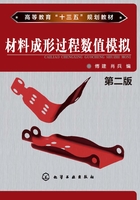
3.2 技术基础
3.2.1 铸件凝固过程的数值模拟
金属铸造成形中的凝固过程是指高温液态金属由液相向固相的转变过程。在这一过程中,高温液态金属所含热量必然会通过各种途径向铸型和周围环境传递,逐步冷却并凝固,最终形成铸件。其中,铸件/铸型系统的热量传递主要包括:铸液内部的热对流,铸件和铸型内部的热传导,铸液、铸件和铸型的热辐射,以及铸液/铸型、铸液/凝固层、铸件/铸型、铸型/环境等界面的热交换。实际上,自然界中的三类基本传热方式在金属铸造成形过程中均有所体现。
铸件凝固过程数值模拟的主要任务就是建立凝固过程的传热模型,然后在已知初边值条件下利用数值方法求解该传热模型,获取其温度场变化信息,并根据温度场的分布及其变化仿真铸件凝固过程,了解与温度场或温度梯度变化相关的物理现象和预测铸件成形质量,例如:冷却速度、凝固时间与凝固分数、液/固相变、晶粒形核与生长以及缩孔、缩松、冷隔、残余应力与应变、宏微观组织与性能等。
数值求解凝固过程温度场的常用方法包括:有限差分法、有限元法和边界元法。其中,前两种方法的基本原理已在第2章分别介绍,第三种方法(边界元法)将在第7章结合塑料注射成形冷却模拟介绍。考虑到有限差分法在处理诸如铸造温度场、流动场方面的简捷性与广泛性,本章只介绍利用有限差分法求解铸件凝固过程的温度场变化。
3.2.1.1 基本假设
①铸液充型时间极短,充型期间铸液和铸型内的温度变化可忽略不计;
②铸液充满模腔后瞬间开始凝固;
③不考虑凝固过程中的液/固相界面推移,即不考虑传质影响(该假设不适合厚大铸件);
④忽略铸液过冷,即凝固是从给定的液相线温度开始至固相线温度结束,金属液的凝固在平衡状态下完成;
⑤铸件/铸型系统传热主要受铸件、铸件凝固层、铸型以及铸件/铸型界面和铸件/铸型界面涂料层(如果有)的热传导控制。
3.2.1.2 热传导控制方程(Fourier方程)
(3-1)
式中 T——温度场;
t——时间;
kx,ky,kz——沿x、y、z方向的导热系数;
ρ,c——材料密度和比热容;
L——比潜热(单位质量液相转变成固相所释放的结晶潜热);
fs——凝固温度区间内的固相质量分数。
式(3-1)表明:基于能量守恒原理,微元体单位时间温度变化获得(或散失)的热量等于单位时间由x,y,z三个方向传入(或传出)微元体的热量加上微元体单位时间相变释放(或吸收)的热量。对于铸件/铸型系统中无相变材料(例如铸型)的导热而言,式(3-1)右边最后一项等于零。
在实际生产中,铸件/铸型系统的热传导控制分三种情况:
①铸件热导率远大于铸型热导率(例如砂型铸造),铸件中的温差相对于砂型温差而言可以忽略不计,铸件/铸型系统的热传导取决于砂型导热;
②铸件在厚涂料金属型中凝固,铸件和铸型的热导率相对于涂料而言很大,铸件/铸型系统的热传导取决于涂料导热;
③铸件在金属型中凝固,铸件与铸型紧密接触,铸件、铸型和铸件/铸型界面的热导率接近,铸件/铸型系统的热传导由铸件、铸型共同决定。
3.2.1.3 结晶潜热的处理
由于凝固金属的液相内能大于固相内能,因此,当铸件金属由液相转变为固相时,会发生内能的变化。这个内能变化以凝固(结晶)潜热的形式展现。潜热的处理与铸件材料的凝固特性有关,常用方法有:等效比热容法、热焓法和温度补偿法。
(1)等效比热容法
该方法认为:铸件凝固过程中的比热容由两部分组成,一是铸件材料的真实比热容,二是结晶潜热对相变过程比热容的贡献,即
cE=c+L0 (3-2)
式中 cE——等效(或当量)比热容;
c——真实比热容;
L0——结晶潜热对相变比热容的贡献。
现将式(3-1)的潜热项移到等号左边并化简,得:
或
(3-3)
显然:
(3-4)
