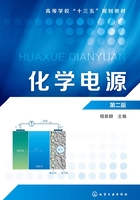
2.5 化学电源中的多孔电极
2.5.1 多孔电极的意义
化学电源大多采用粉末多孔电极。采用多孔电极的结构是化学电源发展过程中的一个重要革新,为研制高比能量和高比功率的电池提供了可行性和现实性。
多孔电极是将高比表面积的粉状活性物质与具有导电性的惰性固体微粒混合,然后通过压制、烧结、涂膏、粘接等方法制成。多孔电极具有较大的孔率,可以大大提高电极的真实表面积,减小工作时的真实电流密度,减小电化学极化;多孔电极可以改善扩散传质情况,减小浓差极化;采用粉状活性物质可以方便地改变物料组成、形貌、尺寸等,也可以方便地改变电极结构和制造工艺;电极反应在微孔内表面进行,减小了物质脱落和枝晶形成。采用多孔电极使得电池性能获得显著的改善,特别是对于锌电极等具有钝化倾向的电极,使用多孔电极可以避免或推迟钝化,因而具有更重要的意义。
按照电极反应的特点,多孔电极可分为两大类,即固-液两相多孔电极和固-液-气三相多孔电极。在两相多孔电极中,电极的内部孔隙中充满了电解液,电化学反应是在固-液两相的界面上进行的,例如像锌-银电池中的锌电极和银电极,铅酸蓄电池中的铅电极和二氧化铅电极等。而对于三相多孔电极,电极的孔隙中既有充满电解液的液孔,又有充满气体的气孔,在气-液界面上进行气体的溶解,而在固-液界面上进行电化学反应。例如金属-空气电池中的空气电极,燃料电池中的氢电极和氧电极都属于三相多孔电极。
在多孔电极中,电极反应是在三维空间结构内进行的,与电极表面距离不同处的极化差别必然存在。因此,存在着一系列的在平面电极上不存在的特殊问题,例如整个电极厚度内反应速率(电流密度)的分布、极化性质的改变等。就是说,在多孔电极内部存在着浓度梯度和由于欧姆内阻而引起的电势梯度,它们使多孔电极的内表面不能充分地被利用,因此使多孔电极的有效性受到限制。
2.5.2 两相多孔电极
在两相多孔电极内部,实际上是由充满电解液的大小不等的液孔和活性物质固相交织组成的,结构复杂。为了方便讨论,我们以一个圆柱形的小孔来讨论,以锌电极的阳极过程为例。
(1)没有浓差极化的情况(欧姆极化和电化学极化控制)图2-7是多孔锌电极的一个小孔及孔内电流的分布。当锌电极作为阳极工作时,电流方向由孔内流向孔外,而孔内各点的位置x是由孔口处向内计算,孔口处x=0,因此x与电流方向相反。假设孔内表面上有a、b两点,相距dx;c、d为表面溶液中相应的两点。

图2-7 两相多孔电极及孔内电流分布
由于金属锌的电导率很小,与电解液相比,金属的电阻可以忽略不计,因此可认为a、b两点是等电势的,但溶液中存在电阻,d、c之间的液相电阻为dR。在电流I流过时,d、c两点之间会产生欧姆电压降dφ=IdR。因此,若取a点的电极电势为φ(即a点相对于c点之间的电势差),则b点的电极电势应为φ-dφ。因为孔内溶液中电流由d点流向c点,所以d点的电势高于c点,也就是说b点的电极电势小于a点的电极电势(因为a、b两点是等电势的),其差值为dφ。
孔内在dx距离内的电阻为:
(2-27)
式中,σ为孔的截面积;κ为溶液的电导率。
所以
(2-28)
(2-29)
电流I是流过孔截面的电流,它随距离x而变化,即I=f(x);在孔口处,电流I为孔内表面各点流出的电流的总和,所以此处I值最大。越向孔内延伸,流过孔截面的电流I越小。所以,对于距离dx,流过孔截面的电流的变化可表示为:
(2-30)
式中,S为dx距离内孔壁的内表面;is为在dx距离内通过孔壁的电流密度。
因为x的方向与电流方向相反,增加距离dx,电流减小dI,所以式(2-30)中有一负号。将式(2-29)对x微分得:
