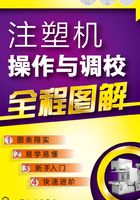
二、全液压式合模机构
1.全液压式合模机构的分类
全液压式合模机构可以分为直动式、充液式和两板式,其说明见表1-21。
表1-21 全液压式合模机构的分类


2.全液压式合模机构的应用
为达到塑料制品高精度的要求,塑料制品的注射成型越来越多地采用精密注塑成型机,对合模机构的要求也越来越高。
①精密注射多用于成型薄壁深腔制品,因此注射压力非常高,一般精密注射压力可达200MPa以上。这对合模机构的刚性和锁模力提出了较高的要求。但刚性和锁模力并不是越高越好,主要要求锁模力具有稳定性和重复性。精密注射对开合模精度的要求也很高。一般开模精度≤0.03mm,合模精度≤0.01mm,这些主要指开合模终点的位置精度。精密注射对模板的平行度也有非常高的要求,锁模力最大时≤0.005mm,锁模力为0时≤0.03mm。
②低压护模及锁模力的精确控制。用于精密成型的模具非常昂贵,因此合模装置必须减小对模具的损害程度。锁模力的大小影响着模具的变形程度,即影响着制品的精度。
③合模机构的工作效率要高,提高开合模的速度,减少开合模的时间,提高生产率同时也要降低能耗。
全液压式两板式合模机构以其自身的优越性能在精密注射成型中得到了非常好的应用。目前的精密注射成型机的合模机构主要有两种类型:一种是两板直压式;另一种是由伺服电动机驱动的电动式合模机构,这类机型主要是由日本厂家生产。目前,两板直压式的全液压式合模机构主要由欧洲厂家生产,如德国的Demag、Arburg、Battenfeld、Krauss-Mallei等公司所生产的两板机代表着当今两板机的最高水平。
如图1-46所示为Demag公司Titan系列两板机的合模机构。这种合模机构的工作过程如下:液压油首先进入到斜对称布置的两个快模液压缸内,实现快速合模;模具合上后,液压油进入到了定模板上的抱闸锁内驱动,位于定模板四个对角上的抱闸对准槽口合紧,然后高压液压油进入到位于动模板四个对角上的锁紧液压缸内对锁紧活塞施加高压,从而实现高压锁模;开模时先卸载高压油,然后液压油进入到移模液压缸内实现快速开模,实现整个开合模动作。这种类型的合模机构分别独立实现合模过程和锁模过程,解决了力和速度之间的矛盾,同时也有效地降低了能耗。这种结构非常紧凑,减小了整个机构的占地面积。Titan系列合模机构有着非常大的拉杆间隙和开合模行程,非常适合于成型深腔制品。Titan系列合模机构最大的特点就是锁模非常简单。目前,这类结构主要应用于大型注塑机上。

图1-46 Demag公司Titan系列注塑机合模机构
如图1-47所示为德国Arburg(阿博格)公司Allrounder C系列注塑机的合模机构。这种合模机构非常精确且稳定。其工作过程如下:液压油首先进入到位于后部支架上的两个并列的快速移模液压缸,实现机构的快速合模并实现护模功能;接着由位于后支架中部的锁紧液压缸对锁模活塞施加高压油实现锁紧;开模过程中首先将锁模液压缸内高压油卸压,两个快速移模液压缸实现快速开模,完成移模机构的工作过程。这种合模系统也同样解决了力和速度之间的问题,精度高、效率高。除此之外,Allrounder C合模机构还有一些独特的优点:当具备适当的液压配备时,可以进行压塑;锁模力变化有利于排气;具有快速和节能的差动活塞。

图1-47 德国Arburg公司Allrounder C系列注塑机合模机构
如图1-48所示为德国Krauss-Maffei公司MX系列注塑机的合模机构。这种合模机构的工作原理与Demag公司Titan系列相似。开合模的动作和锁模动作都是分开实现的。具体的工作过程如下:液压油从B口进入到快速移模液压缸内实现快速合模,当模具合紧时,机械锁紧系统C锁住拉杆,紧接着通过D进入高压油实现锁紧。其优点基本上和Demag公司Titan系列相近,但是MX系列的锁模液压缸面积大,受力更加均衡而且定位精准。

图1-48 德国Krauss-Maffei公司MX系列注塑机的合模机构
20世纪80年代末广东顺德泓利机器有限公司开发的四缸差动注塑机是世界上第一台外循环直压型两板机的雏形。其后,他们在此基础上开发出了全液压四缸直锁二板式注塑机。该机采用了独特的合模机构和液压系统,实现了锁模力和注射力的自适应和模具定位的自适应,使产品具有节能、精密可靠、运行平稳等诸多优点。在国内的精密注塑机发展史上具有非常重要的意义。目前,这种合模机构已经被应用到新开发的光盘注塑机上。
泓利公司的全液压四缸直锁二板式注塑机除了具有两板式液压机的优点之外,还具有两个独特的优点:锁模力与注射压力的自适应及模具位置的自适应。
泓利的四缸直锁二板式注塑机的锁模力,在注射成型过程中是可以变化的。根据注射压力的闭环反馈,在成型过程中,锁模力保持为注射压力的1.5倍;当注射结束后,锁模力随之下降至系统压力;在冷却过程,锁模力变为某一较低压力。适时减少锁模力可减少制品内应力,更重要的是使锁模系统以及模具不再长时间承受高压负荷,疲劳破坏减少。
如图1-49所示为传统肘杆式合模机构与四缸直压式合模机构的锁模力在注射成型过程中随注射压力变化的情况。从图中可以看出,肘杆式合模机构的锁模力在锁模到开模的过程中保持不变,锁模系统一直处于高压状态;全液压式锁模机构的锁模力随着注射压力的变化而变化。当胀模力达到最大时,锁模力也达到最大,能防止出现胀模的现象,在整个过程中锁模力和胀模力同步变化,维持着平衡状态。由于模具承受高压的时间并不长,模具产生的弹性变形量较小,有利于提高制品精度。

图1-49 锁模力在充模过程中的变化
所谓模具的自适应,就是指锁模系统在高压锁模时模具定位。在高压锁模时,如果模具不平行,如图1-50所示,就可能出现间隙β,这时靠近间隙一边的两个液压缸会继续补油,动模板会产生很小摆动并使安装在动模板上的模具也有很小的摆动,以使模具的分型面完全闭合。在继续补油升压后,合模机构才能产生锁模力。

图1-50 模具自适应
对模具实现完全封闭以防出现溢料等现象,这对精密制品来说非常重要。导致模具位置需要自适应主要有模具和模板两方面的因素。精密制品模具的精确度较高,造成需要自适应的主要原因在于模板本身的不平行,以及肘杆长短不一或销轴磨损等造成的模板不平行。对于肘杆式合模机构,这种模板或模具造成的不平行,会使肘杆及模具的受力不平衡,严重时会导致后模板及十字头等的摆动,并导致四条拉杆等受力不均而拉断,而且这种间隙必然导致制品产生飞边。