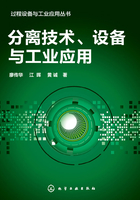
3.5 精馏操作的节能优化技术
分离过程是过程工业中耗能很大的操作,所有分离过程都需要以热和(或)功的形式加入能量,其能量费用与设备折旧费相比,前者占首要地位。由于世界能源日趋紧张,过程节能问题显得越来越重要,因此,确定完成一个所需的理论最小能量,寻求接近此极限的实际过程或减少使用昂贵能量的实际过程是很有意义的。
3.5.1 精馏过程的热力学不可逆性
分离过程所需最小功是由原料和产物的组成、温度、压力所决定的。要提高热力学效率只能采取措施降低过程的净功消耗,使过程尽量接近可逆过程。精馏过程热力学不可逆性主要由以下原因引起:a.通过一定压力梯度的动量传递;b.通过一定温度梯度的热量传递或不同温度物流的直接混合;c.通过一定浓度梯度的质量传递或者不同化学位物流的直接混合。可见,如果降低流体流动过程产生的压力降,减少传热过程的温度差,减少传质过程的两相浓度与平衡浓度的差别,都将使精馏过程的净功消耗降低。
在精馏塔中上升蒸汽通过塔板产生压力降,塔板数较多时,压力降也较大。对板式塔而言,减低气速、降低每块塔板上的液层高度都可减小压力降。然而,降低气速意味着在同等生产能力下需增大塔径,即增加投资。降低塔板上的液层高度会使塔板效率降低。所以,必须根据各种影响因素选择合适的塔径和液层高度。此外,改变板式塔为高效填料塔也是提高生产能力、降低压力降的主要途径。例如,30×104t/a乙烯装置的脱甲烷塔由浮阀塔改成Intalox填料塔,压降由42kPa降至12kPa。负荷提高10%后塔的压降仅为12.3kPa。
在精馏过程中,再沸器和冷凝器分别以一定的温差加入和移走热量。若使传热温差减小,则传热面积需增大,而这又会使投资费用增大,因此,要选用高效换热器及改进操作方式,例如采用降膜式再沸器、热虹吸式再沸器或强制循环式换热器等。另外,如果冷凝器冷却水温度过低,净功消耗必定增加,故从冷凝器中释放热量的回收利用也是精馏过程降低净功消耗的一个重要方面。
进出每块塔板的气液相在组成与温度上的相互不平衡是使精馏过程热力学效率下降的重要因素。由下一块塔板上升的蒸汽与上一块塔板下降的液体相比较,温度要高些,易挥发组分的含量小于与下降液体成平衡时之数值。要降低净功消耗就必须减小各板传热和传质的推动力。这可以归结为应尽量使操作线与平衡线相接近。可用图3-18来讨论这个情况。

图3-18 提高双组分精馏过程的可逆性
图3-18(a)代表在大于最小回流比下操作的一般二元精馏。进入任一板上的液体与蒸汽间的传热推动力和传质推动力将因操作线向平衡线靠拢而减小。图3-18(b)代表最小回流比时的情况。此时,精馏段操作线和提馏段操作线都已经和平衡线相交。最小回流比下操作所需的净功当然小于较大回流比下的数值。但由图3-18(b)可以看出,即使在最小回流比下操作,除了在进料板附近处,其他各板仍有较大的传热和传质推动力。如果将操作线分成不同的几段,就可以减小这些板上的热力学不可逆性。
图3-18(c)是将精馏段操作线和提馏段操作线各分为两段时的情况。此时在精馏段用了两个不同的回流比,上一段的回流比小于下一段的回流比。这相当于在精馏段中间加了一个冷凝器,在提馏段中间加了一个再沸器。在加料板处的气液流率,图3-18(c)和图3-18(b)的情况是一样的,故图3-18(b)所示的塔顶冷凝器负荷必为图3-18(c)所示的即两个冷凝器负荷之总和。再沸器负荷的情况也类似。所以,图3-18(c)与图3-18(b)相比,其热力学效率得以增大并不是由于总热量消耗减少,而是由于所用热量的品质不同。中间再沸器所加入的热量,其温度低于塔底再沸器所加入热量的温度;由中间冷凝器引出的热量,其温度高于由塔顶冷凝器所引出热量的温度。
图3-18(d)是图3-18(c) 的进一步延伸,操作线与平衡线已完全重合,即所谓“可逆精馏”。要达到图3-18(d)这样的情况,就要有无限多个平衡级,无限多个中间再沸器和中间冷凝器。此时,精馏段的回流量是越往下越大,提馏段的蒸汽上升量是越往上越大,塔径应是两头大、中间小。当然,实际上不可能使用“可逆精馏”,它只代表一种极限情况。
3.5.2 多效精馏
采用双效或多效精馏是充分利用能级的一个办法。其原理如同多效蒸发,即采用压力依次降低的若干个精馏塔串联流程,前一精馏塔塔顶蒸汽用作后一精馏塔再沸器的加热介质。这样,除两端精馏塔外,中间精馏装置可不必从外界引入加热介质和冷却介质。多效精馏操作的基本方式如图3-19所示。不论采用哪种方式,其精馏操作所需的热量与单塔精馏相比较,都可以减少30%~40%。而塔压、液体及蒸汽流动组合方式的确定与分离物系的相对挥发度、进料中低沸点组分和高沸点组分的相对比例、进料状态以及热源蒸汽压力和冷却介质的温度等有关。

图3-19 多效精馏的基本方式
甲醇-水体系的逆流双效精馏法如图3-20所示。在该流程中,只向低压塔进料,把低压塔釜液作为高压塔的进料,高压塔釜排放废水。采用蒸汽和液体逆流方式的双效精馏工艺,根据物料衡算,低压塔塔釜约含50%甲醇,因此低压塔塔釜温度比纯水时低。所以,作为低压塔加热源的高压塔蒸汽温度就可以降低,高压塔可以在比较低的压力下操作。

