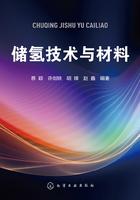
1.4 氢气的制备与纯化
1.4.1 氢气的制备
自然界中不存在纯氢,它只能从其他化学物质中分解、分离得到。由于存在资源分布不均的现象,制氢规模与特点呈现多元化格局。到目前为止.在氢能的开发和制氢技术领域有三个方向,分别为化石燃料转化制氢技术、用水制氢技术和生物质制氢技术,制氢所需的原材料一般为烃类和水。
工业用氢的制备方法主要是化石燃料的热分解,但是,这些技术严重依赖化石燃料的资源并且还排放二氧化碳。近年来也发展了从化石燃料产氢而不释放二氧化碳的方法,但相对来说制氢成本较高,还处于发展阶段。以水为原料的制氢技术,可以形成水分解制氢、氢燃烧生成水的循环过程。由于氢大量存在于水中,因此,从水中制氢的技术成熟并能达到实用后,以氢为主要能源结构支柱便成为可能。
生物技术制氢,与传统的热化学和电化学制氢技术相比,具有低能耗、少污染等优势,已经成为未来制氢技术发展的重要方向。目前,氢主要用作化工原料而并非能源,要发挥出氢对各种一次能源有效利用的重要作用,必须在大规模高效制氢方面获得突破。
(1)化石燃料转化制氢
制氢历史很长,方法也有多种,其中以天然气、石油、煤为原料制取氢气是较为普遍的方法。典型化石燃料制氢工艺如图1-1所示。

图1-1 典型化石燃料制氢工艺
在一次矿物能源中,氢的含量如表1-2所示,目前全世界制氢的年产量约为5×107t,并以每年6%~7%的速度增加,其中煤、石油和天然气等一次矿物能源的制氢约占96%。根据一次矿物能源存在形式的不同,化石燃料转化制氢又可分为:煤制氢、气体燃料制氢、液体化石燃料制氢。下面就上述三种制氢方法作一一介绍。
表1-2 一次矿物能源中的含氢量

①煤制氢 煤制氢技术主要以煤气化制氢为主,此技术发展已经有200年的历史,在我国也有近百年的历史,可分为直接制氢和间接制氢。煤的直接制氢是指煤经过干馏、气化后直接制取氢气。煤的间接制氢过程,是指将煤首先转化为甲醇,再由甲醇重整制氢。煤制氢的核心是煤气化技术。所谓煤气化是指煤与气化剂在一定的温度、压力等条件下发生化学反应而转化为气体产物(煤气)的过程,包括气化、除尘、脱硫、水煤气变换反应、酸性气体脱除等,气化剂为水蒸气或氧气(空气),气体产物中含有氢气等组分,其含量随不同气化方法而异。
气化反应如下:
C(s)+H2O(g)CO(g)+H2(g) (1-10)
CO(g)+H2O(g)CO2(g)+H2(g) (1-11)
煤气化是一个吸热反应,反应所需的热量由氧气与碳的氧化反应提供。煤气化工艺有很多种,如Koppers-Totzek法、Texco法、Lurqi法、气流床法、流化床法等。近年来还研发了煤超临界水气化法、煤热解制氢工艺等多种煤气化的新工艺。如,美国启动了前景21(Vision21)制氢的计划,实质上,它是一个改进的超临界水催化气化方法,其基本思路是:燃料通过氧吹气化,然后变换并分离CO和氢,以使燃煤发电效率达到60%、天然气发电效率达到75%、煤制氢效率达到75%的目标。从该系统的物料循环来看,此过程可以认为是近零排放的煤制氢系统。
②气体燃料制氢 天然气和煤层气是主要的气体形态化石燃料。气体燃料制氢主要是指天然气制氢。天然气制氢是目前化石燃料制氢工艺中最为经济与合理的方法。天然气含有多组分,其主要成分是甲烷。在甲烷制氢反应中,甲烷分子惰性很强,反应条件十分苛刻,需要首先活化甲烷分子。温度低于700K时,生成合成气(H2+CO混合气),在高于1100K的温度下,才能得到高产率的氢气。天然气制氢的主要方法有天然气水蒸气重整制氢、天然气部分氧化重整制氢、天然气催化裂解制氢等。
