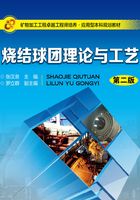
1.3 烧结球团发展趋势
21世纪之前,我国各个钢铁集团大都还没有形成节能减排的意识,烧结球团技术发展主要用在提高企业的生产总量上,对于能源消耗基本没有过高的重视。进入21世纪以来,我国钢铁企业迎来了百年难得的发展机遇,在这种大环境下几乎所有的企业都开足马力加大钢铁的生产量,这种情况一直持续到2008年才暂告一段落。由于我国现已探明的大部分铁矿石储量已被开发利用,而且我国的铁矿石97.5%为贫杂矿(平均含铁量仅为32.7%)。同时,我国长期计划经济所造成的炼铁原料准备结构错位,使球团及细粉精矿生产技术落后于世界先进水平。因此,随着“精料方针”的贯彻,高炉配料需要各钢厂不同程度地进口球团矿,而国内新型烧结矿开发及球团矿生产又需要大量地进口高品位粉精矿。2010年全球球团矿产量3.881亿吨,创历史新高。
2012年,中国成为全球最大的球团矿生产国,产量增至2.0亿吨以上。2015年,我国球团矿产量为12800万吨,烧结矿与球团矿总体比例为89∶11。
1.3.1 含铁品位不断提高
2010年我国烧结工序平均能耗为52.65kg标煤/t,达到钢铁行业(烧结)清洁生产标准三级要求,较2009年下降了2.3kg标煤/t,取得较大进步。烧结矿转鼓指数达到78.77%,符合钢铁行业(烧结)清洁生产标准三级要求,为高炉生产顺行提供了有力支持。烧结工序固体耗较2009年仅下降1kg/t。含铁品位与2009年相比稍有降低,这与2010年铁矿石价格和供应关系较大。未来烧结工序仍需在提高含铁品位上下工夫,力争全面达到清洁生产三级标准要求。与2009年相比,烧结工序日历作业率下降3.21%,在烧结操作工艺方面仍须进一步改进提升,全面达到清洁生产要求。
1.3.2 设备大型化
“十一五”期间,我国钢铁工业适应了国民经济的快速发展,满足了工业化、城镇化等对钢材的旺盛需求,在装备大型化、节能减排、技术创新、综合竞争力增强等方面均有较大进展。“十二五”是我国钢铁工业实现科学发展、加快转变发展方式的攻坚阶段,调整钢铁工业结构,是加快新型工业化进程的重要任务。其中,装备大型化是国家政策要求的方向。
“十二五”期间,我国部分企业依据自身生产实际。新增烧结总面积达到4242m2,新形成烧结矿产能约4325万吨;新增链箅机-回转窑、坚炉10余条(座),产能约1730万吨。对于新建和拟建的烧结球团装备,大型化仍将是主要趋势。另外,在“十二五”期间,为贯彻落实国家相关政策要求,钢铁工业在总量控制的基础上,淘汰落后装备仍是工作重点,一大批落后的烧结机、竖炉被逐渐淘汰,我国烧结、球团装备水平得到进一步提升。
2009年我国重点大中型钢铁企业烧结机总量为491台,烧结机总面积为67731m2,平均单机面积138m2,总生产能力72669万吨,平均单机生产能力148万吨。
2009年我国烧结生产具有以下几个比较突出的特点:一是烧结机装备技术水平取得长足进步,130m2及以上烧结机占烧结机总量的38%,产能上则占到68%。大型烧结机无论是数量还是生产能力上都已逐渐占据主导地位。二是淘汰落后烧结装备工作取得一定成效;由于对节能环保工作的日益重视,钢铁企业小型烧结机各方面的劣势日益突出。在整个钢铁行业淘汰落后装备的大背景下,烧结落后装备淘汰工作取得了一定进展。三是烧结装备在生产、运行、维护等方面均取得显著成效。钢铁企业的烧结生产日历作业率、台时产量、从业人员实物劳产率等基本指标都维持在较高水平。
据统计,2010年新投产烧结总面积约为3575m2,总产能约为3555万吨。2010年我国新投产的烧结机从数量上与2009年相比呈下降趋势。究其原因,主要是受国际金融危机和整个钢铁行业宏观形势的影响。但是从装备水平上来看,2010年新投产的烧结机全部符合《钢铁产业发展政策》的相关要求:烧结机使用面积均大于180m2,平均烧结面积275m2,平均单机生产能力273万吨,其中360m2及以上大型烧结机4台,最大烧结机为450m2。到2016年,单机最大烧结面积达到660 m2(太钢不锈钢股份有限公司),这说明我国烧结机大型化工作正在持续、整体推进。
