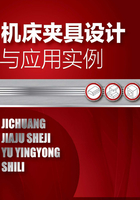
2.3 定位误差分析与计算实例
【实例2-3】 如图2-62所示的工件,本工序为铣通槽,要求保证尺寸、
和槽宽
,为使分析方便,仅讨论
如何保证的问题。

图2-62 工件在V形块中定位
分析:
工件用夹具定位加工时,是以调整法进行的。每当夹具和刀具的相对位置经过一次调整后,就不再变动用来加工一批工件。生产中操作者总是以夹具上定位元件的限位基面为基准来调节刀具的位置。而加工时工件以定位基面与限位基面相接触,这就相当于调节了工件与刀具的相对位置。本例中,要保证尺寸,考虑以K1面或以K2面定位都可限制加工尺寸B所在方向的移动自由度。但是这两种定位方法的定位精度是不同的。若以K2面定位[图2-63(a)],则操作者调整的刀具右侧切削刃S2与支承钉2之间的距离正是要保证的尺寸B,这个距离可认为是不变的,因而加工同批工件时的尺寸B也是稳定的。

图2-63 铣通槽时两种定位方案分析
1,2—导向支承钉
反之,若以K1面定位[图2-63(b)],则操作者调整时以支承钉1为基准,调整刀具左侧切削刃S1与支承钉1的距离,得尺寸B'。此时由于同批工件的毛坯中尺寸Ld是变化的,其变动范围为=Ldmax~Ldmin,这个变动范围就使间接得到的尺寸B也要发生变动,由图可知:δb=
,这就直接影响到尺寸B的精度,即每批工件中尺寸B就不一样了。试想,如果第一个试件尺寸Ld恰好处于极端情况,操作者在调整对刀以及测量时,加工得到的尺寸B就可能会超差;如果要求δb<
,则废品率将更高。
从以上分析可知:工件的定位基准选择不当会给加工尺寸增加一种误差——基准不重合误差。这种误差是因工序基准K2与定位基准K1不重合所致。这时定位基准与工序基准之间的联系尺寸Ld(也称定位尺寸)的公差,就会引起工序基准相对于定位基准在加工尺寸方向上发生变动,这个变动范围就是基准不重合误差ΔB。
显然,在图2-63(a)中,ΔB=0;而在图2-63b中,ΔB=。
2.3.1 造成定位误差的原因
造成定位误差的原因有两个:一是定位基准与工序基准不重合,由此产生基准不重合误差ΔB;二是定位基准与限位基准不重合,由此产生基准位移误差ΔY。
(1)基准不重合误差ΔB
图2-64是在工件上铣缺口,图2-64(a)为在工件上铣缺口的工序简图,加工尺寸为A和B。图2-64(b)为加工示意图,工件以底面和E面定位。C是确定夹具与刀具相互位置的对刀尺寸,在一批工件的加工过程中,C的大小是不变的。

图2-64 基准不重合误差ΔB分析
加工尺寸A的工序基准是F面,定位基准是E面,两者不重合。当一批工件逐个在夹具上定位时,受尺寸S±δS/2的影响。若某个工件前道工序尺寸为Smax,则本道工序尺寸为Amax;若某个工件前道工序尺寸为Smin,则本道工序尺寸为Amin。因此,工序基准F面相对定位基准有一个最大变动范围δS,它影响工序尺寸A的大小,造成A的尺寸误差。δS就是这批工件由于定位基准与工序基准不重合而产生的定位误差,简称基准不重合误差,用ΔB表示。
由此可见,基准不重合误差的大小应等于因定位基准与工序基准不重合而造成的加工尺寸的变动范围。由图2-64(b)可知:
ΔB=Amax-Amin=Smax-Smin=δS
式中 S——定位基准E面与工序基准F面间的距离尺寸,称为定位尺寸。
当工序基准的变动方向与加工尺寸的方向不一致,存在一夹角α时,基准不重合误差等于定位尺寸的公差在加工尺寸方向上的投影,即:
ΔB=δScosα
当工序基准的变动方向与加工尺寸的方向相同时,即α=0°,cosα=1,这时基准不重合误差等于定位尺寸的公差,即:
ΔB=δS
因此,基准不重合误差ΔB是一批工件逐个在夹具上定位时,定位基准与工序基准不重合而造成的加工误差,其大小为定位尺寸的公差δS在加工尺寸方向上的投影。
图2-64上加工尺寸B的工序基准与定位基准均为E面,基准重合,所以ΔB=0。
(2)基准位移误差ΔY
有些定位方式,即使是基准重合,也可能产生另一种定位误差。图2-65所示为圆盘钻孔工序图,图2-65(a)中尺寸D2由钻头保证,尺寸h±0.5δh由夹具保证。图2-65(b)为该工件在夹具中定位钻孔简图,定位基准和工序基准都是内孔中心线,二基准重合。钻套中心与定位销中心之距离h±0.5,按工序尺寸h±0.5δh而定,钻头经钻套引导钻削孔D2。