图3-20 甲醇-水体系逆流双效精馏法
3.5.3 低温精馏的热源
对于组分沸点差较小的低温精馏系统,热泵流程是一种有效的提高热力学效率的手段。它的原理是使用膨胀阀和压缩机来改变冷凝(或沸腾)温度,将塔顶蒸汽绝热压缩后升温,重新作为再沸器的热源,把再沸器中的液体部分汽化。而压缩气体本身冷凝成液体,经节流阀后一部分作为塔顶产品抽出,另一部分作为塔顶回流液,使冷凝器中放出的热量用作再沸器中加热所需的热量。这样,除开工阶段外,可基本上不向再沸器提供另外的热源,节能效果十分显著。应用此法虽然要增加热泵系统的设备费,但一般两年内可用节能省下的费用收回增加的投资。当冷凝器和再沸器不相匹配时,可用辅助冷凝器和再沸器。常用的热泵流程有三种。
(1)用外部制冷剂的热泵
将外部制冷剂用于塔顶冷凝器和再沸器所构成的封闭循环中,冷凝器作为制冷剂的蒸发器,再沸器作为制冷剂的冷凝器。图3-21为该热泵循环用于分离丙烯-丙烷系统的流程。用丙烷作为外部制冷剂,使它在1.67℃下蒸发,并在43.33℃下冷凝,可使冷凝器和再沸器所需的热负荷完全匹配。因此不用冷却水和加热蒸汽,只耗电1173kW(假定制冷剂的压缩过程是等熵的)。

图3-21 用外部丙烷制冷剂的热泵循环低温精馏分离丙烯-丙烷的流程
(2)压缩塔顶蒸汽的热泵
当馏出物是一种好的制冷剂时,塔顶蒸汽被压缩,使它的冷凝温度(35℃)高于塔底产物沸点(16℃),冷凝放出的热量用于再沸器。离开再沸器的冷凝液通过一个膨胀阀,闪蒸到塔顶压力,以提供回流和馏出产品。过剩的蒸汽再循环进入压缩机。此方案常被称为蒸汽再压缩。图3-22给出此类热泵在丙烯-丙烷分离中的应用。由于压缩到1482kPa的塔顶蒸汽不足以提供再沸器所需的全部热量,所以标出了一个辅助的蒸汽加热再沸器。

图3-22 用塔顶蒸汽压缩热泵循环的低温精馏分离丙烯-丙烷的流程
(3)用再沸器液体闪蒸的热泵
当塔底产品是一种好的制冷剂时,塔釜液通过膨胀阀闪蒸到相应于馏出物饱和温度的压力。塔顶分凝器又起再沸器的双重作用,在分凝器中生成的蒸汽在进塔前被再压缩到塔底压力。图3-23为该热泵系统在丙烯-丙烷分离中的应用。将釜液闪蒸到496kPa压力,用它来除去冷凝器中所需的热量。在等熵压缩中,加入的额外热不足以弥补再沸器和冷凝器负荷上的差别,故需要一个辅助的蒸汽加热再沸器。

图3-23 用再沸器液体闪蒸热泵循环的低温精馏分离丙烯-丙烷的流程
以上三种丙烯-丙烷分离流程的热力学效率比较列于表3-5。分析表中数据可见,三种热泵系统的热力学效率均高于普通低温精馏,其中用再沸器液体闪蒸的热泵具有最高的热力学效率。
表3-5 低温下丙烯-丙烷分离的热力学效率

3.5.4 设置中间冷凝器和中间再沸器
在普通精馏塔中,热量从温度最高的再沸器加入,从温度最低的塔顶冷凝器移出。因此,净功消耗大,热力学效率很低。加热和冷却的费用也随釜温的升高和顶温的降低而升高。若采用中等温度下操作的中间再沸器和中间冷凝器,可以使操作向可逆精馏的方向趋近,减少净功消耗。同时可节省和回收较高品位的热能,特别适合于塔顶、塔釜有较大温差的情况。若中间冷凝器和中间再沸器之间加一个热泵,则可获得进一步的改进。图3-24表示出了上述两种情况的流程。

图3-24 使用中间冷凝器和中间再沸器
由Mah,Nicholas和Wodnik评价和开发的SRV精馏是产生二次回流和再沸的另一种方法。在图3-25所示的方案中,精馏段的操作压力高于提馏段,此压差可导致足够的温差,致使精馏段和提馏段的一对塔板之间能进行希望的热交换。沿全塔布置的换热元件能大大降低塔顶冷凝器和塔底再沸器的负荷。这样,液相回流量在精馏段中自上而下稳定地增加,而蒸汽流率在提馏段中自下而上稳定地增加。对于沸点相近的混合物的冷冻分离,SRV精馏可以减少公用费用,所以它很有吸引力。

图3-25 SRV精馏
降低精馏过程能耗的途径是多种多样的,无论采用哪一种措施,均能获得一定程度的节能效果,但最终评价的准则是经济效益。在大多数情况下,精馏过程采取节能措施可使操作费用减少,但需要的节能装置将使设备投资费用增加,而且往往使操作变得更复杂,并要求提高控制水平。因此降低精馏过程的能耗与相应的最大经济效益之间有一最佳节能点。应该说,最大限度节能不一定是最经济的,应寻求最优条件。实际生产中精馏过程是整个生产过程的一个组成部分,因此要对整个生产过程的节能状态进行分析,对精馏过程而言可能不是最佳点,但对全过程节能有利,因此,必须就整个过程加以权衡。