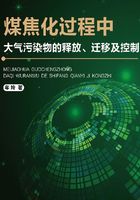
1.6 焦炉烟尘控制的发展历程、现状和技术
1.6.1 我国焦炉烟尘控制的发展历程
20世纪70年代以来,随着一代炉龄结束,国内焦炉相继进入大修期。30多年来,国内焦炉通过改造大修,扩容大修同时消化吸收国外先进技术,提高了焦炉生产的机械化与自动化程度及整体技术装备水平。到2007年年底,国内自行设计建成投产的6m大容积焦炉已达40多座,规划和在建的7.63m超大容积焦炉已近10座。这期间,随着技术进步和环保力度加强,相继增加了必要的环保措施,焦炉环境污染状况明显改善,突出表现在对炼焦过程的烟尘控制方面,但是对机械操作过程中的烟尘控制还难以满足环保要求,这是因为机械操作过程中的烟尘主要产生于炉门、装煤、推焦与熄焦作业等环节,而且它们会在长距离上频繁移动,增加了治理的难度。
目前按焦炉污染物的排放水平,把焦炉污染控制大致分为三类[1]:第一类装备先进,配备完善的装煤和拦焦除尘设施,其焦炉污染物控制基本可达到国内外先进水平,污染物排放约为1.5kg/t焦以下;第二类是用国内设备,装备6m或4.3m焦炉,没有配备装煤和拦焦除尘设施,或只有拦焦除尘设施,但管理严格,生产中炉门、上升管、装煤孔盖基本不冒烟,装煤时坚持用高压氨水喷射,这类焦炉污染物排放总量在3.5~5kg/t焦之间;第三类不仅没有配备装煤和拦焦除尘设施,而且管理不严,生产过程中炉门、上升管、装煤孔冒烟,装煤不能坚持用高压氨水喷射,这类焦炉属于污染物基本无控制的状况,其污染物排放总量大大超过3.5kg/t焦。
2004年国家发改委发布的《焦化行业准入条件》的“环保工艺与设施”中明确规定:新建或改造焦炉要同步配套建设粉碎、装煤、推焦、筛运焦除尘装置。严格执行环保设施“三同时”规定,并要在主体设备投产后6个月内达到设计规定标准,连续运行。
1.6.2 焦炉烟尘控制技术
1.6.2.1 炼焦期间散烟的控制
炼焦期间的散烟及其控制主要在于焦炉炉门、焦炉顶上升管和装煤孔以及相应的焦炉运行管理方面。
(1)炉顶烟尘的控制
炉顶烟尘来源于装煤孔盖、上升管盖、上升管与炉顶连接处等。国内已采取的主要控制措施如下。
1)装煤孔盖泥封 采用人工或装煤车机械浇泥,把泥浆浇灌在孔盖周边加以密封。可以采用泥料SiO2>80%的耐火粉,细度0.074mm以下,体积密度<1.3t/m3,加水搅拌成密度为1.1~1.2t/m3浆液,黏度大于40cP(1cP=10-3Pa·s,下同),pH值小于8,要求悬浮性好,收缩性好,干燥后容易脱落。
2)上升管盖密封 国内20世纪80年代以来,普遍采用水封式上升管盖,水封高度大于上升管内煤气压力,保证荒煤气不外逸。
3)上升管与炉顶连接处封堵 采用耐火材料、泥浆、石棉绳和耐火粉料与精矿粉混合泥浆封堵,承插口处采用氨水水封。
目前国外对装煤孔盖除采用泥封外,对装煤孔盖、孔座的结构设计做了改进,把盖和座的密封沿圆周方向加工成球面,由于球面密封有“万向密合”的优点,即使盖子有点倾斜也能与座贴合良好,保证密封。
(2)炉门烟尘的控制
炉门刀边与炉框镜面接触不严密将使炉内烟气泄露。20世纪50年代,采用小压架顶丝压角钢或丁字钢刀边的刀封炉门结构,但炉门容易产生热变形发生漏缝。20世纪60年代,采用敲打刀边,但不能消除炉门因热变形引起的冒烟现象。20世纪80年代,采用空冷式炉门,改善了炉门铁槽与炉门框因受热而引起的变形,同时采用带弹性腹板的不锈钢刀边,用小弹簧施加弹性力来调节刀边的密封性,基本上消灭了炉门冒烟现象。国内有些厂还采用了气封炉门技术,进一步消灭了炉门冒烟情况。
