样的弯曲强度高些。
4.效果
1)PC的加工流动性较差,加入不同配比的PP与PC共混后,根据测试结果,试样加工流动性有较大提高。
2)与PC/PP相比,在相同的配比条件下,PP-g-MAH或EPDM-g-GMA与PC共混后,共混物的力学性能得到提高,并且其加工流动性也有较大的提高,综合性能较PC/PP共混物有明显增强。SME观察试样发现PC/EPDM-g-GMA两相的黏着力比PC/PP有很大改善,相容性也有明显提高。
二、合金化改性
(一)PC/HDPE/EVA共混合金
1.原材料与配方(质量份)
HDPE为100份,PC为10~30份,EVA为10~30份。其中,HDPE为定值(100份),当不添加EVA时,以PC为变量;当PC加入20份时,以EVA为变量,分别研究PC改性HDPE以及EVA用量对HDPE/DC合金的性能影响。
2.制备方法
(1)工艺条件与参数设置 塑料注射机,注射温度设定(由加料段至口模段)为140℃、180℃、220℃、265℃、280℃、270℃,注射压力为75MPa,注射周期53s;拉伸试验机,拉伸速度45mm/min;热变形试验仪,介质硅油,升温速度为120℃/h,负荷1kg;MFR测试仪,砝码重5kg,设定温度为190℃;单螺杆塑料挤出机,设定温度(由加料段至口模)为140℃、190℃、230℃、240℃、260℃、270℃,螺杆转速为60r/min。
(2)工艺流程 其工艺流程如图3-1所示。

图3-1 工艺流程
3.性能
从表3-27中可以看到,EVA用量相同时,尽管HDPE与PC的形态和结构相差很大,属于极不相容共混体系,但共混物的拉伸强度仍然随着PC含量的增加而增加。产生这种结果的原因尚不明确。PC用量相同时,加入15份EVA的拉伸强度小于未加入EVA共混合金的拉伸强度,这是由于EVA本身的强度低造成的。
表3-27 拉伸强度及断裂伸长率测试结果

4.效果
1)随PC用量的增加,HDPE/PC共混合金的熔体流动速率(MFR)也减小,缺口冲击强度增大,拉伸强度增大,维卡软化点变化不大。说明PC能够提高HDPE的强度,但同时也使体系的加工性能变差。
2)EVA能够改善合金体系的加工流动性和冲击强度,但是会明显降低合金体系的拉伸性能和软化点。
(二)PC/PS共混合金
1.原材料与配方(质量份)

2.制备方法
(1)反应性挤出合成增容剂母粒 将马来酸酐(MA)、苯乙烯(St)、PC、过氧化苯甲酰混合,放入塑料挤出机的漏斗中,在一定温度和转速条件下进行反应性挤出,合成PMA-St-PC增容剂母粒。
(2)共混挤出制备共混物 将PC、PS按w(PC)∶w(PS)=60∶40的比例混合,按一定PMA-St-PC增容剂份数与PC/PS混合物放入挤出机中,在一定条件下进行挤出共混,挤出温度:一段至四段分别为220℃、250℃、250℃、230℃,得到PC/PS/PMA-St-PC共混物。
3.性能分析
合成工艺对增容剂母粒外观的影响 不同的挤出温度和转速条件进行反应性挤出合成增容剂母粒,其外观见表3-28。
表3-28 不同合成工艺条件下合成的增容剂母粒外观

由表3-28可知,在较低的转速条件下和较低的挤出温度条件下,产物的色泽较浅,几乎可达到无色、透明。若转速较低,温度较高,则MA易分解,导致产物的色泽较深;若转速高,温度较低,则MA-St共聚反应可能不完全,尽管色泽较浅,但几乎不透明,呈白色;若转速和温度都较高,则产物色泽仍较深,这是因为MA分解所致。所以合成PMA-St-PC增容剂母粒较好的工艺条件为合成工艺1。试验中还发现,加入增容剂母粒可改善PC/PS共混体系的外观,PC/PS合金体比未加前表面更光洁,透明性更好。
4.效果
1)加工工艺对反应性挤出合成PMA-St-PC增容剂母粒的外观有一定的影响,调节合适的温度和转速,增容剂母粒的透明性更好。加入增容剂母粒可改善PC/PS合金体系的外观,使PC/PS合金体比未加前表面更光洁,透明性更好。
2)增容剂母粒的加入,提高了PC/PS合金体系的相容性,熔体流动速率显著增加,即流动性增加,添加25份增容剂母粒,PC/PS合金体系熔体流动速率最高可达85g/(10min)。
3)增容剂母粒的加入,使PC/PS合金体系的冲击强度和弯曲强度也得到了增强,弯曲强度在增容剂母粒份数为25时达到最大。但当增容剂母粒份数>25时,弯曲强度有所下降。
(三)PC/ABS合金
1.原材料与配方(表3-29和表3-30)
表3-29 PC/ABS合金组成试验配方(质量份)

表3-30 PC/ABS合金不同增容剂试验配方(质量份)

2.制备方法
将ABS与PC分别在90℃和110℃下鼓风干燥12h,然后按表3-29和表3-30中的比例分别在高速混合机中混合,用双螺杆挤出机熔融共混挤出、冷却、切粒,所得粒料再在90℃下鼓风干燥10h后注射成标准试样。
挤出工艺条件:螺杆转速为180r/min,进料转速为170r/min,螺杆造粒温度为230~250℃,机头温度为250℃。
注塑工艺条件:一区至三区温度分别为255℃、260℃、270℃,喷嘴温度为260℃,保压时间为8s,冷却时间为15s,注射压力为70MPa。
3.性能
由表3-31和表3-32可知,未加入增容剂时,PC与ABS的ΔTg为30.31℃;加入4份增容剂S-2001时,PC与ABS的ΔTg下降至29.86℃,说明加入4份增容剂S-2001时,其起到的相容效果最好。
表3-31 SAG-002不同用量下PC/ABS合金的玻璃化转变温度Tg(单位:℃)

表3-32 S-2001不同用量下PC/ABS合金的玻璃化转变温度Tg(单位:℃)

4.效果
1)在增容剂SAG-002用量为2份时,随着PC用量的增加,PC/ABS合金的力学性能随之提高。
2)在PC/ABS质量比为80/20时,增容剂SAG-002和增容剂S-2001的加入会导致PC/ABS合金的强度下降。
3)增容剂S-2001对PC/ABS合金有明显的增韧效果。
4)在PC/ABS质量比为80/20情况下,加入2份增容剂SAG-002和4份增容剂S-2001时,PC与ABS的ΔTg分别为最小,PC/ABS合金的相容性达到最佳状态。
三、填充改性与增强改性
(一)凹凸棒土填充改性PC/PP合金
1.原材料与配方(质量份)

