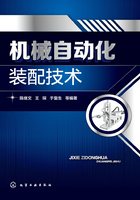
2.3 装配工艺过程的确定
(1)自动装配条件下的结构工艺性
自动装配工艺性好的产品结构能使自动装配过程简化,易于实现自动定向和自我检测,简化自动装配设备,保证装配质量,降低生产成本。反之,如果装配工艺性不好,则自动装配质量问题就可能长期难以解决。可靠的解决途径是在产品结构设计时加强工艺性审查,使产品结构最大限度地具有自动装配工艺性。在自动装配条件下,零件的结构工艺性应符合以下三项原则。
①便于自动给料 为使零件有利于自动给料,产品的零部件结构应符合以下要求:
a.零件的几何形状力求对称,便于定向处理。
b.如果零件由于产品本身结构要求不能对称,则应使其不对称程度合理扩大,以便自动定向时能利用其不对称性,如重量、外形、尺寸等的不对称性。
c.将零件的一端做成圆弧形,这样易于导向。
d.某些零件自动给料时,必须防止其缠在一起。例如:有通槽的零件,宜将槽的位置错开;具有相同内、外锥度表面时,应使内、外锥度不等,以防套入卡死。
②有利于零件的自动传送 零件的自动传送,包括从给料装置至装配工位的传送和装配工位之间的传送,其具体要求如下:
a.零件除具有装配基准面外,还需考虑具有装夹基准面,供传送装置装夹和支承。
b.零部件的结构应带有加工好的面和孔,供传送中定位。
c.零件应外形简单、规则、尺寸小、重量轻。
③有利于自动装配作业
a.零件数量应尽可能少,同时应减少紧固件的数量。
b.零件的尺寸公差及表面几何特征应能保证按完全互换的方法进行装配。
c.尽量减少螺纹连接,以适应自动装配,如用粘接、过盈连接、焊接等方式代替。
d.零件上尽可能采用定位凸缘,以减少自动装配中的测量工作,如将压配合的光轴用阶梯轴代替等。
e.零件的材料若为易碎材料,宜用塑料代替。
f.产品的结构应能以最简单的运动把零件安装到基准零件上去,最好是能使零件按同一个方向安装,这样可避免改变基础件的方向,从而减少安装工作量。
g.对于装配时必须调整位置的配合副,在结构上要尽可能考虑有相对移动的条件,如轴在套筒中沿滑动键直接移动,则可采用开槽的方式使轴和套筒相连接。
h.应最大限度地采用标准件和通用件,以便减少机械加工量,加大装配工艺的重复性。
改进零部件装配工艺性的示例见表2-8。为获得较好的技术经济效果,首先要确定合理的指标,经济上可行,技术上先进,再根据零件的结构工艺性,合理地确定装配作业的自动化程度。
表2-8 改进零部件装配工艺性示例


(2)自动装配工艺设计的一般要求
自动装配的工艺要求比人工装配的工艺要求复杂得多。为使自动装配工艺设计先进可靠、经济合理,在设计中应满足以下要求。
①保证装配工作循环的节拍同步 在自动装配设备中,多工位刚性传送系统多采用同步方式,故总是有多个装配工位同时进行装配作业。为使各工位工作协调,并提高装配工位和生产场地的利用率,要求各个装配工位的工作同时开始和同时结束,即要求装配工作的节拍同步。装配工序应力求可分,对于装配工作周期较长的装配工序,可同时占用相邻几个装配工位,使装配工作在相邻几个装配工位上逐渐完成来平衡各个装配工位的工作时间,从而使装配工作循环的节拍同步。
②除正常传送外,宜避免或减少装配基础件的位置变动 自动装配过程是将装配件按规定顺序和方向装到装配基础件上。通常装配基础件需要在传送装置上自动传送,并要求在每个装配工位上准确定位。故在装配过程中,应尽量避免或减少装配基础件的翻身、转位、升降等位置变动,以免影响装配过程中的定位精度,并可简化传动装置的结构。
③合理选择装配基准面 装配基准面通常应是精加工面或面积大的配合面,同时应考虑装配夹具所必需的装夹面和导向面。只有合理选择装配基准面,才能保证装配定位精度。
④对装配件要进行分类 为提高装配自动化程度,必须对装配件进行分类。大多数装配件是一些形状比较规则、容易分类分组的零件,按几何特性可分为轴类、套类、平板类和小杂件类,每类按尺寸比例又可分为长件、短件、匀称件三组,每组零件又可分为四种稳定状态。经分类分组后,采用相应的料斗装置,即可实现多数装配件的自动给料。
⑤关键件和复杂件的自动定向 多数形状规则的装配件可以实现自动给料和自动定向,但少数关键件和复杂件往往不能实现自动给料和自动定向,并且很可能成为自动装配失败的一个原因。为实现这类少数零件的自动定向,一般可参照以下方法。
a.概率法:零件自由落下呈各种位置,将其送到分类口,分类口按零件的几何形状设计,凡能通过分类口的零件即能定向排列。
