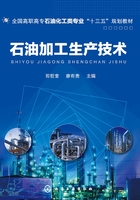
第四节 常减压蒸馏工艺主要操控点
在现场生产过程中,DCS系统会每间隔一两秒钟追踪现场装置的温度、压力、流量、液位等参数,主控制室主、副操岗位及时掌握参数动态,分析判断装置生产的变化趋势,并且及时做出调节,使这些工艺参数控制在工艺卡片允许的波动范围内,才能生产出合格的装置产品。
一、电脱盐罐操作温度
原油温度的高低对于电脱盐罐脱盐效率的影响较大,因此应避免脱盐罐温度大幅度波动,一般变化温度不应超过2℃/15min,脱盐的最佳温度通常为120~140℃。原油在电脱盐罐内为液相,温度高一点会提高脱盐效果,温度提高时,原油的黏度降低,对水滴运动和沉降的应力减小,水滴运动速度增大。与此同时,温度升高时油水界面张力降低,水滴热膨胀,使乳化膜强度减弱,所以较高的温度可以加快原油破乳的速度。但是原油电导率随温度升高而增大,当温度高于140℃后电导率急剧增大,电耗增加。当温度高于140℃后,氯化镁和氯化钙开始水解,也不利于脱盐。而且温度高过一定程度后,会出现水在油相中溶解度增加的倾向。另外,温度过高,也会导致部分烃类汽化而使电脱盐操作不正常,因此要严格控制电脱盐的温度范围。
从原油进装置到电脱盐罐,这一段原油的换热流程称为原油的一段换热系统;从电脱盐罐到初馏塔之间原油的换热流程称为原油的二段换热系统;从初馏塔到常压炉之间初底原油的换热流程,称为原油的三段换热系统。如图2-20所示,原油的一段换热系统终温,决定于此段流程中换热器热流的流量及温降程度(ΔT),如果热流的温降和流量大,那么冷流原油的受热量就大,原油一段换热系统终温将会升高。原油一段换热系统的热源有:减底渣油、常底渣油、常压侧线油、常压中段回流、减压侧线回流、减压中段回流等,按温位从低到高排序流程。每个换热器都有各自的正线和副线,在不改变流量的前提下,热流通过调节副线流量来控制供热量,而冷流(原油)的副线基本不启用,因为原油中的胶质、沥青质和盐含量较高,黏度较大,启用副线易造成管线结垢,经常启用副线也会造成副线阀门关闭不严。

图2-20 换热器冷热流正副线示意图
如图2-21所示,电脱盐罐的操作温度除了与一段原油换热系统有关外,还与进装置原油的初始温度变化有关。原油进装置的温度由原油调和罐区决定,如果原油温度偏低,可直接联系原油调和装置进行调节,以达到工艺生产的要求。原油在调和罐区经过比例调和后,会静止4h后进行多次初步的切水任务,排除一部分盐分。为了较为有效地脱除水分,会在调和后的原油罐底进行蒸汽盘管加热,加热的时间越长,罐内原油温度越高,油水分离越容易,切水脱盐效果越好。所以原油在调和罐区停留的时间增加一天,原油温度都会有相应程度的升高,严格来讲,应该随着原油在罐区停留时间的长短不同,及时调整罐底盘管通入蒸汽的流量。

图2-21 电脱盐罐温度控制显示图
常减压蒸馏装置有三种水:新鲜水、软化水、循环水。循环水用在冷却器中,水质最差也最廉价。软化水最洁净,价格也最高,用于加热产生自用过热蒸汽,然后作为侧线汽提塔和大塔塔底的汽提蒸汽,有些炼厂加热炉为防止炉管结焦,会用软化水注入进炉前的管线中。新鲜水水质和价格居中,电脱盐罐的注水采用的是新鲜水,温度较低。如图2-22所示,在电脱盐的系统中,注水量一般会达到原油加工量的5%~10%,这么大的流量,其温度也会对电脱盐罐操作温度造成很大的影响。所以,一般要对所注的新鲜水尽量用低温位热源预热,避免造成电脱盐罐内原油温度的下降。

图2-22 脱盐罐压力示意图
二、电脱盐罐压力
电脱盐罐内保持一定压力是为了控制原油避免汽化蒸发,如果产生蒸气将导致电脱盐罐操作不正常,严重时引起爆炸。因此脱盐罐内压力必须维持到高于操作温度下原油和水的饱和蒸气压。一般电脱盐罐内压力控制在1.6MPa以上。如果有三级罐串联,则二级罐要高于1.7MPa,一级罐要高于1.8MPa,驱动原油需要罐间保持一定的压差。另外,罐间的静态混合器混合强度也需要消耗一定的压差。以一级罐为例,因为破乳剂和脱金属剂的注入量太小,对于罐内压力的影响可以忽略不计。脱盐罐的注水量与罐底排出的污水量应保持平衡状态,况且注水排水流量约为原油的5%,所以它们对脱盐罐的压力影响也较小。所以,罐内的压力只与进出罐原油流量变化和静态混合器混合强度有关。进罐原油流量由原油泵出口阀门控制,出罐原油量由罐顶出口处的阀门开度来控制。
三、电脱盐罐水的界位
电脱盐罐的水位在原油进口分布器的下方,油水界位要经常检查,高的水位不但缩短原油在弱电场中的停留时间,对脱盐不利,而且水位过高会导致电场短路跳闸。界位过低,会造成脱水带油。一般油水界位控制在25%~35%的范围内,采用较低的水位是为了防止电脱盐罐跳闸。电场对于脱盐罐脱水的作用很大,若因为跳闸造成电场消失,油水分离不利造成含水原油进入后续的初馏塔,将会造成初馏塔冲塔事故,不但初馏塔顶汽油变黑,整体装置的操作都会紊乱。电脱盐罐的内部结构及水位显示如图2-23所示。

图2-23 电脱盐罐内部结构油水界位示意图