天然气水蒸气重整制氢是目前工业上天然气制氢应用最广泛的方法。传统的天然气水蒸气重整过程包括原料的预处理、转化(重整)、水汽变换(置换)、脱碳除杂,如图1-2所示。

图1-2 天然气水蒸气重整制氢工艺流程
天然气中原料含有几十微升/升的H2S和少量的有机硫(20×10-6~30×10-6),因此,原料首先需要预处理,为了脱除有机硫,采用铁锰系转化吸收型脱硫催化剂,并在原料气中加入1%~5%的氢,在约400℃高温下发生下述反应:
RSH+H2H2S+RH (1-12)
H2S+MnOMnS+H2O (1-13)
经铁锰系脱硫剂初步转化吸收后,剩余的硫化氢再在氧化锌催化剂作用下发生下述脱硫反应而被吸收:
H2S+ZnOZnS+H2O (1-14)
C2H5SH+ZnOZnS+C2H4+H2O (1-15)
转化反应是以水蒸气为氧化剂,在镍催化剂的作用下,将甲烷进行水蒸气转化生成富氢混合气,其反应式为:
CH4+H2OCO+3H2 (1-16)
该反应是强吸热反应,温度超过850℃时,反应所需要的热量由天然气的燃烧供给。降低压力有利于甲烷转化率的提高,但为了满足纯氢产品的压力要求以及变压吸附提纯,一般控制压力为1.5MPa。
变换过程是将来自水蒸气转化单元的混合气中的CO和H2O反应生成CO2和H2,其反应式如下:
CO+H2OCO2+H2 (1-17)
按照变换温度,变换工艺可分为高温变换(350~400℃)、低温变换(300~350℃)以及可降低原料消耗的高温串低温变换。在天然气水蒸气重整制氢中,所发生的转化反应和变换反应均在转化炉中完成。
水蒸气重整制氢反应是强吸热反应,制氢过程的能耗很高,仅燃料成本就占生产成本的52%~68%,而且反应需要在耐高温不锈钢制作的反应器内进行。此外,水蒸气重整反应速率慢,该过程单位体积的制氢能力较低,通常需要建造大规模装置,投资较高。
天然气部分氧化重整是合成气制氢的重要方法之一。自20世纪90年代有文献报道天然气部分氧化制氢以来就引起了广泛关注,天然气部分氧化制氢的主要反应为:
CH4+O2
CO+2H2+35.5kJ (1-18)
在天然气部分氧化过程中,为了防止析碳,常在反应体系中加入一定量的水蒸气,这是因为该反应体系除上述主反应外,还有以下反应:
CH4+H2OCO+3H2-206kJ (1-19)
CH4+CO22CO+2H2-247kJ (1-20)
CO+H2OCO2+H2+41kJ (1-21)
甲烷部分氧化法是一个轻放热反应,由于反应速率比水蒸气重整反应快1~2个数量级,与水蒸气重整制氢方法相比,变强吸热为温和放热,具有低能耗的优点,还可以采用廉价的耐火材料堆砌反应器,可显著降低初投资。但该工艺具有反应条件苛刻和不易控制的缺点,另外需要大量纯氧,需要增加昂贵的空分装置,增加了制氢成本。经过20多年,该工艺取得较大发展,但是还有一些关键技术问题,如催化剂床层的局部过热、催化材料的反应稳定性以及操作体系爆炸潜在危险安全性等没有解决,因此迄今为止,并未有该技术工业化的文献报道。这是由于以下几方面的因素限制了部分氧化工艺的发展。
天然气催化热裂解制氢是将天然气和空气按理论完全燃烧比例混合,同时进入炉内燃烧,使温度逐渐上升到1300℃时停止供给空气,只供给天然气,使之在高温下进行热解,生成氢气和炭黑。其反应式为:
CH42H2+C (1-22)
天然气裂解吸收热量使炉温降至1000~1200℃时,再通入空气使原料气完全燃烧升高温度后,再次停止供给空气进行热解,生成氢气和炭黑,如此往复间歇进行。该过程由于不产生二氧化碳而被认为是连接化石燃料和可再生能源之间的过渡工艺过程。目前在国内外均开展了大量的研究工作。该过程欲获得大规模工业化应用,其关键问题是,所产生的碳能够具有特定的重要用途和广阔的市场前景。否则,若大量氢所副产的碳不能得到很好应用,必将限制其规模的扩大。