(3)设置焦炉顶面自动吸尘清扫车
这种清扫装置可以设在装煤车上,也可以独立配置。它可以吸除炉面上的煤粉,防止其扬尘或在炉面上燃烧。
(4)设集气管放散管点火装置
点火装置用于焦炉事故或停电时把集气管内放散出来的荒煤气自动点燃、烧尽,以免排放到大气中,污染环境。
1.6.2.2 焦炉装煤烟尘的控制技术
装煤车把煤通过装煤孔装入赤热的炭化室,此时煤中水分蒸发和挥发分的迅速产生造成炭化室内压力突然上升,形成大量烟尘从炭化室逸出。目前焦化厂普遍采用顺序装煤,焦炉设置双集气管,以及在上升管桥管处采用1.8~2.5MPa的高压氨水(或0.7~0.9MPa蒸汽)喷射,使炭化室形成负压(如装煤孔处压力为-5Pa),以实现无烟装煤。但实际效果并不十分理想,由于国内大多数装煤车装煤伸缩筒、平煤杆套以及装煤孔座气密性差,喷射吸力波动较大,加上重力装煤产生的大量烟尘,不能完全借助高压氨水喷射及时导出,烟尘仍有一部分从装煤孔、小炉门等处逸出进入大气,造成环境污染。
从20世纪70年代起,随着环保要求日益严格,焦炉烟尘污染与治理技术引起世界发达国家的高度重视,并相继在焦炉上试用成功,取得明显成效。目前已采取多种治理技术和措施,分别控制和降低装煤过程中的烟尘排放、炉门和炉顶的冒烟、冒火。国内也先后研究开发和实施了各种装煤烟尘的控制方法,主要可分为密封式可调装煤除尘和抽吸式装煤除尘设施,抽吸式装煤又可以分为车载式和地面站式。现有具体控制措施和治理技术详见图1-7。
1.6.2.3 焦炉拦焦操作的烟尘控制技术
推焦过程是在1~3min内推出炭化室的红焦,红焦质量多达10~50t。红焦表面积大、温度高,与大气接触后收缩产生裂缝,并在大气中氧化燃烧,引起周围空气强烈对流,产生大量烟尘。推焦排放的污染物主要是焦粉、二氧化碳、氧化物、硫化物等。如果焦化不均匀或焦化时间不足,有生焦产生,此时推焦过程产生的烟气呈黑色,烟气中含有较多的焦油物质,粉尘发生量约0.4~3.7kg/t焦。
与焦炉装煤烟尘治理相比,拦焦烟尘治理技术问世较早,成熟也早。由于环保工艺与设施要求焦炉拦焦和装煤烟尘需同步治理,随着技术进步和对焦炉治理经验的积累,拦焦除尘技术不断发展。目前拦焦除尘大致可以分为车载式和地面除尘站以及与装煤除尘合一等方法,具体拦焦烟尘控制措施和治理技术见图1-8。

图1-8 拦焦烟尘控制措施和理论技术
1.6.3 烟气中挥发性有机物控制技术
烟气中挥发性有机化合物(VOCs)的排放控制一般可通过使用清洁生产工艺流程和改进设备来达到。对于已经排放或泄露的VOCs,国内外目前采用的处理技术主要包括回收和降解[11]。
1.6.3.1 回收技术
一般对于浓度高于5000mg/m3的VOCs,宜采用回收技术加以回收利用。该技术回收率高、能耗低,可反复使用,基本不会造成二次污染,且易于推广,具有很好的环境效益和经济效益。常用的回收技术主要有炭吸附、冷凝及膜分离等。
(1)炭吸附技术
该方法利用吸附剂所具有的较大的比表面积,能够实现对烟气中的VOCs的吸附。当废气经过吸附床时,VOCs能被吸附在活性炭的微孔内,从而使气体得到净化。当吸附达到饱和后再用水蒸气洗脱,再生后的活性炭可循环使用。
吸附时通常采用两个吸附器,一个吸附,另外一个洗脱再生,以保证能够连续对烟气进行净化。脱附采用水蒸气作为脱附剂,水蒸气将吸附在炭表面的VOCs脱附并带出吸附器,最后通过冷凝和蒸馏,将VOCs提纯回收。