2.制备方法
(1)AT的表面改性 称取一定量的凹凸棒土,加入适量去离子水,高速搅拌10min呈悬浮状态,去除沉淀的粗矿物杂质;在80℃下加热悬浮液,滴加表面改性剂硅烷AG-102的水溶液,保持高速搅拌3h;将处理物反复抽滤、洗涤数次,经干燥后粉碎过筛。
(2)AT/PP母料的制备 在与PP复合前,首先将AT置于真空烘箱中在105℃下干燥5h,将PP和AT、分散剂EVA蜡按一定比例在高速搅拌机中进行初混,混合均匀后使用德国WP公司ZSK-25WLE型(L/D=48,D=35mm)双螺杆挤出机造粒,机筒各段温度:210℃、215℃、225℃、225℃、220℃(机头),螺杆转速为200r/min。
(3)AT/PP/PC复合材料的制备 PC树脂经120℃真空烘箱干燥6h后与AT/PP母料、PP树脂及增容剂PP-MAH按一定比例混合,使用同样双螺杆挤出机造粒,机筒各段温度:255℃、260℃、275℃、275℃、270℃(机头),螺杆转速为200r/min。所得粒料干燥后,使用CJISONC-Ⅱ型注射机制成标准测试样条。
3.性能
表3-33中对PC、PP/PC、AT/PP/PC复合体系的力学性能进行了比较。
表3-33 PC复合材料与PC力学性能的比较

4.效果
1)采用两步法熔融共混工艺,实现了在PC复合材料中具有核-壳结构分散相包容粒子的设计。即将经过偶联剂表面改性的AT与PP制成母料,然后将母料添加到PC树脂中,可使其在剪切力场的作用下形成以AT为核、PP为壳的相包容粒子。
2)这种核-壳结构的分散相对PC树脂有良好的增韧作用,并且较PP/PC合金体系强度有一定提高。
3)在AT/PP/PC三元共混体系中,可以通过PP相周围基体产生空穴,诱发基体发生屈服形变,分散相被取向、拔出,PP相内AT对分散相的增强作用耗散冲击能。
(二)玻璃纤维增强PC/PBT合金
1.原材料与配方(质量份)

2.制备方法
将物料放在烘箱中进行干燥,其中,PC和PBT在120℃下干燥6h,玻璃纤维在80℃下干燥4h,增韧剂在60℃下干燥6h。物料经过充分干燥之后,通过双螺杆挤出机混合造粒,双螺杆挤出机加热段各区的温度分别为200℃、220℃、240℃、250℃、250℃、250℃、250℃、250℃、250℃,机头温度为245℃。从主喂料加入PC、PBT、增韧剂和抗氧剂,从侧喂料加入玻璃纤维。通过调控主喂料中各组分的比例,以及主喂料和侧喂料的喂料速率,实现玻璃纤维在共混物中的含量为10%,增韧剂含量为5%,抗氧剂含量为0.5%,具体的物料组成见表3-34。作为比较,纯PBT也在相同的挤出参数下从挤出机中挤出。
表3-34 不同组成比例下PC/PBT合金的物料组成

将挤出所得混合粒料在120℃的鼓风烘箱中干燥6h,然后在一定条件下注射成标准试样。注射制得的试样在室温下静置24h后再进行性能测试和结构表征。
3.性能与效果
不同PC/PBT组成比例下PBT升温过程中的熔融焓ΔHm和冷结晶焓ΔHcc,见表3-35。各个试样中PBT的结晶度Xc,见表3-36。
表3-35 PC/PBT合金及纯PBT的差示扫描量热仪(DSC)熔融曲线相关数据

表3-36 不同PC/PBT组成比例的合金和纯PBT的Xc

表3-37列出了不同PC/PBT组成比例下合金的热变形温度(HDT)。随着PBT含量的提高,合金的HDT呈现先降低后增高的变化趋势,并在PC/PBT=70/30时达到最低值99.7℃。
表3-37 不同PC/PBT组成比合金的HDT

(三)晶须增强PC复合材料
1.原材料与原材料(质量份)

2.制备方法
将PC置于120℃的电热鼓风干燥箱中干燥8h,然后装入塑料袋中密封,防止原料再次受潮。用无水乙醇稀释硅烷偶联剂KH-550(偶联剂的用量为填料质量的1%),在填料表面雾状喷入稀释后的偶联剂,将溶剂烘干备用。根据配方称取PC和表面处理过的晶须硅填料,经高速混合机混合均匀后,在双螺杆挤出机中挤出造粒,将粒料置于120℃的电热鼓风干燥箱中干燥8h后,测试材料的热分解温度、熔体流动速率和流变性能,双螺杆挤出机自加料段开始各段温度依次为245℃、260℃、265℃、270℃、280℃、280℃、275℃、275℃,螺杆转速为45r/min。在平板硫化机中将造粒后的材料压制成板材,压制温度为260℃、压力为13MPa,时间为6min,然后制样,并测试材料的热变形温度、力学性能和抗划伤性能。
3.性能
当添加少量的晶须硅时,改性PC体系的抗划伤性能无明显改善,随着晶须硅含量的增加,改性PC体系的抗划伤性能有所提高,但当晶须硅含量大于4%时,改性PC体系的抗划伤性能基本保持不变。
随着晶须硅含量的增加,PC体系的热变形温度随之上升,但增长趋势逐渐变缓。这是因为:晶须硅具有显著的增强作用,经硅烷偶联剂改性后的晶须硅与PC的相容性较好,能够在PC体系中均匀分散,当外界弯曲应力施加在复合材料上时,晶须硅在PC基体中能够承受较大的弯曲应力,使复合材料抵抗外界弯曲变形应力的能力增强,所以其热变形温度升高。但随着晶须硅含量的增多,晶须硅在PC体系中的分散效果会受到一定的影响,所以随着晶须硅含量的增多,热变形温度的增长趋势逐渐变缓。
随着晶须硅含量的增加,改性PC体系的拉伸强度明显上升。
随着晶须硅含量的增加,PC体系的缺口冲击强度和断裂伸长率均呈现先上升后下降的趋势。其中,在晶须硅含量为5%时,PC的断裂伸长率和缺口冲击强度均达到最大值,分别为7.62%kJ/m2和7.32kJ/m2。这是因为:纤维增强型复合材料吸收冲击能的方式分为树脂变形和裂纹扩展至断裂、纤维抽出以及纤维断裂三种,PC体系在冲击载荷作用下的变形能力具有差异,而PC基体较大的变形导致沿纤维弯曲方向产生间隙,因此,一方面将使纤维抽出时吸收的能量减小,另一方面则降低了纤维断裂的可能性,即相当于增加了纤维的临界断裂长度。当晶须硅含量小于5%时,可以认为树脂变形在复合材料缺口冲击强度中的贡献占主导地位;而当晶须硅含量高于5%时,树脂含量减少,导致纤维从树脂中抽出更加容易。另外,晶须硅的端部是裂纹增长的引发点,当晶须硅含量达到一定程度后,继续增加其含量,将会降低材料的冲击强度和断裂伸长率。
改性PC体系熔体为假塑性流体,随着晶须硅含量的增加,体系的黏度和线性相关系数K值逐渐下降,非牛顿指数n值逐渐增大,即非牛顿性减小,剪切速率对体系黏度的影响减小,改性PC体系可以在较宽的剪切速率范围内加工成型。
4.效果
在晶须硅改性PC体系中,当晶须硅含量小于5%时,随其含量的增加,改性PC体系的拉伸强度、断裂伸长率、缺口冲击强度和流变性能呈现上升的趋势;但当晶须硅含量大于5%时,随其含量的增加,改性PC体系的拉伸强度、熔体流动性能和流变性能继续上升,但缺口冲击强度和断裂伸长率却呈现下降的趋势。综上所述,当晶须硅含量为5%时,改性PC体系的综合性能最好,其拉伸强度为66.03MPa,断裂伸长率为7.62%,缺口冲击强度为7.32kJ/m2,K值为736.631,n值为0.843。
(四)玻璃纤维增强改性PC/PBT共混合金
1.原材料与配方(质量份)

