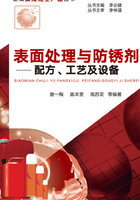
1.2 金属表面处理剂的配方类型
1.2.1 防锈剂
防锈剂是一种超级高效的合成渗透剂,它能强力渗入铁锈、腐蚀物、油污内,从而轻松地清除掉金属的锈迹和腐蚀物,具有渗透除锈、松动润滑、抵制腐蚀、保护金属等性能。并可在部件表面上形成并储存一层润滑膜,可以抑制湿气及许多其他化学成分造成的腐蚀。
常见的水基防锈剂有乙醇胺与酸的复配防锈剂、多元醇酯防锈剂、金属表面自组装防锈剂、硅烷偶联防锈剂、气相防锈剂。
①乙醇胺包括单乙醇胺、二乙醇胺及三乙醇胺,与它们复配的酸可以是无机酸和有机酸。醇胺与酸常温下复配生成醇胺盐。单乙醇胺与二乙醇胺与羧酸加热生成的酰胺也是一种很有效的防锈剂,很稀的烷基醇酰胺溶液既能防止钢铁生锈,又具有良好的耐水解性能,同时对防锈水有增稠作用,从而避免了防锈剂从金属表面流失,并使防锈剂在金属表面牢固附着。有机羧酸醇胺盐和烷基醇酰胺分子中的氮原子和氧原子都有孤对电子,可与铁等有空轨道的金属表面作用生成配合物膜,阻止氧、水等分子与金属表面接触。
②失水山梨醇单油酸酯是一种性能优良的多元醇酯防锈剂,其他还有季戊四醇酯等。
③有机物分子在溶液中能自发地吸附在金属表面,形成一层取向性好、排列紧密的疏水性单分子层,可有效阻止水分子、氧分子及电子向金属表面的传输,使基体金属发生氧化的临界电位正移,金属表面的氧化-还原电流显著降低,从而起到对金属的保护作用,这个过程就是防锈剂分子在金属表面的自组装。
④硅烷偶联剂按其化学结构可分为两大类:单硅烷和双硅烷偶联剂,二者的结构通式分别为Y—(CH2)n—Si—(OR)3和(RO)3—Si—(CH2)n—Y—(CH2)n—Si—(OR)3,其中,Y为官能团,RO—为可水解的烷氧基。硅烷偶联剂被用于金属材料的防锈剂,并有望替代铬酸盐钝化和传统的磷化工艺。当用于防锈剂时,先让硅烷进行水解,生成的硅醇与金属表面的氧化物或氢氧化物发生缩合反应产生Si—O—Me共价键,Me代表被保护的金属,而吸附在金属表面的剩余的—SiOH基团彼此间进行缩合反应而形成致密的硅烷膜。
⑤气相防锈剂是在常温下有较大蒸气压的防锈化学品,把它溶解在水中即得气相防锈水,挥发后的气体吸附在金属表面后,能抑制金属的阴、阳极的电化学反应。
常见的油基防锈剂有软膜防锈油和硬膜防锈油。软膜防锈油由矿物油(如煤油、柴油、机油或润滑油)、油溶性缓蚀剂(如石油磺酸钡、硬脂酸铝)和其他添加剂组成,其特点是操作简单,具有一定的防锈效果(室内存放防锈期2~3月)。硬膜防锈油是将有机树脂(如生漆片、醇酸树脂、聚酯树脂、丙烯酸树脂、环氧树脂等)溶解于有机溶剂(如二甲苯、丙酮、乙酸乙酯等),属于传统的有机涂层防腐处理。
1.2.2 磷化液
磷化是金属与稀磷酸或酸性磷酸盐反应而形成磷酸盐保护膜的过程。磷化液的主要成分是磷酸二氢盐[如Zn(H2PO4)2]以及适量的游离磷酸和加速剂等。加速剂主要起降低磷化温度和加快磷化速率的作用。作为化学加速剂用得最多的氧化剂如、
、
、H2O2等。
