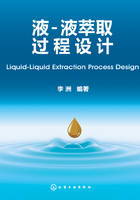
2.3 三萃取循环Purex萃取流程工艺和操作条件的确定
Purex流程的三循环萃取流程是早期建立的工艺流程,它更适用于辐照深度比较深的铀核燃料,它由第一萃取循环,即共去污循环,第二萃取循环——铀、钚分离循环和第三萃取循环——铀和钚并列的萃取净化循环组成。如图2-1所示,第一萃取循环由萃取串级HA柱(假设萃取设备采用萃取柱)和萃取串级HC柱组成,用于铀、钚共萃并去污分离裂变产物;第二萃取循环由铀、钚共萃并去污的1A柱,铀、钚分离的1B柱及反萃取铀的1C柱组成,主要用于铀、钚的分离和净化;第三萃取循环分别由2A钚萃取柱、2B钚反萃柱、2D铀萃取柱和2E铀反萃柱组成,分别用于钚、铀的进一步的净化去污和铀、钚的分离。在每个萃取循环的萃取部分均采用分馏萃取方式,其中HA柱、1A柱、2A柱和2D柱均为水相进料的分馏萃取过程,而1B为有机相进料的分馏萃取过程。反萃取部分采用多级逆流萃取方式。其萃取和反萃级数则根据串级计算确定。各萃取循环的工艺和操作条件的确定需综合考虑各影响因素而后确定,以期取得较佳的萃取和分离效果。
2.3.1 共去污萃取循环
如图2-1所示,铀、钚的共去污是在共去污萃取循环的HA柱内进行的,HA柱是Purex流程中的关键性的操作单元,确定铀、钚共去污的最优的工艺条件和操作条件尤为重要,但要做到这一点并非易事,因为各工艺条件对保证铀、钚的收率和提高去污效果往往是互相矛盾的。例如,提高铀饱和度有助于提高去污效果,但却不利于提高铀、钚的萃取收率。又如,对裂变元素的去除也存在矛盾的因素,锆、铌和钌的萃取行为往往相反,如高酸、高温有助于钌的去除,却不利于锆、铌的去除,反过来,低酸、低温有助于锆、铌的去除,却对钌的去除不利。在这些矛盾面前,确定萃取工艺条件时均需进行综合考虑。表2-5列出了几组不同工艺条件组合时裂变元素的净化结果。
表2-5 不同工艺条件组合时对裂变元素的净化结果[19]

在图2-1所示的萃取流程中采用了低酸进料、高酸洗涤的折中的工艺条件。在此萃取流程中进料的铀浓度高达1.8mol/L,可以判定其处理对象应是天然铀或低浓铀燃料元件,这时,考虑到料液中硝酸铀酰结晶温度的限制,硝酸浓度不宜过高。另外,对天然铀或低浓铀燃料来说,锆、铌在裂变元素中占较大比例,共去污的主要矛盾是锆、铌的去除。
采用低酸进料和低酸浓度的洗涤液有助于锆、铌的去除。进料温度定在50℃,采用45℃的有机溶剂则有助于改善有机相的物性和钌的去除。有机相中TBP浓度的选择主要应考虑体系的水力学性能、生产能力和临界安全三个方面,30%的TBP浓度是一个居中的选择。
流程中的流量为:HAF∶HAS∶HAX=75∶56.2∶355,则其在萃取段和洗涤段的流比分别为2.706和6.316,经与表2-2所列数据核查,在萃取段:nDPu(Ⅳ)=2.706×1.55=4.19>1,nDZr=2.706×0.02=0.054<1;在洗涤段(假设洗涤段的萃取分配系数与萃取段的相同):nDPu(Ⅳ)=6.316×1.55=9.79>1,nDZr=6.316×0.02=0.126<1,符合萃取和洗涤要求。另外,在此流比条件下,计算得到的铀饱和度=1.8/(2.706×1.06)=0.63=63%,属于正常的铀饱和度的范围。