(2-31)
将式(2-30)代入式(2-31)得:
(2-32)
如果以几何表面积是1cm2、厚度是1cm的单位体积的多孔电极为例来讨论,那么σ即为单位体积电极中孔体积所占的分数,即电极的孔率;而S则是单位体积电极的内表面积。
若把电极电势φ写成平衡电极电势φe和电极反应的过电势η之和的形式:
(2-33)
同时利用电化学动力学方程式,将电化学反应的速率和过电势联系起来:
(2-34)
式中,i0为交换电流密度;α、β为传递系数;F为法拉第常数;n为参加电极反应的电子数。
这样将式(2-34)代入式(2-32),同时联系式(2-33)得到:
(2-35)
在这里假设φe值与x无关。如果溶液中决定电极电势的组分在沿所研究的多孔电极的厚度方向有固定的浓度时,这个假设是正确的。
取边界条件为:
(2-36)
式中,ia为电极外表面的表观电流密度;L为孔深,对于有对称电流引线的电极,L等于电极厚度的一半。
利用边界条件,对式(2-34)一次积分,得到以下形式:
(2-37)
式中,η0、ηL分别表示在外表面(x=0)和多孔电极深处(x=L)的过电势值。
将式(2-37)改写为:
(2-38)
即
(2-39)
式中,ia,0、ic,0、ia,L、ic,L分别表示在外表面(x=0)和多孔电极深处(x=L)的氧化内电流与还原内电流。
方程式(2-39)左边表征多孔电极电流分布的均匀性。从方程式看出,极化电流密度越小,而电解液电导率、电极孔率、电极真实表面积越大,多孔电极中电流分布越均匀。提高温度,因为电导率κ数值增大,所以可以改善多孔电极的极化均匀性。
(2)有浓差极化的情况 有时电解液的电导率高,欧姆极化可以忽略,如果电极的电化学极化又小,则当有电流流过时,沿电极孔的纵深方向存在着电解液的浓度梯度。物质传递对电极极化的均匀性有显著的影响。在孔内物质传递的唯一方式是扩散。
为了简化,只讨论一种离子的浓度变化对电极极化均匀性的影响,即对多孔电极内电流分布的影响。还是以碱性介质中的锌电极为例:
Zn+4OH-+2e-
讨论锌阳极溶解时OH-的浓度变化。
由扩散定律,有:
(2-40)
式中,m为扩散的物质质量;S为扩散截面积;Δt为时间间隔;D为扩散系数;为浓度梯度。
通过法拉第定律,将上面的扩散物质量转变为电流密度:
(2-41)
在稳定扩散条件下,浓度梯度存在线性关系,式(2-41)可表示为:
(2-42)
式中,c0为孔外溶液中OH-的浓度;cs为孔内工作电极表面附近OH-的浓度;L为孔内表面上工作点与孔口表面处的距离,当工作点处于孔的底部时,L即为孔的长度。
当孔内工作表面附近OH-的浓度cs=0时,即达到极限扩散电流时,有:
(2-43)
所以
(2-44)
结合式(2-44)与式(2-42)可得:
(2-45)
故
(2-46)
当电化学极化可以忽略时,可认为电极处于热力学平衡状态,因此电极电势可以用能斯特方程表示:
(2-47)
将式(2-46)代入式(2-47),得:
(2-48)
在多孔电极中,如果只考虑浓差极化,而假设孔内溶液中的欧姆电阻为零,那么孔内表面上各点的电极电势应该相等,电极是一个等电势体。由式(2-48)可以看出,如果要孔内表面上各点的电极电势相等,则必须要求i/id是一个常数。
根据极限电流表达式(2-43),虽然n、F、c0是常数,但对于孔内表面上各点而言,D与L的值是不同的。物质在孔内扩散受多孔电极的结构影响(如孔率、孔径和孔的曲折系数等),一般要用有效扩散系数D有效来代替整体溶液中的扩散系数D。
(2-49)