磷化液的配制原则:磷化液应包括乳化性能优异的各种表面活性剂及洗涤剂等组成的去油剂;对金属锈蚀产物有较强溶解作用的酸液、酸式盐,包括有机酸在内组成的除锈剂;对金属表面垢质有较好分解和溶化性能的无机、有机酸和盐类所组成的去垢剂;为确保磷化液在使用中不腐蚀基本金属,加入相应的高效缓蚀剂;为增加对金属表面的保护作用,加入能和基本金属生成钝化膜层的钝化剂,以及在去锈、脱脂、去垢等作用后,能使金属表面生成有很强防腐蚀性能的磷化剂等。
磷化液的基本平衡方程式:
3M(H2PO4)2M3(PO4)2+4H3PO4
此方程的平衡常数K=[M3(PO4)2][H3PO4]4/[M(H2PO4)2]3,M代表Zn、Mn等。可以看出,常数K值越大,磷酸盐沉积的比率越大。而K值与一代和三代金属盐的金属的性质、溶液的温度、pH值及总浓度有关。所以影响磷化液性能的因素至少有pH值、游离酸度、总酸度、温度、离子浓度、金属性质、水质等。
①pH值。锰系磷化液一般控制在2~3之间,当pH>3时,共件表面易生成粉末。当pH<1.5时难以成膜。铁系一般控制在3~5.5之间。
②游离酸度。游离酸度指游离的磷酸的浓度。其作用是促使铁的溶解,以形成较多的晶核,使膜结晶致密。游离酸度过高,则与铁作用加快,会大量析出氢,令界面层磷酸盐不易饱和,导致晶核形成困难,膜层结构疏松、多孔、耐蚀性下降,令磷化时间延长。游离酸度过低,磷化膜变薄,甚至无膜。
③总酸度。总酸度指磷酸盐、硝酸盐和酸的浓度总和。总酸度一般以控制在规定范围上限为好,有利于加速磷化反应,使膜层晶粒细,磷化过程中,总酸度不断下降,反应缓慢。总酸度过高,膜层变薄,可加水稀释。总酸度过低,膜层疏松粗糙。
④温度。温度越高,磷化层越厚,结晶越粗大。温度越低,磷化层越薄,结晶越细。但温度不宜过高,否则Fe2+易被氧化成Fe3+,加大沉淀物量,溶液不稳定。
⑤离子浓度。Fe2+的影响:溶液中Fe2+极易氧化成Fe3+,导致不易成膜,因此,溶液中Fe2+浓度不能过高,否则,形成的膜晶粒粗大,膜表面有白色浮灰,耐蚀性及耐热性下降;Zn2+的影响:当Zn2+浓度过高,磷化膜晶粒粗大,脆性增大,表面呈白色浮灰;当Zn2+浓度过低,膜层疏松变暗。
⑥金属性质。金属工件表面状态对磷化质量影响较大,即使是同一磷化工艺、同一磷化制剂、同一工件的不同部位的磷化膜质量也可能相差较大,这是由工件表面状态差异所致。一般来说,高、中碳钢和低合金钢容易磷化,磷化膜黑而厚,但磷化膜结晶有变粗的倾向,低碳钢磷化膜结晶致密,颜色较浅,若磷化前进行适当的酸洗,可有助于提高磷化膜质量,冷轧板因其表面有硬化层,磷化前最好进行适当的酸洗或表调,否则膜不均匀,膜薄,耐蚀性低。
⑦水质。磷化后用水冲洗磷化膜的作用是去除吸附在膜表面的可溶性物质等,以防止涂膜在湿热条件下起泡、脱落,提高涂膜附着力、耐腐蚀性,通过对同一磷化膜分别采用去离子水、下水道水、车间排放水冲洗实验得知其耐蚀性、柔韧性逐个降低。对于要求较严的阴极电泳涂装,最好在涂装前采用去离子水水洗。
磷化作用如下:
涂装前磷化的作用:增强涂装膜层(如涂料涂层)与工件间结合力;提高涂装后工件表面涂层的耐蚀性;提高装饰性。
非涂装磷化的作用:提高工件的耐磨性;使工件在机加工过程中具有润滑性;提高工件的耐蚀性。
1.2.3 钝化液
钝化液是能使金属表面呈钝态的溶液。一般用于镀锌、镀镉和其他镀层的镀后处理。目的是在镀层表面形成能阻止金属正常反应(氧化)的表面状态,提高其抗蚀性,并增加产品美观。通过配方分析可知,常用的钝化液主要成分是含铬酸根、硝酸根、硫酸根等的金属盐类。