2.制备方法
将PC、PBT在110℃下鼓风干燥16h,然后按比例称取PC、PBT、ACR及其他助剂,经高速搅拌混合机预混合3min,用双螺杆挤出机熔融共混挤出,并在共混挤出过程中在双螺杆挤出机的第二加料口加入(30±2)%的无碱玻璃纤维,料条经自来水冷却后用切粒机切粒。共混工艺的转速为150r/min,加热段各区温度:一区为220℃,二区为230℃,三至六区为240℃,机头为245℃。
共混粒料在120℃下鼓风烘箱中干燥(料层厚度小于2.5cm)后,注射成标准试样,注射温度为230~260℃。
3.结构分析
从亚磷酸三苯酯加入量为1.0%时,不同组成共混体系试样在液氮中冷冻折断后的SEM照片中看不出PBT与PC间的明显相界面,表明共混体系中PBT与PC的相容性较好;同时,可以观察到少量的微孔,这可能是由于PBT与PC共混时发生了副反应酸解而释放出CO2引起的。从共混体系在三氯乙烷中刻蚀前后的电镜照片中可以看出有大量孔洞为刻蚀前的PC相,孔洞尺寸为0.2~1μm,孔洞形状规则,表明分散相PC在共混体系中分散均匀,进一步说明PBT与PC相容性好。
4.性能
改变共混体系中PC与PBT的含量,测试共混体系的力学性能,结果见表3-38。由表3-38可见,在PBT/PC共混体系中,热变形温度随PBT含量的增加先降低,然后再升高,这是由于PBT的结晶度受PC的影响,PC含量越高,对PBT结晶的影响越大。当PBT在共混体系中含量不大时,由于PC的影响,PBT的结晶度小,根据共混体系性能的加和法则,共混体系的热变形温度随PBT含量的增加而降低,并低于纯PC的热变形温度,直到PBT为主要组分时,PC对PBT的结晶影响减小,热变形温度升高。随着PBT组分含量的增加,共混体系的热变形温度接近玻璃纤维增强PBT的热变形温度。
表3-38 原料配比对共混体系力学性能的影响

注:ACR用量为15份。
PC含量很少时,PBT和PC部分相容;PC含量占30%~40%时,则完全相容,若PC含量比较多而又少于30%,PBT/PC共混体系成为PBT、PC、PBT/PC相容物的共混体系。由表3-38可看出,改变共混体系的组成,除热变形温度外,共混体系的其他性能变化不大,说明共混体系中加入ACR后,PBT与PC在更宽的组成范围内有比较好的相容性。
5.效果
1)抗冲改性剂ACR的加入,使PBT/PC共混体系的冲击强度明显提高,但降低了共混体系的其他力学性能,如拉伸强度、弯曲强度以及弯曲模量。同时,ACR的加入,使PBT/PC共混体系的相容性提高。
2)加入少量亚磷酸三苯酯后,由于不同程度地抑制了酯交换反应的发生,PBT/PC共混体系的相容性有所降低,表现为力学性能不同程度的降低。当亚磷酸三苯酯加入量为1.5%时,酯交换反应已基本被抑制住。
四、纳米改性
(一)核-壳结构和层状结构纳米改性PC
1.原材料与配方(质量份)

2.制备方法
(1)纳米SiO2和纳米CaCO3的表面处理 将纳米SiO2或纳米CaCO3在真空烘箱中于105℃干燥2h,称取10g加入装有300mL二甲苯的圆底烧瓶中,加入3g KH-570,通N2保护,在二甲苯的回流温度下回流4h,冷却,过滤。将过滤得到的纳米SiO2或纳米CaCO3用300mL二氯甲烷作为洗涤液在索氏提取器中提取10h,再于60℃下真空干燥24h,研磨,备用。
(2)改性剂的制备 在装有搅拌器、冷凝管,并通N2的2L三口烧瓶中加入1000mL去离子水、20g MMT(或表面处理过的纳米SiO2、纳米CaCO3)、10g十二烷基苯磺酸钠,加热到70℃后一次性加入1g过硫酸铵,在0.5h内滴加由90g丙烯酸丁酯和0.9g二乙烯基苯配成的混合液,反应2h,再在0.5h内滴加90g甲基丙烯酸甲酯,反应4h,冷却,过滤,喷雾干燥得到白色粉末。将含纳米SiO2、纳米CaCO3、MMT的改性剂分别称为纳米SiO2改性剂、纳米CaCO3改性剂和MMT改性剂。
(3)PC合金的制备 先将PC于100℃真空干燥12h,改性剂于80℃真空干燥12h。将干燥过的PC和改性剂以9∶1的质量比机械混合后,用双螺杆挤出机挤出,加工温度为230~250℃,螺杆转速为25r/min。再用注射机加工成拉伸、弯曲和冲击试样,注射温度为250℃,模具温度为80℃。
3.结构分析
(1)纳米SiO2改性剂和纳米CaCO3改性剂的TEM照片 从纳米SiO2改性剂和纳米CaCO3改性剂的TEM照片中可以看出,纳米SiO2和纳米CaCO3以纳米尺寸分散在聚合物中,分散都非常均匀,没有团聚现象。纳米SiO2改性剂粒径为20~50nm,纳米CaCO3改性剂粒径为100~200nm,这两种改性剂可统称为具有核-壳结构的改性剂。
(2)MMT改性剂的高分辨率电子显微镜(HREM)照片 从MMT改性剂的HREM照片中可以看出,聚合物已经插层到了MMT的层间。MMT的层间距由原来的1nm增大到2~3nm,形成了具有层状结构的有机聚合物/无机纳米粒子复合材料。这种改性剂可称为层状结构的改性剂。
4.性能
纳米SiO2改性剂和MMT改性剂均可以使PC的冲击强度得到较大幅度的提高,其中纳米SiO2改性剂可以使PC的冲击强度提高约50%,MMT改性剂可以使PC的冲击强度提高约45%,拉伸强度和弯曲强度基本不降低。这是由于当试样受到冲击力作用时,均匀分散在PC中的改性剂粒子吸收大量的能量,从而使冲击强度提高;而当试样受到拉伸和弯曲作用时,虽然PC合金中PC分子链不如合金化前容易取向,但改性剂粒子在拉伸变形和弯曲变形中仍可吸收大量的能量,导致拉伸强度和弯曲强度基本能与PC持平。
加入改性剂粒子后,PC的加工性能均得到很大改善,最大扭矩和平衡扭矩都降低了,达到平衡扭矩的时间也缩短了,其中含有MMT改性剂和纳米SiO2改性剂的PC合金的加工性能较好。
5.效果
通过乳液聚合的方法制备了含有纳米SiO2或纳米CaCO3的核-壳结构改性剂及含有MMT的层状结构改性剂,并利用这些改性剂对PC进行改性。纳米SiO2改性剂使PC的冲击强度提高约50%,MMT改性剂使PC的冲击强度提高约45%,加入改性剂后PC的拉伸强度和冲击强度基本不降低,加工性能得到很大改善。改性剂粒子在PC中均匀分散,使PC的分子链取向变得困难,拉伸和冲击断面变得粗糙且改性剂粒子在PC中成为应力集中点。
(二)烷基化纳米SiO2/MMA改性PC
1.原材料与配方(质量份)