图2-65 圆盘钻孔工序图
由于工件的定位基准内孔D1和定位销直径d总有制造误差,为了使工件内孔易于套于定位销,二者间还留有最小间隙Xmin,因此,工件的定位基准和定位销中心就不可能完全重合,如图2-66所示。工件的定位基准中心相对定位销中心上、下、左、右任意方向变动,定位基准O的变动就造成工序尺寸的变动,其定位基准在工序尺寸方向上的最大变动范围称为定位基准位移误差,简称基准位移误差,用ΔY表示。

图2-66 基准位移误差
由图2-67可知,当工件孔的直径为最大(Dmax),定位销直径为最小(d0min)时,定位基准的位移量i为最大(imax=OO1),加工尺寸h也最大(hmax);当工件孔的直径为最小(Dmin),定位销直径为最大(d0max)时,定位基准的位移量i为最小(imin=OO2),加工尺寸h也最小(hmin)。

图2-67 基准位移误差分析
因此:
ΔY=hmax-hmin=imax-imin=δi
式中 i——定位基准的位移量;
δi——一批工件定位基准的变动范围。
因此,基准位移误差ΔY是一批工件逐个在夹具上定位时,定位基准相对于限位基准的最大变化范围δi在加工尺寸方向上的数值。
在上述分析的各例中,定位误差的产生只是单方面存在,即只有基准不重合误差ΔB,或只有基准位移误差ΔY。但在实际生产中,有的工件在夹具中定位时,可能这两种定位误差同时存在。因此,定位误差应由这两种误差组成。
2.3.2 定位误差计算方法
定位误差的计算方法有合成法、极限位置法和尺寸链分析计算法(微分法)。这里只介绍合成法。
由于定位基准与工序基准不重合以及定位基准与限位基准不重合是造成定位误差的原因,因此,定位误差应是基准不重合误差与基准位移误差的合成。计算时,可先算出ΔB和ΔY,然后将两者合成而得ΔD。
合成时,若工序基准不在定位基面上(工序基准与定位基面为两个独立的表面),即ΔB与ΔY无相关公共变量,则ΔD=ΔY+ΔB。
若工序基准在定位基面上,即ΔB与ΔY有相关的公共变量,则ΔD=ΔY±ΔB。
在定位基面尺寸变动方向一定(由大变小或由小变大)的条件下,ΔY(或定位基准)与ΔB(或工序基准)的变动方向相同时,取“+”号;变动方向相反时;取“-”号。
2.3.2.1 常见定位方式的定位误差分析与计算
(1)工件以平面定位
工件以平面定位时,若用精基准,定位基面与定位表面可以很好贴合,因平面度引起的基准位移误差很小,可不予考虑。若以毛坯面作粗基准,虽然基准位移误差较大,但主要是影响毛坯面到加工表面的尺寸关系,只要毛坯基准选择得好,也不会产生问题。所以,工件以平面定位可能产生的定位误差,主要是由于基准不重合引起的,实质上就是求基准不重合误差,即:
ΔD=ΔB=δS
【实例2-4】 如图2-64中,若S=40mm±0.14mm,A=20mm±0.15mm和B=25mm±0.15mm,采用图2-64(b)的定位方案,试分析和计算其定位误差,并判断此方案是否可行。
解:对于加工尺寸B=25mm±0.15mm,底面既是工序基准又是定位基准,所以ΔD=ΔB=0;对于加工尺寸A=20mm±0.15mm,F面是工序基准,E面是定位基准,工序基准与定位基准不重合,其基准不重合误差值决定于F面至E面间的尺寸公差,则ΔD=ΔB=δS=0.28mm。
本工序要求保证的加工尺寸A=20mm±0.15mm,其允差为0.30mm,而ΔD=0.28mm。由此可见,ΔD在加工误差中所占比重太大,以致留给其他加工误差的允差仅0.02mm,这就无法保证加工尺寸A=20mm±0.15mm的加工要求。为保证加工要求,需从工艺上采取措施。
(2)工件以圆柱孔定位
工件以圆柱孔定位时,常用的定位元件是定位销和芯轴,其基准位移误差既与二者之间的配合性质有关,还与定位元件的安装方式有关。基准不重合误差随具体情况而异。
① 圆孔与芯轴或定位销过盈配合:无论定位元件水平放置或垂直放置,过盈配合时定位副之间无间隙,定位基准与限位基准相重合,因此,基准位移误差为零,即ΔY=0。求该种情况的定位误差,实质就是求基准不重合误差。
② 工件以圆孔与芯轴或定位销间隙配合:
a.任意边接触:工件上圆孔与刚性芯轴或定位销间隙配合,定位元件垂直放置,构成任意边接触。因定位副之间有最小配合间隙,再加上定位副的制造误差,所以存在基准位移误差。其大小应等于因定位基准与限位基准不重合造成的加工尺寸的变动范围。一批工件定位基准变动的两个极端位置是圆孔直径最大,而定位销(或芯轴)直径最小。
如图2-65(b)所示,当孔径最大,而定位销直径最小,孔左右两边的母线与定位销接触时,可使定位基准沿工序尺寸h方向的位移量最大。其偏移量为最大配合间隙。
故基准位移误差(见图2-68)为:
ΔY=Dmax-d0min
因为 Dmax=D+δD,D=d0+Xmin
所以 Dmax=d0+Xmin+δD
因为 dmin=d0-
将Dmax和dmin代入上式得:
ΔY=δD++ Xmin
式中 δD——工件孔的直径公差,mm;
——定位销的直径公差,mm;
Xmin——最小孔径D与最大定位销直径d相配合的最小间隙,mm。