吸附效果主要取决于吸附剂的性质、VOCs的种类、浓度和吸附系统的操作温度、湿度和压力等因素。常用的吸附剂有颗粒活性炭、活性炭纤维、沸石、分子筛、多孔黏土矿石、活性氧化铝、硅胶和高聚物吸附树脂等。该方法的不足之处在于吸附剂的容量小,所需的吸附剂量较大,从而导致气流阻力大,设备投资高,占地面积大,吸附后的吸附剂需要定期再生处理和更换。
(2)冷凝技术
该法是通过将操作温度控制在VOCs的沸点以下而将VOCs冷凝下来,从而达到回收VOCs的目的,主要适用于VOCs含量高、气体量较小的有机废气回收处理。使用的冷却介质包括冷水、冷冻盐水和液氨。该法对入口VOCs要求严格;冷却温度低于0℃时,大部分气流所含水蒸气在冷凝器中形成冰,冷凝器需定期除霜或气流预先脱水;若冷却温度低于-40℃时,则需要二级冷却,从而造成能源费的增加。该法的回收率与VOCs的沸点有关,沸点高时回收率高,沸点低时回收率偏低。
(3)膜分离技术
该法是采用对有机物具有选择性渗透的高分子膜,在一定压力下使VOCs渗透而达到分离的目的。当VOCs气体进入膜分离系统后,膜选择性地让VOCs气体通过而被富集。脱除了VOCs的气体留在未渗透侧,可以达标排放;富集了VOCs的气体可以通到冷凝回收系统进行有机溶剂的回收。膜分离法主要适用于处理中高浓度的废气,具有可回收有用成分的优点,但有压力损失,同时对膜依赖性强。
对于气体膜分离技术,主要是利用有机废气与空气透过膜的能力不同,而使二者分开。该过程首先进行压缩和冷凝有机废气,再进行膜蒸汽分离,具体流程为:a.含VOCs的有机废气进入压缩机,压缩后计入冷凝器中冷凝,冷凝下来的液态VOCs即可回收;b.物流中未冷凝部分通过分离,形成两部分物流,其中渗透物流含有VOCs,重新返回压缩机进口;c.未透过的去除了VOCs的物流(净化后气体)从系统排出。
1.6.3.2 降解技术
降解技术对于处理中低浓度(<1000mg/m3)的VOCs是较好的治理办法。该法根据VOCs的物化性质,将其转变为无毒无污染的物质,具有去除效率高,产物大多为CO2和H2O,无二次污染,无需进行二次处理,设备体积较小,反应操作易于控制,经济可行等特点。
(1)燃烧技术
燃烧法分为直接燃烧、热力燃烧和催化燃烧。
1)直接燃烧 是把可燃的VOCs废气当作燃料来燃烧的一种方法,适合处理高浓度VOCs废气或者用于净化有害组分燃烧时热值较高的废气。如果可燃组分的浓度高于燃烧上限,可以混入空气后燃烧;如果可燃组分的浓度低于燃烧下限,则可以加入一定数量的辅助燃料维持燃烧。该法不仅会造成浪费还会产生大量大气污染物进入大气,近年来已较少使用。
2)热力燃烧 该法是当废气中可燃物含量较低时,使其作为助燃气或燃烧对象,依靠辅助燃料产生的热力将废气温度提高,从而在燃烧室中使废气氧化去除。该过程一般分为三步:燃烧辅助燃料提供预热能量;高温燃气与废气混合以达到反应温度;废气在反应温度下氧化去除。热力焚烧系统主要由热焚烧炉、辅助燃料供应设施、热交换器、涤气器构成,其工艺过程为:加入辅助燃料,使含VOCs的物料进行焚烧,转化成CO2和H2O。燃烧室温度通常为650~870℃,停留时间0.5~1s,VOCs的去除效率可达95%以上。该法VOCs去除率高、一次投资低、不产生废液和固体废物、维修少。