电脱盐罐的进水与出水达到平衡时,水位将保持不变。进水来源有二:其一为原油中自带的饱和盐水;其二是原油在进入电脱盐罐前的注水。出水也包括两部分:其一是脱盐原油中所携带的微量水分,在正常电脱盐工况下,这部分水分所占比例不大,可以忽略不计;其二是在电脱盐罐底部的排放水。进水与出水是否达到平衡,都是通过水位的显示表现出来,进水和出水无论哪一方出现流量波动,都将破坏油水界位的稳定。
电脱盐的注水量一般占原油加工量的5%~10%,为了减小脱盐原油对初馏塔及后续工序设备的腐蚀强度,注水量应根据净化原油中的盐含量的变化而作出相应的调整,所以注水量的多少,遵循的原则是要尽量洗掉原油中的盐分,而不是平衡脱盐罐的水位。因此当注水量发生变化时,一定要及时调整脱盐罐底部的排水量,使水位保持稳定不变。脱盐罐的总注水量,依据原油中盐含量的变化而作出相应的调整。每级电脱盐罐的注水量也不相同,一般一级罐和二级罐注水量偏多,一级罐出口的原油盐分脱除率约为95%,二级罐出口原油盐分脱除率可达到99%以上,所以为了降低耗水量,一般炼厂均设计采用三级罐排水回注一级罐的工艺。
四、初馏塔顶温度
保持初馏塔顶压力不变,塔顶温度变化影响着初顶产品(初顶汽油)的终馏点,如果塔顶温度过高,则初馏塔内本不该汽化的馏分汽化,并从塔顶馏出,致使初顶汽油终馏点偏高。相反,保持初馏塔顶压力不变,如果塔顶温度过低,则本应该汽化并从塔顶馏出的组分没有汽化而从塔底引出,致使初顶汽油终馏点偏低。一般初馏塔塔顶温度控制在115~120℃范围内。
初馏塔底部的进料是初馏塔热量的唯一来源,其温度约为220℃,因为其流量大,所以温度即使有微小的波动,都会引起初馏塔顶温度很大的变化。初馏塔进料温度主要与原油二段换热系统中各个换热器的换热效果有关,这些换热器的热流正副线流量、温度变化直接影响着原油二段换热终温,即初馏塔进料温度。
初馏塔顶压力升高,一方面因为减小了进料口到塔顶的压降而降低塔内部的上升气速,另一方面因提高了塔内的油气分压,相当于提高各个组分的沸点,这样,高温的较重组分就无法汽化上升到达塔顶而使塔顶温度下降(热量的载体是上升的油气)。
如图2-24所示,初馏塔顶油气出塔温度在120℃左右,从塔顶引出后,经过空气冷却器和循环水冷却器冷却至40℃进入初顶罐,实现油、水、气三相分离后,油相经过初顶汽油泵驱动部分返回至塔顶。因此,通过塔顶冷回流的温度和流量可以降低塔顶的温度,增大冷回流流量和降低冷回流温度,均可以降低塔顶温度。

图2-24 初馏塔顶冷回流示意图
循环水冷却器的工作原理与换热器相同,热流、冷流也均有正线和副线。但一般冷却器冷热流全部都走正线,依据冷流中冷却循环水的温度和流量来调节冷却效果,即如果降低冷却循环水的温度,或增加冷却循环水的流量,则冷却力度加强,塔顶冷回流温度将降低。由于循环水是由装置外供,来水的温度是固定的,所以在调节冷却器冷却力度时,主要靠调节冷却水流量来实现。
五、初馏塔顶压力
保持初馏塔顶温度不变,塔顶压力变化影响着初顶产品(初顶汽油)的终馏点,如果塔顶压力过低,则初馏塔内本不该汽化的馏分汽化,并从塔顶馏出,致使初顶汽油终馏点偏高。相反,如果塔顶压力过高,在塔顶本应该汽化并从塔顶应该馏出的组分没有汽化,而从塔底引出,致使初顶汽油终馏点偏低。一般初馏塔顶压力(表压)控制在0.20~0.25MPa的范围内。
初顶温度的升高,会造成塔顶轻组分的汽化率增大,因此塔顶的气相负荷变大,塔顶压力随之升高。初馏塔顶冷回流温度一般在40℃左右,返塔后大部分会汽化,如果其返塔冷回流流量增大,将会造成塔顶气相负荷增大,压力随之升高。同理,塔顶冷回流中含水量增大,水分进入塔内后汽化,塔顶气相负荷增大,压力随之升高。
常减压蒸馏装置的产品中,直馏汽油和减压渣油中硫含量较多,直馏汽油和减压渣油接触的设备都易发生硫腐蚀,严重时会造成砂眼,发生泄漏,影响装置生产周期。尤其是塔顶挥发线处,易形成露点腐蚀,硫酸盐的浓度较高,腐蚀力度较大。为了减缓硫对塔顶挥发线的腐蚀,一般会向塔顶注入缓蚀剂,缓蚀剂与水混合形成一定浓度,再用柱塞泵提供扬程并按规定的计量注入初馏塔和常压塔的塔顶,在挥发线处形成一层保护膜,这样就增加了塔顶的水含量,这部分水全部进入到塔顶回流罐中,并从罐底引出排入地井。但是一定要做好塔顶回流罐的油水分离工作,避免塔顶冷回流中携带水分,造成塔顶操作波动。
如图2-24所示,初馏塔顶油气先经过空气冷却器冷却,气相有很大部分会变成液相,这样,会造成相变部位的压力降低,这样就形成了塔顶到空冷相变部位的压降,驱使气相从塔顶向空冷相变部位流动。如果空冷冷却力度加大,会增大这种压降,使气相从塔顶到空冷相变部位的流动速度加大,进而降低了塔顶的压力。在现场生产中,将调节初顶空冷冷却力度作为调节初馏塔顶压力的主要手段。
气相从初馏塔顶到初顶罐,形成了封闭的空间,在这个空间里,唯有初顶罐顶部的气体外排阀门是泄压口,此阀门后续连接的是炼厂低压燃料气管网,管网内压力远低于初顶罐内压力,如果此阀门开度增大,将有更多的气体外排,初顶罐的压力将下降,这样等于加大了气相从塔顶到初顶罐的压降,增大了气相从塔顶到初顶罐的流速,进而降低了塔顶压力。