③液体化石燃料制氢 液体化石燃料如甲醇、轻质油和重油也是制氢的重要原料,常用的工艺有甲醇裂解-变压吸附制氢、甲醇重整制氢、轻质油水蒸气转化制氢、重油部分氧化制氢等。
a.甲醇裂解-变压吸附制氢 甲醇与水蒸气在一定的温度、压力和催化剂存在的条件下,同时发生催化裂解反应与一氧化碳变换反应,生成氢气、二氧化碳及少量的一氧化碳,同时由于副反应的作用会产生少量的甲烷、二甲醚等副产物。甲醇加水裂解反应是一个多组分、多反应的气固催化复杂反应系统。主要反应为:
CH3OH+H2OCO2+3H2 (1-23)
CH3OHCO+2H2 (1-24)
CO+H2OCO2+H2 (1-25)
总反应为:
CH3OH+H2OCO2+3H2 (1-26)
反应后的气体产物经过换热、冷凝、吸附分离后,冷凝吸收液循环使用,未冷凝的裂解气体再经过进一步处理,脱去残余甲醇与杂质后送到氢气提纯工序。甲醇裂解气体的主要成分是H2和CO2,其他杂质成分是CH4、CO和微量的CH3OH,利用变压吸附技术分离除去甲醇裂解气体中的杂质组分,获得纯氢气。
甲醇裂解-变压吸附制氢技术具有工艺简单、技术成熟、初投资小、建设周期短、制氢成本低等优点,是受制氢厂家欢迎的制氢工艺。
b.甲醇重整制氢 甲醇在空气、水和催化剂存在的条件下,温度处于250~330℃时进行自热重整,甲醇水蒸气重整理论上能够获得的氢气浓度为75%。甲醇重整的典型催化剂是Cu-ZnO-Al2O3,这类催化剂也在不断更新使其活性更高。这类催化剂的缺点是其活性对氧化环境比较敏感,在实际运行中很难保证催化剂的活性,使该工艺受到商业化推广应用的限制,寻找可替代催化剂的研究正在进行。
c.轻质油水蒸气转化制氢 轻质油水蒸气转化制氢是在催化剂存在的情况下,温度达到800~820℃时进行如下主要反应:
CnH2n+2+nH2OnCO+(2n+1)H2 (1-27)
CO+H2OCO2+H2 (1-28)
用该工艺制氢的体积分数可达74%。生产成本主要取决于轻质油的价格。我国轻质油价格高,该工艺的应用在我国受到制氢成本高的限制。
d.重油部分氧化制氢 重油包括常压渣油、减压渣油及石油深度加工后的燃料油。部分重油燃烧提供氧化反应所需的热量并保持反应系统维持在一定的温度,重油部分氧化制氢在一定的压力下进行,可以采用催化剂,也可以不采用催化剂,这取决于所选原料与工艺。催化部分氧化通常是以甲烷和石油脑为主的低碳烃为原料,而非催化部分氧化则以重油为原料,反应温度在1150~1315℃。重油部分氧化包括烃类与氧气、水蒸气反应生成氢气和碳氧化物,典型的部分氧化反应如下:
2CnHm+nO22nCO+mH2 (1-29)
2CnHm+2nH2O2nCO+(m+2n)H2 (1-30)
CO+H2OCO2+H2 (1-31)
重油的碳氢比很高,因此重油部分氧化制氢获得的氢气主要来自水蒸气和一氧化碳,其中蒸汽制取的氢气占69%。与天然气水蒸气转化制氢相比,重油部分氧化制氢需要配备空分设备来制备纯氧,这不仅使重油部分氧化制氢的系统复杂化,而且还增加了制氢的成本。
化石燃料制氢技术成熟、效率高、成本低,用矿物燃料制氢的一个主要问题是在制氢时会产生大量的CO2,从而对环境产生污染。此外,矿物燃料制氢将来还存在矿物燃料短缺的问题。随着氢气需求量的增大及化石燃料储量的降低,应寻找新的技术路线,发展新的制氢技术。原则上要求制氢技术满足大型化、高效率、低成本,从而使氢气的应用发展有基本的支持。
(2)用水制氢