显然,越往孔的深处,L越大,D有效越小,即越往孔的深处,id越小。为满足i/id是个常数,孔内表面上各点的工作电流密度i必定不等,越往孔的深处,工作电流密度i越小,也就是说由于物质传递的影响,同样使孔内表面上电流分布不均匀。
如果多孔电极的孔率和孔径比较大时,可以改善孔内外物质的传递,使孔内电流分布比较均匀,电极内表面得到较好的利用。
如果工作电流密度较大时,孔内的浓度梯度也变大,物质传递的影响更严重,孔内表面上电流分布会更不均匀。
2.5.3 三相多孔电极
以气体为活性物质的电极与以固体或液体为活性物质的电极不同,它在反应时是在气、液、固三相的界面处发生,如果缺任何一相都不能实现电化学过程。气体反应的消耗以及产物的疏散都需要扩散来实现,所以,扩散是气体电极的重要问题。
对于燃料电池中的氧电极和氢电极,金属-空气电池中的空气电极,它们的活性物质都是气体,而气体在水溶液中的溶解度在常温常压下是很小的。比如,对于完全浸没在电解液中的氧电极,氧的溶解度是10-4mol/L,而且氧在溶液中的扩散速度也不大;在电解液不搅拌的条件下,扩散层厚度δ=10-4m,扩散系数D=10-9m2/s,其极限电流密度id=0.1mA/cm2,如此小的极限电流密度在电池中是没有实际意义的。所以,制备高效的气体电极,成为化学电源研究的一个重要课题。
(1)气体扩散电极的特点 气体扩散电极的理论基础是“薄液膜理论”。威尔曾对4mol/L H2SO4中的铂黑氢电极进行了下列试验。将长为1.2cm、外表面积2.4cm2圆筒状铂黑氢电极浸没在氢饱和的H2SO4溶液中,当氢电极的电极电势维持在0.4V时,流过全浸入的铂黑电极的阳极电流仅0.1mA。但是当小心地将铂黑电极从溶液中慢慢提升时,开始流过电极的电流几乎不变,当电极提升到3mm左右,电极上流过的电流迅速增大,继续将电极向外提升,电极上流过的电流又开始慢慢下降。如图2-8所示。

图2-8 铂电极从4mol/L H2SO4溶液中提出时对氢的氧化电流的影响
实验表明在半浸没电极上只有高出液面2~3mm的那一段能最有效地进行气体电极反应。用显微镜观察电极表面,这一段电极上存在着薄的液膜。
上述实验现象可以用图2-9来解释。氢可以通过几种不同的途径在半浸没电极表面上氧化,其中每一种途径都包括氢迁移到电极表面与反应产物H+迁移到溶液深处去这样的液相传质过程。

图2-9 电极上的薄液膜
如果有一项液相传质过程的扩散途径太长,如b途径中的H2扩散与c途径中的H+的扩散,就不可能获得大的电流密度。按d途径反应时吸附氢还要通过固体表面上的扩散才能到达薄液膜上端的电极/溶液界面,所以更困难。但是,如果按a途径进行反应,则氢与H+的液相迁移途径都较短,因此这一部分电极表面就成为最有效的反应区。电极的工作电流因而迅速上升。
由上述结果看出,制备高效气体电极时必须满足的条件是电极中有大量气体容易到达而又与整体溶液较好的连通的薄液膜。这种电极必然是较薄的三相多孔电极,其中既有足够的气孔使反应气体容易传递到电极内部各处,又有大量覆盖在电极表面上的薄液膜;这些薄液膜还必须通过液孔与电极外侧的溶液通畅地连通,以利于液相反应粒子和反应产物的迁移。因此,理想的气体电极是在电极表面具有大量高效的反应区域——薄液膜层,这时扩散层厚度大大降低。根据极限扩散电流:
极限电流密度比全浸没式电极大为增加,这是气体扩散电极的基本特点。为了达到此目的,常用的气体扩散电极主要采用了3种不同形式的结构。