b.极化法:利用零件的极化,即零件形状和质量的明显差异性,达到定向排列的目的。
c.测定法:按零件的形状,转化为电气量、气动量或机械量,来确定定向排列。
对于自动定向十分困难的关键件和复杂件,为不使自动定向结构过于复杂,有时以手工定向代替自动定向逐个装入可能更为可靠和经济合理。
⑥易缠绕零件要能进行定向隔离 装配件中的螺旋弹簧、纸箔垫片等都是易缠绕粘连的零件,在装配过程中,要实现对它们的定向隔离,主要方法有以下两种:
a.采用弹射器将绕簧机和装配线衔接,其具体特征为:经上料装置将弹簧排列在斜槽上,再用弹射器将其一个一个地弹射出来,将绕簧机与装配线衔接,由绕簧机绕制出一个弹簧后,用弹射器弹射出来,传送至装配线,不使弹簧相互接触而缠绕。
b.改进弹簧结构具体做法是在螺旋弹簧的两端各加两圈紧密相接的簧圈,以防止它们在纵向上相互缠绕。
⑦精密配合副要进行分组选配 自动装配中精密配合副的装配由选配来保证。根据配合副的配合要求,如配合尺寸、重量、转动惯量确定分组选配组数,一般可分3~20组。分组越多,配合精度越高,但选配、分组、储料的机构越复杂,占用车间的面积和空间尺寸也越大。因此,除机械式手表因部件多、装配分组也较多外(15~20组),一般不宜分组过多。
⑧合理确定装配的自动化程度 装配自动化程度的确定是一项十分重要的设计原则,需要根据工艺的成熟程度和实际经济效益确定,具体如下:
a.在螺纹连接工序中,由于多轴工作头对螺纹孔位置偏差的限制较严,又往往要求检测和控制拧紧力矩,导致自动装配机构十分复杂。因此,多用单轴工作头,且检测拧紧力矩多用手工操作。
b.形状规则、对称且数量多的装配件易于实现自动给料,故其给料自动化程度较高;复杂件和关键件往往不易自动定向,故自动化程度较低。
c.装配质量检测和不合格件的调整、剔除等工作的自动化程度较低,可用手工操作,以免自动检测头的机构过分复杂。
d.品种单一的装配线自动化程度较高,多品种装配线的自动化程度则较低,但随着装配工作头的标准化、通用化程度日益提高,多品种装配的自动化程度也可以提高。
e.对于尚不成熟的工艺,除采用半自动化外,需要考虑手动的可能性;对于采用自动或半自动装配而实际经济效益不显著的工序,可同时采用人工监视或手工操作。
f.在自动装配线上,下列装配工作一般应优先达到较高的自动化程度:
• 装配基础件的工序间传送,包括升降、摆转、翻身等改变位置的传送。
• 装配夹具的传送、定位和返回。
• 形状规则且数量多的装配件的供料和传送。
• 清洗、平衡、过盈连接、密封检测等工序。
⑨不断提高装配自动化水平 设计的自动装配线要可扩展,以便于改进完善;设计时要根据具体情况,注意吸收先进技术,如向自动化程度较高的数控装配机或装配中心发展,应用具有触觉和视觉的智能装配机器人等,不断提高装配自动化程度。
(3)装配工艺过程的确定
这个过程需要在不同的水平上分几步进行,是工艺工程师的一项复杂的工作。
①最高层面上的确定 首先要决定该产品是否适合自动化装配,是专用自动化还是柔性自动化。必须对此作具体的分析,甚至要对产品的设计作装配工艺性方面的改进,然后再确定装配的过程。这对产品的批量和生产周期起着重要作用。
②第二层面上的确定 确定装配工艺过程,其具体任务是确定装配操作的顺序,可以借助于流程图来进行。把各种不同的基本组织形式和装配工艺过程的排列顺序(装配工位)做出图来就产生出装配设备结构的不同变种。
③最低层面上的确定 从所要求的功能出发,把装配工艺过程分解到各个实际的组成部分。可以把装配划分为以下4个功能范围:
a.前装配辅助功能。属于这一功能范围的有整理、分离、上料、检验,为真正的装配工作装备基础件和配合件。这项工作也包括更换料仓或者把电子元件从传送带或胶黏带上分离出来。
b.装配功能。装配功能涉及几个具体的功能,例如抓取、移动、连接(压接、旋入、铆接等),其作用是把两个或多个零件先定位配合然后连接到一起。
c.后装配功能。已经完成装配的部件或产品必须从装配设备上取走,空的料仓也必须更换。在开始新的装配动作之前往往还要做功能检查。
d.监控功能。此项功能包括整个装配系统的监测、坐标控制,装配过程控制以及与前仓库和后仓库的信息交换。为了实现这些功能,物流、信息流、能量流是必需的。传输功能完成配合件的供应,送走装配好的部件,这就是物流;物体(零件)在空间的位置和方向信息(信息流),对被装配物体的定位和配合过程是必不可少的。当然,配合和连接过程都离不开力,这就是能量流。