图2-68 孔与销的尺寸分布
当工件用长定位轴定位时,定位的配合间隙还会使工件发生歪斜,影响工件的平行度要求。所以,工件除了孔距公差外,还有平行度要求,定位配合的最大间隙同时会造成平行度误差,即:
式中 L1——加工面长度,mm;
L2——定位孔长度,mm。
【实例2-5】 如图2-69所示,在支承盘上铣圆弧R,要求保证与内孔轴线的距离为h1或与外圆下母线的距离为h2。若内孔与芯轴间隙配合,孔为,轴为
,试分析工序尺寸h2的定位误差。

图2-69 支承盘工序简图
解:首先,求基准位移误差。
ΔY=δD++Xmin=0.021+0.013+0.007=0.041(mm)
其次,求基准不重合误差,即为Z轴方向支承盘外圆半径的误差。
由于工序基准不在定位基面上,所以
ΔD=ΔY+ΔB=0.041+0.05=0.091(mm)
b.固定单边接触:工件上圆孔与刚性芯轴或定位销间隙配合,定位元件水平放置,构成固定边接触。如图2-70所示,存在定位基准位移误差,在Z轴方向的位置最大变动量的两个极限位置:一是定位销直径最大,内孔直径最小,固定在定位销的上母线接触,此时定位基准位于O1;二是定位销直径为最小,内孔直径最大,也与定位销上母线接触,定位基准位于O2。

图2-70 圆孔与芯轴固定单边接触基准位移误差
因此,定位基准位移误差是O1O2之间的距离,即:
综上所述,工件有以圆孔与芯轴或定位销间隙配合的两种接触方式,尽管工序尺寸标注相同,但随着定位元件与定位基准接触方式的不同,其定位精度不同。
(3)工件以外圆柱面在V形块上定位时的定位误差
由于工件外圆有制造误差,它将引起定位基准O1在V形块的对称轴线(Z方向)上产生变动,其最大变动量为O1O2,如图2-71所示。