2.制备方法
(1)烷基化纳米SiO2的制备 在强力分散机(SFJ-400,上海环境工程研究所生产)中加入定量已干燥的纳米SiO2、KH-570及二甲苯,使其充分分散后移入置于油浴的三颈瓶中,通N2保护,磁力搅拌加热并在二甲苯的回流温度下保持一定时间后结束反应。将物料移入烧杯静置分层,取出下层沉淀物,经丙酮洗涤后干燥得烷基化纳米SiO2。
(2)烷基化纳米SiO2/MMA乳液聚合产物的制备 称一定量的烷基化纳米SiO2于上述强力分散机中,加蒸馏水和少量的异丁醇作为分散剂充分分散后,移入水浴中的三颈瓶内,磁力搅拌回流,通N2保护,待升温至反应温度后加入K2S2O8,再滴加精制的MMA进行无皂乳液聚合。反应结束后分离、洗涤、干燥。
(3)复合材料样条的制备 将已干燥的PC与乳液聚合产物混合,在双螺杆挤出机中共混挤出,所得粒料干燥后,于注射机上注射标准样条。
3.结构
从乳液聚合产物经染色后的TEM照片中可看出,聚合产物近似为球形的乳胶粒子。可以看见乳胶粒子具有核-壳结构,键接有KH-570的纳米SiO2即烷基化纳米SiO2,在引发剂引发下与MMA进行乳液聚合时,因KH-570上含双键的大R基团包覆在粒子表面,而使SiO2粒子能稳定地分散在水中,无论体系中有无乳化剂存在,根据“相似相容”原理,MMA单体总是趋向集中在SiO2粒子表面,一旦水相中引发剂分解的自由基扩散到SiO2表面,便引发大R基上的双键及MMA上的双键聚合,PMMA聚合物便包覆在粒子表面;因单体的亲水性大于聚合物,故剩余单体始终处于聚合物与水的界面上,聚合反应就在这一单体层内进行,最后形成以SiO2为核、PMMA为壳的核-壳粒子。至此可以断定:照片中具有核-壳粒子结构的中心深色部分为纳米SiO2,外围浅色部分为PMMA。试验中发现,壳层厚度可用单体用量、引发剂用量、聚合温度、聚合时间等因素来调控。当单体用量为10mL MMA/1L H2O,引发剂用量为0.75g K2S2O8/1LH2O,聚合温度为70℃,聚合反应时间为3h,壳层平均厚度为20~50nm(电镜法),SiO2占70%左右(灼烧法)。这种PMMA为壳层,核-壳间存在化学键连接的复合粒子在聚合物基体中既能良好地分散又能改善界面状况,必然会显著改善聚合物性能。
4.性能
由表3-39可见,2号试样的冲击强度虽比3号试样纯PC有提高,但不太显著,因文中的核-壳粒子为SiO2/PMMA结构,属刚性粒子,而刚性粒子为分散相的复合材料要达到增韧效果,其基体必须有适度的韧性,即要求刚性粒子的弹性模量E及泊松比μ与基体聚合物的E与μ有一定的匹配,否则难以体现增韧效果。经用适量的第三组分A来调节基体的弹性模量与泊松比,使两者的弹性模量E与μ更好地匹配后,体系在脆韧转变点附近,表现出很高的韧性,因而1号试样的缺口冲击强度高达53.71kJ·m-2,为纯PC的13倍。
表3-39 PC复合材料与PC性能的比较

①第三组分为硬壳软核结构,对PC及PMMA有增容作用的有机高聚物,用量为4~10份为宜。
5.效果
1)采用乳液聚合方法能使PMMA包覆在纳米SiO2粒子表面,形成核-壳结构。
2)烷基化纳米SiO2/MMA乳液聚合的乳胶粒子核-壳间存在化学键,当单体用量为10mL MMA/L1 H2O,引发剂用量为0.75g K2S2O8/1L H2O,聚合温度为70℃,聚合反应时间为3h,壳层平均厚度为20~50nm,SiO2占70%左右(由灼烧法得到)。
3)烷基化纳米SiO2/MMA乳液聚合物(即核-壳乳胶粒子)在适量第三组分配合下,使PC的缺口冲击强度、加工流动性、热分解温度均有大幅度提高,其改性效果非常显著。该体系的增韧机理属高韧化增韧理论范畴。
(三)纳米TiO2改性PC-PP光扩散复合材料
1.原材料与配方(质量份)

2.复合材料的制备
首先将在60℃下真空中干燥4h的PP与纳米TiO2进行预混,然后将PP与纳米TiO2在双螺杆挤出机上熔融共混并造粒,制备出TiO2/PP复合物,区域温度为160~190℃,转速为60r/min,混合时间为8min。分别将TiO2/PP复合物与PC在60℃和120℃下真空中干燥4h和12h后,按PP/TiO2复合物与PC质量比为3∶7进行混合,并在双螺杆挤出机上进行熔融共混、造粒,制得最终样品,这一过程的区域温度为220~250℃,转速为300r/min,混合时间为8min。
3.微观结构
随着分散相中纳米TiO2的质量分数从0增加到20%,复合材料始终呈现出二元相分离的“海-岛”状结构,且分散相的形态与尺寸变得较为均一,平均直径逐渐变小。当PP中纳米TiO2粒子质量分数大于10%时,分散相基本以10μm左右的液滴状分散在基体中,说明复合材料中的纳米TiO2粒子起到了分散并固定分散相的作用,避免了小的分散相之间的相互融合。这一相分离的结构与光扩散复合材料的基本结构类似,分散相就相当于光扩散复合材料中的光扩散剂。而分散相在复合材料中的分布以及尺寸对于整个纳米TiO2/PC-PP光扩散复合材料最终的光学性能有直接的影响。
4.性能
当纳米TiO2/PC-PP光扩散复合材料中添加纳米TiO2后,初始热降解温度从410℃提高到420℃以上,而最终的残留量也由3%提高到了13%以上。这是因为纳米粒子的存在阻碍了聚合物链段的运动,从而阻碍了材料的热降解行为,提高了材料的热稳定性。当PP中纳米TiO2的质量分数为5%时,纳米TiO2/PC-PP光扩散复合材料的透光率达到80%,雾度为88%,此时复合材料的光扩散性能效好。
5.效果
1)随着纳米TiO2质量分数的增加,纳米TiO2/聚碳酸酯-聚丙烯(TiO2/PC-PP)光扩散复合材料中分散相的尺寸与形态变得更加均一。
2)随着纳米TiO2质量分数的增加,纳米TiO2/PC-PP光扩散复合材料的总体结晶速率下降,且体系的表观Avrami指数数值变小。
3)纳米TiO2的存在使得纳米TiO2/PC-PP光扩散复合材料的初始热降解温度提高,材料的热稳定性得到改善。
4)随着纳米TiO2质量分数的增加,纳米TiO2/PC-PP光扩散复合材料的透光率明显下降,光学雾度显著提高。当PP中纳米TiO2的质量分数为5%时,纳米TiO2/PC-PP光扩散复合材料的透光率达到80%,雾度为88%,此时复合材料的光扩散性能较好。
综上所述,纳米TiO2在纳米TiO2/PC-PP光扩散复合材料中,不仅在微观上参与了PP的结晶过程,也在一定程度上控制了分散相的形貌,而且最终影响了材料的热稳定性和光扩散性能。
(四)多壁碳纳米管/聚碳酸酯复合材料
1.原材料与配方(质量份)