①水电解制氢 水电解制备氢气是一种成熟的制氢技术,早在18世纪初就已开发,到目前为止已有近100年的生产历史。其工作原理是:借助直流电的作用,将H2O分解成新物质的过程。在电解水时,由于纯水的电离度很小,导电能力低,属于典型的弱电解质,所以需要加入酸性或碱性电解质,以增加溶液的导电能力,使水能够顺利地电解成为氢气和氧气。可见,水电解制氢是氢气与氧气燃烧生成水的逆过程,因此只要提供一定形式的能量,则可使水分解。电解池是电解制氢过程的主要装置,其原理如图1-3所示。其化学反应式如下。

图1-3 水电解制氢过程示意
1—阴极;2—隔膜;3—碱性溶液;4—阳极
a.碱性条件
阳极反应:
2e+2H2OH2↑+2OH- (1-32)
阴极反应:
4OH-O2↑+2H2O+4e (1-33)
总反应式:
2H2O2H2↑+O2↑ (1-34)
b.酸性条件
阳极反应:
2H2O-4eO2↑+4H+ (1-35)
阴极反应:
4H++4e2H2↑ (1-36)
反应遵循法拉第定律,气体产量与电流和通电时间成正比。决定电解能耗技术指标的电解电压和决定制氢量的电流密度是电解池的两个重要指标,电解池的工作温度和压力对上述电解电压和电流密度两个参数有明显影响。由于池内存在诸如气泡、电阻、过电位等因素引起的损失,使得工业电解池的实际操作电压高于理论电压(1.23V),多在1.65~2.20V之间。
水电解制氢的工艺过程简单,无污染,其效率一般为50%~70%,消耗电量大,每立方米氢气的电耗为4.5~5.5kW·h,电费占整个水电解制氢生产费用的80%左右,使得工业化的电解水制氢成本仍然很高,其与其他制氢技术相比不具有优势,很难与其他制氢技术相竞争,利用常规能源生产的电能来大规模电解水制氢显然不合算,目前,采用该方法制氢仅占总制氢量的4%左右,仅用于高纯度、产量小的制氢场合。
电解水制氢的发展方向是与风能、太阳能、地热能以及潮汐能等洁净能源相互配合从而降低成本。这些洁净能源由于其能量大小与时间的关系具有波动性,所以在发电时,系统给出的电能是间歇性的。通常是不可以直接进入电网的,必须进行调节后方可入网。成本最低、最方便的储能方法是将其电解制氢、储氢、输运氢,然后利用氢能发电入网或转化为其他能量形式。
②高温热解水制氢 水的热解反应方程为:
H2O(g)H2(g)+1/2O2(g)ΔH=241.8235.5kJ/mol (1-37)
可以看出,该反应为吸热反应,常温下平衡转化率极小,一般在2500℃时才有少量水分解,只有将水加热到3000℃以上时,反应才有实际应用的可能。高温热解水制氢的难点是高温下的热源问题、材料问题等,突出的技术难题是高温和高压。
③热化学制氢 水的热化学制氢是指在水系统中,在不同的温度下,经历一系列不同但又相互关联的化学反应,最终分解为氢气和氧气的过程。在这个过程中,仅消耗水和一定的热量,参与制氢过程的添加元素或化合物均不消耗,整个反应过程构成一个封闭的循环系统。与水的直接高温热解制氢相比较,热化学制氢的每一步反应温度均在800~1000℃,相对于3000℃而言,该反应在较低的温度下进行,能源匹配、设备装置的耐温要求和投资成本等问题也相对容易解决。热化学制氢的其他显著优点还有能耗低(相对于水电解和直接高温热解水成本低)、可大规模工业生产(相对于再生能源)、可实现工业化(反应温和)、有可能直接利用核反应堆的热能、省去发电步骤、效率高等。
热化学循环制氢过程按反应涉及的物料可分为氧化物体系、卤化物体系、含硫体系和杂化体系等。
a.氧化物体系是用金属氧化物(MeO)作为氧化还原体系的两步循环。它是利用较活泼的金属与其氧化物之间的互相转换或者不同价态的金属氧化物之间进行氧化还原反应而制备氢气的过程。在这个过程中高价氧化物在高温下分解成低价氧化物放出氧气,低价氧化物被水蒸气氧化成高价氧化物放出氢气,这两步反应的焓变相反。其反应方程为:
氢生成:
