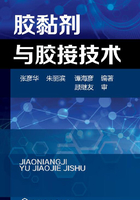
1.3 胶接流变学与胶接破坏
根据胶接的机械结合理论,在胶接木材这类多孔类材料时,胶黏剂以何种程度渗透到其内腔,又以何种方式形成有效的胶钉后才能最大限度地作用胶接强度成为研究重点。胶黏剂如何渗透到木材中的内腔是和胶黏剂的流动特性、木材的表面状态、木材和胶黏剂的浸润等相关。
1.3.1 胶接流变学
有关胶接的试验方法有许多种类,这些方法都与材料的变形和破坏有关,因此在通过试验结果所观察到的有关胶接的各种现象中,不考虑流变学问题难以理解的现象有很多。胶接的流变学主要与胶黏剂的黏弹性、流变学有较大关联,充分掌握胶黏剂的黏弹性,以便准确把握胶接体系的力学性能与结构特性及其应用问题。
1.3.1.1 胶黏剂的黏弹性
胶黏剂是聚合物材料,不仅限于力学方面的弹性,还包含黏性问题,即作为黏弹体而表现其特性。
理想弹性体(如钢制弹簧)在外力作用下平衡形变是瞬时达到的,与时间无关;理想黏性体(如水等低分子液体)在外力作用下,形变是随时间线性发展的;聚合物的形变性质与时间有关,其关系介于理想弹性体和理想黏性体之间。聚合物材料常被称为黏弹性材料。黏弹性是聚合物材料的另一重要特性。
聚合物的黏弹行为表现在蠕变、应力松弛和动态力学性质三个方面。唯象学的研究系从力学模型开始,首先假定聚合物各向同性,并且由均一的结构单元组成(如分子量是单分散的)。然后分别用理想弹簧和理想黏壶为代表研究固体的弹性和黏性。胶黏剂(聚合物)的黏弹性问题,是更准确地把握和解释胶黏剂和胶接接头的力学性能的关键问题。
1.3.1.2 胶接流变学
与胶接相关的性能多数情况是先使胶黏剂和被胶接材料接触后,再以一定的方式(标准等)使其破坏来进行评价的。无论是接触过程,还是破坏过程都伴有流变学特征。胶接体系的破坏形态是多样性的。如内聚破坏和(或)界面破坏,而且非常复杂。为了严密地解析其破坏形态,必须正确地把握各种材料的内应力及应变的分布和破坏条件。
胶接流变学主要从剪切胶接试验、拉伸胶接试验、剥离试验、冲击强度试验、持久强度试验、疲劳强度试验进行论证。
(1)剪切胶接试验 剪切胶接试验是对胶接面平行地施加外力。
(2)拉伸胶接试验 拉伸胶接试验是在与胶接面垂直的方向施加外力。
(3)剥离试验 剥离试验是使被胶接材料的一方大幅度弯曲,并对其施加外力。
(4)冲击强度试验 冲击强度是指胶接试样受到冲击破坏时,胶黏剂可能吸收的能量,或者是胶黏剂可吸收的能量,或者是胶黏剂抵抗冲击能而消耗的功。冲击强度以单位胶接面积上的功表示,单位N·m/m2。
(5)持久强度试验 胶接接头在恒温下和规定的时间内,每单位面积所承受的最大负荷称为持久强度。胶接接头在小于静态破坏力的作用下,胶黏剂层在长时间应力作用下,内部会发生塑性流动,胶接接头失去稳定性,胶接强度不断下降,到一定时间后接头便发生破坏。
(6)疲劳强度试验 接头的疲劳强度是指在给定条件下,对胶接接头重复施加一定载荷至规定的次数而不引起破坏的最大应力。胶接接头在实际应用中不仅承受静态载荷,而且也承受动态载荷。一般情况下,在比静态载荷小得多的动态载荷下,胶接接头就可能产生破坏。因此,必须测定胶接接头的疲劳强度。
1.3.2 胶接破坏
胶接接头在材质上是不完全连续的,通常是应力集中部位,在外力和环境应力作用下,可能导致接头破坏。单位胶接面积或单位胶接长度上所能承受的最大载荷成为接头的破坏强度。胶黏剂多为高分子材料,因此其破坏必定存在流变学现象。破坏强度在黏弹性体上呈现出特征的速度(时间)依赖性或温度依赖性。
胶接接头是零部件材质不完全连续的部分,通常是应力集中部位,在外力和环境应力作用下,可能导致接头破坏。单位胶接面积或单位胶接长度上所能承受的最大载荷称为接头的破坏强度。