3)催化燃烧 其是近几年产生的一门新型技术,是在催化床层作用下加快有机物化学反应。由于催化剂的存在使得有机物在热破坏时比直接燃烧法需要更少的保留时间和更低的温度。通常用于有机废气净化的催化剂主要是金属和金属盐,其中金属包括贵金属和非贵金属。金属催化剂以Pt、Pd为主,技术成熟且催化活性高,但价格比较昂贵且在处理卤素有机物,含N、S、P等元素时,有机物易发生氧化而会造成催化剂失活;非金属氧化剂有过渡族元素钴、稀土等。催化燃烧法的主要优点:起燃温度低,能耗低;处理效率高,无二次污染;对有机物浓度和组分处理范围宽,能耗低,并能回收输出的部分热能,所需设备体积小;造价低。催化燃烧法的缺点是:当有机废气浓度太低时需要大量补充额外的热量才能维持催化反应的进行。
(2)光催化降解技术
光催化法是在光和光催化剂作用下将有机物氧化成CO2和H2O。该方法处理有机污染物操作简单、使用范围广。存在的缺点是由于光催化剂需要附着在填料、器壁或其他载体上,并且需要紫外光进行照射,因此对反应器的结构要求较为严格,容易存在光照不充分的情况。另外,在低浓度条件下,有机污染物的光催化降解速度较慢,并且光催化氧化分解污染物要经过许多中间步骤,生成有害中间产物,某些副产物会附着在催化剂表面,使催化剂表面的活性中心减少,降低催化效率。
光催化降解工艺主要设备包括以下几种。
1)布袋除尘器 为防止废气中的颗粒物对光源和光催化剂的覆盖黏结,必须对废气进行预处理,以去除其中的颗粒物,减少光催化氧化单元的处理负荷。
2)风机 除尘器负压运行,光催化单元正压运行。
3)稳流室 稳定进气的浓度与风速提高后设备的处理效率。
4)光催化氧化装置 光催化氧化室是进行净化处理的主体单元,催化剂纳米TiO2粉体负载在纤维材料上。
5)吸附室 用于进一步吸附分解有机废气,提高净化效率。
(3)生物降解技术
生物降解技术主要是利用微生物的生命活动将废气中有害物质转变成简单的无害物如CO2和H2O及细胞组成物等。一般根据微生物在有机废气处理过程中存在的形式可分为生物洗涤法(悬浮态)和生物过滤法(固着态)。生物洗涤法又称为生物吸收法,指微生物及其营养物配料存在于液体中,气体中的有机物通过与悬浮液接触后转移到液体中而被微生物降解。生物过滤法是微生物附着生长在固体介质(填料)上,废气通过由介质构成的固定床层被吸附、吸收,最终被微生物降解,主要分为生物洗涤器和生物滤池两种形式。
1)生物洗涤器 生物洗涤器是悬浮于活性污泥的处理系统,通常由一个洗涤塔和一个再生池构成。在洗涤塔中,生物悬浮液自吸收室顶部喷淋而下,使废气中的污染物转移至液相,实现传质过程。吸收了废气中有机物的生物悬浮液,并流入再生反应池中,通入空气充氧后再生。在再生池中,被吸收的污染物通过微生物氧化作用被从液相中去除。常用的生物悬浮液是活性污泥悬浮液,但其处理后再生的时间较长。由于吸收和再生所需的时间不同,生物悬浮液的再生是在同一个反应器中进行还是在另外一个反应器中完成,取决于生物悬浮液的活性强度和再生能力。
2)生物滤池 生物滤池法是指具有一定湿度的有机废气进入生物滤池,通过50~100cm的生物活性填料层,污染物从气相转移到生物相,进而被微生物氧化分解的过程。分解过程由异养微生物在有氧和中性微碱条件下完成,一般有机物最终被分解为CO2。
生物滤池的填料层一般是具有吸附性的滤料,通常为土壤、堆肥、木屑、活性炭或几种滤料混合而成。滤料充当微生物的载体,一般应具有良好的透气性和适度的通水性和持水性,以及丰富的微生物群落。生物滤池有单滤床开放式、多滤床封闭式等。与开放式单滤床生物滤池相比,封闭式生物滤池对维护的要求低、占地少,受气候影响小且容易监控,但造价较高。