图2-71 工件在V形块中定位
由△O1EB与△O2FB可知:
δ1与加工尺寸方向一致,故:
式中 α——V形块两限位基面间的夹角,(°);
δd——工件外径直径公差,mm。
上式中未考虑V形块α角的制造公差。这是因为V形块α角的公差很小,对sinα/2影响极微,可以忽略不计。
【实例2-6】 图2-72所示为在轴上铣键槽,以外圆柱面在α为90°的V形块上定位,求加工尺寸分别为A1、A2、A3时的定位误差。

图2-72 铣键槽工序简图
解:① 加工尺寸A1的定位误差。
a.工序基准是圆柱轴线,定位基准也是圆柱轴线,两者重合,ΔB=0。
b.定位基准相对限位基准有位移,根据式:
定位误差为:
② 加工尺寸A2的定位误差。
a.工序基准是圆柱下母线,定位基准是圆柱轴线,两者不重合,定位尺寸,故ΔB=δS=δd/2。
b.基准位移误差为:
c.定位误差合成。工序基准在定位基面上。当定位基面直径由大变小时,定位基准朝下变动;当定位基面直径由大变小、定位基准位置不动时,工序基准朝上变动。两者的变动方向相反,取“-”号,故:
③ 加工尺寸A3的定位误差。
a.工序基准与定位基准不重合,故ΔB=δd/2。
b.基准位移误差为:
c.定位误差合成。工序基准在定位基面上。当定位基面直径由大变小时,定位基准朝下变动;当定位基面直径由大变小、定位基准位置不动时,工序基准也朝下变动。两者的变动方向相同,取“+”号,故:
由上述三种工序尺寸的定位误差分析可知,在同样精度的V形块上定位,工序基准不同,定位误差不等,即:
ΔD(A2)<ΔD(A1)<ΔD(A3)
因此,控制轴类零件键槽深度的尺寸,一般多由下母线注起。
(4)一面两孔组合定位分析
前面介绍了一些常见的典型定位方式,都是以一些简单的几何表面(如表面、内孔和外圆柱面等)作为基准的。但一般机械零件很少以单一几何表面作为定位基准来定位,多数是以两个或两个以上的几何表面作为定位基准而采取组合定位。
【实例2-7】 如图2-61(a)所示,要钻连杆盖上的四个定位销孔。按照加工要求,用平面A及直径为的两个螺栓孔定位。
分析:在批量生产中,加工箱体、杠杆、盖板等类零件时,常以工件的一个平面和两个圆孔作为定位基准实现组合定位,简称一面两孔定位。这时,工件的定位平面一般是加工过的精基面,两定位孔可能是工件上原有的,也可能是专为定位需要而设置的工艺孔。
工件以一面两孔定位时,所用的定位元件是平面用支承板定位,两孔用圆柱销定位。这样,支承板限制了、
、
三个自由度,一个短圆柱销限制了
、
两个自由度,另一个短圆柱销限制了
、
两个自由度,属于重复定位,沿连心线方向的
自由度被重复限制了。当工件的孔间距(L±
/2)与夹具的销间距(L±
/2)的公差之和大于工件两定位孔(D1、D2)与夹具两定位销(d1、d2)之间的配合间隙之和时,将妨碍工件的装入。
(5)一面两孔定位时定位误差的分析与计算
工件以一面两孔在夹具的一面两销上定位时,如图2-73所示。由于O1孔与圆柱销之间存在最大配合间隙X1max,O2孔与菱形销之间存在最大配合间隙X2max,因此会产生直线位移误差ΔY1和角度位移误差ΔY2,两者组成基准位移误差ΔY,即:
ΔY=ΔY1+ΔY2
因为X1max<X2max,所以直线位移误差ΔY1受X1max控制。当工件在外力作用下单向位移时,ΔY1=X1max/2;当工件在任意方向位移时,ΔY1=X1max。
如图2-73(a)所示,当工件在外力作用下单向位移时,工件的定位基准O'1O'2会出现Δα的转角。

