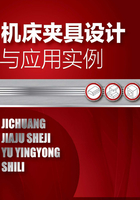
1.2 机床夹具的相关知识
在机床上用来固定加工对象,使之占有正确加工位置的工艺装备,称为机床夹具(以下简称夹具)。对实现机械加工的高质量、高生产率、低成本具有重要的作用。
1.2.1 工件的装夹
(1)工件装夹的实质
在机床上对工件进行加工时,为了保证加工表面相对于其他表面的尺寸和位置精度,首先需要使工件在机床上占有准确的位置,并在加工过程中能承受各种力的作用,从而始终保持这一准确位置不变。前者称为工件的定位,后者称为工件的夹紧,整个过程统称为工件的装夹。
定位和夹紧一般是指装夹工件先后(有时是同时)完成的两个动作,是两个不同的概念,具有不同的功用。定位是使工件占有正确的位置;夹紧是使工件保持定位的位置不变,它并不起定位作用。
由此可知,工件装夹的实质就是在机床上对工件进行定位和夹紧。工件装夹的目的是:通过定位和夹紧使工件在加工过程中始终保持其正确的加工位置,以保证达到该工序所规定的加工技术要求。
(2)装夹工件的方法
在机床上装夹工件的方法一般有两种。
1)将工件直接装夹在机床工作台(或花盘)上。此法一般需要逐个按工件的某一表面或按划线找正工件的加工位置,然后夹紧。
2)使用各种通用的或专用的机床夹具来装夹工件(和引导刀具)。
在机械加工中,在不同的生产条件下,其装夹方式也不同。按照工件定位方式的不同,可分为找正装夹和不找正装夹两种。找正装夹按找正的方式不同,又可分为直接找正装夹和划线找正装夹两种。
① 直接找正装夹:直接找正装夹就是根据工件某些表面,利用划针、百分表或目测来找正工件的位置。例如图1-3所示的偏心环毛坯,要在车床上加工与外圆表面A同轴的孔C和D;用直接找正法装夹,如图1-4所示。先将工件以较小的夹紧力装在车床四爪卡盘的某一位置上,然后用划针盘找正工件外圆表面A,使其轴线与车床主轴回转轴线同轴(即目测划针与外圆表面A之间的间隙,在工件回转一周中,其值应变化很小或不变)之后,将工件夹紧。这种方法是用工件的表面A作为找正装夹的依据,即为直接找正。

图1-3 偏心毛坯

图1-4 直接找正装夹
直接找正装夹的工艺特点如下。
a.装夹精度取决于工人的经验及所用的找正工具,一般误差为0.1~0.5mm。如果是经验丰富的工人,采用比较精确的找正工具,其误差为0.005~0.01mm。
b.找正工件位置所需的时间长,生产率低。
c.采用直接找正装夹,必须由技术较熟练的工人操作。另外,工件还必须具备可供找正的表面。
d.直接找正的装夹方式,不需要使用专用夹具,所以在单件小批生产或修理、试制车间得以应用;此外,对工件装夹精度要求很高(例如堤差为0.005~0.01mm或更小),采用专用夹具不能保证时,可采用精密量具进行直接找正。
② 划线找正装夹:划线找正装夹是根据加工要求,先在工件上划好线,然后利用划针、百分表或目测按线找正工件位置的方法。如图1-5所示,装夹工件前,先在工件端面B上划出一个与外圆表面A的同轴圆F。装夹工件时,用卡盘将工件轻夹(夹紧力小,在某一位置上),然后用划针找正F圆。目测F圆确实与机床主轴轴线同轴,即可最后夹紧工件。