1.2.4 缓蚀剂
缓蚀剂也可以称为腐蚀抑制剂,是一种以适当的浓度和形式存在于环境(介质)中时,可以防止或减缓腐蚀的化学物质或几种化学物质的混合物。
合理使用缓蚀剂是防止金属及其合金在环境介质中发生腐蚀的有效方法。它的用量很小(0.1%~1%),但效果显著,同时还能保持金属材料原来的物理、力学性能不变。主要用于中性介质(锅炉用水、循环冷却水)、酸性介质(除锅垢的盐酸,电镀前镀件除锈用的酸浸溶液)和气体介质(气相缓蚀剂)。缓蚀效率越高,抑制腐蚀的效果越好。有时较低剂量的几种不同类缓蚀剂配合使用可获得较好的缓蚀效果,这种作用称为协同效应;相反地,若不同类型缓蚀剂共同使用时反而降低各自的缓蚀效率,则称为拮抗效应。
按照缓蚀剂作用的电化学理论进行分类,缓蚀剂可分为阳极型缓蚀剂、阴极型缓蚀剂和混合型缓蚀剂。
依据物质中元素组成,缓蚀剂可分为有机缓蚀剂和无机缓蚀剂。
有机缓蚀剂主要有醛类、胺类、有机硫化合物、杂环化合物、羧酸及其盐类、磺酸及其盐类等。有机缓蚀剂通常是由电负性较大的O、N、S和P等原子为中心的极性基及C、H原子组成的非极性基所构成的,能够以某种键的形式与金属表面相结合。有机缓蚀剂的缓蚀机制大多数符合吸附膜理论。
无机缓蚀剂的种类相对于有机缓蚀剂少,而且它要在较高的浓度下才能有效工作。与有机缓蚀剂的作用机制不同,无机缓蚀剂一般是通过氧化金属表面而生成钝化氧化物膜或者在金属表面阴极区形成沉淀膜来抑制腐蚀反应的进行。传统的无机缓蚀剂主要有硅酸盐、磷酸盐和铬酸盐等。其中,磷酸盐和铬酸盐对环境有较大的污染,其应用已逐渐减少。钼酸盐、钨酸盐和稀土化合物等是近期开发应用的、对环境友好的无机缓蚀剂。
根据缓蚀剂在金属表面所形成的保护膜具有的性质,缓蚀剂可被分为氧化膜型、沉淀膜型和吸附膜型三类。
氧化膜型缓蚀剂是指可以直接或间接地氧化金属,在金属表面形成相应的氧化膜型薄膜,阻止腐蚀反应进行的缓蚀剂。但氧化型缓蚀剂存在着一定的缺点:它主要对可钝化金属(铁族过渡金属)表现出良好的保护作用,而对不钝化金属如铜、锌和镁等金属将没有很大的效果。
沉淀膜型缓蚀剂的特点是缓蚀剂会与溶液中离子发生化学反应而产生相应的难溶于水的沉淀物,从而减缓金属的腐蚀。目前沉淀型缓蚀剂主要有硫酸锌、碳酸氢钙、聚磷酸钠等无机盐。
吸附膜型缓蚀剂一般是有机化合物,因有机化合物中多存在着极性基因,这样的极性基团可以被金属表面所存在的电荷吸附,从而在金属表面的阳极和阴极区域形成一层单分子膜,这样就可以阻止或减缓金属表面上所存在的电化学反应。如某些含氮、含硫或含羟基等官能团的有机化合物,因其分子中含有两种性质相反的基团:亲水基和亲油基。这样的化合物分子会以亲水基(例如,羟基、氨基等)吸附于金属表面上,形成一层致密的憎水膜,从而保护金属表面不受腐蚀。