2009年我国球团装备中,竖炉生产能力为8700万吨,带式焙烧机生产能力为740万吨,链箅机-回转窑生产能力为10200万吨,球团矿总生产能力为19640万吨。无论是从数量还是产能上,竖炉、链箅机-回转窑都是我国球团工业的主力生产工艺。在装备数量上,竖炉约占全国球团装备的一半以上;在装备产能上,链箅机-回转窑工艺所占比重最高,达到了51.9%,明显超过竖炉产能,新建项目大多采用链箅机-回转窑球团生产工艺。单机能力在240万吨及以上的链箅机-回转窑生产线发展迅速,逐步成为球团矿的主力。除此之外,2009年带式焙烧机生产球团矿工艺在我国也取得了较大发展。鞍钢、包钢、首钢曹妃甸带式焙烧机的投产,为我国球团工业的多元化发展奠定了基础。
1.3.3 大力发展球团矿
球团与烧结相比,虽然在投资和生产成本上略有增加,但从节能、低碳、废气减排等方面获得的综合效果是非常显著的。据统计,2010年我国新投产的球团装备能力约为570万吨。与2009年相比,新投产的球团装备数量下降较为明显,这与整个钢铁行业的宏观形势密不可分。许多钢铁企业使用的球团矿来自于独立的球团生产企业,并未包括到此次统计之列,而这部分产能所占比重较大。2010年工信部发布《部分工业行业淘汰落后生产工艺装备和产品指导目录》,将8m2以下球团竖炉纳入淘汰范畴,对实现球团工业的健康、快速发展起到积极的促进作用。
跨入21世纪以来,我国钢铁工业进入快速发展的轨道,作为高炉炼铁的一种主要含铁炉料,球团矿生产的发展速度超过了高炉炼铁年增长的速度。据统计,从2001年到2011年,我国生铁年产量由1.5554亿吨增长到6.29695亿吨,11年间年均增长27.71%;而球团矿年产量由1784万吨增长到2.041亿吨,年平均增长速度达到103.28%,球团矿占炉料结构的比例已接近20%。
2001~2013年重点钢铁企业高炉原燃料质量指标见表1-1。2001年以来球团质量、原料消耗、能耗水平取得较大进步。我国链箅机-回转窑球团矿的含铁品位2005~2006年曾上升到高于64.5%的水平,但随着矿价的急剧上涨,2011年又下降到低于63.5%;竖炉球团一直处在62%~63%的水平。近几年,链箅机-回转窑球团矿SiO2含量接近6%,竖炉球团SiO2含量高于6.2%。链箅机-回转窑球团矿的转鼓指数达到95%,竖炉球团矿为91%~92%。近几年,首钢和鞍钢链箅机-回转窑球团矿的含铁品位保持在65.5%以上,接近巴西进口球团矿的水平;武钢程潮链箅机-回转窑球团矿成品球的SiO2含量达到3.75%的优良水平。邯钢球团厂成品球的转鼓指数已达到97%的水平。
表1-1 2001~2013年重点钢铁企业高炉原料质量指标

钢铁生产节省原材料,是资源循环与实现可持续发展的一项重要举措。吨球精矿粉消耗回转窑球团已基本稳定在1000kg以内,竖炉球团也下降到接近1000kg的水平。回转窑球团的吨球膨润土用量已下降到2011年的19.53kg,竖炉球团也下降到2011年的21.04kg。国外球团生产膨润土的用量仅为4~8kg/t球,因此我国球团生产膨润土用量还有一个较大的改善空间。首钢和鞍钢弓矿球团生产的膨润土用量近几年下降到了10~11kg/t球,已接近国外的先进水平。
我国回转窑球团工序能耗已下降到2011年的27.42kg标煤/t球,竖炉球团的工序能耗也下降到2011年的31.76kg标煤/t球。
球团对优化炉料结构意义重大。《2006~2020年中国钢铁工业科学与技术发展指南》提出:“中国高炉炉料中球团比约12%,从当前优化炉料结构发展趋势看,中国应大力发展球团生产,并全面提高球团生产水平。”而球团技术的发展目标是“实现装备大型化,形成以不小于200万吨年产量的链箅机-回转窑为主体的球团生产工艺与装备,加快淘汰小竖炉球团工艺装备”。