图2-73 连杆盖的定位方式与定位误差
【实例2-8】 根据图2-61,计算定位误差,分析定位质量。
连杆盖本工序的加工尺寸较多,除了四孔的直径和深度外,还有63mm±0.1mm、20mm±0.1mm、31.5mm±0.2mm和10mm±0.15mm。其中63mm±0.1mm和20mm±0.1mm没有定位误差,因为它们的大小取决于钻套间的距离,与工件定位无关;而31.5mm±0.2mm和10mm±0.15mm均受工件定位的影响,有定位误差。
解:① 加工尺寸31.5mm±0.2mm的定位误差。
由于定位基准和工序基准不重合,定位尺寸S=29.5mm±0.1mm,所以:ΔD=ΔS=0.2mm
由于尺寸31.5mm±0.2mm的方向与两定位孔连心线平行,故:
ΔY=X1max=0.027+0.017=0.044mm
由于工序基准不在定位基面上,所以ΔD=ΔY+ΔB=0.044+0.2=0.244mm。
② 加工尺寸10mm±0.15mm的定位误差。
由于定位基准与工序基准重合,ΔB=0。
由于定位基准与限位基准不重合,定位基准O1O2可作任意方向的位移,加工位置在定位孔两外侧。故:
左边两小孔的基准位移误差为:
ΔY=X1max+2L1tanΔα=0.044+2×2×0.00138=0.05mm
右边两小孔的基准位移误差为:
ΔY=X2max+2L2tanΔα=0.118+2×2×0.00138=0.124mm
定位误差应取最大值,故ΔD=ΔY=0.124mm。
2.3.2.2 定位误差计算实例
(1)工件以平面定位时的定位误差计算实例
工件以平面作定位基准时,三种定位误差都有可能存在。
【实例2-9】 图2-74(a)所示工件在夹具中,以平面定位铣表面1、2,要求保证的加工尺寸为A±δa=(30±0.08)mm及。已知:尺寸
,K=15mm,两定位基面的垂直度为±Δα=±6',两销钉高度差Δh=0.05mm,试分析并对比图2-74(a)、(b)两种定位方案的定位误差大小。

图2-74 平面定位时的定位误差分析之一(1,2为表面)
解:第一方案由于两定位基面是精基面,它们分别与尺寸A、B的工序基准重合,故对加工尺寸A±δa和B±δb来说,ΔB=0。但对基准位移误差来说,情况就较复杂,因为两定位基面间的位置误差以及限位基面上的支承销高度h的制造误差Δh(图2-74)都会造成定位误差。
如图2-75(a)、(b)所示,由于位置误差±Δα的存在,造成ΔY=±KtanΔα=±15×tan0.1°=±0.0262mm,但能满足(30±0.08)mm的精度要求。
图2-75(c)中,由于定位支承元件的限位基面高度尺寸的存在,使工件定位基面所产生转角误差Δθ为:tanΔθ=Δh/l=0.05÷100=0.0005,则Δθ=0.03°≈1'48″。此转角误差对加工尺寸
来说,若按几何关系仅增加定位误差0.01mm。故也可保证。
在采用图2-75(b)所示的定位方案时,对保证加工尺寸B来说,与前一种定位方案误差相同,即ΔB=0。但对尺寸A来说,虽然ΔY=0,而由于基准不重合,产生了。即使不计由位置误差和支承钉高度误差而引起的定位误差,仅计
,显然该定位方案不能保证尺寸A合格,故只能采用图2-75(a)所示方案。

图2-75 平面定位时的定位误差分析之二
从上述分析可知,欲提高平面定位精度,可采取以下措施。
① 恰当选择限位基面,力求基准重合,并控制定位尺寸公差值的大小,以减小ΔB。
② 提高各限位基面之间的位置精度和形状精度,以减小ΔY。
③ 增大支承钉之间的距离,并在定位元件装配后,将其限位基面同磨一次,以减小Δθ。
本例中,若不计后两种误差,则第一种定位方案可以认为ΔB=0,ΔY=0,Δθ=0,即ΔD=0。
【实例2-10】 镗削如图2-76所示工件ϕ15H7的孔,试求其定位误差。