电脱盐系统虽然会把原油中的含水量降至微小范围内,但无法实现将水分彻底脱除,这是因为装置要完成一定的原油加工量。脱出原油中的水分进入到初馏塔后会汽化并集中在塔顶部位。因此初馏塔进料含水量的变化也会影响塔顶压力,进料含水量增大,则塔顶的水蒸气负荷会增大,气相总负荷将增大,塔顶压力将升高。在实际的操作中,不担心初馏塔进料中含有水分,只要这些水分含量稳定在允许的范围内,便不会造成塔顶压力的较大波动而影响装置的平稳运行。稳定初馏塔进料中的水含量的前提条件是平稳电脱盐系统的操作。
六、初馏塔底液位
如图2-25所示,初馏塔底液位发生变化时,会使初馏塔底泵出口流量发生波动,如果常压炉没有及时调整火嘴的发热量,即没有及时改变燃料油火嘴和燃料气火嘴开度,将会导致常压炉出口温度产生波动,即常压塔进料温度发生变化,这样会影响常压塔的正常操作,严重时会使常压侧线产品质量不合格。所以,初馏塔底液位稳定是常压系统实现平稳运行的前提条件。一般地,初馏塔底液位控制在50(1±10)%的范围内。

图2-25 初馏塔底液位相关流程图
如图2-25所示,对于初馏塔底液位来讲,初馏塔底进料有一,即原油泵的出口流量;出料有二,一为初底泵外排流量,另一为初馏塔内塔底进料的汽化上升量,所以初馏塔底物料是否平衡,只要考虑这三点即可。
初馏塔底进料量主要由原油泵出口流量控制,进料量增大,则初底液面将升高。原油泵的泵送流量不可以随意调节,它关系到常减压蒸馏装置的加工量,根据年初炼厂制定的常减压蒸馏装置的加工任务,厂技术部门将会计算出装置详细到每天的原油加工量,并要求每天平稳完成加工任务。另外,原油泵的出口流量发生变化,将会造成装置后续工艺参数的整体变动,影响装置的平稳运行,一切安全事故和质量事故均是由操作波动引起的。
初底泵出口流量增大,则初馏塔底液面将降低。初馏塔底泵出口流量,即为常压炉进料流量,也即为常压塔底的进料流量。初馏塔底泵出口流量发生变化,如果没有及时相应地调整常压炉燃料油和燃料气的火嘴开度,将会导致常压炉出口温度发生变化,加之常压塔底进料量发生波动,将会造成常压塔的操作波动,严重时会影响常压塔塔顶及侧线产品的质量。因此在调节初底泵出口流量的同时,一定要考虑后续受影响的工艺参数,预见性判断这些工艺参数的变化趋势,及时调整。
初馏塔底汽化率,主要指的是初顶气体和出装置的初顶汽油产率之和占塔底进料的百分比。初馏塔底的汽化率降低,即初顶气体和初顶汽油的产率下降,说明本应该作为初顶产品的组分液相回流至塔底,则初底液面将升高。
保持初馏塔底温度、塔顶温度和压力不变,如果进料密度变小,进料中轻组分的比例增大,则初顶产品产量将会增加,汽化率将升高。初馏塔进料性质即净化原油的性质,也即采油厂或产油矿区的原油性质,一般在短期内各个原油的性质及组成不会发生较大变化,如果炼厂原油调和装置按着规定比例调和原油,一般不会使初馏塔进料性质发生较大波动,所以在调节初馏塔底汽化率时,不会考虑进料性质的影响因素。烃类组分的相变与温度有关,进料温度升高会促进液相组分的汽化,温度升高,则汽化率将升高。初馏塔底进料温度,即为原油二段换热终温,从电脱盐罐出口至初馏塔底进料之间这一段的原油换热系统称为原油的二段系统,系统内换热器的热源,为常压塔侧线、常底渣油、减压塔侧线、减底渣油,这些热流在换热器的流量及温降变化,均可导致初馏塔底进料温度发生变化。初馏塔顶压力也会影响油分的汽化效果,塔顶压力降低,降低了烃类的沸点,促进了较轻烃类组分的汽化。一般通过对空气冷却器的冷却力度和初顶回流罐顶气相外排阀门开度的调节,来控制初馏塔顶压力。
七、初顶中间罐水位控制
塔顶冷回流带水是初馏塔以及其他蒸馏塔操作较为棘手的问题之一,由于水汽化潜热较大,回流带水返塔后不但吸收大量的热量,而且汽化后,体积增加多倍,将引起操作波动,威胁生产安全,发现不及时或处理不当,就会造成冲塔,当塔顶压力超过0.255MPa安全阀定压值时,促使安全阀启跳,造成事故。为了避免塔顶回流带水,必须要稳定初顶中间罐的水位,一般控制在50%±10%范围内。塔顶回流罐结构见图2-26。

图2-26 塔顶回流罐结构示意图
如果进料中含水量波动不大,基本不会影响到初顶罐中水位的稳定。当初馏塔底进料中含水量突然变大,单位时间内进入到初顶罐中的水量会增加,其水位将升高。这时应及时加大排水量,以避免回流带水。初馏塔进料含水量与电脱盐系统的操作有关,只要电脱盐罐主要操作参数,如压力、温度、注水量、排水量、电压、破乳剂注入量、原油泵出口流量等参数稳定后,唯一能造成初馏塔底进料含水量变化的只有原油调和工艺的操作状况。一般认为净化原油的温度及含水量的变化过大波动,会导致电脱盐系统的操作紊乱,进而影响到初馏塔的平稳运行。
根据物料平衡的原理,初顶罐的排水量等于罐进料中的水含量,即可稳定初顶罐的水位平衡。初顶罐的排水量,要考虑塔顶注缓蚀剂液中的水含量,而且根据装置的运行时段及塔顶挥发线腐蚀程度,会相应加大缓蚀剂的注入强度,或者为了稀释塔顶酸液的浓度。有些炼厂常减压蒸馏装置会配置另外加注塔顶新鲜水的工艺,这样相当于加大了初顶罐的进水量,此时应及时调节排水量,以稳定初顶罐的水位。
一定的初顶油气的冷后温度,对应着一定的初顶罐中的油水分离效果。如果冷后温度升高,汽油馏分和水的分离效果将下降,因为水和汽油馏分的分子能量大,运动加强,相互渗透和混合,部分水分子会运动到油相中与汽油一同翻过隔油墙到积油间而造成水位的下降,此部分水随着汽油部分回流至塔顶,会造成塔顶压力的升高,进而降低了塔内的上升气速,单位时间内水蒸气冷却进入到初顶罐的量会减少,初顶罐中的水位将会进一步下降,造成恶性循环。
