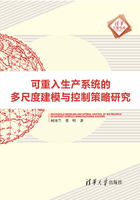
第1章 绪论
1.1 研究背景与课题意义
随着信息产业的迅速发展,可重入生产系统(re-entrant lines)已成为国内外制造界和学术界研究的热点,特别是半导体芯片制造系统,是当今最为复杂的制造系统的典型代表之一。为了提高半导体芯片制造系统各方面的性能指标,有效解决该生产线的建模与优化控制问题已成为半导体制造业研究的焦点。
由于半导体制造业为了满足消费市场紧急订单的达到,比如,短期需求波动和与季节性相关的长期需求结构的变化、引入新的产品或是淘汰旧的产品进行参数化、对产品更新的需求,不断进行新品、新款设计与开发等,增大对市场的产品投入力度,影响系统短期规模和长期规模的产出量,使得半导体芯片制造系统的控制问题变得越来越复杂,严重制约了需求管理的绩效。为了提升我国半导体芯片制造产业国际的竞争能力,不仅要扩大规模,而且要提高系统的产能,降低生产周期,以适应动态变化的市场需求情况。为了把我国的半导体芯片做大做强,不仅需要先进的半导体芯片设计技术、制造工艺技术及装备技术,而且需要先进的生产管理控制技术,从而可以在半导体芯片制造系统中实施高效的生产管理方法。
1.1.1 可重入生产系统的提出及基本特点
半导体制造过程一般分为硅片制造(wafer fabrication)、硅片针测(wafer probe)、芯片封装(assembly and packaging)及最后的综合性能测试(final testing)四个阶段。硅片制造是半导体制造过程中加工工艺最为复杂和关键的部分,同时也是资金投入量最高、耗时最长的部分,占据了我国半导体产业发展的主流地位[1]。相比一般制造系统而言,半导体制造系统中重复访问的机器设备具有更多的在制品(work-in-process,WIP)等待加工。这种重复访问是由于工艺过程的需要;不同于一般制造系统中不良品的返修(重加工,rework)。因此,Kumar等(1993)[2]根据工件在加工路径中呈现规律性重入的典型特点,提出了“可重入生产系统”的概念,是继作业车间(job shop)和流水车间(flow shop)之后的第三类生产系统。图1-1给出了一个简单的可重入生产系统,其中,Mi(i=1,2,3)表示加工设备,Bj(j=1,2,…,5)表示缓冲区,也代表工件的加工工序,箭头表示工件的加工流程。从图1-1中可以很明显看出工件重复进入加工机器的特点。

图1-1 可重入生产线典型结构
半导体生产线存在重入现象的原因:一方面是工件加工工艺过程的需要;另一方面是为了提高加工设备的利用率和资源共享。由于加工设备极其昂贵,工件需要在不同的加工阶段重复访问某些机器,这就使得可能在同一机器前存在不同加工阶段的工件同时等待加工的现象[3]。
以半导体芯片制造为典型代表的可重入生产系统,与其他生产系统相比,不仅具有多重入性,而且具有高度的复杂性。主要表现在以下几个方面。
1.多尺度特征
可重入生产系统的多尺度特征主要体现在以下三个方面。第一,晶圆制造工厂、芯片封装及测试工厂等代表可重入生产系统中的宏观空间结构,而各个具体的工厂内部的产品流则代表了可重入生产系统中的微观尺度空间结构。第二,可重入生产系统中的长期、战略层面的决策(如中长期生产计划)属于宏观时间尺度,而可重入生产系统中各个工厂内部的局部控制、短期决策则属于微观时间尺度。第三,同一芯片类型中不同的加工层次(即多重入特征)。因此,可重入生产系统涉及多个空间、时间、层次的尺度结构。
2.分布式按订单生产模式
随着市场需求的多元化,企业只有在最短的时间内生产出满足不同顾客要求的高质量产品,才能抢占市场。由此,半导体制造系统正在从原始按库存的生产模式逐渐转向具有分布式特点的按订单的代工生产模式(foundry fab),这是未来半导体生产管理面临的一个挑战。