①双层电极 电极由金属粉末和适当的发孔性填料分层压制及烧结制成。靠近气体的一侧是孔径较大的粗孔层(30~60μm),靠近电解液的一侧是孔径较小的细孔层(10~20μm),反应气体有一定的压力以便与细孔中的毛细力相平衡,若将气体压力调节到适当数值,使细孔中充满电解液,粗孔中充满气体,在粗细孔交界处就会建立起弯月面薄液膜层,这就是燃料电池中的培根型双层结构气体扩散电极,如图2-10所示。通常双层电极中的粗孔半径为几十微米,而细孔半径不超过2~3μm,气体的工作压力为0.05~0.3MPa。

图2-10 双层电极示意
②微孔隔膜电极 电池由两片用催化剂微粒制成的电极与微孔隔膜层结合而成。使隔膜的孔径比催化层的孔径更小,于是加入的电解液首先被隔膜吸收,然后湿润催化层。控制加入的电解液的量,使电极处于部分湿润状态,其中既有大面积的薄液膜,又有一定的气孔。一般来说,在半径大的毛细孔中充满气体,而在半径小的细孔和微孔中充满液体,气、液孔的分布,主要取决于气体压力与孔内毛细力之差。这种结构控制较困难,电解液过多、过少或两极气室压力不平衡,均会造成电极“淹死”或“干涸”。这种电池结构如图2-11所示。

图2-11 微孔隔膜电极示意
③憎水电极 通常用催化剂粉末与憎水性材料混合后碾压、喷涂及经过适当的热处理后制成。常用的憎水材料是聚乙烯、聚四氟乙烯等。憎水电极示意图如图2-12所示。由于电极中含有憎水成分,即使气室中不加压力,电极内部也有一部分不被溶液充满的气孔,憎水组分及其周围气孔称为干区。另一方面,由于催化剂表面是亲水的,在大部分催化剂团粒的外表面上均形成了可用于进行气体电极反应的电解液薄膜,电解液及其润湿的催化剂团粒称为湿区。这两种区域相互犬牙交错,形成连续网络。实际憎水气体扩散电极在面向气室的表面上还覆盖一层憎水透气膜,使空气能够源源不断输入电极内部,而电解液却不能透过电极进入气室。

图2-12 憎水电极示意
(2)气体扩散电极中的物质传递 在气体扩散电极中,除了与两相多孔电极一样,具有液相物质传递外,还有气相中的物质传递。在此着重讨论气相物质传递的问题。
处理多孔体内某一相(i)中的传质过程时,一方面要考虑到该项的比体积(Vi),也就是单位体积多孔体中该相所占有的体积即孔率;另一方面还要考虑该相的曲折系数(βi)。所谓某一相的曲折系数,是指多孔体中通过该相传质时实际传质途径的平均长度与多孔层厚度之比。如图2-13中,直通孔的β=1,而曲折孔的β=3。如果多孔体结构是各向异性的,则曲折系数与传质方向有关。

图2-13 多孔体中气体扩散的不同途径
从图2-13还能看到,曲折孔的比体积比直通孔大β倍,而同样条件下的传质速度只有直通孔的1/β。因此,多孔体内某一相(i)中的传质速度应与成正比。考虑到多孔电极中气体扩散的特点,必须对扩散系数D进行修正。如果孔的结构是与气体扩散方向相同的直通孔,则气体扩散透过多孔体时的“有效扩散系数”应为:
(2-50)
如果孔的结构不是直通孔而是曲折孔,则气体的“有效扩散系数”应为:
(2-51)
式中,D气为在整体气相中的扩散系数;V为单位体积多孔体中气相所占的体积,即气孔率。
D有效的值可以从实验求得,也可通过V、D气、β气等参数计算。
从浓差极化方程式
(2-52)
可以看到,在相同的过电势下,极限扩散电流密度id越大,则相应的工作电流密度也越大,即电极性能越优越。因此,像其他类型电极一样,极限扩散电流密度对于气体扩散电极是一个重要的电化学参数。对于气体扩散电极,可以引用极限电流密度公式来估计气相物质传递在整个极化中所占的比例。
实际气体扩散电极的情况很复杂,还应考虑气相中的各种组分在物质传递中的影响。假如气相中含有两种组分,其中组分1为参加电极反应的活性组分(如空气中的氧),组分2为不能参加电极反应的惰性组分(如空气中的氮气和惰性气体)。电极反应的结果促使组分1向孔内反应界面流动的原因,除了扩散作用以外,还有气体的整体流动。因此组分1经过透气层的流量可写成:
