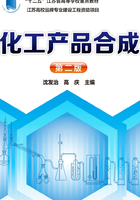
3.3 工作过程指导
3.3.1 制订小试合成方案要领
小李等一行来到了主要的实习岗位——车间小试实验室。完成岗位安全教育后,花工跟小李他们一起讨论氯甲基丁烯的合成方案。
花工拿出了一份当初小试组试制氯代异戊烯的文献方案。
在50mL三口反应瓶中放入磁子,插上温度计和冷凝管,反应瓶置于磁力搅拌的水浴装置中,称取适量氯化亚铜和助剂,转入反应瓶,用注射器转移5mL异戊二烯转入反应瓶,密封。反应液温度为10℃时开始通干燥的HCl,用气相色谱跟踪反应,控制异戊二烯在反应液中含量以确定反应终点,达到反应终点后停止通HCl并用惰性气体置换,撤去水浴,加入少量蒸馏水进行异构化反应,在室温下继续搅拌一段时间,反应结束后经过滤去除氯化亚铜催化剂即得到成品。
花工:“请大家讨论一下,以此文献方案为参考,如何制订小试合成方案?”
小李:“文献方案相对详尽,但有些细节尚不清楚。其一,氯化反应时反应釜内压力是否常压?其二,过程中反应温度控制不详。”
小赵:“助剂没有说明。”
小周:“资料上说气液反应一般可以将气体物料加压以提高浓度,这里可以加压吗?”
花工:“大家看得很仔细。氯化反应时反应釜压力为常压即可,不可以加压,这是因为加压时氯化氢的浓度将显著提高,会造成二氯产物显著提高。这里提几点建议,以便对大家制订小试方案时参考。”
3.3.2 单元反应体系构建和后处理纯化建议
3.3.2.1 氯化反应体系的构建和监控
(1)反应体系构建要点
①生产中一般不用助剂,催化剂直接加入到异戊二烯中,直接将氯化氢气体通入异戊二烯中即可,为让氯化氢与反应液更好接触,通气时可用分布管进行分散。
②如果反应物料较多,通气引起的分散效果不佳时还需用搅拌器搅拌提升氯化氢分散效果。
③虽异戊二烯能溶解氯化氢,但气体易逸出,故反应装置还需要配置尾气吸收装置。
(2)反应控制策略 为防止二氯化产物形成,故反应时应控制好氯化氢的通气速度,为防止异戊二烯聚合,反应要控制在较低的温度。
(3)反应终点的控制 反应过程中应用气相色谱跟踪反应,及时测定异戊二烯的残留量,控制在残留3%左右即到反应终点。
3.3.2.2 氯化反应后处理分离方法
反应达终点后,立即通入N2将残余氯化氢带出,然后过滤出催化剂,常压蒸出未反应的异戊二烯及副反应生成的低沸物,然后减压蒸馏收集79℃/40kPa馏分即为产品。减压蒸馏装置及操作参见附录。
3.3.2.3 产物的纯化
经减压蒸馏后产品已经足够纯。
3.3.3 绘制试验流程图
小试试验流程如图3-1。

图3-1 小试试验流程图
3.3.4 小试试验装置
小试试验需要在压力下进行,则必须配套专门的耐压装置。本项目需要用低压反应釜,反应装置可参考如图3-2。

图3-2 氯甲基丁烯的合成装置流程
1—氯化氢钢瓶;2—流量计;3—干燥塔;4—反应釜;5—磁环冷却塔;6—气液分离器;7—吸收塔
通过氯化氢钢瓶产生氯化氢气体,经过流量计严格控制流量后经干燥器输入反应器。反应器配有进料管、出料管、排气管、夹套、温度计插管及搅拌器等。反应尾气由排气管引出,通过冷却塔、气液分离器、吸收塔吸收后达标排放。反应器夹套中通入热媒进行加温操作,通入冷媒进行冷却操作。反应完毕后,料液由出料管排出。
3.3.5 小试合成工艺的评估
参考情境1评估的方法。
3.3.6 产物的检测和鉴定
1-氯-3-甲基-2-丁烯的检测可依据QB/YN CMB254—2008进行。
物性检测数据:常温折射率(n25)1.4470,沸点110℃。
企业可根据标准品的气相色谱进行定量检测。1-氯-3-甲基-2-丁烯红外标准谱如图3-3(来源:中科院上海有机化学研究所)。

图3-3 1-氯-3-甲基-2-丁烯的红外标准谱
更精确的鉴定还需进行质谱、核磁共振图谱(氢谱和碳谱)的鉴定,特别是在新物质的制备与解析过程中,有兴趣的同学可以参考相关的专业资料。
3.3.7 技能考核要点
参照情境1的考核方式,按下列方案技能考核:
在装有测温、搅拌的1L四口瓶中,加入含量为36%~38%的浓盐酸150mL(1.8mol),加入CuCl催化剂9g,并进行激烈搅拌使其溶解,将母液冷却到3℃以下,滴加入异戊二烯130g(1.9mol),GC跟踪分析,维持20℃,再继续搅拌0.5h,当异戊二烯质量分数达到4.2%左右,用5%Na2CO3中和至中性,分出有机层,饱和氯化钠溶液洗涤1~2次,干燥,减压蒸馏,收集79℃/40 kPa产物。
技能考核要点可参考情境1或情境2技能考核表自行设计。