3MeO+H2OMe3O4+H2 (1-38)
氧生成:
2Me3O46MeO+O2 (1-39)
其中金属(Me)可分别为Mn、Fe、Co。
b.在卤化物体系中,如金属-卤化物体系,反应可表示为:
氢气生成:
6MeX+8H2O2Me3O4+6HX+5H2 (1-40)
其中,金属Me可以为Mn和Fe,卤化物X可以为Cl、Br和I。
卤素生成:
Me3O4+8HX3MeX2+4H2O+X2 (1-41)
氧生成:
MeO+X2MeX2+1/2O2 (1-42)
水解:
MeX2+H2OMeO+2HX (1-43)
卤化物体系中最著名的循环为日本东京大学发明的UT3循环,(University of Tokyo-3),其中金属选用Ca,卤素选用Br,循环由以下四步组成。
水分解成HBr:气-固反应,反应温度730℃,吸热。
CaBr2+H2OCaO+2HBr (1-44)
O2生成:气-固反应,反应温度550℃。
CaO+Br2CaBr2+1/2O2 (1-45)
Br2生成:
Fe2O3+8HBr3FeBr2+4H2O+Br2 (1-46)
H2生成:
3FeBr2+4H2OFe3O4+6HBr+H2 (1-47)
UT3循环具有以下特点:预期热效率高(35%~40%),如果同时发电,总效率可提高10%;循环中两步关键反应均为气-固反应,简化了产物与反应物的分离;整个过程所采用的材料都廉价易得,无须采用贵金属;最高温度为1033K,可与高温气冷反应堆相耦合。
c.含硫体系中最著名的循环是由美国GA公司在20世纪70年代发明的碘-硫循环(iodine-sulfur cycle,IS),又被称为GA流程,循环中的反应为:
本生(Bunsen)反应:
SO2+I2+2H2O2HI+H2SO4 (1-48)
硫酸分解反应:
H2SO4H2O+SO2+1/2O2 (1-49)
氢碘酸分解反应:
2HII2+H2 (1-50)
该循环具有以下特点:低于1000℃就能分解水产生氢气;过程可连续操作且闭路循环;只需加入水,其他物料循环使用,无流出物;循环中的反应可以实现连续运行;预期效率高,可以达到约52%,制氢和发电的总效率可达60%。
d.化学杂化过程是水裂解的热化学过程与电解反应的联合过程。杂化过程为低温电解反应提供了可能性,而引入电解反应则可使流程简化。选择杂化过程的重要准则包括电解步骤最小的电解电压、可实现性以及效率。杂化体系包括硫酸-溴杂化过程、硫酸杂化过程、烃杂化过程和金属-卤化物杂化过程等。以甲烷-甲醇制氢为例说明烃杂化过程,其反应为:
CH4(g)+H2O(g)CO(g)+3H2(g) (1-51)
CO(g)+2H2(g)CH3OH(g) (1-52)
2CH3OH(g)2CH4(g)+O2(g) (1-53)
该循环在压力为4~5MPa的高温下进行,反应步骤不多,原料便宜,所采用的化工工艺也都比较熟悉,效率可达33%~40%,在所有体系中是最高的,并经过循环实验验证效率在目前具有应用价值。目前,热化学制氢目前还很不成熟,还难以达到商业化实用的技术水平。
④等离子体化学制氢 等离子体化学制氢是在离子化较弱和不平衡的等离子系统中进行的。原料水以蒸汽的形态进入保持高频放电反应器。水分子的外层失去电子,处于电离状态。通过电场电弧将水加热至5000℃,水被分解成H、H2、O、O2、OH-和HO2,其中H与H2的含量达到50%。为了使等离子体中氢组分含量稳定,必须对等离子进行淬火,使氢不再与氧结合。等离子分解水制氢的方法也适用于硫化氢制氢,可以结合防止污染进行氢的生产。这种制氢方法设备容积小,产氢效率高,能量转换效率可达80%,但是等离子体制氢过程能耗很高,因而制氢的成本也高。