胶接接头的结构在形成和使用过程中,由于胶黏剂的固化或硬化造成体积的收缩、被胶接材料和胶黏剂不同的热膨胀率及受环境介质的作用等都将造成胶接结构中的内应力,而内应力的分布也是不均匀的。因此胶接结构的破坏从组成该结构的薄弱部分开始,根据接头破坏的位置可以划分为四种破坏类型:被胶接物破坏、内聚破坏、界面破坏和混合破坏,具体类型如图1-1所示。

图1-1 胶接接头破坏类型
被胶接材料破坏和胶黏剂的内聚破坏,主要取决于二者材料的自身强度。当然还与材料内部的缺陷、构成接头后体系内部胶层厚度、被胶接表面处理状况、组分间相互作用等有关。此时,接头强度并不等于材料自身强度,一般略低于材料强度,当然也有少数例外的情况。
界面破坏的原因是被胶接材料的可黏性差。由于材料的非均一性及表面处理、工艺实施等环节的不均一性,完全的界面破坏是不存在的。在理想的条件下,即没有界面区存在时,其破坏强度主要取决于胶黏剂与被胶接物之间的黏附强度。混合破坏的情况,在各种材料强度相近时特别容易发生。
接头破坏类型会随着各种条件的变化而转变。对于黏弹性聚合物,当温度升高时,分子链段热运动增加,应力松弛过程加快,受载时变形较大而强度较低。同样加载速度降低,外力作用时间增加了,应力松弛更充分,因此受载时,变形较大,强度较低。温度和加载速度对胶接强度的上述影响,其内在联系是十分明显的。当增加测试的加载速度或降低测试温度时,接头从内聚破坏转向界面破坏。这是由于胶黏剂的模量和内聚强度增加的缘故。
大量的测试结果表明,胶膜变厚、慢速测试和升高测试温度三者是等效的,往往导致内聚破坏;胶膜变薄、快速测试和降低测试温度也是等效的,结果导致界面破坏。
高分子材料的破坏都表现出一定的流变学特性,其破坏强度具有“时间-温度的等效性”,即增加外力的作用时间等效于提高温度,降低外力作用时间等效于降低温度。
1.3.3 影响胶接破坏(胶接强度)的主要因素
在胶接接头体系破坏的类型中,被胶接物和胶黏剂的内聚破坏是由材料的选择、使用不当或者是材料工业发展水平限制所造成的。在充分润湿的条件下,胶接接头发生纯粹的界面破坏是不可能的。实际上,在各类破坏中都存在着一定程度的界面破坏。此外,接头的破坏还与被胶接物的表面状态、被胶接物和胶黏剂特性、胶接工艺以及环境应力等因素有关。
1.3.3.1 被胶接物的表面状态
表面粗糙度是产生机械胶接力的源泉,机械胶接力是通过湿润和吸附作用而得到的,尤其适用于被胶接物为木材类的胶接。但无论是木材还是其他多孔性材料,随着表面粗糙度系数的增加,有效胶接表面积增加,胶接强度随之增加,但随后表面粗糙度增加到一定值后,胶接强度反而下降。这与金属的情况基本相似。
关于被胶接材料的表面粗糙度对胶接破坏的影响还与其他因素有关。例如,加压的作用,对于表面粗糙的被胶接材料的胶接较为显著,对表面光滑的被胶接材料来说,即使在低压下也能基本上达到加压作用的胶接效果,而对能被胶黏剂润湿的胶接材料,粗糙度对胶接强度的影响较小。此外,粗糙度的影响还需要考虑到被胶接材料的密度,例如密度大的、表面十分粗糙的木材,其胶接效果较差。因此,在确定被胶接材料表面粗糙度时,要根据胶黏剂在被胶接材料表面的润湿情况具体而定。
1.3.3.2 弱界面层
弱界面层的产生是由于被胶接的材料、胶黏剂、环境以及它们共同作用的结果。当被胶接的材料、胶黏剂及环境中的低分子物或杂质等,通过渗析、吸附及聚集等过程,在部分或全部界面内产生这些低分子物的富集区,这就是弱界面层。
胶接力在外力作用下的破坏,必然发生于弱界面层,这就是胶接破坏中的界面破坏,并使胶接强度急剧下降的原因。弱界面层的产生条件:胶黏剂与被胶接材料间的胶接力主要来源于分子间的物理吸附作用,即次价键力的体系,弱界面层才有影响;低分子物在胶黏剂与被胶接材料中有渗析行为,通过渗析作用低分子物迁移界面形成富集区而形成弱界面层时,才对胶接接头破坏起作用;胶接体系中的低分子物对被胶接物的表面有比胶黏剂分子更强的吸附力,使被胶接物的表面产生新的吸附平衡,并形成低分子吸附层,对胶黏剂分子起了解吸作用,才对胶接接头破坏有影响。