共萃铀、钚后的有机相直接进入反萃柱,进行铀、钚的反萃取,反萃液为0.01mol/L的硝酸,流比(V∶L)为383∶488=1∶1.27。
经此萃取循环,铀、钚收率均达99.9%以上,总裂变元素的去污系数达103~104。
2.3.2 铀、钚分离萃取循环
从共去污萃取循环出来的铀、钚反萃液经浓缩和调料后即进入铀、钚分离循环的共去污柱(1A柱),此处的工艺条件和操作条件与共去污萃取循环的HA柱相同。其后,铀、钚萃取有机相即直接进入铀、钚分离柱(由1BX柱和1BS柱组成一分馏萃取串级),反萃剂(四价铀或氨基磺酸亚铁)从1BX柱顶加进,在此实现钚的还原反萃取,并转入水相,铀仍然留在有机相,实现二者的分离。为了提高铀、钚的分离效果,且进行铀的回收,可装设1BS柱进行铀的再萃取。采用适宜的温度和流比条件有利于铀、钚的有效分离。铀的反萃在其后的1C柱内进行,其操作条件与共去污循环的HC柱类同。
经此萃取循环,铀和钚的总γ净化系数均可达103~105,钚中去铀的分离系数可达105,铀中去钚的分离系数可达5×103~5×104,铀和钚的收率均可达99.9%以上。
2.3.3 钚净化萃取循环
此萃取循环的主要任务是进一步去除钚产品液中的铀与裂变元素,同时进行钚产品液的浓缩。与共去污循环相比,此萃取循环有两个特点,其一是料液的放射性强度已大大降低,主要矛盾已从共去污循环的净化去污转到首先要保证钚的收率,然后再兼顾产品的净化。其二是钚与铀的相对含量发生了显著改变,这时铀浓度对钚的萃取平衡的影响可以忽略,使钚的萃取分配系数有所提高。
从铀、钚分离循环来的钚溶液经NaNO2调价至Pu(Ⅳ),并调酸浓度后即进入钚净化萃取循环的2A柱。在此柱内采用了高酸进料、低酸洗涤的搭配。流比的选择需综合考虑钚的收率、去污系数和浓缩倍数等因素,采用了小流比:2AX∶2AF∶2AS=10.9∶37.5∶4.8,如此,在此萃取柱可将钚液浓缩(37.5+4.8)/10.9=3.88倍。在钚反萃柱内可采用低酸(0.01mol/L)反萃取,但低酸反萃存在钚反萃率低、钚中去铀的分离效果差等缺点,还是建议采用还原反萃的办法。在2B柱中通过调节两相流比(V∶L=10.9∶7.0)将钚液进一步浓缩了1.56倍。如此,通过钚净化萃取循环可将钚液浓缩6倍以上,但要注意,为确保临界安全,2BP中的钚浓度一般控制在7.8g/L以下。在此萃取循环中钚回收率为99.9%以上,钚中去铀的分离系数达400~1000,总γ的净化系数达1000~2000。
2.3.4 铀净化萃取循环
铀净化萃取循环的主要任务是进一步去除铀产品液中的微量钚及裂片元素。2DF料液的组成与1AF相似,其差别仅在于在2DF中只有极微量的钚和裂片元素。由于在2D柱中不需要控制钚的水解,为了更有效地去除锆、铌,采用了低酸(0.29mol/L)进料。另外在2D柱中采用了双重洗涤,2DIS用2.6mol/L的硝酸,2DS用蒸馏水,这样可使2DF进料点附近的酸浓度较高,而对钌的去除有利。在2DU出口附近的硝酸浓度很低,对锆、铌的去除及提高铀中去钚的分离系数有利。流比的选择使铀饱和度控制在68%左右。
2E萃取器的操作条件与1C萃取器类似。采用0.01mol/L硝酸作为反萃液,流比(V/L)取为373∶439=1∶1.177,铀反萃率达99.9%,总γ的净化系数为10~103,铀中去钚的分离系数为5~50。