⑤太阳能制氢 在自然界中,氢已和氧结合成水,必须用热分解或电分解的方法把氢从水中分离出来。如果用煤、石油和天然气等燃烧所产生的热或所转换成的电分解水制氢,那显然是划不来的。如果用太阳能作为获取氢气的一次能源,则能大大降低制氢的成本,使氢能具有广阔的应用前景。利用太阳能制氢主要有以下几种方法:太阳能光解水制氢、太阳能光化学制氢、太阳能电解水制氢、太阳能热化学制氢、太阳能热水解制氢、光合作用制氢及太阳能光电化学制氢等。
自1972年,日本科学家首次报道了TiO2单晶电极光催化降解水产生氢气的现象,光解水制氢就成为太阳能制氢的研究热点。
太阳能光解水制氢反应可由下式来描述:
H2OH2+1/2O2 (1-54)
电解电压为:
' (1-55)
式中,(=-237kJ/mol)为摩尔生成自由能;F为法拉第常数,代入公式计算得水的电解电压为1.229eV。理论上,能用作光解水的催化剂的禁带宽度必须大于水的电解电压(1.229eV),且价带和导带的位置要分别同O2/H2O和H2/H2O的电极电位相适宜。
太阳能光解水的效率主要与光电转换效率和水分解为H2和O2过程中的电化学效率有关。在自然条件下,水对于可见光至紫外线是透明的,不能直接吸收光能。因此,必须在水中加入能吸收光能并有效地传给水分子且能使水发生光解的物质——光催化剂。如果能进一步降低半导体的禁带宽度或将多种半导体光催化剂复合使用,则可以提高光解水的效率。
目前,太阳能光解水制氢在实验室已取得突破性进展,制成的太阳能光化学电池,在阳光照射下可以产生氢气,但仍有电极材料、电池结构、电催化、光化学、热化学反应、提高效率及光腐蚀稳定性等一系列技术和理论上的难题需要解决,才能使其实用化。
太阳能光化学制氢是利用射入光子的能量使水的分子通过分解或把水化合物的分子进行分解获得氢的方法。实验证明:光线中的紫光或蓝光更具有这种作用,红光和黄光较差。在太阳能光谱中,紫外光是最理想的。在进行光化学制氢时,将水直接分解成氧和氢非常困难,必须加入光解物和催化剂帮助水吸收更多的光能。目前光化学制氢的主要光解物是乙醇。乙醇是透明的,对光几乎不能直接吸收,加入光敏剂后,乙醇吸收大量的光才会分解。在二苯(甲)酮等光敏剂的存在下,阳光可使乙醇分解成氢气和乙醛。
太阳能电解水制氢的方法与电解水制氢类似。第一步是将太阳能转换成电能,第二步是将电能转化成氢,构成所谓的太阳能光伏制氢系统。光电解水制氢的效率,主要取决于半导体阳极能级高度的大小,能级高度越小,电子越容易跳出空穴,效率就越高。由于太阳能-氢的转换效率较低,在经济上太阳能电解水制氢至今仍难以与传统电解水制氢竞争。预计不久的将来,人们就能够把用太阳能直接电解水的方法,推广到大规模生产上来。
太阳能热化学制氢是率先实现工业化大生产的比较成熟的太阳能制氢技术之一,具有生产量大、成本较低等特点。目前比较具体的方案有:太阳能硫氧循环制氢、太阳能硫溴循环制氢和太阳能高温水蒸气制氢。其中太阳能高温水蒸气制氢需要消耗巨大的常规能源,并可能造成环境污染。因此,科学家们设想,用太阳能来制备高温水蒸气,从而降低制氢成本。
太阳能热解水制氢是把水或蒸汽加热到3000K以上,分解水得到氢和氧的方法。虽然该方法分解效率高,不需催化剂,但太阳能聚焦费用太昂贵。若采用高反射高聚焦的实验性太阳炉,可以实现3000K左右的高温,从而能使水分解,得到氧和氢。如果在水中加入催化剂,分解温度可以降低到900~1200K,并且催化剂可再生后循环使用,目前这种方法的制氢效率已达50%。如果将此方法与太阳能热化学循环结合起来形成“混合循环”,则可以制造高效、实用的太阳能产氢装置。