八、常压塔顶温度
保持常压塔顶压力不变,塔顶温度变化影响着常顶产品(常顶汽油)的终馏点,如果塔顶温度升高,则常压塔内本不该汽化的馏分汽化,并从塔顶馏出,致使常顶汽油终馏点偏高,且常一线产品的初馏点也跟着升高。相反,如果塔顶温度降低,则本应该汽化并从常压塔顶馏出的组分没有汽化,而是从常一线抽出口馏出,这样导致常顶汽油终馏点偏低和常一线初馏点偏低。一般常压塔顶温度控制在120℃附近,常顶汽油比初顶汽油的产率低。
经过常压炉加热后来的进料所提供的热量,是常压塔唯一的热源,进料的温度直接影响到整个大塔的温度。进料温度降低,则大塔各个温位均会下降。另外,进料温度也与原油的三段换热系统的终温变化有关,在原油三段换热系统中,冷热流流量及温度、热流正副线流量比例都会影响常压塔进料温度。
常压塔侧线抽出量越大,则大塔损失的热量就会越多,抽出线上方的各个塔板温度就会下降。常一线抽出量变大,有些较轻的气相组分会在常一线抽出口馏出,这些组分没有把热量携带到塔顶,致使塔顶温度下降。塔顶循环回流抽出与返塔温差越大,抽出量越大,则塔顶损失的热量越多,其回流附近塔板的温度均下降,塔顶温度也会受到不同程度的影响。
常压塔顶冷回流温度一般在40℃左右,当常顶空冷、水冷冷却力度发生变化时,势必会改变常顶罐的温度,如果塔顶冷回流返塔的温度降低,冷回流的流量加大,则塔顶的温度将下降。塔顶压力对塔顶温度的影响主要表现为塔顶压力升高,会降低塔内部上升气速,这样,高温的重组分就无法到达塔顶而使塔顶温度下降。另外,塔顶压力也会影响部分轻组分中纯烃的沸点,塔顶压力偏低,烃类的沸点将下降,塔顶整体汽化率将增大,塔顶气体产率将增大,有更多的热量载体到达塔顶,致使塔顶温度升高。
九、常压塔顶压力
保持常压塔顶温度不变,塔顶压力变化影响着常顶产品(常顶汽油)的终馏点,如果塔顶压力升高,在塔顶本应该汽化并且挥发的组分没有汽化,致使常顶汽油终馏点和常一线初馏点偏低。一般常压塔顶压力(表压)控制在0.01~0.06MPa 的范围内。
塔顶温度升高,会有更多的组分汽化而冲至塔顶,塔顶的气相负荷变大,塔顶压力将升高。无论是大塔塔底注汽,还是侧线汽提塔注汽,所有的水蒸气将全部上升至常压塔顶。如果注汽量增大,则塔顶气相负荷变大,塔顶压力将会上升。但是,影响塔顶气相负荷的主要组分是油气,蒸汽只占很小一部分比例,一般在使用塔底注汽和侧线汽提塔注汽工艺手段时,主要是为了汽提侧线及塔底烃类的轻组分,增加油品产量,调节油品闪点,而不是为了调节大塔顶部的压力。
进料性质稳定时,塔顶的气相负荷将会稳定。如果进料变轻,会有更多的轻组分汽化上升至塔顶,使塔顶的气相负荷变大,塔顶压力升高。进料变轻的原因,一般归结为初馏塔的拔出率,初馏塔的拔出率减小,本应该在初馏塔汽化挥发的组分在常压塔顶汽化馏出,这样相当于增加了常压塔的负荷,造成常压塔顶的压力上升。
如图2-27所示,常压塔顶油气先经过空气冷却器冷却,塔顶挥发出来的气相有很大部分会变成液相,这样会造成相变部位的真空,形成了从塔顶到空冷相变部位的压降,驱使气相从塔顶向空冷相变部位流动。如果空冷冷却力度加大,会增大这种压降,使气相从塔顶到空冷相变部位的流动速度加大,进而降低了塔顶的压力。在现场生产中,调节常顶空冷冷却力度作为调节常压塔顶压力的主要手段。

图2-27 常顶冷回流流程示意图
塔顶回流返塔后,由于沸点低于塔顶温度,所以回流中大部分组分会汽化,如果回流量增大,造成塔顶气相负荷变大,压力随之升高。同理,塔顶回流中含水量增大,水分进入塔内后汽化,塔顶气相负荷变大,压力随之升高。
气相从常压塔顶到常顶罐,形成了封闭的空间,在这个空间里,唯有常顶罐顶部的气体外排阀门是泄压口,此阀门后续连接的是炼厂低压燃料气管网,管网压力低于常顶罐内压力,如果此阀门开度增大,将有更多的气体外排,常顶罐的压力将下降,这样等于加大了气相从塔顶到常顶罐的压降,增大了气相从塔顶到常顶罐的流速,进而降低了塔顶压力。
十、常压塔底液面
如图2-28所示,常压塔底液位发生变化,会使常压塔底泵出口流量发生波动,如果减压炉没有及时调整火嘴的发热量,会导致减压炉出口温度波动,即减压塔进料温度发生变化,这样会导致减压塔操作波动,严重时会使减压侧线产品质量指标不合格。所以,常压塔底液位稳定是减压系统平稳操作的前提条件,一般常压塔底液位控制在50(1±10%)的范围内。

图2-28 常压塔底液位相关流程图
如图2-28所示,常压塔底进料有一,即初馏塔底泵出口流量。而出料有二:其一为常底泵出口流量,其二为常压塔内部的汽化上升量。所以,常压塔底物料是否平衡,只要考虑这三点即可。
常压塔底进料量主要由初底油泵出口流量控制,进料量增大,则常压塔底液面将升高。但是,如果改变了初底泵出口的流量,会引起初馏塔底液位的变化,就需要调节原油泵出口流量,这是不可取的,所以一般不会利用调节初馏塔底泵出口流量来平衡常压塔底液位。