图2-76 工件镗孔工序图
解:① 工件以平面定位,ΔY=0。
② 工序基准在上平面,定位基准在下平面,基准不重合。因此可知:
③ 定位误差为:
ΔD=ΔB=0.12mm
(2)工件以圆孔在芯轴(或短圆销)上定位时的定位误差计算实例
以圆孔作定位基面加工时,定位芯轴(或短圆销)在夹具中有两种安装方式。
① 芯轴水平安装:这种安装方式在车床、外圆磨床、卧式铣床和钻床等机床夹具中被广泛采用。此时若采用图2-77(a)所示的定位方式,由于基准重合,故ΔB=0,于是ΔD=ΔY。

图2-77 采用间隙配合的芯轴定位误差
分析ΔY则有两种情况:a.采用无间隙芯轴安装,则ΔY=0;b.若改用图2-77所示的间隙配合芯轴安装,由于定位副有制造误差,同时为安装方便还增加一最小安装间隙Xmin。于是,当定位基准处于两个极端位置中的最高位置[图2-77(b)中的O1点]和最低位置[图2-77(c)中的O2点]时,最大变动量为O1O2,这就是ΔY,其大小为:
式中 δD——定位孔的制造公差;
——芯轴限位基面的制造公差。
需要注意:同批工件中的任何一件,其定位基准相对于限位基准都要下降,在调整刀具位置(即决定对刀块到定位基准的尺寸)时,需预先加以考虑,使这项常量对加工尺寸不产生影响。
因此,对刀块工作面至限位基准的基本尺寸H(图2-78)应为:
式中 h——塞尺厚度,mm;
Xmin——定位孔与芯轴的最小间隙,mm。

图2-78 对刀块位置尺寸
【实例2-11】 在图2-77中,设a=40mm±0.1mm,,
。求加工尺寸a的定位误差。
解:a.求基准不重合误差ΔB。
定位基准与工序基准重合,ΔB=0。
b.求基准位移误差ΔY。
定位基准与限位基准不重合,定位基准单方向移动。其最大移动量为:
c.求定位误差ΔD。
ΔD=ΔY+ΔB=0.03+0=0.03mm
② 芯轴垂直安装:这种安装方式在齿轮加工机床、立式铣床、插床、立式分度夹具和一面双销定位的夹具中应用甚多。此时工件定位孔与芯轴为非固定边任意接触(图2-79),工件在沿水平面XOY内任何方向上都可能产生双边径向定位误差ΔY。若ΔB=0时,则:
ΔD=ΔY=O1O2=Xmax
式中 Xmax——定位副的最大配合间隙,mm。

图2-79 非固定边任意接触的定位误差
因此,欲减小定位芯轴定位时的定位误差,就应减小配合间隙。
【实例2-12】 如图2-80所示,在金刚镗床上镗活塞销孔。活塞销孔轴线对活塞裙部内孔轴线的对称度要求为0.2mm,活塞以裙部内孔及端面定位,内孔与限位销的配合为ϕ95,求对称度的定位误差。

图2-80 镗活塞销孔示意图
1—工件;2—镗刀;3—定位销
解:查表:,
。
① 求基准不重合误差ΔB。
对称度的工序基准是裙部内孔轴线,定位基准也是裙部内孔轴线,两者重合,则ΔB=0。
② 求基准位移误差ΔY。
定位基准与限位基准不重合,定位基准可任意方向移动。
ΔY=δD+δd+Xmin=0.035+0.022+0.012=0.069mm
或
ΔY=Dmax-dmin=95.035-(95-0.034)=0.069mm
③ 求定位误差ΔD。
ΔD=ΔY=0.069mm
从数值上看,ΔD接近工件要求公差的三分之一。
(3)工件以外圆柱面在V形块上定位时的定位误差计算实例
如图2-81所示,当工件在夹具的V形块上以外圆柱面作为定位基面时,一般认为保证定位基面处于V形块的假想对称平面上,则定位基准在水平方向上的位移误差不存在,;但在垂直方向上,由于定位基面
存在制造误差δd,故产生基准位移误差应为
。因此可以看出,当δd一定时,V形块夹角α越大,则
就越小,定位精度就越高,但其定位稳定性就越差,故一般取α=90°。同时,V形块的定位误差大小还与加工工序尺寸的标注有关,如图2-81所示,有三种情况,并按表2-7所述。