须强调的是,胶接结构的界面破坏,不能全部归结为弱界面层的作用。事实上除了弱界面层的作用外,还有不少其他因素可使胶接结构出现界面破坏。
1.3.3.3 内应力
胶接结构的内应力是胶接接头破坏的重要原因之一,胶接体系的内应力主要是收缩应力和热应力两类。收缩应力是胶黏剂固化过程中体积收缩产生的应力;热应力是被胶接材料的各向异性,在水分变化的条件下,被胶接材料之间收缩膨胀系数不同、温度变化所产生的应力。当胶接接头是由密度不相同的多种材料构成时,不同被胶接材料之间以及它们与胶黏剂之间,由于膨胀系数不相同,温度变化时就产生热应力。
收缩应力产生的本质过程是固化反应中的体积收缩。不同的固化方式产生应力的原因是不同的。溶剂型胶黏剂,其固体含量一般在20%~60%,固化和硬化过程中由于溶剂的挥发而导致体积收缩最严重。热熔型胶黏剂,由于冷却速度的变化、温度的分布梯度、聚合物的结晶度及结晶区的分布等均会产生内应力。热固性胶黏剂,在凝胶之后的分子运动受阻,尤其在玻璃化之后,分子运动更加困难,因此在凝胶之后进一步固化反应是造成收缩应力的主要原因。例如,热固性酚醛树脂,在固化反应中逸出小分子的水,固化体积收缩率比环氧树脂大5~10倍。因此,为了提高胶接接头的强度,应该根据胶黏剂类型及其固化方法,采取降低收缩应力的措施,如降低官能团浓度、加入聚合物增韧剂或加填充剂(填料)。
热应力是热膨胀系数不等的材料胶接在一起,由于温度的变化,在胶接界面产生相应的变化。热应力大小正比于温度的变化、胶黏剂与被胶接材料膨胀系数的差异及材料的弹性模量。因此为了避免热应力的产生,胶接膨胀系数相差很大的材料,一般可选择比较低的固化温度。在许可的范围内,尽量选用模量低、延伸率高的胶黏剂,使热应力通过胶黏剂的变形释放出来。适当提高胶层厚度,选用室温固化的胶黏剂等都可减小胶接接头的热应力。
1.3.3.4 交联度
聚合物胶黏剂的内聚强度,是随着交联密度的增加而增大。这与交联点的数目和交联分子的长度有关,随着交联点的数目的增加,交联间距变短以及交联分子长度变短,交联后的胶黏剂变得又硬又脆,因而会降低胶黏剂的内聚强度。
在胶黏剂中加入交联剂,虽然会减弱相容性并丧失黏附性,但胶黏剂的极性基团被适当吸收在被胶接材料的表面上后,使还未反应的交联剂有提高胶黏剂内聚强度和胶接强度的作用。例如,使用胶接完成后就完成交联的橡胶类胶黏剂,即可得到胶接强度和内聚强度都很高的胶接制品。
1.3.3.5 极性
被胶接材料的极性与润湿性关系较大。含有极性分子水、乙醇、酯类等的胶黏剂能很好地润湿被胶接材料,有利于胶接。一般来说,随着胶黏剂极性的增强(或极性基团的增多),胶接强度在开始时会增加,但到了一定程度后,增加极性基团,胶黏剂的内聚强度增大,胶黏剂不易流动,从而对被胶接材料湿润不良,胶接强度下降。非极性胶黏剂胶接非极性材料,极性胶黏剂胶接极性材料。
1.3.3.6 胶黏剂的分子量及分子量分布
聚合物胶黏剂的分子量大小及其分布对胶接强度有较大的影响。分子量较小时,具有较低的熔点,较小的黏度,胶接性能良好,但内聚能较低,获得的胶接内聚强度不高;聚合物分子量较大时,难以溶解,熔点高,黏度较大,胶接性能较差。不过内聚强度较大,可能获得较高的胶接强度。一般胶黏剂所用聚合物应在相应的分子量范围内,胶黏剂才能有良好的胶接性能和较高的胶接内聚强度。在极性胶黏剂主剂选用和分子结构设计时,应当控制聚合物的分子量。一般在适宜的分子量范围内,分子量偏低时,胶接强度高。另外,聚合物的平均分子量相同而分子量分布不同时,其胶接强度也不同。低聚物含量较高时,胶接接头破坏呈内聚破坏;聚合物含量高时,胶接接头破坏呈界面破坏。
1.3.3.7 胶黏剂的固化