2.制备方法
取一定量碳纳米管放入烧瓶中,加入质量分数为60%~65%的硝酸,于120℃回流24h。将得到的固体用蒸馏水清洗,直到pH=7,真空干燥。将纯化的MWNTs分散到一定量的1-丁基-3甲基咪唑六氟磷酸盐中,球磨混合均匀。得到的MWNTs离子液体凝胶分散到PC/DCB溶液[(1g PC)/(10mL DCB)]中,将其倾倒到玻璃板上,用刮刀铺展成厚度一定的薄膜,在120℃烘箱中保温6h,然后在120℃下真空干燥24h。
3.性能
当MWNTs的质量分数由0.5%增加到1.0%时,试样的表面电阻率从1015Ω降至1014Ω;而当MWNTs的质量分数增至2.0%时,试样的表面电阻率迅速降至106Ω,表面电阻率下降了8~9个数量级;当MWNTs的质量分数再继续增加到4.0%和6.0%时,表面电阻率下降迅速趋缓,表面电阻率分别为105Ω和104Ω。由此可知,在MWNTs的质量分数从1.0%变化到2.0%时,试样的表面电阻率产生了一个突变。因此,MWNTs/PC复合材料的导电阈值在MWNTs的质量分数为1.0%~2.0%时,能形成良好的导电通道,导电效应显现,表面电阻率下降显著。在突变区域过后,继续增加MWNTs的用量,对导电效应的贡献迅速下降。
复合薄膜的拉伸强度随着碳纳米管含量的增加而提高,当碳纳米管质量分数为0.8%时达到最大值67MPa,比纯PC薄膜拉伸强度提高了12%。这主要是由于,经硝化氧化处理并在离子液体存在下,碳纳米管发生了相当程度的解缠,有利于其分散。同时,碳纳米管与咪唑类离子液体的π-π交联作用,有利于其在PC基体中的分散和碳纳米管与PC基体间的相互作用。当添加量小于1.0%时,在复合薄膜中能有效地抑制团聚现象,提高了碳纳米管与PC基体间的相容性和界面结合能力,从而使复合材料的力学性能得到提升。当碳纳米管的质量分数超过1.0%时,薄膜的拉伸强度较快地下降。这可能是因为,随着添加量的增多,碳纳米管之间的团聚现象增多,导致一定程度的相分离。
4.效果
多壁碳纳米管在相容剂[Bmim]PF6的存在下,经溶液混合法制备了MWNTs/PC纳米复合薄膜;利用TEM、SEM等检测手段对碳纳米管处理前后的形态结构、复合薄膜的表观形态进行了表征;改善了碳纳米管与PC的相容性,复合材料的拉伸强度得到了提高,导电阈值出现在碳纳米管的质量分数为1.0%~2.0%的范围内。对复合材料剪切断面的扫描电镜分析表明,碳纳米管比较均匀地分散在PC基体中,没有明显的相分离,对PC起到了一定的增强作用。
(五)短多壁碳米管改性PC复合材料
1.原材料与配方(质量份)

2.制备方法
将PC粒料放入真空烘箱于100℃干燥10h后备用;将8g PC溶于THF中制成PC溶液,2g碳纳米管在THF中超声分散制成碳纳米管分散液,两者混合后继续超声分散1h,然后加入过量甲醇沉淀析出复合材料,过滤并在真空烘箱中干燥至恒重,即可制备碳纳米管质量分数为20%的复合材料母料。将一定配比的纯PC与复合材料母料通过在微型双螺杆挤出机(SJSZ-10A,武汉瑞鸣塑料机械有限公司)上进行两遍熔融混合(熔体温度为240℃,螺杆转速为30r/min),得到碳纳米管质量分数分别为1%和3%的sMWNT(sOMWNT)/PC复合材料粒料;将制得的粒料在真空压缩机(北京富友马科技有限公司)上压制成厚度为1mm的复合材料板材,模压温度为240℃,压力为15MPa。其中,sOMWNT是指羧基化短多壁碳纳米管。
3.性能
表3-40是sOMWNT/PC复合材料的各项力学性能参数。与纯PC相比,sOMWNT/PC复合材料的拉伸屈服强度和拉伸强度均提高,但断裂伸长率降低。当sOMWNT/PC中碳纳米管的质量分数1%时,sOMWNT/PC的屈服强度和拉伸强度分别提高了12.9%和12.8%。
表3-40 PC及sOMWNT/PC复合材料的力学性能

测试结果表明,与sMWNT/PC复合材料相比,sOMWNT/PC复合材料表现出了较好的热稳定性,1%和3%sOMWNT/PC复合材料的热降解起始温度分别提高了30℃和21℃。与纯PC相比,1%sOMWNT/PC复合材料的热降解起始温度没有降低,两者均为483℃。1%sMWNT/PC复合材料为脆性断裂,而1%sOMWNT/PC复合材料为韧性断裂。分析认为这主要是由于sMWNT在PC基体中的分散性差,较大的团聚体引起应力集中从而导致sMWNT/PC复合材料脆性断裂;而对于sOMWNT,由于表面羧基与PC碳酸酯基之间能够形成氢键,使得sOMWNT与PC界面作用增强,有利于sOMWNT的分散。在拉伸过程中,载荷能有效地传递到碳纳米管上,因而提高了复合材料的力学性能。
测试结果表明,3%sOMWNT/PC复合材料在玻璃态时的储能模量明显高于纯PC和1%sOMWNT/PC复合材料的储能模量。与纯PC相比,其在40℃时储能模量提高了15%。sOMWNT/PC复合材料的玻璃化转变温度随着sOMWNT含量的增加而降低。
4.效果
1)与纯PC相比,sMWNT/PC复合材料的热稳定性和拉伸性能均有明显下降。
2)与纯PC相比,sOMWNT/PC复合材料在保持PC原有热稳定性的同时显著提高了其力学性能。
3)sOMWNT/PC复合材料的储能模量随着sOMWNT含量的增加而增加,但玻璃化转变温度则随着sOMWNT含量的增加而呈现下降的趋势。
(六)纳米CaCO3/MAH-SBS改性PC/ABS共混物
1.原材料与配方