由式(3-4)可知,当铸件材料一定时,其凝固过程所释放的结晶潜热与固相质量分数fs和实际凝固温度T有关。因此,等效比热容法的关键是确定凝固过程中fs与T之间的关系。通常,利用铸件合金的平衡相图可以较好地解决该问题。
图3-1是某二元合金相图的一部分,其中:C0、CS、CL分别为给定合金的原始成分(组元B的质量分数,下同)、温度为T时的固相成分和液相成分,Tf、TL、TS分别为组元A的熔点、合金C0开始结晶的液相线温度和结晶完毕的固相线温度。为了简化数学处理,假设相图中的液相线和固相线均为直线,因而在凝固区间的任何温度下,液固两相的浓度(成分)分配比为一常数,即:
(3-5)

图3-1 二元合金相图(局部)
针对图3-1应用杠杆定理,可计算获得凝固温度为T时,单位质量合金C0结晶出的固相质量分数
(3-6)
将式(3-5)代入式(3-6)得到液相成分CL与原始成分C0、已结晶固相质量分数fs和浓度分配比k之间的关系。
(3-7)
由于假设液相线为直线,因此有:
(3-8)
将式(3-7)代入式(3-8)并化简,得:
于是有:
(3-9)
(3-10)
如果合金凝固期间液、固两相的浓度分配比k不为常数或未知,则可借助下述方法处理∂fs/∂T:
先利用热分析法求出合金凝固开始温度TL和结束温度TS,然后假设如下:
①T与fs呈线性关系,即T=TL-(TL-TS)fs,于是
(3-11)
②T与fs呈二次关系,即,于是
(3-12)
根据应用情况,将∂fs/∂T代入式(3-4),即可获得二元合金凝固过程中的等效比热容cE。需要注意的是,合金凝固过程中的等效比热容选取与实际冷却温度T有关,一般
(3-13)
式中 cL,cS——液态和固态下的合金比热容;
c——真实比热容(可以理解为无结晶潜热的系统比热容)。
等效比热容法适合于处理凝固温度区间较宽合金的潜热问题。对于凝固温度区间较窄合金和共晶合金的潜热处理必须进行温度修正,否则便会产生显著误差。
(2)热焓法
热焓法是利用铸件凝固过程中的热焓随温度变化来处理结晶潜热。对于历经凝固的已知成分合金系统,其热焓H被定义为:
(3-14)
式(3-14)对温度求导:
(3-15)
将式(3-15)代入式(3-1)即得:
(3-16)
热焓法与等效比热容法类似,适用于有一定结晶温度范围的合金。
(3)温度回升法
对于纯金属或凝固温度区间很窄或共晶成分合金的结晶潜热处理,通常采用温度回升法。
就上述合金或纯金属而言,在整个凝固过程中,其温度基本上维持在凝固点附近。这是由于铸件凝固释放的结晶潜热补偿了其“显”热的散失,从而抵消了冷却传热造成的温度下降。假设在时间Δt内,从液相中结晶出质量分数为fs的固相释放热量
Q1=Lfs (3-17)
同一时间内,该固相散失热量
Q2=cfsΔT (3-18)
式中 ΔT——因热量散失导致的温度下降。
当Q1=Q2时,意味着释放的潜热完全弥补了冷却的散热,于是又使温度回升ΔT。最后由式(3-17)和式(3-18)可得:
L=ΔTc (3-19)
式(3-19)即是利用温度回升法导出的结晶潜热表达式。
3.2.1.4 铸件/铸型系统的其他传热方式
(1)对流传热
铸液与铸型内壁、铸液与已凝固铸件层、铸型外壁与周围空气以及铸液内部存在对流换热。对流换热的数理描述通常依据牛顿(Newton)冷却公式
qf=α(Tf-Tw) (3-20)
式中 qf——热流密度(单位面积界面上的对流传热量);
α——对流传热系数;
Tf——流体(例如铸液、空气等)温度;
Tw——固体(例如铸型、已凝固铸件层等)边界温度。
需要注意的是,式(3-20)并不涉及铸液(流体)内部的对流传热。由于处理对流传热比处理单纯热传导复杂,因此,在实际计算中常予以简化。
(2)辐射传热