常底泵出口流量增大,则常压塔底液面将降低。但是在调节常底泵出口流量的同时,也要考虑减压系统的操作平稳性,要提前做好减压炉的相关调节工作,如燃料油火嘴和燃料气火嘴的开度、炉膛负压等,以保证减压塔进料的温度稳定,进而稳定整个减压塔的操作。
常压塔的汽化率主要是指常顶气体、常顶汽油、常一线、常二线、常三线产品的产率总和。常压塔的汽化率降低,说明本应该汽化并从侧线馏出的组分没有馏出而是留存在塔底,使得常底液面升高。由于塔底进料的温度较高,所以塔底汽化程度是常压塔底液位的重要影响因素。
保持常压塔底温度不变,进料中轻组分的比例增大,则汽化率将增大。保持常压塔底温度、塔顶温度和压力不变,如果进料中轻组分的比例增大,则常压塔产品总量将会增大,汽化率将增大。常底进料轻组分的含量增大,说明本应该在初馏塔汽化馏出的组分没有馏出,而是随初底原油一同进入到了常压塔,这些组分便会在常压塔顶馏出。
进料温度会促进油分的汽化,温度升高,则汽化率将增大。常压塔底进料温度与常压炉的加热程度和原油三段换热系统终温有关,此系统换热器的热流为减压侧线、常渣及减压渣油,热流的流量、正副线的比例,都会对原油三段换热终温造成影响。另外,塔顶压力也会影响油分的汽化效果,塔顶压力越低,各个组分的沸点也相应降低,则塔内进料整体汽化率将增大。
常压塔底注汽,是为了降低常压塔内部油气分压,促进油分的汽化力度的加强,增大侧线产品的产率。如果加大注汽量,会降低塔顶的油气分压,降低组分的沸点,使汽化的油分增多,汽化率上升。塔底注汽主要改变的是常三线的产量。
十一、减压塔顶压力
减压塔是在较低的温度和压力下进行物料切割的,温度较低是为了避免发生烃类的化学反应。
抽真空蒸汽压力越高,在混合室侧面形成的真空度越高,形成的从减压塔顶到一级抽真空器混合室的压降就会越大,促使减压塔顶向一级抽真空器混合室的气流流速增大,减压塔顶的压力就会降低。
减压塔底注汽量和减压侧线注汽量增大,上升到塔顶的水蒸气就会越多,塔顶的气相负荷将会增大,塔顶的压力就会升高。另外,减压塔内水蒸气的分压越大,则油气分压减小,会促使油相汽化率增大,汽化上升的气体总量增加。
减压炉出口温度不宜过高,以不发生裂解反应为限,但是这个度很难把握。如果减压炉出口温度过高,炉管内的常渣进入减压塔后,将会有更多的轻组分汽化上升至塔顶,使塔顶压力升高。常压拔出率指的是常顶气体、常顶汽油、常一线、常二线及常三线的产率总和。常压拔出率越高,说明常压汽化产出的产品就越多,常渣就会少而重,进入减压塔后,组分的汽化率将会下降,塔顶的气相负荷变小,塔顶压力降低。
减压塔顶温度越高,达到沸点而汽化的组分就越多,本不应汽化的轻组分汽化上升至塔顶,致使塔顶气相负荷变大,塔顶压力升高。
减底液面越高,淹没的格栅和填料越多,提馏的效果就越差,被淹没在液相中的轻组分就会增多,本应汽化上升至塔顶的轻组分减少,塔顶气相负荷变小,塔顶压力降低。虽然减压塔底液位是减顶压力的影响因素,但它的影响程度较小,除非减底液位淹没接近到减五线高度时,塔底液位高度对塔顶压力的影响开始变得突出。
抽真空系统前冷、中冷、后冷却器的冷却水温度越低,流量越大,冷却效果就越好,从塔顶引出的气相在冷却器内冷却为液相的比例增大,抽真空器的负荷就会变小,抽真空器的工作效能增大,使从减压塔顶到抽真空器的压降增大,气流流速增大,减压塔顶气相负荷减弱变快,塔顶压力降低。
十二、减压塔顶温度
减压塔顶温度对于减顶油和减一线油馏程的影响很大。减顶油的馏程较宽,一般为室温至370℃,闪点为室温,如果不影响柴油的闪点,则可以作为轻柴油的调和组分输往油库。但如果闪点不允许,或者减顶油产率过大,则需打入原油泵进口进行回炼。减一线油的馏程为300~370℃,常与常二线、常三线混合生产轻柴油馏分。其他条件不变,减压塔顶温度过高,本不该汽化的组分汽化上升至塔顶,以减顶油馏分馏出,这样就较少了轻柴油的产率,降低装置效益。减压塔顶温度一般控制在50~70℃的范围内,减顶温度各个炼厂有所不同,依据塔顶压力和侧线产品要求而定,但必须使水成为气态。
经过减压炉加热后来的进料,其提供的热量是减压塔唯一的热源,进料的温度直接影响到整个大塔的温度。进料温度低,则大塔各个温位均会下降。侧线抽出量越大,则大塔损失的热量就会越多,抽出线上方的各个温位均会下降。减一线回流、减一中段回流、减二中段回流抽出与返塔温差越大,流量越大,则大塔损失的热量越多,其回流上方的各个温位均下降。
减压塔顶压力对塔顶温度的影响主要表现为塔顶压力升高,一是会降低塔内部上升气速,二是使部分组分的沸点升高无法汽化,这样高温的重组分就无法到达塔顶,造成塔顶温度的降低(热量的载体是上升的油气)。
十三、减压塔底液位
减压塔底液位会不同程度地影响减压塔内汽化率,如果减底液位超高至减五线附近,将会加大影响减压塔内的汽化率,一般控制塔底液位高度为40%~60%。
如图2-29所示,减压塔底进料有一,即常底泵出口流量。而出料有二:其一为减底泵外排量,其二为减压塔内部的汽化上升量,总收率即减顶气、减顶油、减一线、减二线、减三线、减四线、减五线收率的总和。所以,减压塔底物料是否平衡,只要考虑这三点即可。

图2-29 减压塔底液位相关流程图