太阳能光电化学分解水制氢是电池的电极在太阳光的照射下,吸收太阳能,将光能转化为电能并能够维持恒定的电流,将水解离而获取氢气的过程。其原理是:在阳极和阴极组成的光电化学池中,当光照射到半导体电极表面时,受光激发产生电子-空穴对,在电解质存在下,阳极吸光后在半导体带上产生的电子通过外电路流向阴极,水中的质子从阴极上接受电子产生氢气。现在最常用的电极材料是TiO2,其禁带宽度为3eV。因此,要使水分解必须施加一定的外加电压。如果有光子的能量介入,即借助于光子的能量,外加电压在小于1.23V时就能实现水的分解。
高效率制氢的基本途径是利用太阳能。如果能用太阳能来制氢,那就等于把无穷无尽的、分散的太阳能转变成了高度集中的干净能源了,其意义十分重大。利用太阳能制氢有重大的现实意义,但这却是一个十分困难的研究课题,有大量的理论问题和工程技术问题要解决,然而世界各国都十分重视,投入了不少的人力、财力、物力,并且也已取得了多方面的进展。因此,以后以太阳能制得的氢能,将成为人类普遍使用的一种优质、干净的燃料。
(3)生物质制氢
生物质制氢是利用微生物在常温、常压下进行酶催化反应制氢气的方法。该技术在20世纪60年代中期就已提出,20世纪90年代受到重视,德、日、美等一些发达国家制定了生物制氢的发展计划。生物质制氢可分为光合微生物制氢和厌氧发酵有机物制氢两类。
光合微生物制氢是指微生物(细菌或藻类)通过光合作用将底物分解产生氢气的方法。在藻类光合制氢中,首先是微藻通过光合作用分解水,产生质子和电子并释放氧气,然后藻类通过特有的产氢酶系的电子还原质子释放氢气。在微生物光照产氢的过程中,水的分解才能保证氢的来源,产氢的同时也产生氧气。在有氧的环境下,固氮酶和可逆产氢酶的活性都受到抑制,产氢能力下降甚至停止。因此,利用光合细菌制氢,提高光能转化效率是未来研究的一个重要方向。
厌氧发酵有机物制氢是在厌氧条件下,通过厌氧微生物(细菌)利用多种底物在氮化酶或氢化酶的作用下将其分解制取氢气的过程。这些微生物又被称为化学转化细菌,包括大肠埃希氏杆菌、拜式梭状芽孢杆菌、产气肠杆菌、丁酸梭状芽孢杆菌、褐球固氮菌等。底物包括甲酸、丙酮酸、CO和各种短链脂肪酸等有机物、硫化物、淀粉纤维素等糖类,这些底物广泛存在于工、农业生产的污水和废弃物之中。厌氧发酵细菌生物制氢的产率一般较低,为提高氢气的产率除选育优良的耐氧菌种外,还必须开发先进的培养技术才能够使厌氧发酵有机物制氢实现大规模生产。
生物质制氢技术具有清洁、节能和不消耗矿物质资源等突出优点。作为一种可再生资源,生物体又能进行自我复制、繁殖,还可以通过光合作用进行物质和能量的转换,这种转换系统可在常温、常压下通过酶的催化作用而获得氢气。但生物制氢技术目前存在的问题也较多,比如如何筛选产氢率相对高的菌株、设计合理的产氢工艺来提高产氢效率、高效制氢过程的开发与产氢反应器的放大、发酵细菌产氢的稳定性和连续性、混合细菌发酵产氢过程中彼此之间的抑制、发酵末端产物对细菌的反馈抑制等还需要进一步研究。
从能源的长远战略角度看,以水为原料,利用太阳光的能量制取氢气是获取一次能源的最理想的方法之一。许多国家正投入大量财力和人力对生物质制氢技术进行研发,以期早日实现生物制氢技术向商业化生产的转变,也将带来显著的经济效益、环境效益和社会效益。
(4)其他制氢方法
随着氢气作为21世纪的理想清洁能源受到世界各国的普遍重视,许多国家也开始重视制备氢气的方法和工艺的研究,使新的制氢工艺和方法不断涌现出来。除上述介绍的多种制氢方法和工艺以外,近年来还出现了氨裂解制氢、新型氧化材料制氢、硫化氢分解制氢、核能制氢、放射性催化剂制氢等制氢技术。但这些技术都还处于研究阶段,距商业化应用还有较大的距离。
1.4.2 氢气的纯化