吸附膜型缓蚀剂所形成的吸附膜的稳定性和缓蚀性能取决于金属/溶液界面上缓蚀剂吸附膜和界面以及吸附膜分子之间的相互作用力。形成具有较高覆盖度、稳定性强的吸附膜,是产生缓蚀作用的前提。吸附膜的稳定性取决于吸附粒子与金属表面的相互作用力(包括化学吸附和静电相互作用)和吸附粒子之间的相互作用力。缓蚀剂中高电负性的O、N、P、S等元素的亲水性极性基团与表面金属原子未占据的空d轨道形成配位键吸附于金属/溶液之间的界面处,降低金属表面的能量,使能量趋于逐步稳定,腐蚀反应的活化能升高,从而导致金属的腐蚀速率降低;同时,缓蚀剂分子中所含有的非极性基团在金属表面所形成的疏水性的保护层,阻碍金属表面上与腐蚀反应有关的电荷或物质的转移,也会进一步阻碍金属的腐蚀过程。
由于缓蚀剂的缓蚀机理在于能在金属表面成膜,从而阻止金属表面与腐蚀介质的直接接触。为了迅速在金属表面成膜,应要求水中缓蚀剂的浓度足够高,待膜形成后,再降至只对膜的破损起修补作用的浓度;为了得到致密的膜层,金属表面应十分清洁,因此成膜前必须对金属表面进行化学清洗除油、除污和除垢。
1.2.5 抛光液
抛光是通常用于金属表面经过精磨光以后,需要进一步降低表面粗糙度和使表面出现光泽所进行的精加工。抛光的主要目的是减小金属表面粗糙度,改善制品的表面光洁程度,进一步除去制品表面的细微缺陷,得到光亮美观的表面,或者为后续表面处理(如电镀、化学镀等)做好准备。
抛光液通常是一种不含任何硫、磷、氯添加剂的水溶性抛光剂。抛光液的化学成分和周围介质在抛光过程中与抛光金属发生化学反应,大大加强了抛光效果。抛光液应具有良好的去油污、防锈、清洗和增光性能,并能使金属制品表面光亮,具有超过原有的光泽度,且性能稳定、无毒,对环境无污染等。
抛光剂中的液体介质可以是水、有机溶剂。有机溶剂必须具有相当高的挥发性、较低的贝壳松脂丁醇值,并且要有良好的流平性和不能溶解腐蚀汽车表面涂层的性质,有机溶剂介质主要有脂肪烃、异链烷烃、甲基-乙基酮及混合物等。
早期的抛光剂大多添加研磨材料来除去金属表面风化的残余物、氧化物和泥土等。选择合适的抛光用研磨磨料很重要,磨料的材质、粒度、硬度、圆度和每一颗粒表面的结构形态都对制成的研磨剂的抛光效果有直接的影响。常用的研磨材料有铝土、硅藻土、浮石、漂白土、硅土、斑脱土、胶质黏土、氧化铁、氧化锡等。对局部漆面或内层涂料进行深度打磨和抛光时,要使用二氧化硅等具有较高硬度的磨料。
1.2.6 电镀与化学镀液
电镀液利用电化学反应将金属沉积到工件表面,镀液成分不含还原剂、稳定剂。化学镀利用化学反应将金属沉积到工件上,镀液含有金属盐、配位剂、还原剂、稳定剂等;化学镀无需额外电源,电镀需要外加电源。
1.2.6.1 化学镀液
化学镀又称非电镀,是在无电流通过(无外界动力)时利用合适的还原剂使溶液中的金属离子有选择地在催化剂活化的表面上还原析出金属镀层的一种化学处理方法。所以化学镀可以叙述为一种用以沉积金属的、可控制的、自催化的化学还原过程,还原剂经氧化反应失去电子,提供给金属离子还原所需的电子,还原作用仅发生在一个催化表面上。因为化学镀的阴极反应常包括脱氢步骤,所需反应活化能高,但在具有催化活性的表面上,脱氢步骤所需活化能显著降低。化学镀的溶液组成及其相应的工作条件也必须是使反应只限制在具有催化作用的零件表面上进行,而在溶液本体内,反应却不应自发地产生,以免溶液自然分解。