(2-53)
式中,D12为组分1在组分2中的扩散系数;N为气体总浓度(N=c1+c2);c1和c2分别为组分1和组分2的浓度;J总为整体气体的流量。
式(2-53)右方第一项表示浓度梯度引起的扩散流量,第二项表示由于气体整体流动而引起的组分1的流量。若气孔内压差可以忽略,则N为常数。当气孔内物质传递达到稳态,即气相中只有组分1流动时,J2=0,J总=J1,故式(2-53)可写成:
(2-54)
设透气层厚度为δ,取该层面向气室的表面为x=0,即反应区在x≥δ处,而在0<x<δ的范围内,J1为定值,因此式(2-54)可积分如下:
(2-55)
得到:
(2-56)
式中,为x=δ处组分1的浓度。以
代入,就得到相应于透气层极限气相传质速度的极限电流密度为:
(2-57)
令
(2-58)
则
(2-59)
与原式相比较,式(2-59)多了一项校正项f。
用式(2-59)分别计算采用空气和99%的氧气时,氧阴极还原的极限电流密度。
①反应气体为空气时,氧含量约20%,在1atm、25℃时,空气的浓度为4×10-5mol/mL,,
,故f=1.12;若聚四氟乙烯透气膜厚0.02cm,该膜经碾压制成,孔的曲折系数较大,取β气=4,气孔率V气=0.35,氧在氮中的扩散系数D12=0.2cm2/s,则由式(2-50)得到D12的有效值约为4×10-3cm2/s。又n=4,c1=N×0.2=8×10-6mol/cm3,则由式(2-58)得极限电流密度为:
②当采用99%的氧时,=N×0.99=3.96×10-5mol/mL,校正系数f=4.6,则氧电极的极限电流密度为;
从上面计算可见,多孔气体电极中气相传质速度往往是比较大的。只要透气层不太厚,气孔率不太小及反应气体浓度不太低,在一般工作电流密度下不应出现严重的气相浓度极化。通过以上讨论可以看到,当反应气体组成一定时,为提高极限电流密度、降低浓差极化,应该从改进电极的结构着手,如减薄透气层厚度、加大孔率、减小孔的曲折系数等。其中特别是孔的结构很值得注意,因为有效扩散系数与曲折系数的平方成反比。当然,电极的结构还应该结合其他方面的要求综合考虑,如储存性能、寿命等。在气体扩散电极中,究竟是气相还是液相中的物质传递起控制作用,要根据它们的极限电流密度的大小来确定。
(3)气体扩散电极内的电流分布 采用气体扩散电极的目的在于提高电极的工作电流,降低极化;但是,如同两相多孔电极一样,气体扩散电极的反应界面同样不能充分利用。由于气体扩散电极中的电极过程涉及气、液、固三相,它的极化特性和有关因素的影响等动力学问题常常非常复杂,数学处理也比较困难,有些问题至今还不能清楚、简明地加以描述。下面仅在简化了的特定条件下,定性地讨论气体扩散电极在各种极化控制下的电流分布和改进气体扩散电极的可能性。
①电化学极化-欧姆极化控制 这相当于小电流密度下工作的情况(如通讯用的锌-空气电池),假设多孔电极中气相和液相极限传质速度很大,因而可以忽略气、液相中反应粒子的浓差极化,也就是说全部反应层中各相具有均匀的组成;并且设反应层的全部厚度中各项的比体积均为定值。在满足这些假设时,电极的极化主要由界面上的电化学反应和固、液相电阻所引起。这时电极过程受电化学极化和欧姆极化控制。