3.多种产品混合制造、工艺流程复杂、制造周期长
半导体芯片制造的整个加工过程复杂,工序繁多,不同产品具有不同的加工工艺流程和要求,即使是同一种产品,在不同加工阶段的加工顺序和要求也不完全一致。另外就是制造周期长,使得生产系统中存在大量的在制品(WIP)。
4.系统规模庞大、资源要素繁多
晶圆制造是一个规模相当庞大,资源要素错综复杂的系统。系统中包含300余台各种昂贵的加工设备,设备费用将占整个工厂的70%以上。因此,应不断提高加工设备的利用率,避免加工设备的闲置造成资源的浪费。与此同时,晶圆制造的混合流程生产方式增加了资源组织结构的复杂性,即不仅要求制造资源按照功能相同或相似进行多层次的组织,而且总体布局上又必须服从于大多数产品的生产流程。
5.多目标优化
半导体芯片制造系统优化是指在提高设备的利用率、控制系统WIP水平、缩短生产周期、提高多样订单的准时交货率等相互冲突的多目标之间做出权衡的一种策略。因此,需要对半导体芯片制造系统进行合理的建模、分析,以提出更好的优化控制生产方案。
6.不确定性、随机因素的干扰
订单是由预测得到的,具有不确定性的特点,使得按订单生产这种模式的生产计划与控制非常困难。晶圆制造设备均为精细的高端设备,容易出现难以预测的、类型繁多的故障而停机,势必影响系统的产能。由于硅片产品制造过程对环境(高度洁净)与工艺参数非常敏感,成品率是不确定的。此外,成品率还受晶圆在生产线上滞留时间的长短影响:加工时间周期越长,暴露在灰尘下的时间越久,则成品率越低,而成品率的不确定性势必影响实际产出率和投料计划。
1.1.2 可重入生产系统的建模方法
对复杂的半导体芯片生产系统进行有效建模的目的是可以对系统的稳定性、敏感性等性能进行分析,以作为模型改进和调度策略研究的依据,从而对可重入生产系统进行有效的生产控制[4]-[6]。由于实际的半导体生产系统极其复杂,因此要把生产系统中所有的细节都列举出来是极其困难的。因此,所建立的模型只是实际生产系统的一个简化模型。生产系统的建模对研究生产系统运行特性、投料和调度策略的优劣等方面有重要作用。因此,为了对实际半导体制造过程进行优化调度,采用有效的建模工具和建模方法是关键前提。
目前,国内外关于半导体芯片制造模型方面做了大量的研究工作。总的来说,主要有以下几种:排队网络模型、Brownian模型、Petri网模型、流体网络模型、连续模型、仿真模型等。通过对上述建模方法进行综合比较分析,可以知道这些模型均在某些方面表现出一定的优越性,且都有其自身无法克服的缺陷。由于半导体芯片制造系统是一个高度复杂的制造系统,利用离散建模的方法可以模拟出系统中很多细节的东西,得到非常精确的模拟结果。但随着系统复杂度的增加,建立这种具有很多细节的模型却越来越难,甚至出现“维数灾难”而无法求解。
近年来,一些学者[7]-[9]针对可重入生产系统提出了一种新的模型。在这些模型中,将流经生产系统的工件流依据交通中的车辆流[10]形式进行建模。通过引入产品“完成度”的概念[11],在不考虑物料损失的情况下,利用物料守恒定律和流体模型中的连续队列长度的概念结合起来,建立双曲型偏微分守恒方程(partial differential equation,PDE)模型。对生产系统采用连续建模的方法,虽然不能像离散模型那样反映系统的很多细节问题,但是它不受系统规模的影响,能非常快速地得到数值结果,并且随着系统复杂度的增加模拟结果越精确。另外,采用连续建模的方法可以很好地反映系统的瞬态行为。因此,连续建模的方法可以从整体上对一个大规模复杂制造系统的整体性能进行评估,并可以解决长期生产制造系统的优化控制问题[12]。