在化学镀中,溶液内的金属离子依靠得到所需的电子而还原成相应的金属。化学镀溶液的成分包括金属盐、还原剂、配位剂、缓冲剂、pH调节剂、稳定剂、加速剂、润湿剂和光亮剂等。化学镀液中采用的还原剂有次磷酸盐、甲醛、肼、硼氢化物、氨基硼烷和它们的某些衍生物等。化学镀与电镀的区别在于不需要外加直流电源,无外电流通过,故又称为无电解镀(electroless plating)或“自催化镀”(autocatalytic plating)。与电镀相比,化学镀具有镀层厚度均匀,针孔少,不需要直流电源设备,能在任何外形复杂的镀件上获得均匀的镀层,可在金属、半导体等各种不同基材上镀覆等特点。
化学镀不能与电化学的置换沉积相混淆。后者伴随着基体金属的溶解;同时,也不能与均相的化学还原过程(如浸银)相混淆,后者的沉积过程会毫无区别地发生在与溶液接触的所有物体上。随着工业的发展和科技进步,化学镀已成为一种具有很大发展前途的工艺技术,同其他镀覆方法比较,化学镀具有如下特点:
①可以在由金属、半导体和非导体等各种材料制成的零件上镀覆金属;
②无论零件的几何形状如何复杂,凡能接触到溶液的地方都能获得厚度均匀的镀层,化学镀溶液的分散能力优异,不受零件外形复杂程度的限制,无明显的边缘效应,因此特别适合于复杂零件、管件内壁、盲孔件的镀覆;
③对于自催化的化学镀来说,可以获得较大厚度的镀层,甚至可以电铸;
④工艺设备简单,无需电源、输电系统及辅助电极,操作简便;
⑤镀层致密,孔隙少;
⑥化学镀必须在自催化活性的表面施镀,其结合力优于电镀层;
⑦镀层往往具有特殊的化学、力学或磁性能。
1.2.6.2 电镀液
电镀就是利用电解原理在某些金属表面镀上一薄层其他金属或合金的过程,是利用电解作用使金属或其他材料制件的表面附着一层金属膜的工艺。电镀是电化学过程,是在含有欲镀金属离子的溶液中,以被镀材料或制品为阴极,通过电解作用,在基体表面上获得镀层的方法。在电解过程中,电极和电解液之间的界面上发生电化学反应,阳极(释放电子)发生氧化反应,阴极(吸收电子)发生还原反应。为了使得所要求的反应沿着相同的方向进行,必须使用直流电。因此,电镀的三个必要条件是:电源、镀槽(电镀液)和电极。
电镀镀层有单金属的、合金的和复合的(如镍镀层中弥散着碳化硅或金刚石等)。其功能有耐蚀性镀层、装饰性镀层和功能性镀层。耐蚀用镀层常用Zn、Cd、Cr、Sn、Ni、Cu、Au、Pb、Pt等金属以及Zn-Ni、Ni-Sn、Ni-Cr、Cu-Zn等合金。根据镀层与基体金属或中间层金属的电极电位不同,可以将镀层分为阳极性镀层和阴极性镀层。阳极性镀层在镀层有破损时,镀层对基体或中间层金属能起到电化学保护作用;阴极性镀层在镀层有破损时,镀层会加剧基体中间层金属暴露部分的腐蚀。所以阴极性镀层更应注意其致密性和有无破损。
电镀时,镀层金属或其他不溶性材料作阳极,待镀的工件作阴极,镀层金属的阳离子在待镀工件表面被还原形成镀层。为排除其他阳离子的干扰,且使镀层均匀、牢固,需用含镀层金属阳离子的溶液作电镀液,以保持镀层金属阳离子的浓度不变。电镀的目的是在基材上镀上金属镀层,改变基材表面性质或尺寸。可以为材料或零件覆盖一层比较均匀的、具有良好结合力的镀层,以改变其表面特性和外观,达到材料保护或装饰的目的。因此,电镀能增强金属的抗腐蚀性(镀层金属多采用耐腐蚀的金属),增加硬度,防止磨耗及提高耐磨性,提高导电性、光滑性、耐热性、反光性以及恢复零件尺寸,修补零件表面缺陷等。电镀已作为材料表面处理技术中的重要方法,在各个工业部门得到广泛的应用。