由于自然界没有纯净的氢,氢总是以其化合物如水、烃类等形式存在,因此,在制备氢时就不可避免地带有杂质。氢气中带有杂质,就带来了安全隐患,容易发生爆炸,这就要求对氢气原料进行纯化。氢的纯化是指利用物理或化学的方法,除去氢气中杂质的方法总称,也就是将氢中包含的杂质“过滤”出去。随着半导体工业、精细化工和光电产业的发展,半导体生产工艺需要使用99.999%以上的高纯氢。但是,目前工业上各种制氢方法所得到的氢气纯度不高,很难满足高纯度氢气应用的要求,需要对制氢过程中获得的氢气进一步进行纯化处理。氢气的工业纯化方法主要有低温吸附法、低温冷凝法、变压吸附法、膜分离法等。
(1)低温吸附法
低温吸附法就是使待纯化的氢气冷却到液氮温度以下,利用吸附剂对氢气进行选择性吸附以制备含氢量超过99.9999%的超纯氢气。吸附剂通常选用活性炭、分子筛、硅胶等,选择哪种吸附剂,要视氢气中的杂质组分和含量而定。在工业生产中,常常使用两台吸附器,其中一台运行,另一台处于再生阶段。周期定时切换,从而实现连续生产作业。
(2)低温冷凝法
低温冷凝法又称为低温分离法,是基于氢与其他气体沸点差异大的原理,在某一操作温度下,使除氢以外所有高沸点组分冷凝为液体的分离方法。该方法适合氢含量30%~80%(体积浓度)范围内的原料气回收氢,产氢纯度为90%~98%。与低温吸附法相比,低温分离法具有产量大、纯度低和纯化成本低的特点。
(3)变压吸附法
变压吸附技术是近30多年发展起来的一项新型气体分离与净化技术,由于其投资少,运行费用低,产品纯度高,操作简单、灵活,环境污染小等优点,这项技术被广泛应用于石油、化工、冶金、轻工等行业。所谓变压吸附(PSA)是以特定的吸附剂内部表面对气体分子的物理吸附为基础,利用吸附剂在相同压力下易吸附高沸点组分、不易吸附低沸点组分和高压下吸附量增加、低压下吸附量减少的特性,将原料气在一定压力下通过某一特定的吸附剂,相对于氢的高沸点杂质组分被选择性吸附,低沸点的氢气不易被吸附而穿过吸附剂,达到氢和杂质组分的分离而使氢气纯化的目的。
变压吸附气体分离工艺之所以实现,是由于吸附剂在这种物理吸附中所具有的两个基本性质:一是对不同组分的吸附能力不同;二是吸附质在吸附剂上的吸附容量随吸附质的分压上升而增加,随吸附温度的上升而下降。利用吸附剂的第一个性质,可实现对某些组分的优先吸附而使其他组分得以提纯。利用吸附剂的第二个性质,可实现吸附剂在高压低温下吸附,而在高温低压下解吸再生,从而构成吸附剂的吸附与再生循环,达到连续分离气体的目的。需要指出的是,变压吸附法要求待纯化的氢气中的氢含量要在25%以上。
(4)膜分离法
膜分离技术以选择性透过膜为介质,在电位差、压力差、浓度差等推动力下,有选择地透过膜,从而达到分离提纯的目的。可分为无机膜分离和有机高分子有机膜分离。在无机膜分离法中,无机膜在高温下分离气体非常有效。与高分子有机膜相比,无机膜对气体的选择性及在高温下的热膨胀性、强度、抗弯强度、破裂拉伸强度等方面都有明显的优势。在无机膜分离技术中最常用的是钯合金膜扩散法,即所谓的钯膜扩散法。在一定温度下,氢分子在钯膜一侧离解成氢原子,溶于钯并扩散到另一侧,然后结合成分子。经一级分离可得到99.99%~99.9999%纯度的氢。钯合金无机膜存在渗透率不高、力学性能差、价格昂贵、使用寿命短等缺点,该方法只适于较小规模且对氢气纯度要求很高的场合使用。因此需要开发具有高氢选择性、高氢渗透性、高稳定性的廉价复合无机膜。
(5)其他方法
①金属氢化物法 金属氢化物法是利用储氢合金对氢的选择性生成金属氢化物,氢中的其他杂质浓缩于氢化物之外,随着废气排出,金属氢化物分离放出氢气,从而使氢气纯化。
②催化脱氧法 催化脱氧法是用钯或铂作催化剂,使氧和氢发生反应生成水,再用分子筛干燥脱水。这种方法特别适用于电解氢的脱氧纯化,可制得纯度为99.999%的高纯氢。