图1-5 划线找正装夹
划线找正装夹的工艺特点如下。
a.装夹精度比直接找正装夹低。主要原因是:除目测误差外,还增加了划线误差和冲中心眼的误差(需按中心眼划F图),这些误差累积起来,就造成了装夹精度低。
b.由于增加了划线工序,使工艺路线加长,而且划线要由技术熟练的工人来操作,耗费时间较长,所以,既降低了生产率,又增加了成本。
c.装夹时是按照划好的线找正,比直接找正需要的时间短,故加工工序的生产率较高。
d.划线找正的装夹方式,一般应用在单件小批生产中或在加工大型零件时,或采用专用夹具(不找正)不经济或没有直接找正的表面时。当毛坯制造误差很大,表面粗糙,工件结构复杂(如箱体件),以致使用专用夹具装夹(不找正)不能保证加工表面有足够的余量或余量不均匀,以及不能保证工件的加工面与不加工面之间的位置精度时,也应采用划线找正装夹法。
③ 不找正装夹:工件装夹时,不需任何找正,将工件装夹在夹具中,就能保证工件与机床、刀具间正确的相对位置,这种装夹方式称为不找正装夹。
图1-6所示是用专用车床夹具进行不找正装夹的示意图。此夹具上有两个相对于车床主轴轴线可做径向等距移动的V形块(双V形块自动定心机构)。装夹时,将工件放在双V形块之间,使双V形块同时向心移动;V形块与工件的外圆表面A接触并夹紧。该车床夹具是专为加工此偏心环(图1-3)设计制造的,它能使工件在装夹时迅速而正确地定位并夹紧,保证A面与机床主轴同轴。这种装夹方式即为不找正装夹。

图1-6 不找正装夹
不找正装夹方式的工艺特点是:定位精度由夹具保证,不用较高技术等级的工人,就能保证较高的定位精度;降低了生产费用;减轻了工人的劳动强度;提高了劳动生产率。因此,不找正装夹在成批、大量生产中得到了广泛的应用。表1-1为各种装夹方法的比较。
表1-1 各种装夹方法的比较

1.2.2 机床夹具的组成
【实例1-2】 加工如图1-7所示连杆盖的A平面和B平面,生产类型为成批生产,在立式铣床上用立铣刀加工。

图1-7 连杆盖
解:为了保证加工精度要求,需要限制工件的六个自由度。选用D平面及两个孔为定位基准。
图1-8就是为此工序设计的夹具。夹具体左右两端的U形豁口用来穿螺栓,以便将夹具紧固在机床工作台上。夹具体12下面装两个夹具定向键13,用来插入铣床工作台的T形槽中(定向键侧面与T形槽配合),起定向作用。夹具的对刀块1用来对刀,即用于使工件相对于刀具在垂直方向和水平方向保持应有的位置。夹具的支承板8和圆柱销10、菱形销2是定位元件。在工件装夹时,将已加工好的两个孔分别套在两个定位销上,并使D面与夹具定位板贴紧,然后将压板7转移到工件上表面,拧紧螺母4,用压板7压紧工件。该夹具定位板限制三个自由度,两个定位销也限制三个自由度。