发展球团生产对改善高炉技术经济指标有重要意义。球团矿已成为我国高炉炼铁与高碱度烧结矿搭配的一种主要炉料。25%~30%球团矿的配入可提高入炉矿品位1.5%以上,同时可降低1.5%的渣量,总体可降低焦比4%,提高产量5.5%。因此,球团矿生产对改善高炉技术经济指标起着重要的作用。
发展球团矿生产有利于高炉炼铁的节能减排。球团矿与烧结矿相比,工序能耗仅为后者的43%,可见发展球团矿生产对节能减排、改善环境有着明显的优越性。国外球团矿的含铁品位普遍高于65%,SiO2含量低于3%。我国链箅机-回转窑球团的含铁品位已达到63.5%的水平,SiO2含量低于6%,比烧结矿的品位高出5个百分点,渣量普遍低40%,燃料比降低13%以上。这说明,发展球团矿对高炉炼铁的节能减排具有重大意义,若球团矿的品位和SiO2含量达到或接近国际水平,所起的作用会进一步增强。球团矿作为高炉炼铁的搭配炉料,对高炉炼铁节能减排的作用(每提高1.5%的品位,降低15%的渣量)明显。此外,今后的球团矿将是氧化镁质的酸性球团矿,还会发展一定数量的熔剂性球团矿,这两类球团矿的发展及其冶金性能的改善将对高炉炼铁的节能减排发挥更大的作用。
我国球团矿生产已经获得了高速发展,但仍存在一些问题要认真对待。
问题一:焙烧球团矿的设备工艺发展方向。到目前为止,我国已经年产超过2亿吨球团矿。竖炉球团工艺目前有大小不同200多座设备在生产,占产量的比例接近40%,但因质量和环保等问题,圆形土竖炉、小于8m2的矩形竖炉在不久的将来会被淘汰,10~12m2(含)以上矩形竖炉在一定的时期内还会存在。今后大中型链箅机-回转窑和带式焙烧机将成为我国球团矿生产的主要工艺设备,建设年产200万吨以上,具有贮存仓、烘干窑、强力混合机、高压辊磨机、大型造球机等设备的装备配置将成应当成为发展的主流。
问题二:球团矿生产的资源配置。磁铁精矿是我国球团生产的主要资源,但已严重短缺。解决球团生产资源短缺的问题,应采取多方面的措施:抓好精矿资源的结构调整,逐步做到细精矿用于球团生产,不再用于烧结生产;短缺部分可采用外购赤铁矿粉生产,对于赤铁矿粉用于球团生产的效率和能耗问题,应开展专项研究,取得成功后推广应用。
广东粤裕丰公司采用适当配比赤铁精粉取得球团生产成功的例子:自筹建2×120万吨球团生产线起,进行了系统的赤铁矿粉球团生产的研究,针对赤铁矿粉成球难,采用高压辊磨,改变赤铁矿粉的外部形貌、增加比表面积等手段,证明赤铁精粉用于球团生产是可行的。
问题三:提高设备配置质量,有效降低球团生产能耗。我国链箅机-回转窑的最低能耗尚比世界先进水平高一倍以上,这与用于球团生产的工艺设备的制作精度和保温材料的质量相关。我国须强化高温设备密封技术和保温技术的研究和推广,通过对标挖潜缩小与世界先进水平的差距。
问题四:回转窑结圈。回转窑结圈是普遍存在的一个问题,不同程度影响着生产,对链箅机-回转窑工艺的生产率和能耗都有很大的损失。结圈的原因主要是粉末和局部高温,归根结底是链箅机-回转窑工艺亟待完善工艺技术和检测手段,使生产的各个环节实现数字控制,解决回转窑结圈的问题。
问题五:提高造球水平,全方位改进球团矿质量。我国球团生产十几年来发展速度快,质量提高却不大,与国外球团矿质量相比,含铁品位低,SiO2含量高,膨润土配加比例大,粒度粗(8~16mm粒级低于85%),表面粗糙,酸性球团MgO含量低,冶金性能差。
全方位改进我国球团矿的质量,应着重解决以下问题:一是现行的铁矿球团冶金行业标准亟待修订,现行标准粒径(10~16mm≥80%)太大,含铁品位和SiO2无具体范围指标要求,不符合节能减排的操作方针;二是提高造球水平,球团生产技术首先要造好球,做到粒度均匀,表面光滑无裂缝;三是膨润土配加量高于20kg/t球,比国外先进指标4~8kg/t球高出一倍以上,应采取原料预处理和有机粘结剂或复合粘结剂的方案,大幅度降低膨润土配加量,达到低于10kg/t球;四是提倡大力发展MgO质酸性球团矿和熔剂性球团矿,改善球团矿的冶金性能,为高炉降低燃料比创造条件;五是继续贯彻精料方针,提倡生产高品位(TFe≥65%)、低硅(SiO2≤4%)和高镁(MgO≥1.5%)的优质球团矿。