减压塔底进料量主要由常底泵出口流量调节,进料量增大,则减压塔底液面将升高。常底泵出口流量应根据常压塔底液位的变化而变化,其主要目的是维护常压系统的操作稳定,所以常压塔底泵的出口流量不可作为减压塔底液位的调节手段。减底泵出口流量增大,则减压塔底液面将降低。减压塔底泵出口流量的大小除了对于原油一段、二段、三段换热系统的换热终温有一定的影响外,对本装置的平稳操作没有影响,因此一般把调节减压塔底泵出口流量作为调节减压塔底液位平衡的首选手段。但是,为了兼顾后续装置的平稳运行,在调节减压渣油出装置流量时,要及时通知下游装置做好应对准备,尤其是当下游装置没有原料罐和减压渣油直接进入下游装置的缓冲罐加工时,应提前通知下游装置主控室,做好变量操作的前提准备。
减压塔底的汽化率升高,则减底液面将下降。减压塔内的汽化率主要与减压塔底进料性质、进料温度、塔顶压力及塔底注汽量有关。保持减压塔底温度不变,如果常压塔拔出率降低,说明本应该在常压塔内汽化并从常压侧线馏出的组分进入到减压塔内汽化,这样就增大了减压塔负荷,减压塔内的汽化率增大。塔顶压力也会影响油分的汽化效果,塔顶压力越低,则汽化率就会越大。在保持减压塔顶压力不变的前提下,进料温度的升高会促进油分的汽化,而使塔内汽化率增大。减压塔底注汽,是为了降低减压塔内部油气分压,促进油分的汽化。如果加大注汽量,将会降低塔顶的油气分压,降低油分的沸点,则汽化的油分增多,汽化率增大。
如果减压炉温度超高,会导致炉管内的常渣发生裂解反应而生成轻组分,进入减压塔的较轻组分的比例增大,汽化率增大,会导致减压塔底液位下降。但是,在烃类发生裂解反应的同时,也会发生稠环芳烃的缩合反应,生成碳氢比更高的焦炭,聚集在高温部分,腐蚀设备而缩短装置的生产周期,因此减压操作的重点是避免发生炉温的超高现象。如果想要提高减压拔出率,应尽可能地提高减压塔顶的真空度。
十四、常压加热炉出口温度
常压炉出口温度是常减压蒸馏装置的重要操作工艺参数,也是装置实现平稳操作较为重要的控制点,常压炉出口温度波动,将会导致常压塔操作的紊乱,严重时会导致常压塔侧线产品质量不合格。常压炉结构示意图见图2-30。

图2-30 常压炉结构示意图
保持其他工况条件不变,加热炉提供的热量一定,加热炉进料温度升高,则炉出口的温度就会上升。常压炉进料温度取决于原油三段换热效果,即换热器热流正线的流量及温度、冷流的正线流量。一般冷流原油不会走副线,因为流量减少而使正副线管线都结垢,慢慢会导致管线堵塞。所以,在调节原油三段换热终温时,一般都是调节热流的副线流量。
保持其他工况条件不变,加热炉提供的热量一定,进料量越少,则炉出口的温度就会越高。常压炉的进料量由初底泵出口阀门开度来调节。但是,一旦装置的处理量趋于稳定后,基本不把调节加热炉的进料量作为调节炉温的手段,因为进料量变化后,后续的系统参数都会相应发生变化,比如常压炉后的常压塔底液面、减压炉出口温度、减压塔底液面等。
单位时间内,燃料气用量越大,则炉出口温度越高。燃料气用量的决定因素是燃料气的压力,压力越大,阀门开度不变,则气体流量就会越大。因为常减压蒸馏装置是原油加工的龙头装置,处理量较大,单靠燃料气加热,可能达不到工艺生产要求的炉出口温度,一般炼厂的常减压蒸馏装置的加热炉都要设燃料油火嘴。常减压蒸馏装置所用的燃料油就是减压渣油,其压力的调节,本装置可以完成,只要调节减压渣油换热器燃料油分支流程阀门开度即可。单位时间内,燃料油用量越大,则炉出口温度越高。燃料油用量的决定因素是燃料油的压力,压力越大,阀门开度不变,则燃料油流量就会越大。
保持加热炉烟气有足够的氧含量,是燃料在加热炉中能够完全燃烧的前提,也是燃料放出最大能量的前提。所以在一定范围内,烟气中氧含量越高,可使燃料,特别是馏分较重、热值较高的燃料油能够完全燃烧,提供的热量就越大,加热炉出口温度就会越高。烟气中的氧含量是由进炉空气提供的,进炉空气会消耗加热炉的热量,进炉空气的温度越高,则消耗加热炉的热量就会越少,会有更多的热量去加热炉管内的介质,炉出口的温度就会升高。为提高加热炉的热效率,烟气的氧含量不可过高,根据燃料油的特点确定,一般都控制在4%以下。
十五、减压加热炉出口温度
减压炉出口温度也是常减压蒸馏装置的重要工艺操作参数,减压炉出口温度是否稳定直接影响减压塔能否平稳运行。与常压炉不同的是,减压炉对流室还有加热自产蒸汽的作用,所以进炉自产蒸汽流量及温升也是影响减压炉出口温度的一个因素。
保持其他工况条件不变,如果加热炉提供的热量一定,减压炉进料温度升高,则炉出口的温度就会上升。减压炉进料,即常压塔底出来的常底渣油,在进入减压炉之前没有任何的换热升温设备,所以减压炉进料温度与常底渣油温度的变化趋势相同。保持其他工况条件不变,如果加热炉提供的热量一定,进料量越少,则炉出口的温度就会越高。减压炉的进料量由常底泵出口阀门开度来调节。阀门开度越大,则减压炉进料量就会越大。与常压炉一样,减压炉进料也不作为减压炉出口温度的调节手段,为免引起减压塔操作的波动。
在减压炉的对流室,有自产蒸汽盘管通过,目的是加热自产蒸汽,使其温度达到过热状态,一般温度要达到340℃以上,然后这些过热蒸汽注入常压塔底、减压塔底和各汽提塔底作为汽提蒸汽使用。这些蒸汽由饱和蒸汽过渡到过热蒸汽所需要的热量就是由减压炉对流室提供的。如果过热蒸汽流量越大,或者过热蒸汽进出温升越大,则需要的热量就会越多,本来用来加热减压炉管内介质的热量来加热过热蒸汽,致使减压炉出口温度降低。