图1-8 铣连杆盖凹台面的专用夹具
1—对刀块;2—菱形销;3—螺栓;4—螺母;5—球面垫圈;6—凹面垫圈;7—压板;8—支承板;9—弹簧;10—圆柱销;11—定位板;12—夹具体;13—夹具定向键;14—螺钉;15—销钉
从该例题可以看出,机床夹具由以下几部分组成。
(1)定位元件
这是用来与工件定位基准接触,以便确定工件与机床、刀具的相对位置的夹具元件。如图1-8中的定位板11、圆柱销10、菱形销2。
(2)夹紧机构
夹紧机构也称为夹紧装置。它是用来夹紧工件,使其在切削力、重力、离心力等作用力下仍能牢固地紧靠在定位元件或其他支承上所用的机构。如图1-8上的压板7、螺栓3、弹簧9、球面垫圈5、凹面垫圈6及螺母4。
(3)对刀元件和导向元件
铣床夹具具有对刀块1和夹具定向键13,钻床夹具具有钻模套(导向套)。
(4)夹具体
这是夹具的基础件,夹具的所有元件和机构都装在它上面。整个夹具通过夹具体12与机床相连接。
(5)其他元件和机构
例如,为了实现多工位的分度机构及锁紧装置、车床夹具的平衡锤等而设置的元件。
其中,定位元件、夹紧机构、夹具体是机床夹具的基本组成部分。
1.2.3 机床夹具的分类
尽管机床夹具的种类繁多、形状千差万别,但可以通过其使用特点、工艺过程、机床的种类、所采用的夹紧动力源等方法进行分类。
(1)按使用特点分类
① 通用夹具:是指已经标准化的、可用于一定范围内加工不同工件的夹具。如三爪自定心或四爪单动卡盘、机用虎钳、回转工作台、万能分度头、磁力工作台等。这类夹具已作为机床附件,可充分发挥机床技术性能和扩大工艺范围。
② 专用夹具:图1-8是专门为铣连杆盖凹台面工序而设计制造的专用夹具。它一般在一定批量生产中应用,是本课程研究的主要对象。
③ 通用可调与成组夹具:这两类夹具结构相似。其共同点是:在加工完一种工件后,经过调整或更换个别元件,即可加工形状相似、尺寸相近或工艺相似的多种工件。在当前多品种、小批量生产条件下,这两类夹具是改革工艺装备设计的一个发展方向。
④ 组合夹具:是指按某一工件的某道工序的加工要求,由一套事先准备好的通用的标准元件和部件组合成的夹具。这种夹具用完后,可以拆卸存放、多次反复使用,具有组装迅速、周期短的特点,是多品种、小批量或新产品试制、数控加工中的一种较经济的夹具。
⑤ 拼装夹具:拼装夹具是在成组工艺基础上,用标准化、系列化的夹具零部件拼装而成的夹具。虽有组合夹具的优点,但比组合夹具有更好的精度和刚性,更小的体积和更高的效率;同时,它的基础板和夹紧部件中常带有小型液压缸,因而较适合柔性加工的要求,常用作数控机床夹具。
(2)按工艺过程分类
按工艺过程,可分为机床夹具、检验夹具、装配夹具、焊接夹具等。
(3)按机床的种类分类
按机床的种类,可分为车床夹具、铣床夹具、加工中心夹具、钻床夹具等。
(4)按所采用的夹紧动力源分类
按所采用的夹紧动力源,可分为手动夹具、气动夹具等。
1.2.4 机床专用夹具应满足的基本要求
机床专用夹具设计是工艺准备的重要工作内容之一。机床专用夹具设计必须满足以下基本要求。
① 保证工件的加工精度:保证工件的加工精度是机床夹具设计的根本目的。专用夹具应有合理的定位、夹紧方案,尤其对于精加工工序,应有合适的尺寸、公差和技术要求,并进行必要的精度分析,确保工件的尺寸公差、形位公差和表面质量等。
② 提高生产率:专用机床夹具的复杂程度及先进性应与工件的生产纲领相适应,根据工件的生产批量的大小进行合理的设置,以缩短辅助时间,提高生产率。
③ 工艺性好:专用机床夹具的结构应简单、合理,便于加工、装配、检验和维修。
④ 使用性好:专用机床夹具的操作应简便、省力,安全可靠、排屑方便,必要时可设置排屑装置。
⑤ 经济性好:应能保证专用夹具具有一定使用寿命和较低的夹具制造成本。适当提高夹具元件的通用化和标准化程度,以缩短专用夹具的制造周期,降低专用夹具成本。
在考虑上述几个因素的要求时,应在满足加工要求的前提下,处理好几个因素的关系。
1.2.5 机床专用夹具的功用
(1)保证工件的加工精度
在成批、大量生产条件下,通常所采用的不找正装夹加工中,工件加工表面相对于其他表面的位置精度主要是由夹具保证的。用该种方法(即完全用夹具将工件定位),可以比较容易地获得精度,并使一批零件的加工精度稳定。
(2)提高劳动生产率
使用机床夹具装夹工件,通常不需要划线和找正,这样可以减少辅助时间。此外,用机床夹具装夹工件,还容易实现多件加工、多工位加工,使基本时间与辅助时间重合,可以进一步缩短辅助时间,提高劳动生产率。
(3)扩大机床的应用范围
在一些中小型工厂里,为了满足不同零件的加工要求,并且使各种机床的负荷能够比较均衡,常常需要以一种机床代替另一种机床来工作。这可以通过采用适当的夹具来实现。例如,在车床或铣床上采用镗模夹具,可以对箱体件进行镗孔,使车床、铣床具有某些镗床的功能。
(4)减轻工人的劳动强度
夹具越先进,工人的劳动强度越小。采用气动夹具、液压夹具等,可以大大减轻工人的劳动强度。
1.2.6 夹具保证加工精度的原理与工艺系统
【实例1-3】 图1-9(a)所示为铣轴上键槽的工序,试分析该机床夹具能否保证工序加工精度要求。
解:图1-9(a)所示为铣轴上键槽的工序,工件以外圆柱60.2mm和端面C为定位基面,在V形块5和圆柱销6上定位,用液压传动的压板3夹紧,所采用的夹具结构如图1-9(b)所示。本工序加工中,键槽的技术要求能否保证取决于以下因素。