图2-81 工序尺寸标注不同时的定位误差
表2-7 外圆柱表面工序尺寸标注不同时的定位误差对比

由上述三种工序尺寸的不同标注方式所得的三种定位误差对比可以看出:
<ΔD<
。故在控制轴类零件上(如键槽深度、端面孔心距等)工序尺寸时,一般多以下母线或轴线作工序基准。
【实例2-13】 如图2-82所示的定位方式在阶梯轴上铣槽,V形块的夹角为90°,试计算加工尺寸74mm±0.1mm的定位误差。

图2-82 阶梯轴在V形块中定位铣槽
解:查表可知ϕ40f9(),ϕ80f9(
)。
① 定位基准是小圆柱的轴线,工序基准在大圆柱的素线上,基准不重合误差为:
ΔB=δd/2+t=0.074÷2+0.02=0.057mm
② 基准位移误差为:
③ 工序基准不在定位基面上,则定位误差为:
ΔD=ΔY+ΔB=0.057+0.044=0.101mm
【实例2-14】 如图2-83所示,工件以外圆柱面在V形块上定位加工键槽,保证键槽尺寸,试计算其定位误差。

图2-83 定位误差计算
解:① 求基准不重合误差ΔB。
定位基准为工件的中心线,设计基准为工件的下母线,故:
② 基准位移误差ΔY为:
③ 求定位误差ΔD。因为设计基准在定位基面上,且设计基准变动方向与定位基准变动方向相反,故ΔD=ΔY-ΔB≈0.0177-0.0125=0.0052mm
(4)工件以一面两孔定位时的定位误差计算实例
当工件以一面两孔定位、夹具以一面双销限位时,应在分析基准位移误差的基础上,根据加工工序尺寸标注,通过几何关系转换为定位误差。
这种定位方式的基准位移误差包括两类(图2-84)。

图2-84 双孔定位误差计算
① 沿图示平面内任意方向移动的基准位移误差ΔY,它的大小取决于第一定位副的最大间隙X1max[图2-84(a)],即:
ΔY=+
+X1min=X1max
② 转角误差Δα[图2-84(b)]近似值为:
所以
式中 ——孔直径公差;
——销直径公差;
X1max,X2max——两定位副的最大配合间隙。
注意:若工件可以任意方向角位移,则应按双向转角误差2Δα计。
【实例2-15】 钻铰如图2-85(a)所示凸轮上的两个小孔ϕ16mm,定位方式如图2-85(b)所示。定位销直径为,求加工尺寸(100±0.1)mm的定位误差。

图2-85 凸轮上钻孔定位方案
解:① 工序基准与定位基准重合,ΔB=0。
② 定位基准相对限位基准固定单边移动,定位基准移动方向与加工尺寸方向之间的夹角为30°±15'。所以。
③ 定位误差为ΔD=ΔY=0.02mm。
【实例2-16】 泵前盖工序简图如图2-86所示,工件以上表面和孔定位,镗削
孔,同时铣削两端面尺寸
。现设计双销中心距及偏差、两销的基本尺寸及偏差,并计算其定位误差。

图2-86 泵前盖一面双孔定位的定位误差
解:首先进行一面两孔定位其定位元件设计。
① 确定两定位销的中心距。
两定位销中心距的基本尺寸应等于工件两孔距的平均尺寸,其公差一般为:
因
故取
② 确定定位销d1的直径。圆柱定位销的基本尺寸应等于与之配合的工件孔的最小极限尺寸,其公差带一般取g6或h7。
泵前盖定位孔直径为,故取圆柱销的直径d1=9.972mm。
③ 选择菱形销宽度b。按表2-6,选取b=4mm。
④ 确定菱形销直径d2。
a.计算补偿量:
b.计算最小间隙
c.计算菱形销的直径:
⑤ 取公差带h6,可选用标准代号为B9.956×12GB/T 2203的菱形销。再进行定位误差计算。
a.垂直度0.050mm,则ΔD=0。
b.对称度0.03mm,则ΔB=0。
已知=0.016mm、
=0.015mm、X1min=0,则基准位移误差ΔY为:
c.平行度0.05mm,当工件歪斜时,转角误差Δα的计算公式为:
因为ΔB=0,得定位误差,设计结果如图2-87所示。

图2-87 泵前盖一面双孔定位设计