其他因素,如燃料气、燃料油、烟气中氧含量、冷风预热程度对减压炉出口温度的影响与常压炉相同。
十六、初馏塔顶汽油终馏点
常减压蒸馏装置直馏汽油终馏点一般控制在不大于170℃。一方面是因为直馏汽油的下一道工序是催化重整工艺,它是烷烃环化脱氢生产芳烃和环烷烃异构、脱氢生成芳烃的过程,在此过程中汽油馏分的终馏点一般会提高25℃以上,车用汽油的国家标准中规定其终馏点为不大于205℃,这样必须要求直馏汽油终馏点要留出余量,以保证催化重整汽油终馏点不超标。另一方面是为了增产煤油和柴油。
一定的塔顶压力会对应一定的塔内汽化率,塔顶压力升高,会升高轻组分的沸点,整体上降低轻组分的汽化率,等于降低了塔顶产品的馏出率,进而降低初顶汽油的终馏点。同样,一样的塔顶温度,也对应着一定的汽化率,塔顶温度升高,轻组分汽化率增大,塔顶馏出的产品就会增多,初顶汽油的终馏点则升高。
初顶汽油的终馏点,还与初馏塔内的气速有关,只是受塔内气速的影响不是很大,一般认为初馏塔内气速增大,会出现重组分被携带至塔顶馏出的现象,这样初顶汽油中掺入了重组分而使终馏点略微升高。其实这种现象也算是冲塔,只不过没有严重到影响塔顶产品的质量。造成塔内气速突然增大的原因有很多,如进料突然变轻、塔顶压力突然降低等。初馏塔进料水含量突然变大,多数是因为电脱盐罐跳闸,此时会造成初馏塔操作的紊乱,严重时会造成初馏塔冲塔事故。
初馏塔内上升气速稳定,进料性质也稳定后,初顶汽油的终馏点会随着其产率的变化而变化。产率增大,初顶汽油的终馏点将会升高。所以,初顶汽油的终馏点也会与常减压蒸馏装置的加工量有微小的关系,装置的加工量下降,使初顶汽油的产率会增大,初顶汽油的终馏点也会有微小的升高。
十七、常顶汽油终馏点
常压塔产品从上到下依次是常顶气体、常顶汽油馏分、常一线煤油馏分、常二线轻柴油馏分、常三线重柴油馏分及常底渣油馏分,相邻侧线抽出的馏分相互间会有馏程上的重叠和影响,上一侧线产品的终馏点会影响下一侧线产品的初馏点。所以,相邻侧线产品在产率上也会互相影响。常顶汽油馏分的终馏点会影响到常一线的初馏点,所以常顶汽油的终馏点偏高,则说明属于常一线不应该汽化而从塔顶馏出的组分从常压塔顶汽化馏出,致使常一线煤油馏分的收率降低。如果炼厂有生产煤油(一般是航空煤油)的生产计划,则常顶汽油馏分的终馏点不会高,让出一部分较重的汽油馏分从常一线抽出,以增大常一线产率。这时常顶汽油馏分的终馏点的控制就需要低一些,一般控制在不大于170℃(各个炼厂有所不同)。
保持其他工况条件不变,一定的塔顶压力会对应一定的汽化率,塔顶压力升高,会提高轻组分的沸点,整体上降低了轻组分的汽化率,相应地降低了塔顶产品的馏出率,进而降低常顶汽油的终馏点。保持其他工况条件不变,一定的塔顶温度,也对应着一定的汽化率,塔顶温度升高,轻组分汽化率增大,塔顶馏出的产品就多,初顶汽油的终馏点将会提高。
常一线抽出量如果减少,本应该在常一线馏出的轻组分,从常顶汽油中馏出,势必会提高常顶汽油的终馏点。常一线提轻力度也可影响到常顶汽油的终馏点,常一线提轻塔底再沸温度升高,提轻塔内轻组分汽化增强,致使大塔常一线抽出的轻组分返回大塔的量就会增多,而这些组分相对常顶汽油来说属于较重组分,它们全部从塔顶馏出,这样就会提高常顶汽油的终馏点。
十八、常一线初馏点
常一线(喷气燃料)初馏点是常减压蒸馏装置的一个指标控制点,它主要会影响直馏汽油收率、炼厂喷气燃料收率和柴汽比。常一线初馏点偏高,则直馏汽油的终馏点偏高,汽油收率增大,喷气燃料收率减小,柴汽比将会减小。一般生产3#喷气燃料的炼厂控制常一线初馏点为不小于145℃,各厂依据喷气燃料产品质量要求及发热值的不同会有相应的调整。
常顶汽油终馏点和常一线初馏点变化规律相同,常顶汽油终馏点升高,则常一线初馏点也会升高。如前所述,常顶汽油的终馏点与常顶压力、常顶温度、常一线抽出流量及常一线汽提力度变化有关。
如果常减压蒸馏装置加工的原油性质稳定,初顶气体、常顶气体、初顶汽油、常顶汽油收率高,说明应该在常顶汽油以前馏出的产品就较为彻底,残留在常一线的轻组分的比例将会减小,常一线的初馏点就会升高。所以,稳定初馏系统和常压系统塔顶的操作,有利于常一线产品的稳定。
十九、常一线终馏点
常一线(喷气燃料)终馏点变化,将会影响到组成的变化,进而影响诸多物理性质,如净热值、馏程、密度、黏度等。所以,稳定常一线终馏点是稳定炼厂喷气燃料产品性质的前提条件。国标规定,喷气燃料的终馏点为不大于300℃,一般炼厂为了不影响柴油的产率,在发动机允许的范围内及满足军航、民航的要求基础上,会适当降低常一线的终馏点。
如果塔内上升的气速一定,一定的常一线馏出温度,会对应相应的常一线终馏点。常一线馏出温度越高,常一线的终馏点就会越高。常一线抽出口上方有常顶循环回流、常顶冷回流,下方有常一中段回流,这些回流的流量和温降变化,会影响到附近塔板温度的变化,进而会很精确地影响到常一线抽出温度。如:常顶循环回流和常一中段回流的返塔温度降低,或者回流量增大,常一线抽出口的温度将会下降,本应该汽化并从常一线馏出的组分没有汽化馏出,致使常一线组成整体变轻,常一线终馏点降低。