1.1.3 可重入生产系统的优化控制策略
在半导体生产系统中,从对系统控制[13]的角度来看,影响或控制系统产出率的方式主要有两种:一种是投料速率的控制,主要指安排投料时间、投料数量及产品类型的投料顺序;另一种是调度策略的控制,主要指安排生产线中各类工件在各类设备上的实际加工序列和开始加工时间。研究表明,投料策略对生产系统的性能指标有非常大的影响,特别是对多种产品同时加工的生产系统。对一般制造企业而言,FIFO是最直接有效的调度策略,而物料投放策略,会根据资源状况及订单需求,合理控制物料的投放时间与数量。
1.投料控制
投料控制用于决定何时投入多少不同种类的物料到生产系统,在保证系统生产能力满足的情况下,同时优化生产系统的性能指标以满足客户需要,是半导体芯片工厂进行有效生产控制的关键一环[14]。因此,合理的投料策略不仅可以提高生产系统的运行性能,提高机台利用率,同时为后续的优化调度问题提供重要的保障。相反,则直接导致生产系统效益的低下。在实际的生产系统中,为了追求机台的高利用率,可以通过系统的投料策略来避免机台的闲置,因此容易造成过早投料的情形;然而,在追求机台高利用率时,则必须相对地投入更多的在制品,从而使得生产系统中堆积过多的在制品,导致生产周期过长,资金成本的过早投入以及产品良率的下降[15]。
为了在较长时期内对生产系统的整体性能与指标进行分析,基于PDE模型,通过对系统投料速率的控制以获得期望的系统产出率是本书研究的关键问题之一。对多产品种类(multiple product)的生产线而言,存在多种不同的产品同时等待加工的过程,因此,投料策略对系统中各产品性能指标的影响是很大的。为了提高系统中不同产品的准时交货率,使得一定时间周期内系统的产出量和市场需求量相同或尽可能相近,本书提出了多产品可重入生产系统的最优投料控制策略。
2.调度策略
目前,根据研究的重点和采用研究方法的不同,半导体制造系统的调度问题已经取得了大量的研究成果。总体而言,这些调度策略存在以下一些不足[16]:①调度策略优化的目标比较单一;②调度策略难以适应随机、动态系统,大多是基于静态调度策略;③由于制造系统具有高度复杂性的特点,给建模带来了极大的困难,因此调度策略很少是基于模型的,大多数都是基于启发式的。结合以上三点不足,建立基于模型的、满足多目标优化及实时动态的调度策略成为当前研究的主要方向。
由于半导体芯片的生产周期较长,大多数时候,需求的波动变化相比工厂的加工周期是在一个更短的时间尺度上进行的,使得采用初始调度策略来响应波动的市场需求量问题变得越来越困难。由于生产过程的随机性和需求波动的变化,所以在产出量和需求量之间存在差异。在实际生产过程中,给定一段时间内的生产目标,为了减少产出量和需求量之间的差值,并且硅片的后期加工过程可以通过调度策略来加快或是减慢。针对具有大需求量的波动情况,需要通过调整系统的投料速率来弥补期望在制品的变化,在这里主要考虑如何应对小需求量的变化情况。
目前,几乎没有文献提到如何解决:晶圆制造厂在满足其生产能力的情况下,收到意外订单时,系统中的产品将会出现剧增或是短时间内硅片的突然增加所带来的影响。为了能更好地控制生产系统以响应动态变化的市场需求量情况,提出了一个新的控制变量——“推拉点”的概念,建立了基于推拉调度策略的连续模型。建立该模型的基本原理是:在推拉点位置前端的生产线采取推式调度策略,同时在推拉点位置后端的生产线采取拉式调度策略。为了提高生产系统的准时交货率,通过调整系统中的生产加工步来有效控制系统的产出率。基于推拉调度策略的连续模型,根据不同的控制原理,依次提出了基于推拉点的调度控制策略和基于推拉点的线性反馈控制策略,仅仅依靠移动推拉点本身来实时响应动态变化的市场需求量问题。