图1-9 液压铣槽夹具
1—夹具体;2—液压缸;3—压板;4—对刀块;5—V形块;6—圆柱销;7—定向键;8—铣床工作台
① 键槽的宽度B和表面粗糙度,由铣刀保证。
② 夹具通过两个定向键7与铣床工作台8的T形槽配合,由于T形槽与机床导轨方向一致,而夹具上的V形块5的轴线(即工件的轴线)与底面及定向键的一侧面(称为夹具的安装基面)平行,因而能保证所加工键槽的侧面和槽底与其轴线平行,其公差在0.1mm以内。
③ 工件在V形块5上定位时,其轴线在V形块的对称中间平面上,而对刀块4的垂直工作面至V形块对称面的距离为B/2+S(B为铣刀宽,S为塞尺厚),通过塞尺对刀,可使铣刀和V形块两者对称面的对称度误差在0.2mm之内。
④ 对刀块的水平工作面至V形块轴线之距离H=24.6-S,通过塞尺对刀,又可使槽深的加工尺寸24.6mm得到保证。
⑤ 工件定位时,其端面C紧靠圆柱销6,故槽长l可由铣床工作台上的行程挡铁来控制(图中未表示)。
这样,该夹具就使同批工件在夹具中有一致的正确装夹位置;而夹具借对刀块将刀具调到加工面的位置上;加工时,夹具又借定向键和底面正确安装在机床上。机械加工中在“机床-刀具-夹具-工件”这一工艺系统内,四要素构成了相应的静/动态几何关系。图1-10(a)所示为夹具和机床、刀具、工件之间的联系关系,由于夹具由各元件和组件构成,图中点画线框内即为夹具的各元组件和其他三要素的联系关系。图1-10(b)为四要素之间相互直接联系的尺寸/几何关系。因此夹具设计时最基本的要求就是保证图1-10(b)中工件加工尺寸在工序完成后,达到工序尺寸/几何精度要求。最后再考虑如何提高生产率和降低成本等其他问题。

图1-10 “机床-刀具-夹具-工件”工艺系统内四要素之间的相互联系关系
1.2.7 夹具设计工作的特点和基本要求
1.2.7.1 夹具设计工作的特点
① 针对性强,设计人员必须全面掌握工艺和生产现场的实际情况。专用夹具是为某零件的某工序设计的,设计人员必须全面了解和掌握产品零件的要求,工艺过程的安排以及所使用的机床、刀具、辅具的具体情况,才可能提出合理可行的最佳方案,确定最合理的定位、夹紧装置。
② 保证加工质量和劳动生产率是夹具设计的两项主要任务,而保证加工质量又是第一位的。
夹具设计时,应重点把住定位方案的确定和精度分析这两道关,对于制造精度要求不高的零件,其夹具设计应重点保证提高劳动生产率和改善劳动条件。
③ 夹紧机构对整个夹具结构起决定性作用。夹紧装置的结构形式和种类很多,选用的灵活性很大,特别是夹紧装置中力源及传动机构的设计对夹具结构的影响最大。因此,在同样能保证工序要求的情况下,每个人设计的结构可能大不相同。而不同复杂程度的夹具在不同的生产规模条件下,其经济效果也不一样,设计人员必须使自己的设计与生产规模相适应,不可片面追求高精度而忽视了经济性。
④ 夹具的制造多属于单件生产。设计时应考虑采用组合加工、修配和调整等措施来保证夹具的制造精度,尽可能地考虑设置修配和调整环节,而不能依靠用完全互换的办法来保证制造精度。
⑤ 设计周期短,一般不进行强度、刚度计算。夹具设计是直接为产品生产服务的生产技术准备工作,其设计周期要求短,因此设计时多采用参照法或凭经验确定的办法来保证受力件的强度和刚度,通常不进行详细计算,有时采用简便公式或用图表作为设计参考。但是应注意,在设计一些具有较高精度要求的夹具时,应该对定位精度、夹紧力(矩)等进行必要的计算和分析。
1.2.7.2 夹具设计的基本要求
夹具设计的原则是经济和适用,它可以概括为“好用、好造、好修”这6个字。其中好用是主要的,但好用也必须以不脱离生产现场的实际制造和维修水平为前提。具体要求如下。
① 夹具的构造应与其用途和生产规模相适应,正确处理好质量、效率、方便性与经济性四者的关系。
② 保证工件精度。
③ 保证使用方便,要便于装卸、便于夹紧、便于调整、便于测量、便于观察、便于排屑排液、便于安装运输,保证安全第一。
④ 注意结构工艺性,对加工、装配、检验和维修等问题应通盘考虑,以降低制造成本。