塔顶压力会影响到常一线抽出口附近的压力,此压力越低,则馏分的沸点随之降低,本不应该汽化的较重组分汽化并从常一线抽出口馏出,致使常一线组分偏重,终馏点升高。
如果常二线的抽出量下降,会导致本应该从常二线抽出口馏出的较轻组分从常一线的抽出口馏出,这样就使常一线的馏分变重,终馏点上升。常二线汽提塔的过热蒸汽用量变大,则汽提塔内的油气分压会下降,轻组分的沸点降低,汽化率增大,会有更多的常二线轻组分汽化上升,从汽提塔顶引出返回大塔,而从常一线抽出口馏出,致使常一线重组分含量增加,终馏点升高。
喷气燃料冰点合格是喷气燃料发动机得以正常工作的必要条件,所以原油在常减压蒸馏的过程中,要求喷气燃料在组成上保证冰点的合格,一般控制在不大于-48℃。喷气燃料冰点主要受正构烷烃的物理性质的影响,正构烷烃的含量越高,喷气燃料冰点就会越高。喷气燃料冰点与常一线的初馏点和终馏点也会有所关联:一定馏程的喷气燃料,会对应一定的冰点。终馏点相同,初馏点越低的喷气燃料,冰点会越高;初馏点相同,终馏点越低的喷气燃料,其冰点也会越低。馏程相同的喷气燃料,冰点也有差异,因为在相同馏程范围内有效影响冰点的正构烷烃组分含量会有不同。不同炼厂生产的喷气燃料,会出现馏程相同、冰点不同的现象。
随着温度的升高,燃料油表面上蒸发的油气增多,当油气与空气的混合物达到一定浓度,以明火与之接触时,会发生短暂的闪光(一闪即灭),这时的油温称为闪点。测定闪点的方法有开口杯法和闭口杯法两种,开口杯法测定的闪点要比闭口杯法低15~25℃,闪点的高低与油品的组成及油面上的环境压力有关,环境压力高,闪点高。开口闪点是表征油品发生火灾的一项重要指标。在敞口容器中,油的加热温度应低于开口闪点10℃,在压力容器中加热则无此限制。常一线闪点一般控制在不小于38℃。一定馏程的喷气燃料,会对应一定的闪点:终馏点相同,初馏点越低的喷气燃料,闪点也会越低;初馏点相同,终馏点越低的喷气燃料,其闪点也会越低。闪点是喷气燃料馏程的一个表征现象。不同炼厂、馏程相同的喷气燃料,闪点也有差异,如果馏程范围内的较轻组分比例偏大,则闪点就偏低。
一定馏程的常一线产品,会对应一定的密度:终馏点相同,初馏点越低,其密度也会越小;初馏点相同,终馏点越低,其密度也会越小。一般炼厂控制常一线(喷气燃料)密度为ρ20≥775.1kg/m3。馏程相同的常一线,密度也有差异,如果馏程范围内的轻组分比例偏大,则密度就偏小。
二十、常二线终馏点
常二线(轻柴油)终馏点的变化,将会影响到组成的变化,进而影响诸多物理性质,如闪点、凝点、冷滤点、密度、馏程等。所以,稳定常二线终馏点是稳定炼厂轻柴油产品性质的前提条件。一般常二线、常三线和减一线合输油库作为轻柴油的调和组分,其中常二线占很大比例,常三线和减一线馏程较常二线窄而偏重,在生产中炼厂多以卡边操作控制常二线终馏点不大于365℃来最大限度地生产轻柴油。
保持其他工况条件不变,一定的常二线馏出温度,会对应相应的常二线终馏点。所以,常二线馏出温度越高,常二线的终馏点就会越高。常二线抽出口位于常一中段回流和常二中段回流之间,所以常二线抽出口附近的温度就依靠常一、二中段回流来调节。常一、二中段回流返塔的温度越低,流量越大,则说明常一、二中段回流外放的热量就越大,对于大塔来说,常一、二中段抽出口的热量损失就越多,其附近塔板的温度均会下降,以致使常二线抽出口附近的塔板温度也随之下降,故常二线抽出温度将会降低。
塔顶压力会影响到常二线抽出口附近的压力,此压力越低,则油分的沸点随之降低,常二线馏出的组分将会变重,常二线的终馏点就会升高。反之,塔顶压力升高,油分的沸点随之升高,本应汽化馏出的组分没有从常二线的抽出口馏出,而是落到了常三线塔板上,这样就导致常二线的终馏点下降。如果常三线的抽出量下降,会导致本应该从常三线抽出口馏出的组分从常二线的抽出口馏出,这样就使常二线的组分变重,终馏点上升。
常三线汽提塔的过热蒸汽用量变大,则汽提塔内的油气分压会下降,轻组分的汽化率增大,会有更多的常三线轻组分返回大塔,而从常二线抽出口馏出,提高了常二线的终馏点。反之,常三线的汽提蒸汽用量变小,轻组分汽化返塔量变小,从常二线馏出的重组分将变少,常二线终馏点就会降低。
一定馏程的常二线,会对应一定的凝点。对于黏温凝固为特点的柴油馏分来讲,终馏点相同,初馏点越低,其凝点也会越低。对于骨架凝固为特点的柴油馏分来讲,初馏点相同,终馏点越低,其凝点会越高。凝点的高低变化规律,与有效影响黏温特性的组分含量有关。不同炼厂生产的馏程相同的轻柴油,因为原油的性质不同,柴油馏分的凝点也有差异。
一定馏程的常二线,会对应一定的闪点。终馏点相同,初馏点越低,其闪点也会越低;初馏点相同,终馏点越低,其闪点也会越低。常二线闪点是常二线馏程的一个表征现象。国标轻柴油闪点要求不小于55℃。不同炼厂、馏程相同的轻柴油,闪点也有差异,如果馏程范围内的轻组分比例偏大,则闪点就越低。
中石油某炼厂常减压蒸馏装置主要工艺参数指标见表2-8。
表2-8 中石油某炼厂常减压蒸馏装置主要工艺参数指标

①减压炉出口温度指标随处理量变化而有所改动。