2.制备方法
(1)PC-ABS共混树脂的制备 充分干燥PC、ABS后,在0~70%范围内改变PC的质量分数,按照配方准确称量,加入高速混合机,常温下混合5min,出料后加入挤出机中挤出造粒,挤出温度为230~240℃,挤出粒料干燥后,采用注射机制作标准试样,注射温度为240~250℃。
(2)MAH-SBS-纳米CaCO3复配改性PC-ABS复合材料的制备 固定质量比PC∶ABS(质量比)=1∶1,按照配方准确称量物料,加入纳米CaCO3、SBS、MAH-SBS以及纳米CaCO3与MAH-SBS的复配改性体,调整工艺尽量使其混合均匀,加工工艺参数同上。
3.性能与效果
1)不同质量分数的聚碳酸酯(PC)与丙烯腈-丁二烯-苯二烯三元共聚物(ABS)形成的PC-ABS共混材料性能差异较大,用量比为1∶1左右时,综合性能较好。
2)一定用量范围内,纳米CaCO3大幅度提高了PC-ABS合金的拉伸强度,缺口冲击强度略有上升,用量在4%左右时,拉伸强度出现极大值,约为61.5MPa。
3)单独使用苯乙烯-丁二烯-苯乙烯嵌段共聚物(SBS)无法对PC-ABS合金增强或增韧。
4)马来酸酐接枝苯乙烯-丁二烯-苯乙烯嵌段共聚物(MAH-SBS)可以提高PC-ABS合金的缺口冲击强度,但拉伸强度下降,用量在4%左右时,缺口冲击强度出现极大值,约为104kJ/m2。
5)在合适用量下,MAH-SBS与纳米CaCO3具有协调作用,MAH-SBS改善了纳米CaCO3在PC-ABS合金中的分散和界面结合,发挥了两者的增韧和增强效果。MAH-SBS用量为4%、纳米CaCO3用量为4%时,PC-ABS合金的缺口冲击强度由80kJ/m2上升至108kJ/m2左右,拉伸强度由57.0MPa上升至61.5MPa左右。
五、功能改性
(一)无卤阻燃PC/ABS合金
1.原材料与配方(质量份)

2.制备方法
将PC在100℃干燥24h,将ABS、增容剂MPC 1545R、阻燃剂BDP、TPP等在80℃干燥2h,然后按配方比例称量后,加入高速混料锅中高速混合3~4min,出料,将上述预混料于245~270℃经双螺杆挤出机挤出造粒,制得相应PC/ABS合金,粒料烘干后经注射机注射标准试样。双螺杆挤出机的共混挤出温度:一区为220℃,二~四区为230℃,五~七区为225℃,机头为230℃;螺杆转速为180r/min;注射温度为240~260℃;注射压力为75MPa左右。
表3-41列出了PC与ABS配比对PC/ABS合金力学性能和熔体流动速率(MFR)的影响。
表3-41 PC与ABS配比对PC/ABS合金力学性能和MFR的影响

由表3-42可看出,加入BDP或BDP与TPP复配阻燃剂后,PC/ABS合金的LOI及阻燃性能显著提高。
表3-42 阻燃剂用量对PC/ABS合金性能的影响

在3种不同螺杆组合工艺下,用双螺杆挤出机熔融共混挤出切粒,并测试其性能,结果见表3-43。
表3-43 不同螺杆组合工艺下阻燃PC/ABS合金的力学及燃烧性能

3.效果
1)加入MPC 1545R,能有效改善在PC/ABS体系的相容性,可提高PC/ABS合金的力学性能。当PC与ABS的质量比为7∶3、MPC 1545R用量为5份时,PC/ABS合金的综合力学性能最佳。
2)单一BDP阻燃剂及BDP与TPP复配阻燃剂均能显著提高PC/ABS合金的阻燃性能,BDP与TPP复配阻燃剂比单一BDP阻燃剂的阻燃效果好。当BDP与TPP复配阻燃剂为13.5份(BDP为10份,TPP为3.5份)时,LOI达到27.9%,阻燃等级达到V-0级。
3)不同的螺杆组合工艺对阻燃PC/ABS合金的力学性能有显著影响,适当地降低螺杆的剪切强度,提高螺杆的分散能力,可以获得性能及外观较好的阻燃PC/ABS合金。
(二)S-N-P阻燃剂改性PC
1.原材料与配方(质量份)

2.制备方法
将PC与S-N-P阻燃剂均在100℃下真空干燥12h,然后按不同的配比混合均匀,使用双螺杆挤出机挤出、造粒,挤出温度为240~260℃,螺杆转速为85.8r/min。粒料经充分干燥后使用注射机注射成标准试样,注射温度为260~270℃。
S-N-P阻燃剂的结构式为

3.性能
表3-44是不同添加量的S-N-P阻燃剂对PC力学性能的影响。
表3-44 不同添加量的S-N-P阻燃剂对PC力学性能的影响

测试结果表明,S-N-P阻燃剂在升温范围25~900℃内有两个显著的失重阶段,同时可以得出S-N-P阻燃剂的初始分解温度为458.8℃,说明自制的S-N-P阻燃剂具有较好的热稳定性,能满足大多数聚合物的加工温度要求。在900℃下S-N-P阻燃剂的残炭率为31.5%,这表明阻燃剂本身具有良好的成炭能力。
4.效果
1)S-N-P阻燃剂是PC的高效阻燃剂和抗滴落剂。当其质量分数为0.1%时,阻燃PC的LOI值为35.5%,与纯PC相比提高了43.15%,能通过UL94 V-0等级。
2)S-N-P阻燃剂的加入使PC提前分解成炭,炭层对基材内部起到保护作用,但形成的炭层不稳定,最终使PC残炭率较纯PC降低。
3)当S-N-P阻燃剂质量分数为0.1%时,与纯PC相比,阻燃PC的拉伸强度提高了17.35%,弯曲强度提高了36.7%,断裂伸长率提高了121.6%,缺口冲击强度仅下降了7.63%。
(三)次磷酸铝/苯氧基环三磷腈改性阻燃聚碳酸酯
1.原材料与配方(质量份)

2.制备方法
称料→配料→混料→计量→切粒→包装。
3.性能
表3-45给出了PCPZ和AHP改性PC的阻燃性能。
表3-45 单组分阻燃剂改性PC的阻燃性能

表3-46给出了阻燃剂的质量分数为10%时,PCPZ和AHP以不同质量比复配对PC阻燃性能的影响。
表3-46 复配阻燃剂改性PC的阻燃性能

表3-47给出了PCPZ和AHP按1∶1的质量比复配,协效阻燃剂的质量分数对改性PC的阻燃性能的影响。
表3-47 协效阻燃剂的质量分数对改性PC的阻燃性能的影响

由表3-48可知,添加了PCPZ和AHP协效阻燃剂后,阻燃改性PC材料的阻燃性能得到进一步提高。
表3-48 协效阻燃剂的质量分数对阻燃PC的燃烧性能

由表3-49可知,协效阻燃剂的质量分数从2.5%增加到7.5%时,残炭率增加缓慢;但是从7.5%增加到10.0%时,残炭率发生突变。这和燃烧量热测试数据一致,说明协效阻燃剂的质量分数在10.0%以上时,可以有效提高PC材料的阻燃性能,可通过UL 94 V-0级。
表3-49 阻燃PC在N2中的热重残炭率

4.效果
1)通过单组分阻燃剂改性PC的阻燃性能对比,AHP比PCPZ的阻燃效果更好。
2)将PCPZ和AHP按1∶1的质量比复配,协效阻燃剂的质量分数为10.0%时,阻燃PC的极限氧指数为35.5%,可通过UL 94 V-0(1.6mm),说明复配后两者之间存在协同阻燃作用,明显提高了PC的阻燃性能。
3)从微型量热测试数据可知,复配阻燃改性PC材料的燃烧数值均有所降低。与纯PC 2200的燃烧数值相比,协效阻燃剂的质量分数为10.0%时,热释放速率降至367J/(g·K),降低了37.16%,热释放速率峰值为510.8W/g,降低了37.85%,总热释放量为17.6kJ/g,降低了15.38%。
4)通过热重分析,研究了协效阻燃PC的热重过程。添加阻燃剂后可以使PC的热分解延迟,残炭率从0.22%增加到13.19%。
(四)芳基二磷酸酯改性聚碳酸酯
1.原材料与配方(质量份)