在这种情况下,气体扩散电极和两相多孔电极的情况非常相似。由于孔内电解液中的欧姆电压降,使孔壁表面各点相对于溶液的电极电势不相等,如图2-14所示,孔壁附近溶液中A'电势比C'为正,假设忽略固相电阻,则孔壁上A点相对于溶液的电极电势要比C点为负,因为讨论的氧电极为阴极过程,所以流过A点电极表面的电流要大于流过C点的电流,即在毛细孔内,电流比较集中于靠近电解液的一端;越往孔的深处,电流分布越小,甚至趋于零。如图2-14(b)所示。当工作电流密度越大时,这种电流分布的不均匀性就越为严重。为了降低欧姆极化,除合理选择电解液外,常从改变催化层的结构着手(如增大催化层的孔率和孔径、减小毛细孔的弯曲程度等);当为了降低电化学极化而采用高效催化剂时,电极表面电流分布更不均匀,所以气体扩散电极的催化层常常做得很薄,因为电化学反应主要集中在催化层面向电解液一侧很薄的区域内,厚的催化层对电极性能的改善并没有贡献。

图2-14 电化学极化-欧姆极化控制时气体扩散电极孔内电流分布
②扩散控制 当电极在高电流密度下工作时,电极表面活性物质消耗的速度很快,气相和液相中的物质传递起控制作用,此时称电极为扩散控制。
为简化起见,假设电极的电化学极化很小,与浓差极化相比,可以忽略,同时假设电解液的电导率很高,多孔体内不发生欧姆电压降(这在实际情况下当然是不可能的,只是为使问题简化);对于氧的还原反应,物质传递包括毛细孔中氧气向电解液弯月面的扩散,溶液在电解液中的氧向电极反应表面的扩散以及生成物OH-从液膜中向孔外整体溶液中的扩散等;假设溶解在电解液中的O2向电极反应表面的扩散起控制作用,则根据简化条件下的扩散电流方程式,有:
(2-60)
可知,溶液中氧的初始浓度c0、电极表面氧的浓度cδ以及液膜层中扩散层厚度δ都影响扩散电流的大小。溶液中氧的初始浓度c0为定值,当电解液中欧姆电压降为零时,电极表面上各点相对于溶液的电极电势均相等,即处于等电势。若电化学极化可以忽略,则由能斯特方程可知,电极表面各点反应物的浓度必定相等,即在稳定扩散条件下,cδ为一定值。因此,扩散电流的大小只取决于扩散层的厚度δ,如图2-15所示。

图2-15 扩散控制时气体扩散电极孔内电流分布
由于憎水剂的存在,使电极处于不完全润湿状态,在某些毛细孔的壁上,电解液形成了一个弯月面和弯月面以上的一部分很薄的液膜,氧从气相通过液膜向电极表面扩散的途径很短,也就是δ很小,所以扩散电流很大,越往电解液深处延伸,氧的扩散层越厚,扩散电流也就越小,最后降至零。即在电极处于扩散控制下,电流分布是集中在毛细孔面向气体的一面,而在毛细孔面向电解液的一面的孔壁上几乎没有氧的还原反应发生。
实际上气体扩散电极内欧姆电压降不可能为零,特别是在大电流密度下工作时,欧姆电压降更为严重。因此,这时实际上往往为扩散-欧姆控制。为了改善电极的性能,既要改善气体的扩散,又要能减小电极孔内电解液中的欧姆电压降。但这两方面往往是相矛盾的,如对于憎水气体扩散电极,增加电极中聚四氟乙烯含量,可以使气体的扩散阻力减小,但却使液孔数量下降,从而使液相电阻增高;相反,假如减小电极中聚四氟乙烯含量,则使气孔减小,液孔增加,结果液相电阻下降,但气体扩散阻力增大。所以此时应掌握主要的控制因素,重点解决。
从以上讨论可以看出,电化学极化-欧姆极化控制和扩散控制,两者的电流分布情况恰好相反,在电化学极化-欧姆极化控制时,电流多分布于靠近电解液的一侧,而扩散控制时,电流多分布于靠近气体的一侧。这是两种极端情况,因此,可以推论,实际电化学反应最强烈进行的地带必然在两者之间。
由于气体扩散电极内部结构十分复杂,而且对它研究的历史也比较短,因此对它的动力学规律认识得还不很充分,特别是因为在气体扩散电极内部,各种极化的控制程度在不断变化着,因此,要说清楚某种条件下,究竟属于哪一种或哪两种控制是很困难的。尽管目前提出了各种模型和理论分析,但是这些模型和理论与实际气体扩散电极的结合还需要做大量的工作。