胶黏剂在固化或者硬化过程的物理化学性质的变化,对胶接强度和胶接破坏产生很大的影响,因为胶黏剂的固化或者硬化是决定胶接制品质量的一个重要方面。从胶黏剂的固化方式可将其分成硬化和固化两种。硬化是物理过程,是指胶黏剂通过干燥、结晶等物理过程而变硬的现象。固化是化学过程,是指胶黏剂通过化学反应(聚合、缩聚等)提高强度等性能的过程。
(1)溶液胶黏剂 溶液胶黏剂是指可溶解于适当的溶剂的胶黏剂。其固化是通过润湿被胶接材料表面之后将溶剂挥发掉,从而产生一定的胶接力。溶剂胶黏剂的硬化是随着溶剂的挥发,溶液的浓度不断增大,最后达到一定强度。因此溶剂胶黏剂的硬化速度决定溶剂的挥发速度。一些难以挥发的溶剂需要很长的固化时间,相反,如果溶剂挥发的速度太快,胶黏剂的黏度增加速度也过快,这样不利于润湿被胶接材料的表面,胶接强度下降。因此在合成溶液胶黏剂时要根据其适用环境和胶接强度要求选择合适的溶剂。
(2)乳液胶黏剂 乳液胶黏剂也是采用硬化的方式进行胶接,主要是通过乳液中的水分逐渐渗到被胶接的材料中或挥发掉,使乳液的浓度不断增大,最后在表面张力的作用下,使乳液的胶体颗粒发生凝聚而变硬,从而达到胶接效果。环境温度对乳液的凝聚影响较大,当环境温度足够高时,乳液凝聚形成连续的胶膜,当环境温度低于最低成膜温度时,就形成白色不连续的胶膜,胶接强度较低。因此使用乳液胶黏剂时,要注意其使用温度不能低于自身的最低成膜温度。
(3)热熔胶黏剂 热熔胶黏剂一般为热塑性聚合物胶黏剂,是通过加热使其熔融而获得流动性,从而润湿被胶接材料的表面,冷却而发生硬化,达到胶接效果。在配置热熔胶黏剂时,必须解决好胶黏剂的强度和熔融体黏度的关系。聚合物的胶黏剂必须有足够高的分子量才能具有一定强度和韧性,但熔融体的黏度也是随着分子量的增加而增大,提高温度可以降低熔融体的黏度,但温度过高又会引起聚合物的降解而影响强度。因此,为了提高热熔胶的流动性和对被胶接材料的黏附作用,必须加入各种辅助成分。热熔胶包括很多组分,其中最重要的是黏料(使两种被胶接材料结合在一起时起主要作用的组分)、蜡类、增黏剂、填料和抗氧化剂。
(4)热固性胶黏剂 热固性胶黏剂是具有三维网状体型结构的聚合物。获得三维网状结构的胶黏剂有两种方法:一是把线型结构的聚合物通过加入固化剂或者其他助剂进行交联起来。例如,橡胶的硫化、环氧树脂的固化剂以及不饱和聚酯的引发剂等。二是由多官能团的原料或者以缩聚或者聚合等方式形成三位交联结构的树脂。例如,脲醛树脂、酚醛树脂、聚氨酯胶黏剂等。在一些热固性胶黏剂的固化过程中,这两类交联反应可能同时存在,例如,脲醛树脂、酚醛树脂等。
1.3.3.8 胶层厚度
要想获得良好的胶接强度,胶接层的厚度在不产生缺胶的条件下,应尽可能地薄且均匀。为防止缺胶,胶黏剂的用量要足够,以便能够填充被胶接材料表面的孔隙,并填平凹凸不平的表面,形成连续的胶膜,形成有效的胶接强度。一般希望胶接层的厚度在20~50μm。其理由为:①薄胶层变形需要的力比厚胶层大,胶接层越薄,使凝聚力降低,缺陷进入的概率减小,减少了胶接层中的应力集中点;②在胶接层中产生的内应力小,而且能使其易于向被胶接材料分散,耐老化性也提高,胶层越厚,由膨胀差引起的界面内应力与热应力越大;③随着胶层厚度的增加,流变或蠕变的概率变大;④坚硬的胶黏剂,胶接界面在弯曲应力的作用下,薄胶层的断裂强度比厚胶层的高;⑤胶层越厚,气泡及其他缺陷的数量增加,早期破坏的概率增加。
1.3.3.9 其他影响因素
获得良好的胶接强度除上述阐述的重要影响因素外,还与被胶接材料的特性、胶黏剂的特性、胶接工艺的相关因素有关。例如,如被胶接材料为木材,则与木材的密度、树种、含水率、纤维方向、抽提物有关;胶黏剂的特性还有胶黏剂的黏度、pH值、渗透性;胶接工艺的影响有调胶工艺、适用期、施胶量、陈化与陈化时间、加压与加压时间以及固化温度与时间。