2.制备方法
(1)DMP-RDP及DMP-HDP的合成 图3-2中给出了两种芳基二磷酸酯DMP-RDP及DMP-HDP的合成路线,具体的合成方法为:在装有温度计、恒压滴液漏斗和回流冷凝管的四口瓶中先加入48.87g的2,6-二甲酚和0.5g无水氯化铝,边搅拌边升温至110℃,滴加30.7g三氯氧磷,2h后滴加完毕,然后逐渐升温控制反应。稳定进行至磷酰化反应完全。反应结束后将体系温度降至100℃,加入11g间苯二酚和0.25g无水氯化铝,逐渐升温至反应稳定,5h后反应结束。体系自然冷却至50℃左右,向反应瓶中加入乙醇与水的混合液,然后加热回流1.5h后将体系温度降至30℃,此时向体系中滴加10mL浓度为10%的盐酸溶液,体系变成白色浑浊液体,用冰水冷却后,变成白色黏稠液体,静置一段时间后溶液中出现白色的固体。抽滤、烘干后得到白色粉末状固体,产率为94.2%。
按照上述反应方法,将间苯二酚换成对苯二酚时,合成了白色粉末状的DMP-HDP,产率为95.3%。

图3-2 DMP-RDP和DMP-HDP的合成路线
(2)阻燃PC材料的制备 将PC在120℃下于鼓风干燥箱中烘干4h,阻燃剂DMP- RDP和DMP-HDP在60℃下真空烘干12h。将PC分别与DMP-RDP和DMP-HDP按一定的质量配比在转矩流变仪中加热熔融混合均匀,取出后压片,制成标准试样进行性能测试。
3.性能
由表3-50可知,DMP-RDP及DMP-HDP的起始热分解温度(Tinitial)(失重1%)分别为269℃及222℃,说明合成的两种化合物具有较好的热稳定性,能满足大多数聚合物的加工温度要求。两种芳基二磷酸酯在800℃的残炭率都为0,说明合成的产物在高温情况下都会完全分解,其中DMP-RDP在399℃出现最大热分解速率峰,其最大热失重速率为20.5%/min,而DMP-HDP在404℃时出现最大热分解速率峰,对应的热失重速率为14.7%/min。
表3-50 DMP-RDP及DMP-HDP的热重分析数据

表3-51和表3-52分别为添加了不同量阻燃剂DMP-RDP和DMP-HDP的阻燃PC的阻燃性能测试结果。纯PC的极限氧指数(LOI)为28%,能通过UL94 V-2级,而当阻燃剂DMP-RDP的添加量为4%时,阻燃PC的LOI达到34.8%,材料通过了UL94 V-0级,并且随着DMP-RDP添加量的增大,LOI值逐渐增大。
表3-51 同DMP-RDP添加量PC的阻燃性能

表3-52 不同DMP-HDP添加量PC的阻燃性能

同时,当DMP-HDP的添加量也为4%时,阻燃PC的LOI值达到34.2%,材料通过UL94 V-0级,并且随着添加量的增大,LOI也明显增大。测试结果表明,合成的阻燃剂对PC具有很好的阻燃效果。
4.效果
有人采用无溶剂技术成功制备了两种芳基二磷酸酯阻燃剂,合成过程更加方便及环保,并对其化学结构进行了表征确认。合成的两种磷酸酯阻燃剂具有较好的热稳定性,能满足大多数聚合物的加工要求。当合成的磷酸酯阻燃剂的添加量仅为4%时,材料能成功通过UL94 V-0级,LOI达到了34%以上,对PC材料具有很好的阻燃效果。
(五)无卤阻燃ACS/PC合金
1.原材料与配方(质量份)

2.制备方法
将PC于120℃干燥6h,ACS和增容剂AS-g-MAH于80℃干燥4h,将ACS、PC、增容剂、阻燃剂等按上述配方中的用量加入高混机,于1000r/min混合10min出料,用双螺杆挤出机挤出造粒,挤出机温度为180~205℃,螺杆转速为150~200r/min。采用注射机制样,注射温度为150~215℃。
3.性能
固定ACS、PC、AS-g-MAH的质量比为75∶25∶5,考察磷系阻燃剂对阻燃ACS/PC阻燃性能和力学性能的影响,结果见表3-53。
表3-53 阻燃剂用量对阻燃ACS/PC综合性能的影响

从表3-54中的数据可知,在相同基础配方的条件下,阻燃ACS中添加较少量的磷酸酯即可达到V-0阻燃等级,而阻燃ABS/PC中磷酸酯的添加量则明显偏高。磷酸酯阻燃ACS/PC既含磷元素,又含氯元素,受热燃烧时,磷酸酯生成聚偏磷酸保护膜,ACS可放出难燃性HCl气体,HCl能与火焰中活性自由基·OH、·O·和·H发生反应,从而切断火焰的自由基反应。磷酸酯阻燃ACS/PC存在磷-氯协同效应,进一步提高了阻燃效果。此外,经人工紫外老化120h后,阻燃ACS/PC的色差大幅低于阻燃ABS/PC,这也验证了线性饱和CPE橡胶的耐候性能显著优于聚丁二烯橡胶。
表3-54 磷酸酯阻燃ACS/PC、ABS/PC的性能对比

注:ACS/PC中ACS与PC的质量比为75∶25,ABS/PC中ABS与PC的质量比为75∶25。
4.效果
1)适量添加PC可改善ACS的力学性能和HDT,PC用量过高会引起ACS热降解从而导致性能恶化。
2)增容剂AS-g-MAH可在一定程度上改善阻燃ACS/PC的冲击性能,但不宜添加过量,否则易导致材料的性能下降。
3)固体磷酸酯与ACS存在磷-氯协同效应,磷酸酯阻燃ACS/PC的生产成本相对较低,相对磷酸酯阻燃ABS/PC,其耐候性更好,综合性能较优。
(六)聚硼硅氧烷-有机磷酸酯阻燃改性聚碳酸酯
1.原材料与配方(质量份)

2.制备方法
首先将PC原材料在102℃下干燥处理24h,然后将物料称重,投入混合器中在260℃下混合,直至混合均匀。其制品可在290℃下用注射机注射成型。
3.性能与效果
1)对聚硼硅氧烷-有机磷酸酯(PB-OPP)阻燃剂复配阻燃聚碳酸酯(PC)体系研究结果表明,添加PB阻燃剂可以提高体系的极限氧指数(LOI),当PB阻燃剂质量分数小于1.25%时,提高不明显,有的体系反而略有下降,其主要原因是OPP阻燃剂的熔滴作用影响,OPP阻燃剂的熔滴作用使燃烧残炭无法在PC的燃烧表面均匀覆盖。当PB含量增加,成炭作用成为主要阻燃机制,熔滴作用被削弱,复配阻燃PC体系(FR- PC)的LOI提高。
2)PB阻燃剂对PC具有促进成炭的作用,在PB-OPP/PC复合阻燃体系中,PB降解生成的Si-O-Si和B-Si炭层和OPP生成的液态酸膜覆盖在FR-PC燃烧表面,阻碍热量和氧气的交换、抑制可燃性气体逸出,使得FR-PC燃烧过程中热量、烟以及CO释放速率均有不同程度的降低,缓和了整个燃烧过程,保证热量与外界环境及时传递,减小了火灾危害。
3)适当添加PB,可以提高OPP/PC体系的拉伸强度、弯曲强度、维卡软化点以及材料的透光率。
(七)聚铝硅氧烷阻燃改性聚碳酸酯
1.原材料与配方(质量份)