铸件、铸型与周围空气之间的换热方式还包括辐射传热,特别是在静止空气中冷却且铸件或铸型温度相对较高时,铸件或铸型表面与大气之间的换热以辐射方式为主。辐射传热遵循斯忒藩-玻耳兹曼定律(Stefan-Boltzman)定理
(3-21)
式中 qr——单位面积界面上的辐射传热量;
E——铸件或铸型的表面黑度;
S——Stefan-Boltzman常数;
T,T∞——铸件或铸型的表面温度和环境(空气)温度。
3.2.1.5 热传导控制方程的差分格式
根据第2章介绍的有限差分原理,将式(3-1)中的各项改写成差分格式,例如
当 Δx=Δy=Δz(微元体边长相等)时,有
综合上述各式,得铸件/铸型系统热传导控制方程的差分格式(假设kx=ky=kz=λ)
(3-22)
式中 T——当前(即t)时刻温度;
T'——下一(即t+Δt)时刻温度;
Δt——时间步长。
3.2.1.6 温度场数值解稳定收敛的基本条件
将式(3-22)改写成数值迭代形式
(3-23)
式中 ——热扩散系数;
。
令[与微元i相邻的6个微元温度的平均值(见图3-2)],于是有
(3-24)
无相变时(例如铸型导热),式(3-24)转变成
(3-25)

图3-2 当前微元位于6个邻接微元中间
此时,微元i的温度变化ΔT取决于该微元当前温度T与相邻6个微元平均温度之差。差值
即为驱使微元i温度变化的动力,而微元i温度变化的终极目标是趋向周围6个相邻微元温度的平均值,即ΔT=0。作为实际过程数值模拟的迭代计算,必须真实地反映这一现象:任何时刻,任何单元都不能出现温度变化的反常。显然,如果式(3-25)中的时间步长Δt取值不当,就会造成迭代计算的温度值振荡。换句话说,Δt的取值必须保证微元温度的变化ΔT满足条件
(3-26)
将式(3-25)代入式(3-26),有
化简得到温度场数值解稳定收敛的基本条件
(3-27)
即:按式(3-27)选取时间步长,可保证式(3-25)在无相变前提下存在稳定收敛的数值解。对存在液、固相变的铸件导热,将3.2.1.3小节对结晶潜热处理的表达式代入式(3-24),然后再代入式(3-26),同样可推导出相应热传导控制方程的有限差分格式和稳定数值解的收敛条件。
3.2.1.7 初边值条件的设定
(1)初始条件
根据基本假设①和②,当t=0时,有
通常将铸件初始温度Tc定义为等于或略低于铸液浇注温度,铸型初始温度Tm定义为铸型预热温度或室温。若假设充型结束时,铸液与铸型完全接触,且其界面温度瞬间趋于一致(如图3-3所示),于是可用下式计算t=0时的界面温度T0
(3-28)

图3-3 界面初始温度
式中 bc,bm——铸件和铸型的储热系数,;
ac,am——铸件和铸型的热扩散系数。
(2)边界条件
计算铸件凝固过程温度场的边界条件参见第2章式(2-36)~式(2-38),其中最重要的边界条件是界面传热(换热)系数h。涉及铸造凝固传热的界面按物质分类通常有:铸件/铸型、铸件/空气、铸件/涂料、涂料/铸型、铸件/冷铁、冷铁/砂型、冒口/空气、铸型/空气以及铸型/大地等。应根据生产实际(如铸造方法、铸型类别、界面性质等)分别设置各界面的传热系数。此外,还需重视一些特殊边界的处理。例如:当铸件和铸型之间无涂料过渡时,应考虑界面间隙的辐射传热或(和)空气对流传热;同理,在金属型铸造或铸件明冒口顶部不加覆盖剂的场合,需适当考虑对流传热和辐射传热。又例如:当铸件/铸型系统的几何形状和边界条件之间存在某种对称关系时,为了节约计算工作量,往往只对铸件/铸型系统中的一部分区域进行求解,此时的对称边界类似绝热边界,即在对称边界上,求解热传导方程式(3-1)的第一、第二类边界条件应设置为。表3-1是金属铸造成形中常见界面传热系数的经验值,可作为一般数值计算参考。
表3-1 常见界面传热系数

应严格说来,界面传热系数是温度和界面性质的函数,如果条件允许,应尽可能选择(或通过物理实验获取)真实的界面传热系数。