2.制备方法
首先将PC在100~110℃下干燥10~24h,然后用挤出机按照配方比例称量喂料,使其混合挤出造粒待用。
3.性能与效果
1)5%的聚铝硅氧烷阻燃PC材料的拉伸强度在54.9~58.5MPa之间,与纯PC的拉伸强度55.0MPa相比有明显提高。
2)5%的聚铝硅氧烷对PC弯曲强度的影响较小。
3)5%的聚铝硅氧烷可明显提高PC的冲击强度,R/Si=2.0、Ph/Me=6/4的聚铝硅氧烷阻燃PC的冲击强度最高,为21.0kJ/m2,比纯PC提高了31%。
4)PC/聚铝硅氧烷的维卡软化点随着聚铝硅氧烷含量的增加先增后降,聚铝硅氧烷含量低于8%时,均使PC的维卡软化点得到提高。
(八)纳米氧化锑(ATO)改性聚碳酸酯阻红外隔热复合材料
1.原材料与配方(质量份)

2.制备方法
(1)纳米ATO/PC复合材料的制备 称取49.85g的PC溶于150mL四氢呋喃中,在磁力搅拌下加热回流,以1~3滴/s的速度滴加7.5g浓度为2%的纳米ATO-四氢呋喃分散液。滴加完毕后,继续搅拌回流并使其凝胶熟化,脱除溶剂,于120℃下干燥2h,即得到纳米ATO含量为0.3%的纳米ATO/PC复合材料。改变PC的质量及ATO的添加量即可制得其他纳米ATO含量的纳米ATO/PC复合材料。
(2)硅烷改性纳米ATO/PC复合材料的制备 称取49.85g的PC溶于150mL四氢呋喃中,在磁力搅拌下加热回流,以1~3滴/s的速度滴加7.5g浓度为2%的硅烷偶联剂KH-570改性纳米ATO-四氢呋喃分散液。滴加完毕后,继续搅拌回流并使其凝胶熟化,脱除溶剂及水,于120℃下干燥2h,即得到纳米ATO含量为0.3%的硅烷改性纳米ATO/PC复合材料。改变PC的质量及硅烷偶联剂KH-570改性纳米ATO的添加量即可制得其他纳米ATO含量的硅烷改性纳米ATO/PC复合材料。
3.性能
表3-55为不同硅烷改性纳米ATO含量的纳米ATO/PC复合材料的力学性能。
表3-55 不同硅烷改性纳米ATO含量的纳米ATO/PC复合材料的力学性能

纯PC在可见光区域的透射率高达90%;当纳米ATO的含量为0.3%~0.5%时,纳米ATO/PC复合材料的透射率降低至80%左右,这说明纳米ATO的加入在一定程度上影响了PC的可见光透射率,但复合材料的可见光透射率仍维持在较高水平;当纳米ATO含量提升至0.6%~0.7%时,纳米ATO/PC复合材料的透射率进一步降低。
纯PC膜片测试盒及纳米ATO含量分别为0.3%、0.4%、0.5%、0.6%和0.7%的纳米ATO/PC膜片测试盒的内外温差ΔT分别为1.6℃、2.5℃、3.1℃、3.9℃、4.2℃和4.5℃。由此可见,随着PC膜片中纳米ATO粒子含量的增加,纳米ATO/PC复合膜片的隔热性能逐渐增强。
4.效果
通过溶胶-凝胶法制备出不同纳米氧化锑锡(ATO)含量的纳米ATO/聚碳酸酯(PC)复合材料,性能测试结果表明:
1)经硅烷偶联剂KH-570改性后,纳米ATO的团聚现象明显减弱,平均粒径为60~80nm,在PC基体中分散均匀。
2)纳米ATO粒子具有很好的阻红外隔热能力,随着PC基体中纳米ATO粒子含量的增加,纳米ATO/PC复合材料的阻红外隔热能力逐渐提升,力学性能没有明显变差,但透明性却相应下降。
3)当改性纳米ATO的加入量为0.5%时,可在确保80%可见光透射率的情况下,获得尽可能高的阻红外隔热性能。
(九)膨化石墨填充PC/ABS导电材料
1.原材料与配方(质量份)

2.制备方法
可膨化石墨先经高温烧制成EG,制备的EG分成两类,一类未经处理,一类经过砂磨机研磨(转速为800r/min)后,再经超声(1200W)破碎。PC和ABS按7∶3的比例和两类EG分别按特定的比例,并加入PC/ABS相容剂600A密炼混合,制备PC/ABS/EG共混物。
3.性能
石墨拥有比炭黑、碳纳米管(CNT)、碳纤维等炭族填充物更优良的导电性能,炭黑、CNT由于粒径为纳米级别,表面能太高,容易团聚,如何均匀地分散在共混物中一直是个难题。石墨由于表面能相对较小,团聚得非常轻微,因此在共混物中的分散性能更好。一般来说,对于同一种颗粒,颗粒分散得越均匀,排列得越规整,共混物的导电性就越好。石墨由于是片状、长条形颗粒,在基体中更容易形成导电网络。因此,破碎后的石墨(TEG)比破碎前的EG填充到共混物中导电性能更佳。研究结果表明,TEG添加到共混物中,使其电阻率得到了明显的降低,导电性能大幅提升;颗粒粒径较大的EG添加到共混物中,共混物的电阻率降低的不明显,这是由于颗粒较大,同等添加量下填充在基体中不利于导电网络的形成。TEG的添加量从3%提升到5%时,共混物的电阻率降低了9个数量级。
随着EG的加入,共混物的拉伸强度从42.53MPa增加到添加量为2%时的47.14MPa,增幅为10.8%;而随着TEG的加入,共混物的拉伸强度最大增加到添加量为3%时的54.22MPa,增幅达到27.5%。
随着EG的加入,共混物的冲击强度从41.03kJ/m2增加到43.9kJ/m2,增幅为7%;而TEG的加入能使其冲击强度最大达到46.5kJ/m2,增幅达13.3%。TEG对共混物拉伸强度的提高优于对冲击强度的提高。未添加EG的PC/ABS共混物的降解温度为396℃,添加了5%TEG的共混物其降解温度提高到408℃,提高了12℃,共混物的热稳定性得到了极大提升。在600℃时,PC/ABS已经降解完,而此时PC/ABS/TEG的残余量仍有8%左右,到750℃仍有5%的残余量。
4.效果
TEG相对于EG在共混物中的分布更为均匀,与共混物的相容性更好,对共混物性能的提升更为明显。TEG的添加量从3%提升到5%时,共混物的电阻率降低了9个数量级;当添加量为5%时,共混物的降解温度提高了12℃;TEG的加入使共混物的拉伸强度提高了27.5%,冲击强度提高了13.3%,比EG对共混物的拉伸强度、冲击强度的提升分别高了16.7%和6.3%。